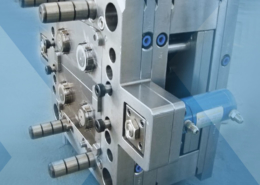
LLDPE Injection Molding Guide(2024) - polyethylene injection molding
Author:gly Date: 2024-10-15
Of course, there is also a certain percentage of waste (e.g., 3%) during the injection molding process, but because the proportion is relatively small, it can be ignored when estimating costs.
Different products have different tolerance standards, with higher precision leading to higher costs. The cost of a mold with a tolerance of ±0.2mm will certainly differ from that of a mold with a tolerance of ±0.02mm.
The cost of plastic molds, like all products, is “you get what you pay for.” The more complex, precise, and durable the mold, the higher the cost.
Today, we will mainly introduce the cost structure of injection molding factories. If you are a peer in the injection molding industry, you are also welcome to read the latter part of the article about how injection molders can reduce injection molding costs.
Our experienced design, tooling, molding, and assembly team along with the latest molding technologies offer aerospace and defense manufacturers the ability to out perform competitors in a highly demanding market with the highest quality aerospace plastic injection molded parts.
A more complex example: Assuming the cost of ABS plastic pellets is $1500 per ton. A mold produces parts in a 1-to-4 ratio, with each part weighing 200 grams and the runner material for 1-to-4 being 100 grams. What is the cost of raw materials per part? The calculation method is to account for each part’s weight as 200 grams + 25 grams of runner material, totaling 225 grams, and then calculate the cost as described above.
If the product structure is simple and the quantity to be produced is small, a one-to-one cavity mold can be used, which will be relatively cheaper.
The volume and weight of the packaged plastic products, as well as the method of transportation, will affect transportation costs.
Controlling injection molding costs is a shared responsibility between factories and product designers. The majority of methods to save on injection molding costs come from the injection molding factory. Here are some suggestions for reducing injection molding costs provided to injection molding factories as peers.
I am Li Yang. If you are interested in the injection molding service quotation from FirstMold, please click “Injection Molding Service Quotation“.
For example: Assuming ABS plastic pellets cost $1500 per ton (this is an example, please refer to the actual local price). If the shell weight of a product after injection molding is 200 grams, then the raw material cost of the product is $1500 / 1000000 * 200 = 0.0015 * 200 = $0.3.
General-purpose plastic raw materials are relatively inexpensive. If the plastic raw material has high strength and strong chemical resistance, the cost will be higher (including some modified materials).
Because this process produces semi-finished products that require further processing, there may be an increased risk of defects in the coating process. An economically viable suggestion is, if you want to save costs and achieve a beautiful finish, consider adding colorants directly to the raw material. This eliminates the need for secondary processing while still allowing for the production of products in various colors.
The more cavities on a mold, the higher the complexity and precision of mold development, and consequently, the mold price will be higher.
If the product needs to be produced in large quantities, it is recommended to develop a mold with multiple cavities. Although the cost of mold development may be relatively higher, the production efficiency will be faster. Additionally, due to large-scale production, the unit price of the product can be reduced. Comparisons based on the number of cavities can be seen in the table below: The number of cavities represents the quantity of products produced at once, with lower costs for higher production quantities. If you are still unsure, just tell the plastic injection molding factory the estimated production volume, and an experienced plastic injection molding factory will help you calculate the most suitable number of mold cavities.
Employee wages are a relatively easy part to calculate. The wages of employees involved in mold design, mold processing, etc., are calculated as part of the mold cost. However, the wages of employees in the injection molding production workshop are only calculated as part of the company’s operational costs when the customer commissions injection molding production. For example, depending on the characteristics of different products, some products may require workers to be stationed at the injection molding discharge position for processing. Common processing steps include trimming runners, visual inspections, packaging, etc.
We have previously detailed the costs of injection molds. For product design companies or companies outsourcing plastic part production, they are more likely to commission injection molding factories to provide plastic injection molding services for their products, rather than just commissioning the factory to produce injection molds. After all, the mold is one part of the entire injection molding production process. Therefore, they are more concerned with the injection molding costs.
Factors affecting the cost of plastic molds include: size, complexity, material, expected quantity, and different mold cavity numbers and tolerance requirements also affect cost. For detailed mold costs, please refer to the article “Injection Mold Costs”.
Trying to find the best plastic injection molding companies in America with aerospace/defense experience? As injection molding experts, you can have peace of mind knowing Plastimold is taking care of manufacturing your product. Our approach to producing plastic injection molds in both China and the USA allows us to rapidly construct the most economical mold for your application. All production injection molded parts are made in the USA at our Delray Beach, Florida facility.
Assuming the price of an injection molding machine is $100,000, then the daily machine cost is $100,000 / 5 / 180 = $111. If the injection molding machine works 22 hours per day, the hourly cost is approximately $5. Based on the hourly output of one injection molding machine (related to the layout of the mold and the molding time), the injection molding cost per part can be calculated.
