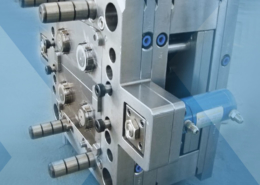
Low-Volume Injection Molding: Exploring Production ... - low cost plastic inject
Author:gly Date: 2024-10-15
Can recycled materials be used in CNC machining?Yes, certain recycled materials, such as recycled PET (rPET), can be used in CNC machining. They can offer cost savings and environmental benefits but should be evaluated for consistency and performance compared to virgin materials. In general, plastics with a high (25%+) percentage of recycled content tend to be more brittle and have degraded physical properties.
This blog post aims to explore five different methods for manufacturing plastic prototypes, highlighting the advantages and limitations of each method.
Sheet metal fabrication takes thin, flat, and bendable sheets of different types of metal and cuts, bends, and assembles them into a variety of products...9/2/2021 PDF FileSheet Metal Fabrication
The software needed to print prototypes is often exclusive to the hardware utilized; nonetheless, the following list of CAD applications is used to produce models:
ApplicationsComponents for packaging machinery, such as guides, rollers, and conveyor parts.Food processing equipment, including gears, bearings, and seals, because of its food-grade properties and resistance to chemicals.Precision automotive components like gears, bushings, and fasteners.Suitable for electrical insulators, connectors, and housings for electronic components.Various medical device components such as housings, covers, and supports, take advantage of its biocompatibility and ease of sterilization.Gears, cams, and tensioners for textile machinery for their strength, durability, and low friction characteristics.Laboratory equipment parts, including containers, holders, and fixtures.Printing machine components such as rollers, guides, and feed mechanisms, benefit from its dimensional stability and wear resistance.PropertiesExcellent tensile strength and rigidity.Resistant to a wide range of chemicals, including acids, bases, and solvents,Maintains its shape and size under various conditions, offering high dimensional stability, which is crucial for precision parts.Low water absorption, ensuring that its mechanical properties remain stable in humid or wet environments.Can withstand moderate temperatures without significant deformation or degradation, making it suitable for applications involving heat exposure.Excellent electrical insulating properties.Good wear resistance, which contributes to its durability and longevity in high-friction applications.Other Advantages:Can be easily machined, molded, and thermoformed, facilitating its use in a variety of manufacturing processes.PET is highly recyclable, contributing to environmental sustainability and making it a preferred material in industries that prioritize eco-friendly practices. Recycled rPET can be used to produce new products, reducing the environmental impact of plastic waste.
A product’s usability and popularity among customers are improved by strategically placing interface elements.Prototyping also helps to save a lot of time. Additionally, it facilitates the design creation process, and during the prototyping phase, it is easy to spot extraneous components that are best left out. The workload of the designer during the manufacturing process is greatly reduced by this technique, ultimately resulting in cost savings for the client.
When choosing a prototype option, cost is always an important factor to take into account. The quantity of prototype components needed is essential in determining the procedure since some prototyping methods are only financially viable for lesser numbers.
Consideration of specific part requirements, such as wear resistance, weight, and hardness, is crucial for material selection.Wear Resistance - Many plastics offer good wear resistance and are suitable for parts subjected to wear, such as gears and bushings.Weight - For applications where weight is a critical factor, certain plastics, which are lightweight, should be selected.Hardness - Plastic materials with high hardness are suitable for parts requiring high wear resistance and durability.
One of the most expedient ways to produce plastic prototypes is through CNC precision machining. CNC machines use a range of cutting tools and cutter paths that are specially designed for the desired cut when carving a 3D model directly from a solid block of plastic.
PropertiesResistant to many acids, bases, salts, and organic solvents.Good tensile strength and impact resistance.Excellent electrical insulator.Withstands exposure to the elements, including UV radiation, without significant degradation.Absorbs very little water.Other AdvantagesIt is available in rigid and flexible forms, offering versatility in use, making it a popular choice for CNC machining applications.Parts made of PVC are durable and have a long service life.Unlike many other plastics, PVC is inherently flame-retardant. It is self-extinguishing, which means it stops burning when the ignition source is removed. This property is highly valued in the construction, electrical insulation, and transportation industries.PVC is relatively inexpensive compared to other engineering plastics like PEEK or PTFE. Its cost-effectiveness makes it a popular choice for large-scale applications, particularly in the construction and infrastructure sectors.
Selecting the right plastic material for CNC machining to manufacture parts is a critical decision that can impact both the cost and performance of a project. By following the guidelines outlined in this article you can avoid common pitfalls and make informed decisions so that you can select the right plastic material for your CNC machined parts.IntroductionPlastic Materials for CNC MachiningNylonPTFE (Polytetrafluoroethylene) or TeflonAcetal (POM)PEEKPolyvinyl Chloride (PVC)Polyethylene terephthalate (PET)ABS (Acrylonitrile Butadiene Styrene)Comparison - Material Properties and ApplicationsHow to Select a Plastic Material for CNC MachiningFactors for Selecting a Plastic Material for CNC MachiningApplication NeedsPart NeedsConclusionThe Komacut AdvantageFAQs
Additionally, a prototype using this technique will enable you to test every component you want. Additionally, it will serve as the basis for the succeeding mold that will be used for your whole manufacturing process.
Based on the product and application requirements, establish criteria for selecting the plastic type, considering factors such as machinability, cost, availability, and suitability for the application.Shortlist Material Options - Shortlist your potential materials and then evaluate trade-offs between material properties, cost factors, and application requirements.Consult References: Refer to material selection guides, handbooks, and databases to compare the properties of different plastics and their suitability for CNC machining.Cost Analysis: Compare the cost of each material, including raw material cost, machining costs, and any additional costs (e.g., surface treatment, post-machining operations).Final Selection: Based on the above considerations, select the plastic material that best meets the requirements for the CNC machining process.Fig. 2: Simple CNC Machined Parts Made of Plastic
Plastics offer several advantages over metals, including lighter weight, corrosion resistance, lower cost, and ease of machining.How does the machinability of plastics compare to metals?Plastics generally have better machinability compared to metals due to their lower hardness and density. They require less cutting force and can be machined at higher speeds, reducing tool wear and production time. However, some plastics may have specific challenges, such as melting or deforming under high temperatures, which need to be managed during machining.What surface finishes can be achieved with CNC-machined plastics?CNC-machined plastics can achieve a variety of surface finishes depending on the machining process and tools used. Common finishes include a smooth, polished finish, matte or textured finishes for improved grip or reduced glare, and precision finishes for tight tolerance parts.Are there any special considerations for machining reinforced plastics?Reinforced plastics, such as those with fiberglass or carbon fiber, require special considerations due to their abrasive nature. These materials can cause increased tool wear and may require the use of carbide or diamond-coated tools.How does production volume impact the choice of plastic material for CNC machining?For low production volumes, CNC machining is a cost-effective method for producing plastic parts and is often used for prototyping or pilot productions due to the lack of any requirement for mold or tooling investment. However, for medium to high-volume production, other manufacturing methods such as vacuum casting or injection molding will have a definite cost advantage.Can recycled materials be used in CNC machining?Yes, certain recycled materials, such as recycled PET (rPET), can be used in CNC machining. They can offer cost savings and environmental benefits but should be evaluated for consistency and performance compared to virgin materials. In general, plastics with a high (25%+) percentage of recycled content tend to be more brittle and have degraded physical properties.
How does the machinability of plastics compare to metals?Plastics generally have better machinability compared to metals due to their lower hardness and density. They require less cutting force and can be machined at higher speeds, reducing tool wear and production time. However, some plastics may have specific challenges, such as melting or deforming under high temperatures, which need to be managed during machining.What surface finishes can be achieved with CNC-machined plastics?CNC-machined plastics can achieve a variety of surface finishes depending on the machining process and tools used. Common finishes include a smooth, polished finish, matte or textured finishes for improved grip or reduced glare, and precision finishes for tight tolerance parts.Are there any special considerations for machining reinforced plastics?Reinforced plastics, such as those with fiberglass or carbon fiber, require special considerations due to their abrasive nature. These materials can cause increased tool wear and may require the use of carbide or diamond-coated tools.How does production volume impact the choice of plastic material for CNC machining?For low production volumes, CNC machining is a cost-effective method for producing plastic parts and is often used for prototyping or pilot productions due to the lack of any requirement for mold or tooling investment. However, for medium to high-volume production, other manufacturing methods such as vacuum casting or injection molding will have a definite cost advantage.Can recycled materials be used in CNC machining?Yes, certain recycled materials, such as recycled PET (rPET), can be used in CNC machining. They can offer cost savings and environmental benefits but should be evaluated for consistency and performance compared to virgin materials. In general, plastics with a high (25%+) percentage of recycled content tend to be more brittle and have degraded physical properties.
