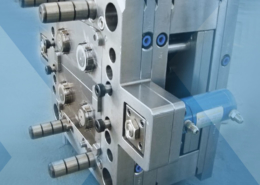
List of 10 Medical Injection Molding Companies in the World - medical injection
Author:gly Date: 2024-10-15
We have worked with HLH Prototypes on a number of projects over the past year and have always been very satisfied with their services. We have produce with them high quality rapid prototypes for testing before tooling as a means to make sure we have the best design possible.
I would like to congratulate you and your company with your service and prototyping quality. The communication with our company was very clear and constructive. The prototypes have a very good quality and the delivery speed are fantastic. With your prototypes we can communicate better and faster with our clients and give them a glance of how the product will look and feel like.Ing. Marc E.J. Van Strydonck Industrial designer
HLH Prototypes. What can’t they prototype? We have had everything from soft rubber to hard plastics, various grades of aluminum to stainless steel parts prototyped via HLH to characterize the performance and gain high level of confidence on design months before actual verification parts and data is available. We have used many of their arsenals of processes from SLA, CNC mill, lathe, forming, wire-cutting, EDM, vacuum cast and my favorite – custom springs. Product development is so much more progressive and easier with HLH as your prototype partner.
Each MMM primary subset can also be further subdivided into secondary and tertiary subsets, and even further in some cases.[4] This can be advantageous when fine tuning or other general calibration of a specific MMM process is desired. Each primary subset is outlined further in the following sections.
Multi-material injection molding (MMM) is the process of molding two or more different materials into one plastic part at one time.[1] As is the case in traditional injection molding, multi material injection molding uses materials that are at or near their melting point so that the semi-liquidous (viscous) material can fill voids and cavities within a pre-machined mold, thus taking on the desired shape of designed tooling. In general, advantages of MMM over other production techniques include, but are not limited to, creating parts that have an elastic modulus that varies with location on the part (different regional polymer hardness), creating a single-structure part with different regional materials (similar to the previous advantage, but more focused on joining different types of polymers like rubber and plastic), and also creating a single part with multiple independent polymer colors. Applications range from simple household items like a toothbrush to more heavy duty construction of items like power tools.[2]
We have always been very impressed by the level of service and quality provided by HLH. HLH gives our company a real competitive advantage in allowing us to provide our clients with quick and cost effective pre-production quality prototypes.
We have had everything from soft rubber to hard plastics, various grades of aluminum to stainless steel parts prototyped via HLH to characterize the performance and gain high level of confidence on design months before actual verification parts and data is available. We have used many of their arsenals of processes from SLA, CNC mill, lathe, forming, wire-cutting, EDM, vacuum cast and my favorite – custom springs. Product development is so much more progressive and easier with HLH as your prototype partner.
Injection Moulding & rapid prototyping can also come in the form of injection molded parts. How? Rapid tooling (bridge tooling) delivers low volume production quality parts (up to 100,000) from production resins. Think of rapid injection molding as end use prototype manufacturing. End use because your parts are identical to production parts. Prototype because the lead times and costs of rapid injection molding are significantly reduced compared to full production tooling.
Thank you very much again for your teams speed and effectiveness in producing our RP molds. The quality in finish as always was fantastic especially the clear plastic parts.
Rapid plastic molding tools are made from steel or aluminium. We use both options but most of our custom injection molding tools are steel. Why? More value for you. Our steel rapid tool injection molding services will typically deliver more than double the parts than comparable aluminium programs.
Prototypes from real materials, bridge between prototype and production, low volume production, market testing, rapid parts
Not only was the work done to a high standard, and with considerable speed despite the harsh deadlines, but with the kindest and warmest of attitudes. I am delighted to have worked with your company, and would definitely recommend you to others.
We have always been very impressed by the level of service and quality provided by HLH. HLH gives our company a real competitive advantage in allowing us to provide our clients with quick and cost effective pre-production quality prototypes.
Our engineers were just commenting on how the quality in the surface and spray finishing are superior to the models that we had received before from other China based RP houses in the past.
If the desired object is manufacturable using MMM, it is definitely best to use MMM over traditional injection molding. Some of the key features that makes MMM a better approach are:
All projects and manufacturing processes come with their own challenges to and guidelines for success. For rapid prototyping there are a number of things you can do to reduce the cost and lead time.
Please place file(s) for transfer in the same folder and ZIP or RAR before attaching. Larger attachments can take a few minutes to transfer depending on your local internet speed :) For attachments over 20MB, click WeTransfer and send to info@HLHPrototypes.com.