As for other complex company operational costs, each company will have its own calculation standards. These costs are usually calculated by the factory’s finance department, with a rough formula to distribute the results evenly among each injection molded part.
The operational costs of a company are very complex and include employee wages, rental costs, electricity bills, administrative expenses, etc.
For example, for a mold with a 1-to-1 layout and a molding time of 60 seconds, only 60 parts can be produced in one hour. So, the machine cost per part is $100,000 / 60 = $0.08.
The cost composition of injection molding is actually quite transparent in the industry, mainly including: plastic mold costs, molding costs, secondary processing costs, raw material costs, packaging and transportation costs, and factory operation costs.
The packaging of plastic injection molded products generally includes plastic bags and cardboard boxes for semi-finished parts. For assembled components, there is the cost of assembly equipment. The more complex the product, the longer the assembly time, which may result in higher costs and affect the overall expense.
We offer other value added services such as Precision CNC machining, product assembly for final and sub assemblies, part marking, and fulfillment services. Plastimold is ISO9001 and ISO 13485 certified and compliant to AS9100. To make things more efficient, Plastimold Products can pick, label, and ship your parts to your end customers.
Regarding the specific cost of raw materials consumed by injection molded products, this part of the raw material cost can be deduced from the weight of the molded shells in injection molding.
We can calculate the annual injection molding cost based on a 5-year depreciation of the injection molding machine. For example, if the industry’s startup rate for the injection molding machine is 50% (i.e., 180 days per year), divide the annual depreciation of the injection molding machine by 180 days to calculate the daily machine cost.
With the development of digital marketing, the prices of injection molding processes online are becoming more transparent. Understanding the costs of injection molding processes helps product design companies create better products and encourages injection molding factories to adhere to industry standards, creating a positive atmosphere for the injection molding industry.
Some clients who frequently outsource injection molding production also often feel confused about how to evaluate the cost of plastic injection products, and they may doubt whether the quotations from plastic injection manufacturers are reasonable. This confusion stems from a lack of understanding of the cost structure of plastic injection products, leading to clients spending a lot of time and energy when asking for quotes from manufacturers, and sometimes they have to pay the cost of trial and error to gain experience.
Note: If the mold used for injection molding has a cold runner system, there will be residual material in the runners after each injection molding cycle. When calculating, the weight of the runner material should also be included.
Some plastic injection molding factories also provide finishing services, including surface treatments such as coating, printing, painting, and electroplating.
It is also important to note that there is a basic operation time for mold setup and removal. The time required depends on the size and function of the mold. If the order quantity is lower than the cost of changing the mold, there may be additional costs. However, plastic injection molding manufacturers usually clarify the minimum purchase quantity in advance.
It is worth mentioning that if the quantity of plastic parts produced is not large, the cost of the mold will account for a relatively large proportion of the total price; if the quantity of plastic parts produced is large enough, many factories may even waive the mold cost.
The cost of raw materials depends on the functionality and requirements of the product. Common plastic raw materials include PP, PE, PC, ABS, PBT, and dozens of others. All plastic raw materials are influenced by fluctuations in the price of petroleum raw materials. If the product requires blending or colorants, the costs will be calculated separately.
Parts manufactured for the Aerospace and Defense industries require expertise in aesthetics and demand strict and specific requirements. Our molding processes and procedures ensure repeatability on every project. The Plastimold quality department takes careful consideration when documenting validation documentation. In business for over 22 years, you can rest assured our team has experience in molding commonly used aerospace engineering polymers such as PPO and PTFE.
Common raw material prices: PEEK > PA66 > PC > PA6 > ABS > PS > LDPE > HDPE > PBT > PET. Specific prices can be referenced based on local market prices.
The cost of plastic injection molding depends on the size of the machine and the molding cycle. There are differences in processing costs, so injection molding costs can also be said to be part of the injection molding machine’s cost. The larger the machine, the more energy it consumes, which can increase the molding cost. Additionally, the shorter the production cycle, the faster the production speed.
GETTING A QUOTE WITH LK-MOULD IS FREE AND SIMPLE.
FIND MORE OF OUR SERVICES:
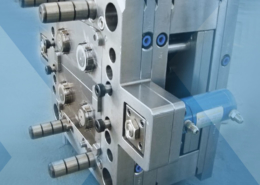
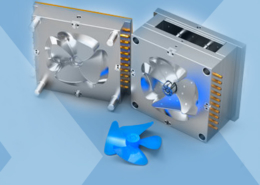
Plastic Molding

Rapid Prototyping
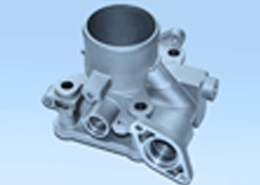
Pressure Die Casting
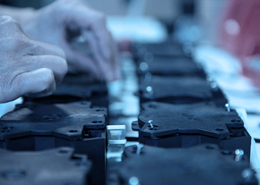
Parts Assembly
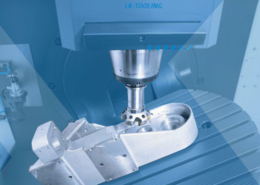