Finalize Requirements & Selection CriteriaBased on the product and application requirements, establish criteria for selecting the plastic type, considering factors such as machinability, cost, availability, and suitability for the application.Shortlist Material Options - Shortlist your potential materials and then evaluate trade-offs between material properties, cost factors, and application requirements.Consult References: Refer to material selection guides, handbooks, and databases to compare the properties of different plastics and their suitability for CNC machining.Cost Analysis: Compare the cost of each material, including raw material cost, machining costs, and any additional costs (e.g., surface treatment, post-machining operations).Final Selection: Based on the above considerations, select the plastic material that best meets the requirements for the CNC machining process.Fig. 2: Simple CNC Machined Parts Made of Plastic
PropertiesExcellent dimensional stability.Exceptional machinability.Low friction.Low moisture absorption.Other AdvantagesPOM is easy to cut, drill, and shape using CNC machining processes. It is often the best choice for CNC machining plastic parts that require high precision, stiffness, low friction, dimensional stability at elevated temperatures, and low water absorption.POM is often used for machining gears because of its high strength, low friction, and excellent wear resistance.
How does production volume impact the choice of plastic material for CNC machining?For low production volumes, CNC machining is a cost-effective method for producing plastic parts and is often used for prototyping or pilot productions due to the lack of any requirement for mold or tooling investment. However, for medium to high-volume production, other manufacturing methods such as vacuum casting or injection molding will have a definite cost advantage.Can recycled materials be used in CNC machining?Yes, certain recycled materials, such as recycled PET (rPET), can be used in CNC machining. They can offer cost savings and environmental benefits but should be evaluated for consistency and performance compared to virgin materials. In general, plastics with a high (25%+) percentage of recycled content tend to be more brittle and have degraded physical properties.
Because larger parts take longer to print than smaller ones, the component volume also affects the cost of additive manufacturing. While some processes need a lot of labor and have high unit costs, other methods are significantly more productive and cost-effective.
Vacuum casting would produce components that are almost comparable to those of injection molding and may be utilized without post-processing, but alternative procedures, like 3D printing, may require some post-processing time but are considerably more versatile for complex shapes.
Consider Part UseDetermine the specific requirements of the part, including mechanical properties (strength, hardness, etc.), dimensional tolerances, surface finish etc.Consider the applicationDoes your target application have any special requirements for the parts in terms of electrical conductivity, self-lubrication, etc.?What kind of environment is the application – is it highly corrosive? Is there a high degree of exposure to UV or weathering? High heat?Are there regulatory or certification requirements?Finalize Requirements & Selection CriteriaBased on the product and application requirements, establish criteria for selecting the plastic type, considering factors such as machinability, cost, availability, and suitability for the application.Shortlist Material Options - Shortlist your potential materials and then evaluate trade-offs between material properties, cost factors, and application requirements.Consult References: Refer to material selection guides, handbooks, and databases to compare the properties of different plastics and their suitability for CNC machining.Cost Analysis: Compare the cost of each material, including raw material cost, machining costs, and any additional costs (e.g., surface treatment, post-machining operations).Final Selection: Based on the above considerations, select the plastic material that best meets the requirements for the CNC machining process.Fig. 2: Simple CNC Machined Parts Made of Plastic
Material PropertiesTensile strength, yield strength, hardness, and ductility are important mechanical properties. Higher tensile strength and hardness are desirable for parts subjected to high loads, while ductility is important for parts that require deformation without breaking.Thermal PropertiesThermal conductivity and coefficient of thermal expansion are important for parts subjected to temperature variations. High thermal conductivity helps in dissipating heat generated during machining, while a low coefficient of thermal expansion ensures dimensional stability at different temperatures.Chemical PropertiesCorrosion resistance and chemical compatibility are crucial for parts exposed to corrosive environments or chemicals.MachinabilityFactors such as material machinability, complexity of the part, and machining time. Materials that are easy to machine, may result in shorter machining times compared to harder materials.CostsCost-effectiveness in material selection involves evaluating the cost per kilogram of material and the machining time required to produce the part. Some materials may have a higher initial cost but offer cost savings in terms of reduced machining time.
The material greatly influences the quality of the prototype. Selecting components made via additive manufacturing may not be the best option if functional features are connected to unique material qualities, such as surface polish and durability. Following are a few examples of common plastic materials used in various industrial processes:
PEEK (polyetheretherketone) is a high-performance engineering thermoplastic with very good mechanical properties, including high-temperature resistance, strength, and chemical resistance. PEEK is commonly used in CNC machining for applications where durability and reliability are critical.ApplicationsSeals, bushings, and brackets for high strength-to-weight ratio, thermal stability, and resistance to radiation.As PEEK is biocompatible and sterilizable it is an ideal material for medical components and applicationsBearings, piston parts, and transmission elements because of high temperature and chemical resistance.Excellent electrical insulating properties make it suitable for high-performance electrical connectors and insulators.Valve seats, and compressor components due to resistance to harsh chemicals and high pressures.Semiconductor fabrication equipment because of their low outgassing and high purity.Pump parts, valve components, and other equipment in aggressive chemical environments.Parts that require compliance with food safety standards, having resistance to high temperatures and chemicals.Its excellent wear resistance and low friction make PEEK suitable for machining into bearings, bushings, and other wear-resistant parts.PropertiesMaintains its mechanical properties at temperatures up to 260°C.Highly resistant to a wide range of chemicals, including acids, bases, and organic solvents.High tensile strength and stiffness.Low coefficient of friction and excellent wear resistance.Maintains its dimensions and shape under varying thermal and mechanical conditions.Biocompatible and suitable for medical implants and devices.Can withstand high levels of radiation without significant degradation.Excellent insulating properties.Low outgassing.Relatively high cost (the most expensive of standard machined materials)Other AdvantagesPEEK is available in medical grades, making it suitable for biomedical applications such as implants, surgical instruments, and medical devices where biocompatibility and sterilizability are crucial.It is inherently flame resistant and generates very low smoke and toxic emissions when exposed to fire
Next, a two-part liquid material such as polyurethane or epoxy resin is poured into the mold cavity. The mold is placed in a vacuum chamber, where the air is removed, creating a vacuum that forces the liquid material into the mold’s cavities and ensures the part is free from air bubbles or voids.
The use of rapid prototyping technologies during the production process guarantees a high degree of precision and accuracy. It is fair to believe that design drawings of CAD software are quite accurate. Precision is a crucial component to take into account since it guarantees that your product will be produced consistently.
Chemical PropertiesCorrosion resistance and chemical compatibility are crucial for parts exposed to corrosive environments or chemicals.MachinabilityFactors such as material machinability, complexity of the part, and machining time. Materials that are easy to machine, may result in shorter machining times compared to harder materials.CostsCost-effectiveness in material selection involves evaluating the cost per kilogram of material and the machining time required to produce the part. Some materials may have a higher initial cost but offer cost savings in terms of reduced machining time.
Other AdvantagesPEEK is available in medical grades, making it suitable for biomedical applications such as implants, surgical instruments, and medical devices where biocompatibility and sterilizability are crucial.It is inherently flame resistant and generates very low smoke and toxic emissions when exposed to fire
What surface finishes can be achieved with CNC-machined plastics?CNC-machined plastics can achieve a variety of surface finishes depending on the machining process and tools used. Common finishes include a smooth, polished finish, matte or textured finishes for improved grip or reduced glare, and precision finishes for tight tolerance parts.Are there any special considerations for machining reinforced plastics?Reinforced plastics, such as those with fiberglass or carbon fiber, require special considerations due to their abrasive nature. These materials can cause increased tool wear and may require the use of carbide or diamond-coated tools.How does production volume impact the choice of plastic material for CNC machining?For low production volumes, CNC machining is a cost-effective method for producing plastic parts and is often used for prototyping or pilot productions due to the lack of any requirement for mold or tooling investment. However, for medium to high-volume production, other manufacturing methods such as vacuum casting or injection molding will have a definite cost advantage.Can recycled materials be used in CNC machining?Yes, certain recycled materials, such as recycled PET (rPET), can be used in CNC machining. They can offer cost savings and environmental benefits but should be evaluated for consistency and performance compared to virgin materials. In general, plastics with a high (25%+) percentage of recycled content tend to be more brittle and have degraded physical properties.
