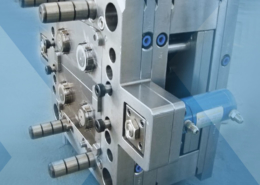
Low Volume Injection Molding: Cost-Effective Solutions For ... - small scale inj
Author:gly Date: 2024-10-15
One of our experts will be happy to discuss the specifics of your project in detail. Contact SIMTEC by phone or email to get started today.
In conclusion, overmolding is a versatile and widely used plastic molding technique that enhances product functionality and aesthetics. Despite its complexity, with proper material selection, precise mold design, and attention to key issues like adhesion, short shots, and flash, overmolding offers significant benefits.
This makes 2-shot molding more efficient and labor-saving. Additionally, since the substrate remains hot during overmolding in 2-shot processes, it often results in a stronger bond between the substrate and overmolding material.
Commonly, the substrate in overmolding is a hard plastic like PA or PC. The overmolded material, however, can be a flexible plastic such as TPE or TPU, or even another hard material.
There are instances of double overmolding as well, which necessitates three molds, resulting in a product composed of three materials or color variations.
The substrates in over-molding often include materials like PA, PC, ABS/PC, and ABS, while TPE, TPU, TPR, and TPO are common choices for the overmolding layer. This blend of soft and hard plastics represents the most typical form of overmolding.
Poor Adhesion: This issue often arises due to incompatibility between materials. For different materials, compatible overmolding materials must be selected. Additionally, a low temperature of the substrate’s surface can lead to poor adhesion. On the other hand, excessively strong adhesion can create recycling challenges for the product.
In traditional overmolding, the substrate is first injection molded, removed from the mold, and then manually placed into another mold for overmolding.
SIMTEC’s ISO-certified Class 8 cleanroom mitigates the risk of parts contamination from dust and other airborne particles, and meets the stringent ISO standards necessary for hygienic manufacturing.
Since 2002, SIMTEC has manufactured billions of custom silicone components of all sizes and complexities. Our high-capacity molds and fully-automated injection molding technology and class 8 clean room allow us to meet our customers high volume, hygienic production requirements. With our manufacturing facility and office headquarters in Miramar, Florida we are located minutes from all major transportation hubs, allowing us to facilitate the delivery of your parts to anywhere in the world.
Theoretically, the possibilities extend beyond these mentioned materials. Essentially, any plastic can be used for over-molding. For specific requirements, please feel free to contact us for more information.
Additionally, in scenarios where the maximum thickness of an injection-molded product is exceeded, a two-shot injection molding process may be used. This approach ensures each individual molding stays within the maximum allowable thickness.
Insert molding typically involves inserting pre-fabricated parts, often made of metals like copper or stainless steel, into an injection mold. These parts can also be made from other materials such as glass, wood, or fiber.
Overmolding, also called plastic overmolding, molding over molding, or injection overmolding, is a crucial injection molding technique widely used in everyday items like toothbrushes, power tool housings, and car light panels. This article will explain overmolding, highlighting its common challenges and essential precautions.
For specific, information about LSR’s suitability for medical device injection molding, we recommend visiting our technical information page or contacting us directly.
High precision LSR medical device injection molding enables the manufacturing of perfectly uniform components directly out of the machine. The flexibility of the material is ideal for valves, diaphragms, and other silicone medical products which need to yield under pressure but fully close when pressure is released. Because LSR is inert and has superior physical properties it is also perfectly suited for components that come into contact with chemicals, blood, and bodily fluids such as connectors, seals, gaskets, and impellers used in dialysis filters and infusion pumps.
In summary, while overmolding technology offers enhanced functionality and aesthetics, it also brings challenges in cost, design, and material selection.
Conversely, a gap that is too small or negative, such as -0.01 to -0.02mm, can create indentations on the substrate surface. Therefore, the mold must be manufactured with high accuracy.
In addition to silicone medical device injection molding, we also provide a full portfolio of value-added services including early design and prototyping support, high-capacity, class 101 molds, custom injection molded LSR, LSR multi-shot and LSR overmolded components, and a variety of secondary processes performed in-line for added precision and value.
With our focus on the highly customized production of injection-molded silicone medical parts, we tailor our QA processes.
While theoretically, overmolding can be repeated multiple times, such practices are rare in real-world applications and are not the focus of this discussion.
Overmolding is a widely used plastic molding process with many advantages but also some limitations. Here are the main pros and cons of overmolding:
Overmolding is a process where a substrate, typically a pre-formed plastic part, is placed inside a mold. During the process, molten plastic is injected into the mold cavity, enveloping the substrate in the empty areas. Once cooled, the two materials fuse into a single product.
Medical, healthcare and life science companies have high expectations – parts must adhere to increasingly tight tolerances and meet cleanliness requirements. Compared to other materials and processes, medical grade LSR coupled with SIMTEC’s advanced molding technology, class 8 clean room, and highly automated LSR/LSR 2-shot / multi-shot manufacturing provide greater clarity, chemical resistance, purity, and value for high precision silicone components.
Overmolding usually involves a single overlay, requiring two injection molds. The final product is a combination of two materials or two color variations of the same material.
Components used in surgical, medical and healthcare devices have strict requirements. Clean, hands-free manufacturing, biocompatible medical grade materials, and in some cases post-curing and sterilization post-molding processes are also required. SIMTEC’s ISO 13485 certified quality and environmentally-controlled LSR, LSR multi-shot and LSR overmolding manufacturing cells meet these requirements. Our fully automated hands-free injection molding, and ISO class 8 clean room ensure precision accuracy, high quality and protect critical components from dust, particles, and contaminants.