Also referred to as co-injection molding,[4] multi-component injection molding describes insertion of multiple viscous materials injected simultaneously, as opposed to placing one material as an additional layer relative to another. In other words, it creates a sandwich-like structure where both materials mold around each other as dissimilar liquids, and exist in such a state at the same time. Relative to the part center, materials can be injected concentrically using the same mold/gate, or regionally using gates at different locations.[2]
Also referred to as sequential injection molding,[4] multi-shot injection molding refers to creation of multiple layers relative to the starting axis of the initial mold. In other words, the warm, heated materials are inserted into the mold in a very specific sequence one after another. This creates a layering effect between materials while maintaining relatively high-energy interactions at material boundaries. This is important because it implies that the inter-layer bonds are stronger in many cases than when the layers are applied to a previously cooled part, as is more closely the case of over molding. While there are other applications, this operation is preferred when varying molds (different geometries) are desired between material layers.[2]
The prototypes arrived this morning and they look great. Thank you very much for your work on this project and your prompt and thorough communication. We will certainly be in contact again in the future.
Hi HLH, I received the CNC prototypes last week and have spent the past few days assembling them. I would like to thank you and HLH for the work you have done CNC machining these parts and for delivering them to us as quickly as possible. I look forward to working with HLH again as new projects arise in the future.
All projects and manufacturing processes come with their own challenges to and guidelines for success. For rapid prototyping there are a number of things you can do to reduce the cost and lead time. Surface finish is one. The less processing we need to do to the tool to achieve your desired surface finish the quicker and cheaper it will be. We suggest a SPI Finish B-1 600 Grit Paper as far as possible. To learn more talk to our rapid CNC manufacturing team today.
I would like to convey my sincere thanks to your company for all the work you have provided over the past year in helping to create parts for our models and the dedication you brought to our projects.
The prototypes arrived this morning and they look great. Thank you very much for your work on this project and your prompt and thorough communication. We will certainly be in contact again in the future.
Thank you very much again for your teams speed and effectiveness in producing our RP molds. The quality in finish as always was fantastic especially the clear plastic parts. Our engineers were just commenting on how the quality in the surface and spray finishing are superior to the models that we had received before from other China based RP houses in the past. Like the previous years, we look forward to displaying your RP models as various international toy trade shows, where they have proven themselves in the past with strength and durability
Hi HLH, I received the CNC prototypes last week and have spent the past few days assembling them. I would like to thank you and HLH for the work you have done CNC machining these parts and for delivering them to us as quickly as possible. I look forward to working with HLH again as new projects arise in the future.
Follow us on Facebook or LinkedIn for daily tips, advice, trends, and opinions on rapid manufacturing. For fast parts, click below to start.
I would like to convey my sincere thanks to your company for all the work you have provided over the past year in helping to create parts for our models and the dedication you brought to our projects. Not only was the work done to a high standard, and with considerable speed despite the harsh deadlines, but with the kindest and warmest of attitudes. I am delighted to have worked with your company, and would definitely recommend you to others.
We have worked with HLH Prototypes on a number of projects over the past year and have always been very satisfied with their services. We have produce with them high quality rapid prototypes for testing before tooling as a means to make sure we have the best design possible. We will surely be continuing our working relationship with HLH Prototypes in many years to come
I would like to congratulate you and your company with your service and prototyping quality. The communication with our company was very clear and constructive. The prototypes have a very good quality and the delivery speed are fantastic. With your prototypes we can communicate better and faster with our clients and give them a glance of how the product will look and feel like.Ing. Marc E.J. Van Strydonck Industrial designer
The less processing we need to do to the tool to achieve your desired surface finish the quicker and cheaper it will be. We suggest a SPI Finish B-1 600 Grit Paper as far as possible.
Like the previous years, we look forward to displaying your RP models as various international toy trade shows, where they have proven themselves in the past with strength and durability
Over molding is effectively the use of layering effects in polymer application techniques. This process is centered around the use of a liquidous resin to add additional layers of shape and structure to an existing component. An example of such a resin could be a polymer that has been heated to a temperature just above its glass transition temperature). The existing component to which the resin is being added is often injection molded as well, and may be near its own glass transition temperature. This process works well when layers with varying geometric profiles are desired around a central "core" structure.[2]
GETTING A QUOTE WITH LK-MOULD IS FREE AND SIMPLE.
FIND MORE OF OUR SERVICES:
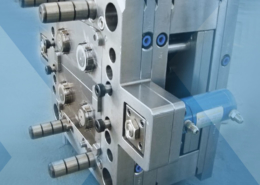
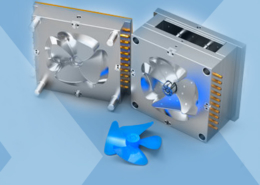
Plastic Molding

Rapid Prototyping
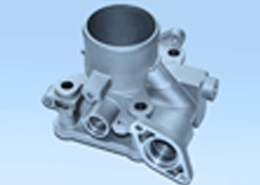
Pressure Die Casting
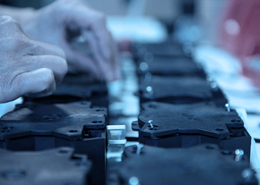
Parts Assembly
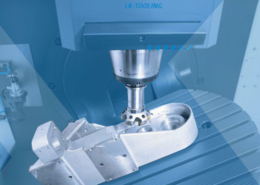