PropertiesMaintains its mechanical properties at temperatures up to 260°C.Highly resistant to a wide range of chemicals, including acids, bases, and organic solvents.High tensile strength and stiffness.Low coefficient of friction and excellent wear resistance.Maintains its dimensions and shape under varying thermal and mechanical conditions.Biocompatible and suitable for medical implants and devices.Can withstand high levels of radiation without significant degradation.Excellent insulating properties.Low outgassing.Relatively high cost (the most expensive of standard machined materials)Other AdvantagesPEEK is available in medical grades, making it suitable for biomedical applications such as implants, surgical instruments, and medical devices where biocompatibility and sterilizability are crucial.It is inherently flame resistant and generates very low smoke and toxic emissions when exposed to fire
CNC-machined plastics can achieve a variety of surface finishes depending on the machining process and tools used. Common finishes include a smooth, polished finish, matte or textured finishes for improved grip or reduced glare, and precision finishes for tight tolerance parts.Are there any special considerations for machining reinforced plastics?Reinforced plastics, such as those with fiberglass or carbon fiber, require special considerations due to their abrasive nature. These materials can cause increased tool wear and may require the use of carbide or diamond-coated tools.How does production volume impact the choice of plastic material for CNC machining?For low production volumes, CNC machining is a cost-effective method for producing plastic parts and is often used for prototyping or pilot productions due to the lack of any requirement for mold or tooling investment. However, for medium to high-volume production, other manufacturing methods such as vacuum casting or injection molding will have a definite cost advantage.Can recycled materials be used in CNC machining?Yes, certain recycled materials, such as recycled PET (rPET), can be used in CNC machining. They can offer cost savings and environmental benefits but should be evaluated for consistency and performance compared to virgin materials. In general, plastics with a high (25%+) percentage of recycled content tend to be more brittle and have degraded physical properties.
PropertiesExcellent tensile strength and rigidity.Resistant to a wide range of chemicals, including acids, bases, and solvents,Maintains its shape and size under various conditions, offering high dimensional stability, which is crucial for precision parts.Low water absorption, ensuring that its mechanical properties remain stable in humid or wet environments.Can withstand moderate temperatures without significant deformation or degradation, making it suitable for applications involving heat exposure.Excellent electrical insulating properties.Good wear resistance, which contributes to its durability and longevity in high-friction applications.Other Advantages:Can be easily machined, molded, and thermoformed, facilitating its use in a variety of manufacturing processes.PET is highly recyclable, contributing to environmental sustainability and making it a preferred material in industries that prioritize eco-friendly practices. Recycled rPET can be used to produce new products, reducing the environmental impact of plastic waste.
Cost-effectiveness in material selection involves evaluating the cost per kilogram of material and the machining time required to produce the part. Some materials may have a higher initial cost but offer cost savings in terms of reduced machining time.
Nylon’s versatility and performance characteristics make it a preferred choice for parts used in various industries manufactured using CNC machining. Nylon is strong, has good impact resistance, and is widely available in block or bar form.ApplicationsLightweight components like gears, bushings, gaskets, and bearing surfaces, replacing metal parts for weight reduction and fuel efficiency.Electrical connectors and insulating partsMachine parts like pulleys and rollersPropertiesExcellent mechanical properties.Impact strength.Chemical resistance.Abrasion resistance.Low coefficient of friction.Susceptible to water and moisture absorption.Other AdvantagesEase of machining.Low cost.
Plastics generally have better machinability compared to metals due to their lower hardness and density. They require less cutting force and can be machined at higher speeds, reducing tool wear and production time. However, some plastics may have specific challenges, such as melting or deforming under high temperatures, which need to be managed during machining.What surface finishes can be achieved with CNC-machined plastics?CNC-machined plastics can achieve a variety of surface finishes depending on the machining process and tools used. Common finishes include a smooth, polished finish, matte or textured finishes for improved grip or reduced glare, and precision finishes for tight tolerance parts.Are there any special considerations for machining reinforced plastics?Reinforced plastics, such as those with fiberglass or carbon fiber, require special considerations due to their abrasive nature. These materials can cause increased tool wear and may require the use of carbide or diamond-coated tools.How does production volume impact the choice of plastic material for CNC machining?For low production volumes, CNC machining is a cost-effective method for producing plastic parts and is often used for prototyping or pilot productions due to the lack of any requirement for mold or tooling investment. However, for medium to high-volume production, other manufacturing methods such as vacuum casting or injection molding will have a definite cost advantage.Can recycled materials be used in CNC machining?Yes, certain recycled materials, such as recycled PET (rPET), can be used in CNC machining. They can offer cost savings and environmental benefits but should be evaluated for consistency and performance compared to virgin materials. In general, plastics with a high (25%+) percentage of recycled content tend to be more brittle and have degraded physical properties.
ApplicationsAutomobile dashboard parts, instrument panels, and trims.Various medical device housings and components that do not require sterilization.Housings and structural components of home appliances.Components for blenders, mixers, and coffee makers.Various small parts and enclosures for machinery and equipment.PropertiesIt is a relatively tough but lightweight and low-cost material, able to withstand heavy impacts without shattering.Has a relatively low density, making it lightweight.Has good dimensional stability.Resistant to a wide range of chemicals, including acids and alkalis.Moderate heat resistance, with a melting point typically between 200°C to 240°C.Some ABS grades are flame retardant, making them suitable for applications where fire safety is a concern.Good electrical insulating properties.Easy to machine, drill, and cut, allowing for the creation of intricate shapes and designs.Other advantagesABS parts are often used as prototypes before mass production.One of the key advantages of ABS is its high impact strength, which allows it to withstand sudden loads and impacts without breaking or cracking. This property makes it ideal for parts that may be subjected to rough handling or impactsIt can be easily finished and painted, providing a smooth and aesthetically pleasing surface in many colors and textures.It is recyclable, allowing it to be reused, contributing to sustainability.
One of the primary challenges in plastic material selection for CNC machining is that not all plastic materials are suitable for a particular part Or application. It’s important to select the right material for any part, but selecting a plastic for machining is particularly tricky.Some plastics also exhibit significant dimensional instability, impacting tolerances, and some also have limited color options. There are strength considerations, resistance to stress cracking, or heat expansion. Application-specific considerations such as chemical resistance, food safety, or self-lubrication can also be an aspect.The potential cost implications and performance issues associated with incorrect material choices cannot be overstated. Using the wrong material can lead to increased scrap rates, longer lead times, and higher overall production costs. It can also result in parts that do not meet the required specifications, leading to quality issues and customer dissatisfaction.Fig. 1: CNC Machined Plastic Parts
Rapid prototyping is appropriate for plastic products that must have an exact dimension or fit. Engineers and product designers sometimes have to test the plastic prototype several times quickly to fulfill deadlines to attain perfection. As the name says, rapid prototyping has this benefit.
ABS is a widely used thermoplastic known for its excellent mechanical properties, impact strength, heat resistance, machinability, and relatively low cost making it a popular choice for CNC machining applications.ApplicationsAutomobile dashboard parts, instrument panels, and trims.Various medical device housings and components that do not require sterilization.Housings and structural components of home appliances.Components for blenders, mixers, and coffee makers.Various small parts and enclosures for machinery and equipment.PropertiesIt is a relatively tough but lightweight and low-cost material, able to withstand heavy impacts without shattering.Has a relatively low density, making it lightweight.Has good dimensional stability.Resistant to a wide range of chemicals, including acids and alkalis.Moderate heat resistance, with a melting point typically between 200°C to 240°C.Some ABS grades are flame retardant, making them suitable for applications where fire safety is a concern.Good electrical insulating properties.Easy to machine, drill, and cut, allowing for the creation of intricate shapes and designs.Other advantagesABS parts are often used as prototypes before mass production.One of the key advantages of ABS is its high impact strength, which allows it to withstand sudden loads and impacts without breaking or cracking. This property makes it ideal for parts that may be subjected to rough handling or impactsIt can be easily finished and painted, providing a smooth and aesthetically pleasing surface in many colors and textures.It is recyclable, allowing it to be reused, contributing to sustainability.
