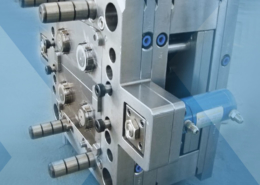
List of 10 Medical Injection Molding Companies in the World - top 10 injection m
Author:gly Date: 2024-10-15
Warping deformation defects of plastic parts can be improved by balancing cooling system, adjusting cooling time, holding pressure and holding time.
Appears as poor demolding, mold damage, or pull. Mainly because draft angle is not enough or mold surface is rough, molding conditions also have an influence.
Occurs at confluence of two streams, such as confluence of two inlets, confluence of bypass bypassing core, is due to decline in material temperature and poor exhaust.
Industrial Plastic Water Bottle Caps Injection Molding Machine adopts proportional pressure and flow control, the pressure and the speed can be adjusted, stable movement curve and gentle shock, the computer is imported from Industry family.The LCD displaying screen with high clarity has Chinese and English language to use.Close-loop PID temperature control with the advantage of high precision.The operating table of the injection moulding machine have two safety, one is machine safety, another is electrical safety, that ensures the operators's safety.
1) LCD computer control with big display screen2) Hydraulic double proportional valve3) Hard chrome plated high tensile strength steel tie bars4) Generous space for fitting large moulds5) Large opening stroke6) Two position transducers to control Clamping and Injection7) Four stages of injecting, independent velocity and pressure control8) Hydraulic mould height adjustment device9) Screw cold-start prevention device10) Melt decompression control11) Screw back pressure control12) Multiple hydraulic ejection13) Differential high speed clamping14) Centralized lubrication system15) Low pressure mould protection device16) Mechanical safety interlock17) Double electrical safety interlock18) Oil return filter19) Oil tank with inner stainless steel container
Thin-wall injection molding technology is also known as thin-wall plastic injection molding technology. There are three types of definitions:
Mold correction, mold re-clamping, increase clamping force, lower material temperature, reduce injection pressure, reduce holding time, reduce holding pressure.
When thickness of plastic part is reduced, influence of condensate layer on flow will increase exponentially, which also explains influence of condensate layer in thin-wall injection molding. If only considering injection molding, it is necessary for injection molding machine to have a high injection rate, so that rate at which plastic melt fills cavity exceeds growth rate of condensation layer (or growth rate of condensation layer is slowed), so that filling action can be completed before flow section is closed, thin-walled plastic parts are injection molded.
For PC materials, sometimes mold temperature is too high, mold surface has residual glue and oil stains. It is necessary to clean mold surface in time, lighten processing, and reduce mold temperature.
Ratio of flow length to thickness L / T, that is, ratio between flow length L from melt entering mold to the furthest point of cavity where melt must be filled and corresponding average wall thickness T is 100 or 150, which is being called thin-wall injection molding;
You can change gate, lighten runner, increase cold area of runner, increase gate, and add bite on the surface (you can also adjust line by adjusting machine or repairing mold). It can solve problems such as mold temperature, reducing injection speed and reducing injection pressure.
At present, commonly used thin-wall injection molding materials are: polycarbonate (PC), acrylic-butadiene-styrene (ABS), PC / ABS blends, and PA6. As wall thickness decreases, plastics with better physical properties are needed to maintain product strength.
1.Can your factory provide he whole plant from A to Z?Yes, we can provide the complete plant, from bottling making plant,water purification plant,to filling packing plant.2.Are all machinery your factory made?Our factory make the water purification and filling packing plants.we do not make the bottle making machinery,we have good quality bottle making machinery partner,and we provide to customer same long warranty time and good after service.3.How can I know the machinery quality before i order?First,we will invite you visiting our factory to check the machines quality,and show the machines running for you in our factory.4.What certificates you can provide?Our factory provide the CE,SGS,ISO,and according to some countries,we also can provide the PVOC, COC,SONCAP...etc.
