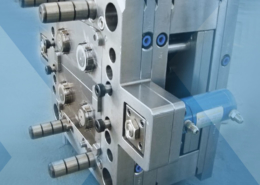
Unveiling the Potential of Ejector Rod Injection Molding
Author:gly Date: 2024-06-08
Introduction
Ejector rod injection molding stands as a pivotal advancement in the realm of plastic injection molding, revolutionizing the production of intricate and high-quality plastic components. This innovative technique involves the integration of ejector rods into the mold design, facilitating the ejection of molded parts with enhanced precision, efficiency, and reliability. As industries continue to push the boundaries of design complexity and manufacturing efficiency, the application of ejector rod injection molding emerges as a game-changer. In this article, we embark on a comprehensive exploration of ejector rod injection molding, unraveling its mechanisms, applications, advantages, challenges, and future prospects.
Mechanisms of Ejector Rod Injection Molding
Integration of Ejector Rods
Ejector rod injection molding distinguishes itself through the incorporation of ejector rods within the mold assembly. These rods, strategically positioned within the mold cavity, serve as dynamic elements that facilitate the ejection of molded parts upon completion of the injection molding process. By applying controlled force through the ejector rods, manufacturers can ensure precise and consistent part ejection, minimizing the risk of damage or deformation to the molded components.
Dynamic Ejection Control
Central to the effectiveness of ejector rod injection molding is the dynamic control of ejection forces throughout the molding cycle. Advanced molding machines equipped with servo-driven ejector systems enable precise adjustment of ejection speed, force, and timing, tailored to the specific requirements of each part design. This dynamic control mechanism ensures optimal part release while minimizing cycle times and maximizing production efficiency.
Parting Line Optimization
The design and placement of ejector rods within the mold assembly play a crucial role in optimizing parting line geometry and minimizing flash formation. By strategically positioning ejector rods along the parting line, manufacturers can exert uniform pressure during ejection, effectively sealing off the mold cavity and preventing plastic leakage or flash formation. This meticulous attention to parting line optimization enhances part quality and dimensional accuracy while streamlining post-processing operations.
Applications of Ejector Rod Injection Molding
Complex Geometries
Ejector rod injection molding excels in the production of components with intricate geometries and undercuts, where traditional ejection methods may prove inadequate. By leveraging the controlled ejection forces exerted by ejector rods, manufacturers can effectively release complex parts without compromising on design integrity or dimensional accuracy. This capability makes ejector rod injection molding ideal for applications in automotive, aerospace, and consumer electronics industries, where design complexity is paramount.
Multimaterial Overmolding
In the realm of multimaterial overmolding, ejector rod injection molding offers unparalleled versatility and precision. By integrating ejector rods into the mold design, manufacturers can achieve seamless bonding between different thermoplastic materials, creating robust and aesthetically pleasing multi-component assemblies. This capability opens up new possibilities for product innovation and differentiation across various industries, including medical devices, consumer goods, and industrial equipment.
High-Volume Production
The efficiency and reliability of ejector rod injection molding make it well-suited for high-volume production environments, where consistent part quality and cycle time optimization are paramount. By incorporating advanced automation and robotics systems, manufacturers can further enhance production throughput and minimize downtime, maximizing the return on investment in ejector rod injection molding technology. This scalability and efficiency make it a preferred choice for applications requiring large quantities of precision-engineered plastic components.
Advantages and Challenges
Advantages
Enhanced Precision
: Ejector rod injection molding enables precise and consistent part ejection, ensuring dimensional accuracy and surface finish quality.
Optimized Cycle Times
: Dynamic ejection control mechanisms minimize cycle times, maximizing production efficiency and throughput.
Versatile Applications
: From complex geometries to multimaterial overmolding, ejector rod injection molding offers versatility across a wide range of industries and applications.
Challenges
Tooling Complexity
: Designing and fabricating molds with integrated ejector rod systems can be challenging and may require specialized expertise and equipment.
Process Optimization
: Fine-tuning ejection parameters and parting line design to minimize flash formation and maximize part quality requires iterative testing and optimization.
Cost Considerations
: The initial investment in ejector rod injection molding technology and tooling may be substantial, necessitating careful cost-benefit analysis for adoption in production environments.
Conclusion
Ejector rod injection molding represents a significant advancement in plastic injection molding technology, offering unprecedented precision, efficiency, and versatility. From intricate geometries to multimaterial overmolding, this innovative technique enables manufacturers to push the boundaries of design complexity and production efficiency, driving innovation across various industries and applications. As the demand for high-performance plastic components continues to rise, the application of ejector rod injection molding is poised to play a pivotal role in shaping the future of manufacturing.
By embracing the principles of continuous improvement and technological innovation, manufacturers can unlock the full potential of ejector rod injection molding, driving advancements in product design, performance, and sustainability. Through collaborative research, development, and knowledge sharing, the industry can address current challenges and explore new frontiers in ejector rod injection molding technology, paving the way for enhanced productivity, competitiveness, and market differentiation.
GETTING A QUOTE WITH LK-MOULD IS FREE AND SIMPLE.
FIND MORE OF OUR SERVICES:
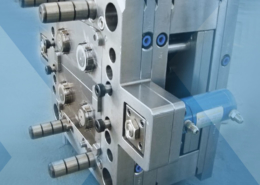
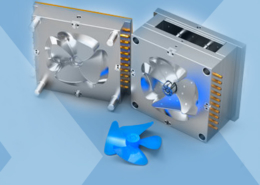
Plastic Molding

Rapid Prototyping
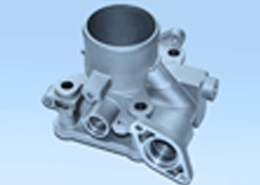
Pressure Die Casting
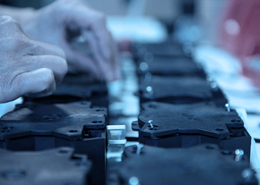
Parts Assembly
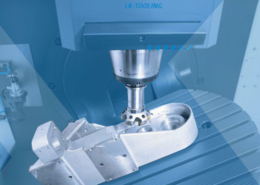