Tensile strength, yield strength, hardness, and ductility are important mechanical properties. Higher tensile strength and hardness are desirable for parts subjected to high loads, while ductility is important for parts that require deformation without breaking.Thermal PropertiesThermal conductivity and coefficient of thermal expansion are important for parts subjected to temperature variations. High thermal conductivity helps in dissipating heat generated during machining, while a low coefficient of thermal expansion ensures dimensional stability at different temperatures.Chemical PropertiesCorrosion resistance and chemical compatibility are crucial for parts exposed to corrosive environments or chemicals.MachinabilityFactors such as material machinability, complexity of the part, and machining time. Materials that are easy to machine, may result in shorter machining times compared to harder materials.CostsCost-effectiveness in material selection involves evaluating the cost per kilogram of material and the machining time required to produce the part. Some materials may have a higher initial cost but offer cost savings in terms of reduced machining time.
Many companies struggle to find reliable and cost-effective suppliers for low and medium-volume production – prototyping companies charge high set-up costs and per-piece pricing; larger manufacturers are not interested in orders of several hundred or even thousand pieces. Not to mention the time and expertise needed to manage and coordinate with these suppliers. Komacut is a solution to bridge the gap between prototyping and mass production, with instant quotes, easy management, and flawless execution from quote to order to delivery.For more information on designing and manufacturing CNC machining and machined parts, please visit the Komacut website. Instant quotations and design feedback, a range of materials, engineering design guidelines, and more - visit Komacut today for superior CNC machining solutions.Try Komacut
Through the use of a plastic injection mold prototype, you may see a practically identical development of your finished product in reality. Many companies, including those in the automotive, electronic, healthcare, and packaging sectors, often use this strategy. It works effectively for items that need a lot of testing and certification.
Several types of plastics can be used in combination with CNC milling and turning, but the choices are generally more limited compared to injection or other fabrication processes, due to the heat and stress introduced to plastic material during the machining process. This means that many standard plastic materials are not widely, or ever, used to manufacture plastic parts by machining.
This particular kind of plastic is the one that is most usually used. The key feature that sets them apart from thermosets is their capacity for several melt and solidification cycles. It can be heated to change its shape or geometric properties. The technique results in no chemical bonding, therefore, recycling or melting thermoplastics is a possibility.
Since there are some methods to get the desired objective, each has its unique benefits and drawbacks that should be considered. How to choose the suitable one? Continue to read!
MachinabilityFactors such as material machinability, complexity of the part, and machining time. Materials that are easy to machine, may result in shorter machining times compared to harder materials.CostsCost-effectiveness in material selection involves evaluating the cost per kilogram of material and the machining time required to produce the part. Some materials may have a higher initial cost but offer cost savings in terms of reduced machining time.
Other AdvantagesPOM is easy to cut, drill, and shape using CNC machining processes. It is often the best choice for CNC machining plastic parts that require high precision, stiffness, low friction, dimensional stability at elevated temperatures, and low water absorption.POM is often used for machining gears because of its high strength, low friction, and excellent wear resistance.
ApplicationsIdeal for bearings and bushings due to its low coefficient of friction and high dimensional stability.Electrical components that require high dielectric strength and resistance to moisture.Precision parts due to dimensional stability and ease of machining.Automobile parts such as fuel system components, belt buckles, and various mechanical parts.Screws, nuts, and other fastening components for its strength and ease of threading.Various medical device components due to its biocompatibility and ease of sterilization.Valves and valve seats for applications that require precise control and resistance to wear and chemicals.PropertiesExcellent dimensional stability.Exceptional machinability.Low friction.Low moisture absorption.Other AdvantagesPOM is easy to cut, drill, and shape using CNC machining processes. It is often the best choice for CNC machining plastic parts that require high precision, stiffness, low friction, dimensional stability at elevated temperatures, and low water absorption.POM is often used for machining gears because of its high strength, low friction, and excellent wear resistance.
After checking the prototypes, the designer and client can more precisely assess the outcome. That’s why we need to make plastic prototypes.
For more information on designing and manufacturing CNC machining and machined parts, please visit the Komacut website. Instant quotations and design feedback, a range of materials, engineering design guidelines, and more - visit Komacut today for superior CNC machining solutions.Try Komacut
Making prototypes before starting full-scale production of your items might be highly beneficial. The industrial sector has benefited from prototyping improvements by quickly producing plastic prototypes.
Selecting materials based on the operational environment and final product requirements involves considering the following important factors:Corrosive Environments - Certain plastics offer excellent chemical and corrosion resistance and are suitable for applications in corrosive environments, such as moisture with salts, acidic environments, high temperatures, pollutants, and organic chemicals.Electrical Conductivity - Plastic materials have low electrical conductivity and are useful as insulators and casing to avoid electrical leakages and shocks.Food Grade Applications - Many plastics are food-grade and should be selected for applications in food processing or medical industries. ABS, PET, and PP are common selections for food-grade materials, while fiberglass blended plastics should be avoided.
PropertiesExcellent mechanical properties.Low deformation under load.High tensile strength.Good impact resistance.Excellent electrical insulator even at high temperatures.Resistant to a wide range of chemicals, acids, and solvents.Low coefficient of friction.Other AdvantagesPTFE itself is often machined in CNC machining operations to create components that require good thermal stability. It can withstand temperatures above 200 degrees Celsius without losing its mechanical properties, making it suitable for high-temperature applications where other plastics would degrade.It has the lowest coefficient of friction of any known solid material, providing excellent lubricity and making it ideal for applications such as bearings and seals.
Time is an essential factor when performing plastic prototyping. Post-processing and assembling parts from low-quality prototypes will take longer than from high-quality prototypes.
Another great technique for making plastic prototype components swiftly is injection molding. The procedure begins with the construction of an aluminum or steel mold equipped with a runner system, a channel that allows molten plastic to flow to the chamber of the mold. The required plastic prototype is created by injecting molten plastic ingredients into the mold, allowing them to cool and solidifying them.
Factors such as material machinability, complexity of the part, and machining time. Materials that are easy to machine, may result in shorter machining times compared to harder materials.CostsCost-effectiveness in material selection involves evaluating the cost per kilogram of material and the machining time required to produce the part. Some materials may have a higher initial cost but offer cost savings in terms of reduced machining time.
Whether you’re a seasoned professional or a novice in the field, this post will provide you with valuable insights into the world of plastic prototype manufacturing and help you make informed decisions about which method to choose for your project.
ApplicationsSeals, bushings, and brackets for high strength-to-weight ratio, thermal stability, and resistance to radiation.As PEEK is biocompatible and sterilizable it is an ideal material for medical components and applicationsBearings, piston parts, and transmission elements because of high temperature and chemical resistance.Excellent electrical insulating properties make it suitable for high-performance electrical connectors and insulators.Valve seats, and compressor components due to resistance to harsh chemicals and high pressures.Semiconductor fabrication equipment because of their low outgassing and high purity.Pump parts, valve components, and other equipment in aggressive chemical environments.Parts that require compliance with food safety standards, having resistance to high temperatures and chemicals.Its excellent wear resistance and low friction make PEEK suitable for machining into bearings, bushings, and other wear-resistant parts.PropertiesMaintains its mechanical properties at temperatures up to 260°C.Highly resistant to a wide range of chemicals, including acids, bases, and organic solvents.High tensile strength and stiffness.Low coefficient of friction and excellent wear resistance.Maintains its dimensions and shape under varying thermal and mechanical conditions.Biocompatible and suitable for medical implants and devices.Can withstand high levels of radiation without significant degradation.Excellent insulating properties.Low outgassing.Relatively high cost (the most expensive of standard machined materials)Other AdvantagesPEEK is available in medical grades, making it suitable for biomedical applications such as implants, surgical instruments, and medical devices where biocompatibility and sterilizability are crucial.It is inherently flame resistant and generates very low smoke and toxic emissions when exposed to fire
ApplicationsLightweight components like gears, bushings, gaskets, and bearing surfaces, replacing metal parts for weight reduction and fuel efficiency.Electrical connectors and insulating partsMachine parts like pulleys and rollersPropertiesExcellent mechanical properties.Impact strength.Chemical resistance.Abrasion resistance.Low coefficient of friction.Susceptible to water and moisture absorption.Other AdvantagesEase of machining.Low cost.