2-shot molding combines both substrate molding and overmolding in a single injection molding machine. Here, after the substrate is molded, it’s rotated to another station within the same machine for overmolding, eliminating the need to manually transfer the substrate.
It’s crucial that the overmolding material has a melting point equal to or lower than the substrate’s. Using the same material for both is possible, but it requires careful adjustment of the injection molding temperature to prevent the substrate from partially melting.
Precision Fit Between Substrate and Mold: The fit between the substrate and the mold cavity in overmolding needs to be very precise. The gap between the substrate and the mold cavity after inserting the substrate should be between 0.01 to 0.03mm. This precision is crucial because materials like TPE, known for their fluidity, can easily cause flash if the gap is too large.
Understanding the nuances between overmolding, insert molding, and 2-shot molding is crucial for selecting the right process for specific applications, balancing efficiency, cost, and production volume.
From this distinction, it’s evident that insert molding usually requires just one injection mold, whereas overmolding necessitates at least two, and occasionally three, molds.
Liquid Silicone Rubber is ideal for medical injection molded components, such as tubing connectors. The main characteristics of LSR that benefit this type of application include high purity, transparency, flexibility, and inertness.
Unlike many natural rubber/latex products, Liquid Silicone Rubber’s molecular structure is composed of an inorganic backbone, and it is naturally stable, hypoallergenic and bio-compatible, which makes it an ideal material for silicone medical devices with skin contact applications, such as respirator masks and other respiratory devices.
Flash: Excessive gaps between the mold cavity and the substrate can lead to flash (excess plastic). Moreover, if the gate design is improper, leading to excessive injection pressure (to avoid short shots), it can also result in flash.
Multi-component molding offers the benefits of improved part quality and consistency. Complicated assemblies can be eliminated by direct mechanical and chemical bonding of LSR onto plastics or metal, thereby reducing assembly time and costs. Over-molding LSR onto surgical tool handles provides added grip strength for increased accuracy and comfort, while at the same time providing a surface that can be sterilized or auto-claved. Multi-component valves, washers, and seals also benefit from LSR’s material properties and the reduced assembly steps of LSR 2-Shot medical device injection molding or over-molding.
Short Shot: Even a slight inadequacy in the injection can cause aesthetic defects, leading to product rejection. It’s crucial to design the gate location thoughtfully to prevent short shots. A Design for Manufacturability (DFM) assessment can be used to evaluate the suitability of gate placement, focusing mainly on the required injection pressure.
It’s also possible to use hard plastics for both the substrate and the overmold, usually the same material, often employed in multi-color combinations for aesthetic appeal.
However, 2-shot molding requires highly precise molds and thus involves greater initial investment costs. Therefore, the choice between these methods depends on the production volume:
To mitigate adhesion issues, it’s common to design holes or grooves at the edges of the overmolded area. These features, being larger internally, help to lock the overmold in place and reduce the reliance on adhesive strength, making it easier for the overmold to bond with the substrate.
Creating molds for overmolding requires higher precision and a thorough understanding of the overmolding materials. The following are essential aspects to consider in overmolding mold design:
Gate Design in Overmolding: The design of the gates in overmolding molds is highly critical. They must ensure complete filling while maintaining sufficient adhesive force. The key is to ensure that all areas to be overmolded are not too far from the gates. This is to avoid insufficient injection pressure or too low temperatures in those areas, which could affect the quality of the over molding.
Liquid Silicone Rubber (LSR) is naturally inert, resistant to many substances, and bio-compatible, making it an ideal choice for a wide range of medical and healthcare devices, mother and child care products, sanitary and others with hygienic requirements. For some medical and healthcare products, hygiene is critical and requires production in a hygienic, environmentally controlled environment.
Although insert molding and 2-shot molding fall under overmolding, they are often referred to separately. In a narrower definition, overmolding specifically involves a plastic substrate manually placed into the mold.
To meet these needs, SIMTEC Silicone Parts offers LSR and LSR Multi-Shot molding in its ISO-certified Class 8 Clean Room.
Using the right design and LSR material for syringe stoppers and plugs ensure optimal sealing pressure and friction. LSR’s low compression set and superior strength make the material perfect for silicone medical products, such as syringe stoppers. Our automated, high-precision injection molding technology ensures consistent, repeatable, high-quality parts. In-line assembly or direct over-molding can add value for syringe stopper applications by reducing or eliminating assembly costs and errors.
GETTING A QUOTE WITH LK-MOULD IS FREE AND SIMPLE.
FIND MORE OF OUR SERVICES:
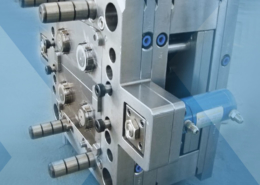
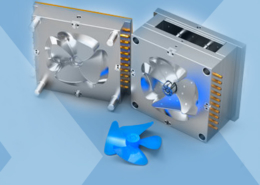
Plastic Molding

Rapid Prototyping
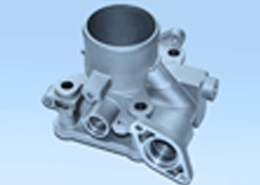
Pressure Die Casting
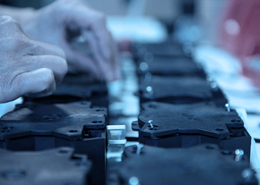
Parts Assembly
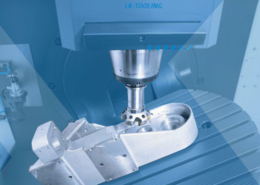