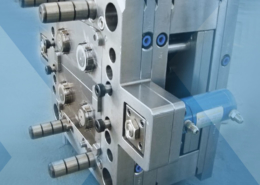
Low Volume Injection Molding Machines - low cost plastic injection molding
Author:gly Date: 2024-10-15
There are many diverse types of materials that can be used in injection molding medical devices. Some useful and commonly used materials include:
1) LCD computer control with big display screen2) Hydraulic double proportional valve3) Hard chrome plated high tensile strength steel tie bars4) Generous space for fitting large moulds5) Large opening stroke6) Two position transducers to control Clamping and Injection7) Four stages of injecting, independent velocity and pressure control8) Hydraulic mould height adjustment device9) Screw cold-start prevention device10) Melt decompression control11) Screw back pressure control12) Multiple hydraulic ejection13) Differential high speed clamping14) Centralized lubrication system15) Low pressure mould protection device16) Mechanical safety interlock17) Double electrical safety interlock18) Oil return filter19) Oil tank with inner stainless steel container
Clamping Unit5-point twin toggle clamping system by modular optimization software designing.Strong clamping with rapid and stable, tomeet the strict clamping condition.Mould height adjustment by hydraulic driven gear system with rapid and stable.Automatic mould height adjustment as per the setting clamping force(optional).Injection UnitBaIanced double injection cylinder technology makes screw to have evenly distributed force during fast injection,Five_star Hydraulic motor with big torque,Ensure the excellent plastic molding condition.Research and develop different screws according to difierent iniection condition, suitable for the progressive demand and greatly improve the injection quality.Control UnitImported computer special for Injection Molding Machine with multiple functions and precise control processing.World famous electrical components and high quality circuit hardware with stable and reliable running.
Plastic injection molding is widely used in the medical device industry. Plastics are often used alongside the injection molding process to produce prototypes and full-production units of medical devices and equipment components. As newer plastic materials and component designs are developed, injection molding medical devices has increasingly contributed to lower infectious disease rates, and lower medical costs.
1.Can your factory provide he whole plant from A to Z?Yes, we can provide the complete plant, from bottling making plant,water purification plant,to filling packing plant.2.Are all machinery your factory made?Our factory make the water purification and filling packing plants.we do not make the bottle making machinery,we have good quality bottle making machinery partner,and we provide to customer same long warranty time and good after service.3.How can I know the machinery quality before i order?First,we will invite you visiting our factory to check the machines quality,and show the machines running for you in our factory.4.What certificates you can provide?Our factory provide the CE,SGS,ISO,and according to some countries,we also can provide the PVOC, COC,SONCAP...etc.
Injection molding is a method to obtain molded products by injecting plastic materials molten by heat into a mold, and then cooling and solidifying them. The method is used for mass production of products with complicated shapes and plays a large part in plastic processing. Injection molding for medical devices can be performed by using many sorts of materials such as metals, confections, and most commonly thermoplastic and thermosetting polymers.
Industrial Plastic Water Bottle Caps Injection Molding Machine adopts proportional pressure and flow control, the pressure and the speed can be adjusted, stable movement curve and gentle shock, the computer is imported from Industry family.The LCD displaying screen with high clarity has Chinese and English language to use.Close-loop PID temperature control with the advantage of high precision.The operating table of the injection moulding machine have two safety, one is machine safety, another is electrical safety, that ensures the operators's safety.
Gilero provides a range of manufacturing services, including plastic injection molding and injection mold tool building. We focus solely on the medical device and drug delivery markets. Our medical injection molding facilities follow strict design protocols and process controls to ensure that all products meet the required specifications. Depending on client needs and product requirements, we can offer manual or fully automated production lines for molding and assembly.
Medical device injection molding also has many other advantages, such as compliance with industry standards and regulations. Engineering-grade plastics can be used in the process to create parts that enhance patient safety and comply with FDA (Food and Drug Administration) guidelines. There is flexibility with injection molding, as the parts can be fully customizable to fit the user. The ability to fulfill high-volume orders with high accuracy and precision is also an advantage of injection molding medical devices. In addition, injection molding is a cost-effective manufacturing method. With automation technology and energy-efficient equipment, we further reduce our labor and utility costs.
GETTING A QUOTE WITH LK-MOULD IS FREE AND SIMPLE.
FIND MORE OF OUR SERVICES:
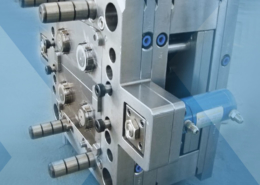
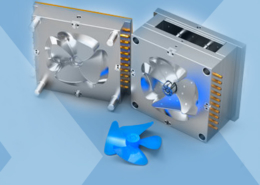
Plastic Molding

Rapid Prototyping
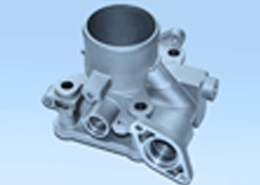
Pressure Die Casting
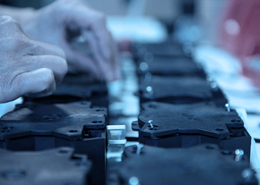
Parts Assembly
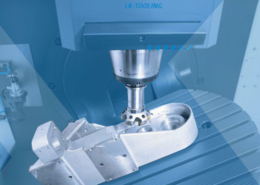