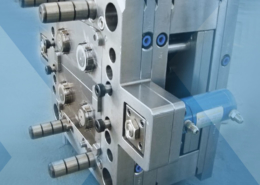
LG Chemical HIPS 408AF Injection Molding Grade - hips injection molding
Author:gly Date: 2024-10-15
Never once during this procedure is the product taken out of the mold or moved about in the mold. With the exception of any post-process defects brought on by factors like uneven cooling, the finished product is therefore made with the same precision as the mold itself.
The designer can combine the most outstanding qualities of many injection molding materials via two-shot injection molding. Engineering plastics may have a wide range of beneficial yet quite distinctive qualities. To precisely accomplish the necessary outcomes, the designer can blend the solid structural qualities of hard plastic with the supple and attractive attributes of another material.
Makuta produced products for the medical and pharmaceutical device industries for the last 20 years. Our customers count on us to meet all of their application requirements including:
With this method, you may produce plastic storage containers. Along with rubberized edges to secure lids and soft container surfaces to safeguard contents, other colors can be incorporated.
The chemistry of the materials must be taken into consideration while choosing ones for double shot injection molding. Some materials may establish a compelling molecular connection even when they may not all link correctly. The table below shows compatibility with adhesion.
Due to plastic’s advantageous characteristics in a water environment, two-shot injection molding works well in this situation. Softer seal surfaces can be coupled with durable foundation sections.
Budgets for designing and developing new products may be constrained during a period of constrained resources and cost-cutting. In certain businesses, the tools and expertise required to effectively finish an LSR molding operation are also scarce. As a top supplier of LSR 2-Shot injection molding services, Prototool can assist you in effectively, affordably, and promptly finishing such tasks. For more information on how Prototool can assist you with your LSR 2-Shot injection molding needs, get in touch with us right now.
Makuta Micro Molding specializes in micro injection molded parts for numerous segments of the medical industry. Parts we mold for our customers are used in:
The reduction in manufacturing time is a crucial advantage of two-shot injection molding. There is frequently no need to do secondary assembly of the item since it can add many product tiers during this operation. With the advent of mixed molding, traditional injection molding would have required a whole secondary stage in manufacturing.
Products created using a two-shot method can maintain the necessary structural characteristics while still having a very appealing appearance. The load-bearing structural component can be molded in the first phase of this procedure, and the finishing touches can be applied in the second step using a more attractive material.
In 2-shot molding, several tool sets are employed to create the molds. The tools in a rotating platen configuration have the same cores but different cavities. The runners must be built such that they may be turned off during the inactive molding processes.
With two-shot molding, items like toothbrushes may be accurately shaped. It can combine a rigid base plastic with a softer rubber second shot for improved grip and coloring.
Two-shot injection molding is a procedure that is ideal for producing goods that are ergonomically designed. It is simple to cover or add to structural plastic with materials that are more suitable for human contact. Because it offers a more excellent grip and a gentler touch, soft, rubbery material is more suited for human hands.
People inject two separate materials into the same mold to create the product in two-shot injection molding. These substances are administered sequentially rather than simultaneously. The product is not discharged from the mold between the two shoots but is produced in a single step.
Because two-shot injection molding does not require several production stages, it gives designers more freedom. It offers molding manufacturers a number of benefits, including reduced manufacturing costs, improved ergonomics and aesthetics, superior mechanical bonding, and quicker production times. This process can produce a wide range of goods, including toys, vehicle components, medical equipment, containers, and toiletries.
As the name implies, two injection shots are used in this method instead of simply one, as in traditional injection molding. This procedure makes use of a unique mold that meets the needs of these two injections. The mold and the systems that support it are made to produce two shots without requiring the removal of the half-finished product between them.
Before starting a two-shot injection molding process where adhesion combinations are unknown, an adhesion test must be performed. Undercuts, shoulders, or grooves may be added to the design to lock the two components together when the intrinsic bonding capacity is insufficient.