Polyethylene terephthalate (PET) is a widely used thermoplastic with excellent properties, making it suitable for various CNC machining applications.ApplicationsComponents for packaging machinery, such as guides, rollers, and conveyor parts.Food processing equipment, including gears, bearings, and seals, because of its food-grade properties and resistance to chemicals.Precision automotive components like gears, bushings, and fasteners.Suitable for electrical insulators, connectors, and housings for electronic components.Various medical device components such as housings, covers, and supports, take advantage of its biocompatibility and ease of sterilization.Gears, cams, and tensioners for textile machinery for their strength, durability, and low friction characteristics.Laboratory equipment parts, including containers, holders, and fixtures.Printing machine components such as rollers, guides, and feed mechanisms, benefit from its dimensional stability and wear resistance.PropertiesExcellent tensile strength and rigidity.Resistant to a wide range of chemicals, including acids, bases, and solvents,Maintains its shape and size under various conditions, offering high dimensional stability, which is crucial for precision parts.Low water absorption, ensuring that its mechanical properties remain stable in humid or wet environments.Can withstand moderate temperatures without significant deformation or degradation, making it suitable for applications involving heat exposure.Excellent electrical insulating properties.Good wear resistance, which contributes to its durability and longevity in high-friction applications.Other Advantages:Can be easily machined, molded, and thermoformed, facilitating its use in a variety of manufacturing processes.PET is highly recyclable, contributing to environmental sustainability and making it a preferred material in industries that prioritize eco-friendly practices. Recycled rPET can be used to produce new products, reducing the environmental impact of plastic waste.
Vacuum casting involves first creating a master pattern of the desired part using 3D printing or CNC machining. This pattern is then used to make a silicone mold.
Businesses and entrepreneurs may benefit significantly from prototyping. It is a method of testing your concept before moving forward with large-scale manufacturing. Additionally, it enables the designer to present his idea to potential investors.
The process of CNC machining is subtractive. In other words, it entails removing material from an unfinished item. A milling machine is used to do CNC machining on plastic components. A milling machine has many axes that may be manipulated.
In certain cases, a quick prototyping industry will simply require an initial design to start the production process and create a computer model. OEMs (original equipment manufacturers) that want a high-quality prototype quickly and have the financial means to do so may consider using rapid prototyping.
Other advantagesABS parts are often used as prototypes before mass production.One of the key advantages of ABS is its high impact strength, which allows it to withstand sudden loads and impacts without breaking or cracking. This property makes it ideal for parts that may be subjected to rough handling or impactsIt can be easily finished and painted, providing a smooth and aesthetically pleasing surface in many colors and textures.It is recyclable, allowing it to be reused, contributing to sustainability.
Manufacturers can swiftly make a high-quality product thanks to injection molding. It works well for extremely small manufacturing runs. You don’t have to compromise product quality in the process of manufacturing. It helps you determine what you need for a full production run.
Other AdvantagesIt is available in rigid and flexible forms, offering versatility in use, making it a popular choice for CNC machining applications.Parts made of PVC are durable and have a long service life.Unlike many other plastics, PVC is inherently flame-retardant. It is self-extinguishing, which means it stops burning when the ignition source is removed. This property is highly valued in the construction, electrical insulation, and transportation industries.PVC is relatively inexpensive compared to other engineering plastics like PEEK or PTFE. Its cost-effectiveness makes it a popular choice for large-scale applications, particularly in the construction and infrastructure sectors.
In today’s fast-paced world, product development is becoming more competitive than ever. In order to stay ahead of the competition, engineers and designers must be able to produce high-quality plastic prototypes quickly and efficiently.
The method of efficiently manufacturing products is called rapid prototyping. Rapid prototyping is a tool engineers and product designers use for all types of product development. It is a paid professional service.
Acetal, or polyoxymethylene (POM), known by the commercial trade name Delrin, is a strong, rigid plastic often used in CNC machining.ApplicationsIdeal for bearings and bushings due to its low coefficient of friction and high dimensional stability.Electrical components that require high dielectric strength and resistance to moisture.Precision parts due to dimensional stability and ease of machining.Automobile parts such as fuel system components, belt buckles, and various mechanical parts.Screws, nuts, and other fastening components for its strength and ease of threading.Various medical device components due to its biocompatibility and ease of sterilization.Valves and valve seats for applications that require precise control and resistance to wear and chemicals.PropertiesExcellent dimensional stability.Exceptional machinability.Low friction.Low moisture absorption.Other AdvantagesPOM is easy to cut, drill, and shape using CNC machining processes. It is often the best choice for CNC machining plastic parts that require high precision, stiffness, low friction, dimensional stability at elevated temperatures, and low water absorption.POM is often used for machining gears because of its high strength, low friction, and excellent wear resistance.
Determine the specific requirements of the part, including mechanical properties (strength, hardness, etc.), dimensional tolerances, surface finish etc.Consider the applicationDoes your target application have any special requirements for the parts in terms of electrical conductivity, self-lubrication, etc.?What kind of environment is the application – is it highly corrosive? Is there a high degree of exposure to UV or weathering? High heat?Are there regulatory or certification requirements?Finalize Requirements & Selection CriteriaBased on the product and application requirements, establish criteria for selecting the plastic type, considering factors such as machinability, cost, availability, and suitability for the application.Shortlist Material Options - Shortlist your potential materials and then evaluate trade-offs between material properties, cost factors, and application requirements.Consult References: Refer to material selection guides, handbooks, and databases to compare the properties of different plastics and their suitability for CNC machining.Cost Analysis: Compare the cost of each material, including raw material cost, machining costs, and any additional costs (e.g., surface treatment, post-machining operations).Final Selection: Based on the above considerations, select the plastic material that best meets the requirements for the CNC machining process.Fig. 2: Simple CNC Machined Parts Made of Plastic
Thanks to 3D printing, you may swiftly and effectively create parts for various applications. By using the appropriate 3D printing method and material combination, you may produce things with the desired mechanical properties, functional attributes, or aesthetics.
After treatment of condensation polymerization, they are also referred to as thermosets and show the primary bond between molecular chains. In thermosetting materials, polymers undergo another process known as healing, which is triggered by heat, light, or other suitable radiation. Thermosetting polymers do not melt when heated; instead, they break down and do not reform when cooled. Thermosets cannot be recycled or converted back into their original component.
CostsCost-effectiveness in material selection involves evaluating the cost per kilogram of material and the machining time required to produce the part. Some materials may have a higher initial cost but offer cost savings in terms of reduced machining time.
Reinforced plastics, such as those with fiberglass or carbon fiber, require special considerations due to their abrasive nature. These materials can cause increased tool wear and may require the use of carbide or diamond-coated tools.How does production volume impact the choice of plastic material for CNC machining?For low production volumes, CNC machining is a cost-effective method for producing plastic parts and is often used for prototyping or pilot productions due to the lack of any requirement for mold or tooling investment. However, for medium to high-volume production, other manufacturing methods such as vacuum casting or injection molding will have a definite cost advantage.Can recycled materials be used in CNC machining?Yes, certain recycled materials, such as recycled PET (rPET), can be used in CNC machining. They can offer cost savings and environmental benefits but should be evaluated for consistency and performance compared to virgin materials. In general, plastics with a high (25%+) percentage of recycled content tend to be more brittle and have degraded physical properties.
Therefore, if you are a skilled independent businessperson and can make a prototype by hand, it will only cost you in terms of time and materials.
Thermal PropertiesThermal conductivity and coefficient of thermal expansion are important for parts subjected to temperature variations. High thermal conductivity helps in dissipating heat generated during machining, while a low coefficient of thermal expansion ensures dimensional stability at different temperatures.Chemical PropertiesCorrosion resistance and chemical compatibility are crucial for parts exposed to corrosive environments or chemicals.MachinabilityFactors such as material machinability, complexity of the part, and machining time. Materials that are easy to machine, may result in shorter machining times compared to harder materials.CostsCost-effectiveness in material selection involves evaluating the cost per kilogram of material and the machining time required to produce the part. Some materials may have a higher initial cost but offer cost savings in terms of reduced machining time.
For low production volumes, CNC machining is a cost-effective method for producing plastic parts and is often used for prototyping or pilot productions due to the lack of any requirement for mold or tooling investment. However, for medium to high-volume production, other manufacturing methods such as vacuum casting or injection molding will have a definite cost advantage.Can recycled materials be used in CNC machining?Yes, certain recycled materials, such as recycled PET (rPET), can be used in CNC machining. They can offer cost savings and environmental benefits but should be evaluated for consistency and performance compared to virgin materials. In general, plastics with a high (25%+) percentage of recycled content tend to be more brittle and have degraded physical properties.
