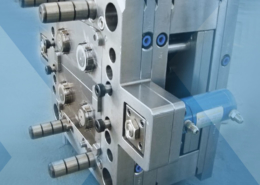
Unlocking the Potential of Double Shot Injection Molding
Author:gly Date: 2024-06-08
Double shot injection molding, a sophisticated manufacturing process, has emerged as a versatile solution for producing complex plastic parts with enhanced functionality and aesthetics. In this article, we delve into the realm of double shot injection molding, exploring its principles, applications, advantages, challenges, and future prospects.
Introduction
Double shot injection molding, also known as two-shot molding or dual-material molding, involves the sequential or simultaneous injection of two different materials or colors into a single mold to create a composite part. This innovative technique offers manufacturers the ability to integrate multiple materials with diverse properties, such as soft and rigid plastics, or different colors, into a single component, thereby enhancing design flexibility and product performance. As we embark on a journey to explore the intricacies of double shot injection molding, we unravel its potential to revolutionize the manufacturing landscape.
Principles of Double Shot Injection Molding
At the heart of double shot injection molding lies a series of intricate processes and principles aimed at achieving precise control and synchronization of material injection. The process typically begins with the injection of the first material, forming the substrate or base component, followed by the injection of the second material to create the overmolded or encapsulated feature. The sequence, timing, and coordination of material injection, as well as the design of the mold and the selection of compatible materials, are critical factors that influence the quality and performance of double shot molded parts.
Advantages and Applications
Double shot injection molding offers several advantages over traditional injection molding techniques, including improved part quality, reduced assembly costs, enhanced design flexibility, and increased product functionality. By integrating multiple materials with complementary properties, such as hardness, flexibility, or texture, manufacturers can create innovative products with superior performance and aesthetics. Common applications of double shot injection molding include soft-touch handles, multi-color buttons, automotive interior trim, medical device housings, and consumer electronics components.
Challenges and Considerations
Despite its many benefits, double shot injection molding presents unique challenges and considerations that must be addressed to ensure successful implementation. These include mold design complexity, material compatibility, shot-to-shot consistency, and process validation. Additionally, the selection of suitable materials and additives, as well as the optimization of processing parameters, are critical factors that influence the quality and reliability of double shot molded parts. By leveraging advanced simulation tools, mold flow analysis, and real-time monitoring systems, manufacturers can mitigate risks and optimize the double shot injection molding process for maximum efficiency and performance.
Future Prospects and Innovations
Looking ahead, the future of double shot injection molding is ripe with opportunities for innovation and advancement. Emerging trends such as additive manufacturing, bio-based polymers, and smart materials hold promise for expanding the capabilities and applications of double shot injection molding. Moreover, ongoing research and development efforts aimed at improving material compatibility, cycle times, and part quality will further drive the adoption of double shot injection molding in various industries. By staying abreast of technological developments and market trends, manufacturers can harness the full potential of double shot injection molding to stay ahead of the competition and meet the evolving needs of customers.
Conclusion
In conclusion, double shot injection molding stands as a versatile and innovative manufacturing technique that enables the production of complex plastic parts with enhanced functionality and aesthetics. With its ability to combine multiple materials or colors in a single process, double shot injection molding offers manufacturers a competitive edge in product design, performance, and differentiation. By understanding the intricacies of the double shot injection molding process and embracing advancements in materials, equipment, and technology, manufacturers can unlock new opportunities for innovation and growth in the dynamic world of injection molding.
Through this exploration, we gain a deeper understanding of the potential of double shot injection molding to transform the way products are designed, manufactured, and experienced. As we look to the future, the continued evolution of double shot injection molding holds promise for driving progress and innovation in the manufacturing industry, shaping the way we create and interact with products in the years to come.
GETTING A QUOTE WITH LK-MOULD IS FREE AND SIMPLE.
FIND MORE OF OUR SERVICES:
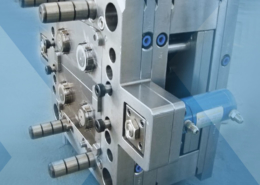
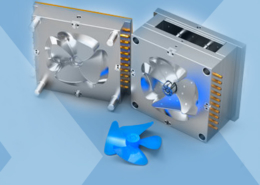
Plastic Molding

Rapid Prototyping
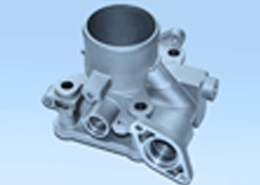
Pressure Die Casting
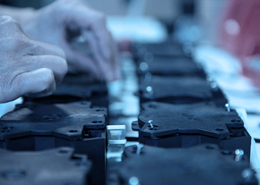
Parts Assembly
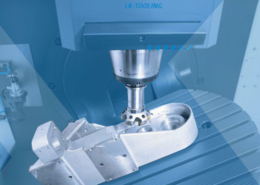