Since its inception, the plastic injection molding market has advanced significantly. It has advanced significantly in terms of productivity, cost-effectiveness, and new and creative approaches to product manufacturing. Two-shot injection molding is one of these creative methods. Multi-material injection molding, two-color injection molding, two-k injection molding, or double-shot injection molding are other names for this procedure.
Below are just some examples of the range of medical parts we mold. Please refer to Pharmaceutical and Microfluidics pages for more examples of medical-related parts we mold.
As with regular injection molding, the procedure begins with mold sealing to create the first cavity. In this initial configuration, the secondary step’s runner is sealed off while the runner for the first cavity is aligned with the base material’s sprue. The first substance is then injected into the opening, filling it.
Makuta, Inc. | 2155 Intelliplex Dr., Shelbyville, IN 46176 | Phone: 317.642.0001 | Email: info@makuta.com | Copyright 2022. All rights reserved.
Earning the trust of many medical companies has required not just the technology, but also an unwavering commitment to a clean molding environment and defect-free molding to protect the safety of patients and medical professionals. Makuta’s production environment is a certified class 8 cleanroom.
Utilizing two-shot molding, you may produce medical equipment such as bone saws. Rubber grips have a crucial role in how well this equipment works. Compared to conventionally constructed things, two-shot molded objects improve cleanliness since there are fewer fissures where sub-parts contact.
Nave ISK-8, Parque Industrial y Logístico Sky Plus, Avenida Mineral de Cinco Señores No.100, del Parque Industrial Santa Fe, Silao de la Victoria, Guanajuato, México
Following the first stage, the mold opens, allowing the platen holding the finished product to rotate 180 degrees on a horizontal axis and line up with the sprue of the following stage. The first cavity is isolated from any injection in this stage. The second shot now starts molding the remaining portion of the product since the sprue of the second material is now in line with the runner for the second cavity.
Double-shot injection molding offers exact production compared to conventional molding and assembly or even more contemporary techniques like insert molding. There is no possibility of material misalignment because the semi-finished product does not need to be withdrawn from the mold between phases. The finished product can be just as precise as the mold if thermal impacts are appropriately managed through effective product design.
Two-shot injection molded products have excellent mechanical characteristics. Given the excellent material selection, the product’s various levels combine molecularly throughout the molding process. This bond is frequently more durable than traditional molding and assembly and even more durable than other cutting-edge techniques like over- and insert molding.
Two-shot injection molding excels in this situation. Thanks to two-shot molding, A production line can now produce more complicated goods with fewer stages than ever. Think about the standard injection molding procedure: Two distinct materials would have needed to be molded separately in two different molds, followed by a manual assembly phase, if a certain object was made of those materials. In two-shot injection molding, these two components are fused and formed in a single mold configuration, eliminating the need for any assembly.
Two-shot molding may be used to make plastic electrical items with built-in LEDs efficiently. A transparent insert can be sculpted into the design to distribute or color the LED light.
GETTING A QUOTE WITH LK-MOULD IS FREE AND SIMPLE.
FIND MORE OF OUR SERVICES:
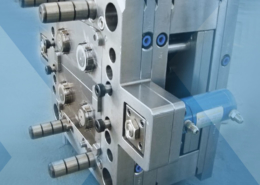
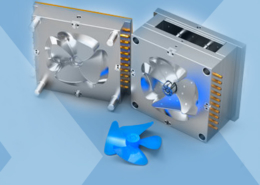
Plastic Molding

Rapid Prototyping
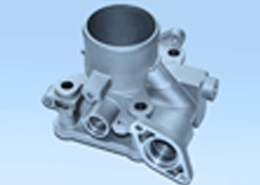
Pressure Die Casting
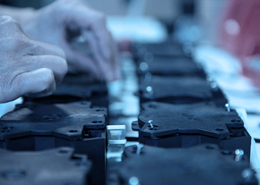
Parts Assembly
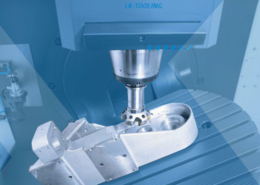