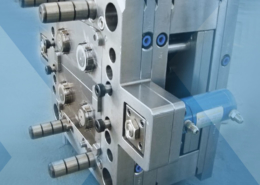
Exploring the World of Custom Molded Plastics
Author:gly Date: 2024-06-08
Custom molded plastics have revolutionized various industries, offering unparalleled versatility, durability, and efficiency. From intricate components in aerospace technology to everyday household items, the applications of custom molded plastics are vast and ever-expanding. In this article, we delve into the fascinating realm of custom molded plastics, exploring its intricacies, applications, and future prospects.
Understanding Custom Molded Plastics
Custom molded plastics refer to the manufacturing process of creating plastic components tailored to specific designs and requirements. Unlike standard plastic fabrication techniques, such as injection molding or extrusion, custom molding allows for precise shaping and detailing, resulting in products that meet exact specifications.
The Manufacturing Process
The process typically begins with the design phase, where engineers use CAD software to create digital models of the desired product. These models serve as blueprints for the molding process, guiding the creation of molds and tooling. Once the design is finalized, the actual molding takes place, where molten plastic is injected into the molds under high pressure. After cooling and solidification, the finished parts are removed from the molds, often requiring secondary operations such as trimming or finishing.
Materials Used
Custom molded plastics can be fabricated from a wide range of materials, including thermoplastics and thermosetting polymers. Each material offers unique properties such as strength, flexibility, and chemical resistance, making it suitable for specific applications. Common materials used in custom molding include polyethylene, polypropylene, ABS, and polycarbonate.
Applications Across Industries
The versatility of custom molded plastics makes them indispensable across various industries, serving diverse needs and requirements.
Automotive
In the automotive sector, custom molded plastics are used for interior and exterior components, such as dashboards, bumpers, and door panels. Their lightweight nature, coupled with high strength and durability, makes them ideal for improving fuel efficiency and vehicle performance.
Medical
In the medical field, custom molded plastics play a crucial role in the manufacturing of medical devices and equipment. From surgical instruments to implantable devices, plastics offer biocompatibility, sterilization capability, and design flexibility, meeting the stringent requirements of the healthcare industry.
Electronics
Custom molded plastics are extensively used in the electronics industry for housing and enclosures of electronic devices. Their electrical insulation properties, along with resistance to heat and chemicals, ensure the protection and longevity of sensitive electronic components.
Consumer Goods
In the realm of consumer goods, custom molded plastics are ubiquitous, found in products ranging from toys and appliances to packaging containers. Their cost-effectiveness, customizable aesthetics, and ease of mass production make them preferred materials for manufacturers catering to consumer needs.
Advantages and Challenges
While custom molded plastics offer numerous advantages, they also present certain challenges that need to be addressed.
Advantages
Design Flexibility
: Custom molded plastics allow for intricate and complex designs that would be difficult or impossible to achieve with other materials.
Cost Efficiency
: Mass production capabilities and material versatility contribute to cost-effective manufacturing processes.
Lightweight
: Plastics are inherently lightweight, making them suitable for applications where weight reduction is essential.
Challenges
Tooling Costs
: The initial investment in molds and tooling can be significant, particularly for complex designs or low-volume production runs.
Material Selection
: Choosing the right material for a specific application requires careful consideration of factors such as strength, temperature resistance, and environmental impact.
Environmental Concerns
: The disposal and recycling of plastic waste remain significant challenges, highlighting the need for sustainable practices and materials.
Future Perspectives
As technology continues to advance, the future of custom molded plastics holds promise for innovation and sustainability.
Advanced Materials
Research and development efforts are focused on the development of biodegradable and recyclable plastics, addressing environmental concerns and promoting sustainable manufacturing practices.
3D Printing
Advancements in 3D printing technology are revolutionizing the custom molding process, allowing for rapid prototyping and on-demand production of complex plastic components with reduced lead times and costs.
Industry 4.0 Integration
The integration of custom molding processes with Industry 4.0 technologies such as IoT, AI, and automation is enhancing efficiency, quality control, and customization capabilities in plastic manufacturing.
Conclusion
In conclusion, custom molded plastics represent a cornerstone of modern manufacturing, offering unparalleled versatility, efficiency, and customization possibilities across various industries. While challenges such as environmental concerns and material selection persist, ongoing research and technological advancements promise a future where custom molded plastics are not only innovative but also sustainable. As we continue to explore new frontiers in materials science and manufacturing technology, the role of custom molded plastics will undoubtedly remain indispensable in shaping the world around us.
GETTING A QUOTE WITH LK-MOULD IS FREE AND SIMPLE.
FIND MORE OF OUR SERVICES:
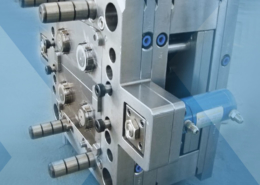
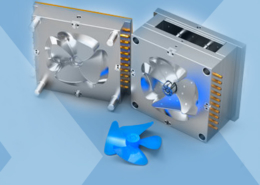
Plastic Molding

Rapid Prototyping
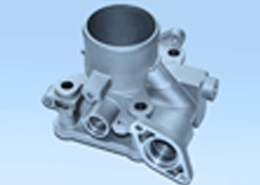
Pressure Die Casting
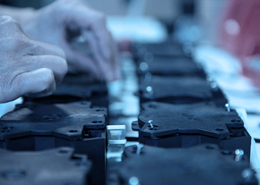
Parts Assembly
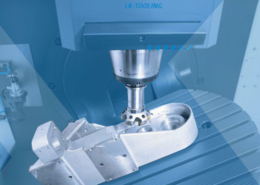