Consider the part typeIs it a bushing, an enclosure, a shaft, a gear?What are the characteristics of this type of part? Does it need to be smooth and frictionless, or is strength the priorityConsider Part UseDetermine the specific requirements of the part, including mechanical properties (strength, hardness, etc.), dimensional tolerances, surface finish etc.Consider the applicationDoes your target application have any special requirements for the parts in terms of electrical conductivity, self-lubrication, etc.?What kind of environment is the application – is it highly corrosive? Is there a high degree of exposure to UV or weathering? High heat?Are there regulatory or certification requirements?Finalize Requirements & Selection CriteriaBased on the product and application requirements, establish criteria for selecting the plastic type, considering factors such as machinability, cost, availability, and suitability for the application.Shortlist Material Options - Shortlist your potential materials and then evaluate trade-offs between material properties, cost factors, and application requirements.Consult References: Refer to material selection guides, handbooks, and databases to compare the properties of different plastics and their suitability for CNC machining.Cost Analysis: Compare the cost of each material, including raw material cost, machining costs, and any additional costs (e.g., surface treatment, post-machining operations).Final Selection: Based on the above considerations, select the plastic material that best meets the requirements for the CNC machining process.Fig. 2: Simple CNC Machined Parts Made of Plastic
Some plastics also exhibit significant dimensional instability, impacting tolerances, and some also have limited color options. There are strength considerations, resistance to stress cracking, or heat expansion. Application-specific considerations such as chemical resistance, food safety, or self-lubrication can also be an aspect.The potential cost implications and performance issues associated with incorrect material choices cannot be overstated. Using the wrong material can lead to increased scrap rates, longer lead times, and higher overall production costs. It can also result in parts that do not meet the required specifications, leading to quality issues and customer dissatisfaction.Fig. 1: CNC Machined Plastic Parts
Other AdvantagesPTFE itself is often machined in CNC machining operations to create components that require good thermal stability. It can withstand temperatures above 200 degrees Celsius without losing its mechanical properties, making it suitable for high-temperature applications where other plastics would degrade.It has the lowest coefficient of friction of any known solid material, providing excellent lubricity and making it ideal for applications such as bearings and seals.
Other Advantages:Can be easily machined, molded, and thermoformed, facilitating its use in a variety of manufacturing processes.PET is highly recyclable, contributing to environmental sustainability and making it a preferred material in industries that prioritize eco-friendly practices. Recycled rPET can be used to produce new products, reducing the environmental impact of plastic waste.
Thermal conductivity and coefficient of thermal expansion are important for parts subjected to temperature variations. High thermal conductivity helps in dissipating heat generated during machining, while a low coefficient of thermal expansion ensures dimensional stability at different temperatures.Chemical PropertiesCorrosion resistance and chemical compatibility are crucial for parts exposed to corrosive environments or chemicals.MachinabilityFactors such as material machinability, complexity of the part, and machining time. Materials that are easy to machine, may result in shorter machining times compared to harder materials.CostsCost-effectiveness in material selection involves evaluating the cost per kilogram of material and the machining time required to produce the part. Some materials may have a higher initial cost but offer cost savings in terms of reduced machining time.
What kind of technique and post-processing you need will depend on how accurately the final product must be produced. You should also think about how well your prototype compares to your finished product in terms of quality. Rapid plastic prototyping techniques provide prototype items with a high-quality surface finish.
By adding CAM software to the process, manufacturers can fully automate it. Plastic pieces may be machined at a reasonable price, and the whole process takes minimal time. CAD rendering is all you need to get started with CNC plastic prototyping.
What are the most commonly used plastics in CNC machining?Commonly used plastics in CNC machining include ABS, polycarbonate, nylon, PEEK, Delrin (acetal), and PTFE (Teflon). Each of these materials offers unique properties suitable for various applications.How do I determine which plastic is best for my project?To determine the best plastic for your project, consider factors such as mechanical properties, thermal resistance, chemical compatibility, and cost. Additionally, the specific requirements of your application, such as load-bearing capacity, wear resistance, and environmental conditions, should guide your selection.What are the advantages of using plastic over metal in CNC machining?Plastics offer several advantages over metals, including lighter weight, corrosion resistance, lower cost, and ease of machining.How does the machinability of plastics compare to metals?Plastics generally have better machinability compared to metals due to their lower hardness and density. They require less cutting force and can be machined at higher speeds, reducing tool wear and production time. However, some plastics may have specific challenges, such as melting or deforming under high temperatures, which need to be managed during machining.What surface finishes can be achieved with CNC-machined plastics?CNC-machined plastics can achieve a variety of surface finishes depending on the machining process and tools used. Common finishes include a smooth, polished finish, matte or textured finishes for improved grip or reduced glare, and precision finishes for tight tolerance parts.Are there any special considerations for machining reinforced plastics?Reinforced plastics, such as those with fiberglass or carbon fiber, require special considerations due to their abrasive nature. These materials can cause increased tool wear and may require the use of carbide or diamond-coated tools.How does production volume impact the choice of plastic material for CNC machining?For low production volumes, CNC machining is a cost-effective method for producing plastic parts and is often used for prototyping or pilot productions due to the lack of any requirement for mold or tooling investment. However, for medium to high-volume production, other manufacturing methods such as vacuum casting or injection molding will have a definite cost advantage.Can recycled materials be used in CNC machining?Yes, certain recycled materials, such as recycled PET (rPET), can be used in CNC machining. They can offer cost savings and environmental benefits but should be evaluated for consistency and performance compared to virgin materials. In general, plastics with a high (25%+) percentage of recycled content tend to be more brittle and have degraded physical properties.
Polyvinyl chloride (PVC) is a versatile thermoplastic known for its durability and chemical resistance, making it suitable for a wide range of applications including construction, healthcare, automotive, and packaging.ApplicationsOften used for fitting, valves, and couplings due to durability, chemical resistance, and ease of joining.Can be used for insulating spacers, bushings, or other parts in electrical assemblies due to its excellent electrical insulating properties.Automotive components like bushings, washers, and protective covers because of mechanical strength and resistance to oils and chemicals.Components such as pump housings, seals, and custom fittings are made from PVC to ensure their resistance to corrosive chemicals.Weather-resistant sign boards and display frames.Fittings and housings for marine environments due to PVC’s resistance to saltwater and UV exposure.HVAC system parts, such as ducting components and vent covers, are due to PVC’s lightweight and fire-resistant properties. PropertiesResistant to many acids, bases, salts, and organic solvents.Good tensile strength and impact resistance.Excellent electrical insulator.Withstands exposure to the elements, including UV radiation, without significant degradation.Absorbs very little water.Other AdvantagesIt is available in rigid and flexible forms, offering versatility in use, making it a popular choice for CNC machining applications.Parts made of PVC are durable and have a long service life.Unlike many other plastics, PVC is inherently flame-retardant. It is self-extinguishing, which means it stops burning when the ignition source is removed. This property is highly valued in the construction, electrical insulation, and transportation industries.PVC is relatively inexpensive compared to other engineering plastics like PEEK or PTFE. Its cost-effectiveness makes it a popular choice for large-scale applications, particularly in the construction and infrastructure sectors.
Additionally, prototyping is a crucial step in the creation of a product. A CAD model is a computer-generated illustration of your concept. Using a CAD model, you may evaluate how your prototype or model will fit together. It will also demonstrate how your product will work, which is more important.
We hope that this article has given you a solid understanding of plastic rapid prototyping processes. It is crucial for both the manufacturer and the client to learn about the features, advantages, and usage of their product globally. By choosing the best prototyping method and service provider, we can improve our product in line with how quickly the world is changing.
The potential cost implications and performance issues associated with incorrect material choices cannot be overstated. Using the wrong material can lead to increased scrap rates, longer lead times, and higher overall production costs. It can also result in parts that do not meet the required specifications, leading to quality issues and customer dissatisfaction.Fig. 1: CNC Machined Plastic Parts
PropertiesExcellent mechanical properties.Impact strength.Chemical resistance.Abrasion resistance.Low coefficient of friction.Susceptible to water and moisture absorption.Other AdvantagesEase of machining.Low cost.