It can be processed by modifying core, ejector pin, and sandblasting of mother mold surface. It can reduce brightness of mold surface, reduce injection speed, and reduce injection pressure.
Small parts and corners of finished product cannot be completely formed. Due to insufficient mold processing or poor venting, design defects (insufficient thickness) are caused due to insufficient injection dose or pressure.
Requirements for raw materials: large flow length, high impact strength, high thermal deformation temperature, high thermal stability, low directivity, and good dimensional stability; also consider low temperature impact rigidity, flame retardancy, mechanical assembly and appearance quality of plastic materials.
When flow length is 300mm and wall thickness of plastic part is 3.0 mm, L / T is 100 at this time, which is easily achieved by conventional injection molding technology; but when wall thickness of plastic part drops below 1.0mm, this once-to-be-achieved flow-length-thickness ratio (100) becomes very difficult to achieve.
Increase draft angle, polish mold surface, increase or change pull pin when sticking female mold surface. Pay attention to horn diameter when feeding horns, add bite to male mold, reduce injection pressure, reduce holding pressure and time.
Injection molding method where thickness of molded plastic part is less than 1 mm, and projected area of plastic part is above 50 c㎡;
Filling and cooling processes of conventional injection molding are intertwined. When polymer melt flows, front of melt encounters a core surface or cavity wall with a relatively low temperature, and a condensation layer is formed on the surface. Melt continues to flow forward in condensate layer. As thickness of condensate layer increases, actual cavity flow channel becomes narrower. Thickness of condensate layer has a significant effect on polymer flow. Because thickness of plastic part is thicker in conventional injection molding, influence of condensation layer on injection molding is not great at this time. However, in thin-wall injection molding, when ratio of thickness of condensing layer to thickness of plastic part gradually increases as thickness of plastic part becomes thinner, this effect is great. Especially when sizes of the two can be compared with each other.
Thin-walled injection molding is defined as a thin-walled injection molding when wall thickness of molded plastic part is less than 1 mm (or 1.5 mm), or t/d (thickness t of plastic part, diameter d of plastic part, for disc-shaped plastic parts) is less than 0.05 .
It can be seen that critical value defined by thin-wall injection molding will also change, and it should be a relative concept.
Short shot refers to incomplete quality defect of plastic part due to incomplete filling of mold cavity, that is, melt has set before filling is completed.
You can change inlet, add cold material wells, open vent grooves, or bite male mold surface, or increase material temperature, mold temperature, etc.
Transparent finished PC material is easy to appear. Because gas is not exhausted during injection process, improper mold design or improper molding conditions can have an impact.
Warpage deformation is a plastic defect caused by uneven internal stress. Cause of warpage deformation is uneven shrinkage, uneven orientation, and uneven cooling.
Increase R angle at the corner, increase demolding angle, increase ejector pin or increase its cross-sectional area, polish mold surface, polish ejector pin or oblique pin, reduce shooting rate, reduce injection pressure, reduce holding pressure and time.
It often occurs in uneven wall thickness or flesh thickness of molded product, which is caused by difference in cooling or curing shrinkage of hot-melt plastic. Such as back of ribs, edges with side walls, back of BOSS column.
It often occurs at the junction of male and female molds, due to poor mold clamping, or improper processing of corners of mold surface. Molding temperature is often insufficient due to insufficient clamping force, high material temperature, and high pressure.
Reduce thickness, but keeping at least 2/3 of thickness, can be improved by thickening runner, increasing gate, increasing exhaust, increasing material temperature, increasing injection pressure, and extending holding time.
It is easy to occur at the corner of thin wall of molded product or at the root of thin wall RIB. It is caused by poor force during demolding, improper setting of ejector pin or insufficient draft angle.
According to surveys, domestic thin-wall injection molding has been widely used in food containers, medical boxes, cosmetics, stationery and even multimedia packaging. For example: disposable packing boxes, cosmetics bottles and other daily necessities.
