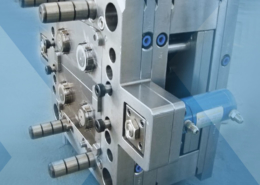
LSR Molding For Medical Equipment - molding medical
Author:gly Date: 2024-10-15
5. Increase the cross-sectional area of the gate (main runner, branch runner, and feed port), and reduce its length, to allow the resin to flow more easily
5. Does the strong friction between the metal wall of the hopper loader and the acrylic pellets cause the metal wall to peel off?
7. Increase the cross-sectional area of the gate (main runner, branch runner, and feed port) and reduce its length, to allow the resin to flow more easily and reduce the barrel temperature.
These are the ring-shaped stripes that occur on the surface of a product and are centered around the feed port. It can be prevented by taking the following measures:
6. Is there any soot or dust mixed in from the vents of the hopper loader, or whether there are foreign substances generated by the hopper loader itself?
Rotational molding, or "roto-molding," involves pouring melted plastic into a mold, which is then rotated at a high speed. This coats the plastic evenly along the walls of the heated metal mold, leaving the interior hollow. This method is primarily used for large, hollow-walled containers, storage bins, and even kayaks.
Compression molding is most often used with thermoset plastics whose chemical structure changes when melted and cooled to create a hard, rigid final product. Plastic resin is heated to a soft, almost "putty" state where it's not quite liquid, then it's placed into a heated mold. The putty is then pressed into shape by the mold and allowed to cool.
PMMA acrylic are widely used in all aspects of the optical field, so it is extremely necessary to prevent the mixing of impurities. Usually, there are many ways for foreign substances to be mixed in. It is time-consuming to find out the reason, but you can start with the following aspects:
Thermoforming involves heating a large sheet of plastic until it is soft and flexible, then stretching it over a single-sided, custom mold. Vacuum pressure or compressed air presses the thermoplastic tightly against the mold, creating the desired shape.
9. Increase the cross-sectional area of the gate (main runner, branch runner, and feed port) and reduce its length, to allow the resin to flow more easily.
1. When cooled with water after ejection, increase the temperature of the cooling water or reduce the water-cooling time
These are the cracks that occur on the surface or the contact surface with the insert of a product. When viewed from a certain angle, it will flicker and emit light. The causes of this defect are relatively complicated, which, however, can be prevented by taking the following measures:
These are the silver-white streaks on the product surface which are generated in the feed port along the flow direction of the resin. Caused by multifaceted factors, silver streaks can be prevented by taking the following measures:
This is caused because the resin does not fill the cavity fully. To prevent its occurrence, we can take the following measures:
Since 1988, Advanced Plastiform, Inc., has been providing superior custom plastic molding and fabrication services to companies in North Carolina, South Carolina, Maryland, Georgia and Pennsylvania. Contact us to make an appointment Mon-Fri 8-5.
When designing plastic products and components, one of the most challenging decisions is determining the right method of manufacturing them. Your goal is to have a durable, high-quality finished product while minimizing costs and speeding up efficiency and the right manufacturing method is key to meeting these goals. There are six main types of plastic manufacturing, and our thermoforming company in North Carolina is looking at each type and the associated benefits they offer.
At Advanced Plastiform, Inc., we specialize in heavy-gauge thermoforming and injection molding. Our experienced team includes engineers and designers as well as manufacturers, all of whom are dedicated to helping you meet your goals. Our company works with industries across the Mid-Atlantic and Southeast, including North Carolina, South Carolina, Pennsylvania, Maryland, Tennessee, Georgia, and Virginia. To learn more, call us at 919-404-2080 or fill out the contact form to get started.
These are the voids that occur where the product wall is thick. For transparent PMMA products, they will become an exterior defect that cannot be remedied later. Insufficient drying before molding or excessive barrel temperature may cause voids to occur in areas other than the center of the thick wall. If the shrinkage is concentrated in the thick wall, voids will appear in the center of the thick wall. It can be solved by the prevention of shrinkage, or by the following measures:
Blow molding is similar to injection molding as the plastic is heated to a liquid state and injected into a mold. However, once the plastic is placed in the mold, air is injected into the plastic, inflating it so that it presses against the walls of the mold and achieves the desired shape.
3. Are there any other resins mixed in the pre-dryer, or are there any foreign substances caused by friction between the dryer and the receiver?
The defects in the injection molding of acrylic PMMA usually include: short shot, silver streaks, sink marks, voids, jetting, weld marks, gray / black specks, cracking, warpage, and material impurity, while the preventive measures against them are usually:
Extrusion molding is primarily used to manufacture long, straight pieces, such as tubing, hoses, or pipes. This method involves forcing liquid plastic into a die to form a shape. While round pieces are common, t-shapes, l-shapes, and squares are also achieved, depending on the shape of the die. Many thermoplastics can be used during extrusion molding.
Injection molding is a plastic manufacturing method in which a thermoplastic is melted to a liquid, then injected into a double-sided mold using a highly pressurized injector. The plastic coats and fills the mold to create the needed shape, and is then cooled and ejected for finishing.
GETTING A QUOTE WITH LK-MOULD IS FREE AND SIMPLE.
FIND MORE OF OUR SERVICES:
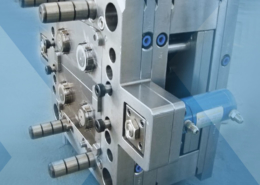
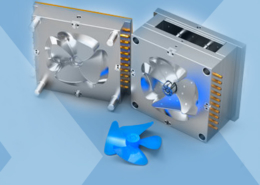
Plastic Molding

Rapid Prototyping
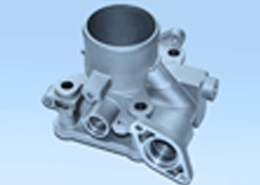
Pressure Die Casting
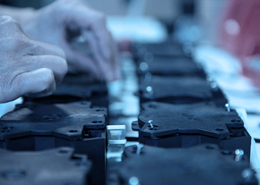
Parts Assembly
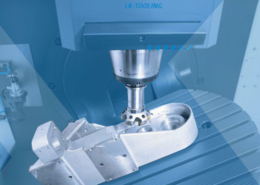