PropertiesIt is a relatively tough but lightweight and low-cost material, able to withstand heavy impacts without shattering.Has a relatively low density, making it lightweight.Has good dimensional stability.Resistant to a wide range of chemicals, including acids and alkalis.Moderate heat resistance, with a melting point typically between 200°C to 240°C.Some ABS grades are flame retardant, making them suitable for applications where fire safety is a concern.Good electrical insulating properties.Easy to machine, drill, and cut, allowing for the creation of intricate shapes and designs.Other advantagesABS parts are often used as prototypes before mass production.One of the key advantages of ABS is its high impact strength, which allows it to withstand sudden loads and impacts without breaking or cracking. This property makes it ideal for parts that may be subjected to rough handling or impactsIt can be easily finished and painted, providing a smooth and aesthetically pleasing surface in many colors and textures.It is recyclable, allowing it to be reused, contributing to sustainability.
Are there any special considerations for machining reinforced plastics?Reinforced plastics, such as those with fiberglass or carbon fiber, require special considerations due to their abrasive nature. These materials can cause increased tool wear and may require the use of carbide or diamond-coated tools.How does production volume impact the choice of plastic material for CNC machining?For low production volumes, CNC machining is a cost-effective method for producing plastic parts and is often used for prototyping or pilot productions due to the lack of any requirement for mold or tooling investment. However, for medium to high-volume production, other manufacturing methods such as vacuum casting or injection molding will have a definite cost advantage.Can recycled materials be used in CNC machining?Yes, certain recycled materials, such as recycled PET (rPET), can be used in CNC machining. They can offer cost savings and environmental benefits but should be evaluated for consistency and performance compared to virgin materials. In general, plastics with a high (25%+) percentage of recycled content tend to be more brittle and have degraded physical properties.
Selecting the right plastic material for CNC machining is indeed a critical decision, as it significantly influences the performance, cost, and quality of the final product. Several factors need to be considered when choosing a material:Consider the part typeIs it a bushing, an enclosure, a shaft, a gear?What are the characteristics of this type of part? Does it need to be smooth and frictionless, or is strength the priorityConsider Part UseDetermine the specific requirements of the part, including mechanical properties (strength, hardness, etc.), dimensional tolerances, surface finish etc.Consider the applicationDoes your target application have any special requirements for the parts in terms of electrical conductivity, self-lubrication, etc.?What kind of environment is the application – is it highly corrosive? Is there a high degree of exposure to UV or weathering? High heat?Are there regulatory or certification requirements?Finalize Requirements & Selection CriteriaBased on the product and application requirements, establish criteria for selecting the plastic type, considering factors such as machinability, cost, availability, and suitability for the application.Shortlist Material Options - Shortlist your potential materials and then evaluate trade-offs between material properties, cost factors, and application requirements.Consult References: Refer to material selection guides, handbooks, and databases to compare the properties of different plastics and their suitability for CNC machining.Cost Analysis: Compare the cost of each material, including raw material cost, machining costs, and any additional costs (e.g., surface treatment, post-machining operations).Final Selection: Based on the above considerations, select the plastic material that best meets the requirements for the CNC machining process.Fig. 2: Simple CNC Machined Parts Made of Plastic
Yes, certain recycled materials, such as recycled PET (rPET), can be used in CNC machining. They can offer cost savings and environmental benefits but should be evaluated for consistency and performance compared to virgin materials. In general, plastics with a high (25%+) percentage of recycled content tend to be more brittle and have degraded physical properties.
How do I determine which plastic is best for my project?To determine the best plastic for your project, consider factors such as mechanical properties, thermal resistance, chemical compatibility, and cost. Additionally, the specific requirements of your application, such as load-bearing capacity, wear resistance, and environmental conditions, should guide your selection.What are the advantages of using plastic over metal in CNC machining?Plastics offer several advantages over metals, including lighter weight, corrosion resistance, lower cost, and ease of machining.How does the machinability of plastics compare to metals?Plastics generally have better machinability compared to metals due to their lower hardness and density. They require less cutting force and can be machined at higher speeds, reducing tool wear and production time. However, some plastics may have specific challenges, such as melting or deforming under high temperatures, which need to be managed during machining.What surface finishes can be achieved with CNC-machined plastics?CNC-machined plastics can achieve a variety of surface finishes depending on the machining process and tools used. Common finishes include a smooth, polished finish, matte or textured finishes for improved grip or reduced glare, and precision finishes for tight tolerance parts.Are there any special considerations for machining reinforced plastics?Reinforced plastics, such as those with fiberglass or carbon fiber, require special considerations due to their abrasive nature. These materials can cause increased tool wear and may require the use of carbide or diamond-coated tools.How does production volume impact the choice of plastic material for CNC machining?For low production volumes, CNC machining is a cost-effective method for producing plastic parts and is often used for prototyping or pilot productions due to the lack of any requirement for mold or tooling investment. However, for medium to high-volume production, other manufacturing methods such as vacuum casting or injection molding will have a definite cost advantage.Can recycled materials be used in CNC machining?Yes, certain recycled materials, such as recycled PET (rPET), can be used in CNC machining. They can offer cost savings and environmental benefits but should be evaluated for consistency and performance compared to virgin materials. In general, plastics with a high (25%+) percentage of recycled content tend to be more brittle and have degraded physical properties.
Numerous varieties of plastic are available for 3D printing, each with unique qualities that make it best suited for particular situations. The main categories of plastics used in 3D printing are described as follows:
What are the advantages of using plastic over metal in CNC machining?Plastics offer several advantages over metals, including lighter weight, corrosion resistance, lower cost, and ease of machining.How does the machinability of plastics compare to metals?Plastics generally have better machinability compared to metals due to their lower hardness and density. They require less cutting force and can be machined at higher speeds, reducing tool wear and production time. However, some plastics may have specific challenges, such as melting or deforming under high temperatures, which need to be managed during machining.What surface finishes can be achieved with CNC-machined plastics?CNC-machined plastics can achieve a variety of surface finishes depending on the machining process and tools used. Common finishes include a smooth, polished finish, matte or textured finishes for improved grip or reduced glare, and precision finishes for tight tolerance parts.Are there any special considerations for machining reinforced plastics?Reinforced plastics, such as those with fiberglass or carbon fiber, require special considerations due to their abrasive nature. These materials can cause increased tool wear and may require the use of carbide or diamond-coated tools.How does production volume impact the choice of plastic material for CNC machining?For low production volumes, CNC machining is a cost-effective method for producing plastic parts and is often used for prototyping or pilot productions due to the lack of any requirement for mold or tooling investment. However, for medium to high-volume production, other manufacturing methods such as vacuum casting or injection molding will have a definite cost advantage.Can recycled materials be used in CNC machining?Yes, certain recycled materials, such as recycled PET (rPET), can be used in CNC machining. They can offer cost savings and environmental benefits but should be evaluated for consistency and performance compared to virgin materials. In general, plastics with a high (25%+) percentage of recycled content tend to be more brittle and have degraded physical properties.
Commonly used plastics in CNC machining include ABS, polycarbonate, nylon, PEEK, Delrin (acetal), and PTFE (Teflon). Each of these materials offers unique properties suitable for various applications.How do I determine which plastic is best for my project?To determine the best plastic for your project, consider factors such as mechanical properties, thermal resistance, chemical compatibility, and cost. Additionally, the specific requirements of your application, such as load-bearing capacity, wear resistance, and environmental conditions, should guide your selection.What are the advantages of using plastic over metal in CNC machining?Plastics offer several advantages over metals, including lighter weight, corrosion resistance, lower cost, and ease of machining.How does the machinability of plastics compare to metals?Plastics generally have better machinability compared to metals due to their lower hardness and density. They require less cutting force and can be machined at higher speeds, reducing tool wear and production time. However, some plastics may have specific challenges, such as melting or deforming under high temperatures, which need to be managed during machining.What surface finishes can be achieved with CNC-machined plastics?CNC-machined plastics can achieve a variety of surface finishes depending on the machining process and tools used. Common finishes include a smooth, polished finish, matte or textured finishes for improved grip or reduced glare, and precision finishes for tight tolerance parts.Are there any special considerations for machining reinforced plastics?Reinforced plastics, such as those with fiberglass or carbon fiber, require special considerations due to their abrasive nature. These materials can cause increased tool wear and may require the use of carbide or diamond-coated tools.How does production volume impact the choice of plastic material for CNC machining?For low production volumes, CNC machining is a cost-effective method for producing plastic parts and is often used for prototyping or pilot productions due to the lack of any requirement for mold or tooling investment. However, for medium to high-volume production, other manufacturing methods such as vacuum casting or injection molding will have a definite cost advantage.Can recycled materials be used in CNC machining?Yes, certain recycled materials, such as recycled PET (rPET), can be used in CNC machining. They can offer cost savings and environmental benefits but should be evaluated for consistency and performance compared to virgin materials. In general, plastics with a high (25%+) percentage of recycled content tend to be more brittle and have degraded physical properties.