It occurs at the gate, because mold temperature is not high, injection speed and pressure are too high, gate is not set properly, and plastic encounters spoiler structure during feeding.
Clamping Unit5-point twin toggle clamping system by modular optimization software designing.Strong clamping with rapid and stable, tomeet the strict clamping condition.Mould height adjustment by hydraulic driven gear system with rapid and stable.Automatic mould height adjustment as per the setting clamping force(optional).Injection UnitBaIanced double injection cylinder technology makes screw to have evenly distributed force during fast injection,Five_star Hydraulic motor with big torque,Ensure the excellent plastic molding condition.Research and develop different screws according to difierent iniection condition, suitable for the progressive demand and greatly improve the injection quality.Control UnitImported computer special for Injection Molding Machine with multiple functions and precise control processing.World famous electrical components and high quality circuit hardware with stable and reliable running.
Occurs at joints of male and female modules, sliders, oblique pins, etc., which appear as uneven levels of joint surface, etc., due to improper mold clamping or problems with mold itself.
It often occurs on the back of a reduced bosom column or ribs, or stress marks are reduced due to high core and thimble design.
Increase exhaust, change gate (inlet gate increases), PC flow path must be polished, strict drying conditions, increase injection pressure, reduce injection speed, etc.
Slender pieces, large-area thin-walled pieces, or large finished products with asymmetric structures are caused by uneven cooling stress or uneven ejection forces during molding.
Analysis of common defects: Although there are many advantages to thin walled plastic parts, formability of plastic parts is reduced, so that these thin walled plastic parts cannot be molded by conventional injection molding methods. When forming thin walled plastic parts, following common problems exist:
During design, you can reduce or change position of welding line by reducing number of gates or changing position of gates to meet design requirements of plastic parts.
Generally, changing holding time and injection pressure (second stage) has the greatest effect on size. For example, increasing injection pressure, pressure-retaining and shrinking effect can significantly increase size and lower mold temperature. Increasing inlet can improve adjustment effect.
Molds at missing parts can be modified, taking or improving exhaust measures, thickening material, improving gate (enlarge gate, increase gate), increasing injection dose, increasing injection pressure and other measures to improve.
Correct ejector pin, set tensioning pin, etc. If necessary, adjust deformation of male mold with bite adjustment, adjust temperature of male and female mold to reduce holding pressure, etc. Adjustment of deformation of small parts mainly depends on pressure and time, and adjustment of large pieces of deformation generally depends on mold temperature.
Welding line is boundary formed when two or more melt flow fronts within a cavity are fused. Stress concentration is easy to occur at welding line, which weakens mechanical strength of plastic part, which is particularly detrimental to mechanical properties of plastic part, especially thin-walled plastic part. Plastic part is very easy to crack at welding line after external force.
GETTING A QUOTE WITH LK-MOULD IS FREE AND SIMPLE.
FIND MORE OF OUR SERVICES:
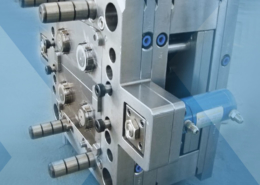
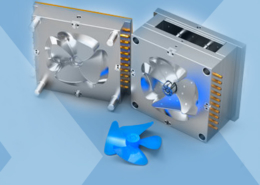
Plastic Molding

Rapid Prototyping
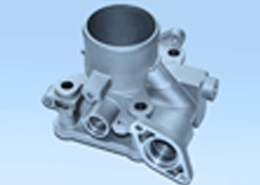
Pressure Die Casting
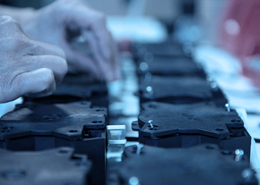
Parts Assembly
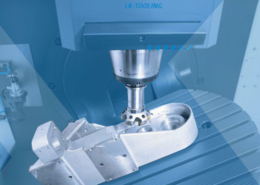