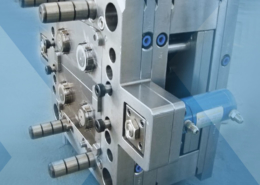
LDPE INJECTION MOULDING - ldpe injection
Author:gly Date: 2024-10-15
The process involves running gas through the channels built into the mold. The gas (Nitrogen gas) passes through the middle of these thicker sections. Also, this creates the pressure necessary to press the resin tightly against the mold, making a smooth, structurally sound part with zero sink marks.
Silicone doesn’t react with biological tissue, making it even more suitable to implant it safely. However, this injection molding process requires many steps. This is also dependent on the properties expected of the resultant silicone product.
Machines capable of measuring backflow, provide operators with the opportunity to change the no-return valve before problems with the injection moulding process lead to poor parts quality.
The process of medical injection molding edges out similar production procedures in the industry. With its smooth and seamless operation, there are numerous advantages the process offers, and they include but are not limited to:
The gas-assisted injection molding method is not suitable for creating tools with sharp corners in their design, because gas pressure will reduce if it doesn’t flow in a straight line. However, this type is more suitable for producing complex parts.
Devices produced with this injection molding type include wearable devices, surgical tools, and catheter ablation tools.
With the level of results of this process, it’s no surprise that it serves as the medical prototype development approval process for the FDA. Here, we explain what this medical injection molding process entails and its role in the medical industry.
In the process of plastic injection for the medical device industry, exceptional accuracy is a must. Due to the tight tolerance margin, every inch, millimeter, or centimeter count can influence the whole molding development. Besides, it is essential to use skilled injection molding facilities to achieve this high-level accuracy.
Given the critical nature of medical products, smart functionality designed to overcome material inconsistencies and gas issues are essential to ensuring highly consistent moulding and parts quality.
The materials utilized in this production process easily withstand the invasion of contaminates. Also, they don’t need much sterilization to stay germ-free. Because of this factor, the material easily meets the FDA standards and other stipulated requirements.
To produce intricate electrical parts, features such as high-speed acceleration injection control, active gas venting, intelligent plasticising control, sensitive mould production and multi cavity pressure channels are extremely useful.
There should be no breakable plastics in manufacturing devices to avoid or minimize biohazards in the medical field. Hence, each selected material should have a satisfactory durability index before being put to use. More so, they should be able to exhibit a high level of tensile strength.
A minimal need for medical products but is important. All housing equipment or facility, or device parts that come in contact with the human body must be contaminant-resistant. They should also go through sterilization processes without damage.
The application of plastic molding injection in the medical device industry is diverse. Medical suppliers go for this process as the products easily attain the stipulated standards of quality and safety. Besides, medical device plastic injection molding comes in handy in areas like:
To avoid costly repairs and protect the mould clamp and ejector mechanisms, intelligent functions on some injection moulding machines monitor the torque applied to them, preventing damage should this increase beyond certain parameters.
The ability to withstand adverse conditions is a crucial consideration for plastic molding materials. They must be reliable and durable when subjected to heat, corrosives, liquid, vibrations, and other human body movements. Most of the plastics used in this process come out tops in this requirement.
Manufactures providing injection molding services use different plastic molding techniques to produce medical-grade parts. But here, we will be looking at the 4 common types, which include:
To prevent air and burn problems from occurring during the injection moulding process, some machines are equipped with a sensitive pre-injection function. This useful feature is ideal for sensitive moulding applications such as the production of light guides.
This is a more complicated molding type. When carrying out regular molding, the thicker parts tend to dry or solidify slower than the thinner walls. The reason is that there isn’t enough pressure to pack the resin properly and make it even.
Trade moulders and manufacturers no longer need different machines to produce different kinds of parts. Some injection moulding machines are so versatile that they will produce anything from extremely precise and delicate items like camera lenses to products that require high levels of exertive force to produce (such as battery cases).
The way the medical plastic injection process is set up helps cut unnecessary injection molding costs — massive production deliveries and high-volume manufacturing help to maximize the process. Hence, whenever there is an extraordinary volume of medical injection parts being produced, the injection molding process can reduce the cost per part.
Machines capable of measuring backflow, provide operators with the opportunity to change the no-return valve before problems with the injection moulding process lead to poor parts quality.
Some medical devices like tubes and respiratory masks are quite difficult to keep hygienic. So, liquid silicone injection molding is generally the most suitable in producing equipment like these.
Validating your moulds guarantees perfect moulding parameters, ensuring you get acheive the best possible results right from the start.
The medical injection molding process uses a vast range of material options to manufacture medical and pharmaceutical parts. There are various plastic injection molding materials used that give the process high efficiency. Some of them are:
Given the critical nature of medical products, smart functionality designed to overcome material inconsistencies and gas issues are essential to ensuring highly consistent moulding and parts quality.
To prevent air and burn problems from occurring during the injection moulding process, some machines are equipped with a sensitive pre-injection function. This useful feature is ideal for sensitive moulding applications such as the production of light guides.
If you’re looking for an injection parts medical manufacturer, you can visit RapidDirect’s Injection Molding Services for more in-depth information. RapidDirect, an ISO 9001 certified industry, is a renowned name in the injection parts industry, offering you a rich experience in making injection molded parts, including medical injection parts. Also, we provide custom injection molding services at a competitive price and detailed reports of inspection and material tests. You can stand to get an instant quote and free automated DfM feedback after you upload a CAD file.
Achieving extremely consistent part weights even when viscosities are varied requires precise digital control of the screw.