ApplicationsOften used for fitting, valves, and couplings due to durability, chemical resistance, and ease of joining.Can be used for insulating spacers, bushings, or other parts in electrical assemblies due to its excellent electrical insulating properties.Automotive components like bushings, washers, and protective covers because of mechanical strength and resistance to oils and chemicals.Components such as pump housings, seals, and custom fittings are made from PVC to ensure their resistance to corrosive chemicals.Weather-resistant sign boards and display frames.Fittings and housings for marine environments due to PVC’s resistance to saltwater and UV exposure.HVAC system parts, such as ducting components and vent covers, are due to PVC’s lightweight and fire-resistant properties. PropertiesResistant to many acids, bases, salts, and organic solvents.Good tensile strength and impact resistance.Excellent electrical insulator.Withstands exposure to the elements, including UV radiation, without significant degradation.Absorbs very little water.Other AdvantagesIt is available in rigid and flexible forms, offering versatility in use, making it a popular choice for CNC machining applications.Parts made of PVC are durable and have a long service life.Unlike many other plastics, PVC is inherently flame-retardant. It is self-extinguishing, which means it stops burning when the ignition source is removed. This property is highly valued in the construction, electrical insulation, and transportation industries.PVC is relatively inexpensive compared to other engineering plastics like PEEK or PTFE. Its cost-effectiveness makes it a popular choice for large-scale applications, particularly in the construction and infrastructure sectors.
PTFE, commonly known by the brand name Teflon, is an engineering thermoplastic. It is suitable for a variety of industrial and consumer applications.ApplicationsSeals and gaskets to make them resistant to chemicals and high temperatures.Electrical insulators and components for electronic applications.Bearings and Bushings because of their low coefficient of friction and good wear resistance.Valve Seats for fluid control applications, benefiting from its chemical inertness and ability to maintain integrity at high temperatures.Washers for applications requiring superior chemical resistance and stability.PropertiesExcellent mechanical properties.Low deformation under load.High tensile strength.Good impact resistance.Excellent electrical insulator even at high temperatures.Resistant to a wide range of chemicals, acids, and solvents.Low coefficient of friction.Other AdvantagesPTFE itself is often machined in CNC machining operations to create components that require good thermal stability. It can withstand temperatures above 200 degrees Celsius without losing its mechanical properties, making it suitable for high-temperature applications where other plastics would degrade.It has the lowest coefficient of friction of any known solid material, providing excellent lubricity and making it ideal for applications such as bearings and seals.
Selecting the right plastic material involves a step by step consideration of the application, the part type and geometry, and the final performance required. The good news is that by following our guidelines, and with the right feedback from your machining supplier, highlighting the best options aren’t as difficult as it appears.
This plastic CNC machining technique is incredibly adaptable and practical for a wide range of product sizes, complexity, and threaded features, and it is especially well-suited to prototypes that need to meet strict tolerance requirements.
Consider the applicationDoes your target application have any special requirements for the parts in terms of electrical conductivity, self-lubrication, etc.?What kind of environment is the application – is it highly corrosive? Is there a high degree of exposure to UV or weathering? High heat?Are there regulatory or certification requirements?Finalize Requirements & Selection CriteriaBased on the product and application requirements, establish criteria for selecting the plastic type, considering factors such as machinability, cost, availability, and suitability for the application.Shortlist Material Options - Shortlist your potential materials and then evaluate trade-offs between material properties, cost factors, and application requirements.Consult References: Refer to material selection guides, handbooks, and databases to compare the properties of different plastics and their suitability for CNC machining.Cost Analysis: Compare the cost of each material, including raw material cost, machining costs, and any additional costs (e.g., surface treatment, post-machining operations).Final Selection: Based on the above considerations, select the plastic material that best meets the requirements for the CNC machining process.Fig. 2: Simple CNC Machined Parts Made of Plastic
Corrosion resistance and chemical compatibility are crucial for parts exposed to corrosive environments or chemicals.MachinabilityFactors such as material machinability, complexity of the part, and machining time. Materials that are easy to machine, may result in shorter machining times compared to harder materials.CostsCost-effectiveness in material selection involves evaluating the cost per kilogram of material and the machining time required to produce the part. Some materials may have a higher initial cost but offer cost savings in terms of reduced machining time.
To determine the best plastic for your project, consider factors such as mechanical properties, thermal resistance, chemical compatibility, and cost. Additionally, the specific requirements of your application, such as load-bearing capacity, wear resistance, and environmental conditions, should guide your selection.What are the advantages of using plastic over metal in CNC machining?Plastics offer several advantages over metals, including lighter weight, corrosion resistance, lower cost, and ease of machining.How does the machinability of plastics compare to metals?Plastics generally have better machinability compared to metals due to their lower hardness and density. They require less cutting force and can be machined at higher speeds, reducing tool wear and production time. However, some plastics may have specific challenges, such as melting or deforming under high temperatures, which need to be managed during machining.What surface finishes can be achieved with CNC-machined plastics?CNC-machined plastics can achieve a variety of surface finishes depending on the machining process and tools used. Common finishes include a smooth, polished finish, matte or textured finishes for improved grip or reduced glare, and precision finishes for tight tolerance parts.Are there any special considerations for machining reinforced plastics?Reinforced plastics, such as those with fiberglass or carbon fiber, require special considerations due to their abrasive nature. These materials can cause increased tool wear and may require the use of carbide or diamond-coated tools.How does production volume impact the choice of plastic material for CNC machining?For low production volumes, CNC machining is a cost-effective method for producing plastic parts and is often used for prototyping or pilot productions due to the lack of any requirement for mold or tooling investment. However, for medium to high-volume production, other manufacturing methods such as vacuum casting or injection molding will have a definite cost advantage.Can recycled materials be used in CNC machining?Yes, certain recycled materials, such as recycled PET (rPET), can be used in CNC machining. They can offer cost savings and environmental benefits but should be evaluated for consistency and performance compared to virgin materials. In general, plastics with a high (25%+) percentage of recycled content tend to be more brittle and have degraded physical properties.
ApplicationsSeals and gaskets to make them resistant to chemicals and high temperatures.Electrical insulators and components for electronic applications.Bearings and Bushings because of their low coefficient of friction and good wear resistance.Valve Seats for fluid control applications, benefiting from its chemical inertness and ability to maintain integrity at high temperatures.Washers for applications requiring superior chemical resistance and stability.PropertiesExcellent mechanical properties.Low deformation under load.High tensile strength.Good impact resistance.Excellent electrical insulator even at high temperatures.Resistant to a wide range of chemicals, acids, and solvents.Low coefficient of friction.Other AdvantagesPTFE itself is often machined in CNC machining operations to create components that require good thermal stability. It can withstand temperatures above 200 degrees Celsius without losing its mechanical properties, making it suitable for high-temperature applications where other plastics would degrade.It has the lowest coefficient of friction of any known solid material, providing excellent lubricity and making it ideal for applications such as bearings and seals.
GETTING A QUOTE WITH LK-MOULD IS FREE AND SIMPLE.
FIND MORE OF OUR SERVICES:
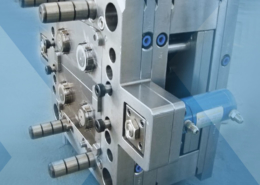
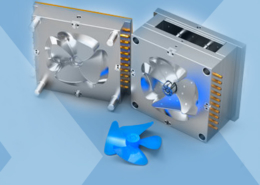
Plastic Molding

Rapid Prototyping
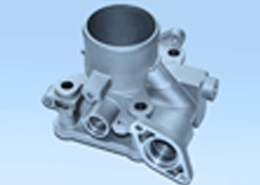
Pressure Die Casting
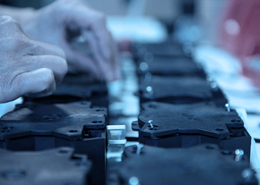
Parts Assembly
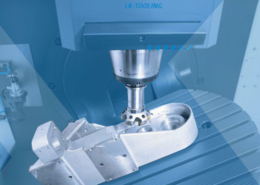