The materials used in production are greatly dependent on the object being made. These molds (prototypes) go through extensive rounds of testing to ensure their usability.
Cutting-edge machines achieve high levels of stability and repetitive accuracy through sampling intervals of under 20 microseconds.
The process of plastic injection molding for medical devices is critical, with a high probability of failure. Thus, there are some factors one needs to consider before and during the design, planning, and operational procedure. They include:
Use a mould test to define the best injection moulding process before you start production. This ensures that all parameters correspond perfectly and you obtain the best results from your process.
After injection comes the removal of the binding agent through various means, including solvent, a catalytic process, thermal furnaces, or even a combination of these methods. This leaves behind injection parts with a 100% density at the end.
Medical injection molding is a cheaper and more efficient method of making medical and pharmaceutical parts, including medical devices, laboratory tools, equipment, and testing instruments. Medical parts made from this method reach a high level of precision, quality, and accuracy.
The use of metal in medical device manufacturing is a technique that we cannot overlook. The reason is that metal equipment plays a significant role when it needs equipment with high density, small size, and maneuverability. This doesn’t detract from the numerous uses and advantages of traditional 3D printing, medical plastic molding, or gas-assisted molding.
Plastics have a wide range of use in the medical field. They are almost indispensable in creating plastic injection molding medical parts and tools like Syringes, surgical gloves, IV tubes, catheters, etc. These products are for one-time use only, erasing the need for sterilization and reducing the spread of highly contagious or virulent diseases.
The strict requirements of this process require a hygienic environment for production. This environment ensures that no ambient air, dust, or moisture settles on the mold or mixture while it sets. The rubber-like substance produced through this process is highly chemical resistant.
Always consider the material’s area of use before selection. For instance, single-use materials like syringes, needles, tubing, and connectors should be transparent, flexible, and easy to sterilize. Likewise, surgical injection parts should be lightweight and ergonomic.
The innovative medical injection molding process is a ground-breaking invention that has swept through the industry. The manufacturing of medical injection parts not only satisfies laid down industry standards but makes the usage process smooth. This article explained some of the rudiments of the process and other important details.
More complex applications often require inserts or labels to be added. As part of a moulding cell, some state-of-the-art machines can be easily supplemented with robots that pick and place these inserts very precisely at high speed.
Equipment made in this manner has a high requirement for its material. While the walls are thin, the device or tool maintains its integrity and durability to an extent. As a result of these requirements, its base materials tend to be plastic (especially LCP or Polypropylene, or even nylon).
For medical component manufacturing, FDA requirements are the standards to aim at in all processes. The regulations for sterility and cleanliness are stringent and require strict observance. In all the stages of productions, ensure all inputs meet or surpass the laid down standards. For medical-grade approval, the factory must pass the standards in the components and production process.
As a result, the resin ends up looking misshapen, ugly, and weaker structurally than it should due to the sink marks. Gas-assisted injection molding is the solution to this problem of making plastic injection molding medical parts.
If you want to produce high-quality machined parts with a sleek appearance, it’s essential to consider some critical factors related to CNC machining.
Medical-grade plastic materials are simply plastics designed to create medical products. It is also suitable for manufacturing Vitro diagnostics and primary packaging products. These products help preserve and contain medicines to avoid contamination in pharmaceuticals.
The production of optical products requires extreme levels of accuracy and consistency. The nature of these items requires machines to be capable of maintaining long high pressure holding times and providing exacting levels of control on both low and high speed pressure.
For varied applications, such as automotive, more versatile machines are equipped with over six different screws. To ensure they can mould products with differing material characteristics, specifications should also include high duty injection units, active gas venting, sensitive mould protection and multi cavity pressure channels.
Generally, atomization technology creates a powder mix from the desired metals. This powder is made into a pellet (feedstock), which includes a binding agent that makes it easier to mold.
To ensure you benefit from improved cycle times, machines should come with functions such as pre-injection, pre-ejection and parallel movements.
The injection molding procedure offers the widest range of options for choosing materials. Although medical injection molding narrows the scope of injection molding materials, there are still many materials that are suitable for manufacturing medical-grade components. We’ll touch on that more in the later parts of this guide.
A known fact about plastics used in injection molding is that it is ruggedly durable. These materials provide dogged strength and resistance to adverse environments and usage. Therefore, the products of this process can comfortably withstand heat, blunt force, and vibration without any incidence of cracks or breakages. Also, when they undergo sterilization in autoclaves, they don’t cave to the heat.
To produce intricate electrical parts, features such as high-speed acceleration injection control, active gas venting, intelligent plasticising control, sensitive mould production and multi cavity pressure channels are extremely useful.
One way of producing durable and reliable medical-grade components that meet FDA standards is through medical injection molding. The process is now the go-to procedure for manufacturing state-of-the-art medical equipment because it offers countless advantages.
Think of the best laboratory facility and medical devices, made with top quality finish, and it’s undoubtedly through the medical plastic molding process. One good thing about the procedure is that it is both cost-efficient and delivers with exceptional accuracy and consistency. Besides, it comes in handy when the volume of productions is high and requires a masterpiece level of construction.
In plastic injection molding for the medical device industry, thin-wall molding is one of the most common processes. It is for producing tools or effects that involve both function and patient comfort. The walls of the injection parts of the medical device are much thinner relative to the complete pieces. The walls are usually thinner than 1mm.
The extremely high level of precision needed within the aerospace industry makes CNC machining a suitable manufacturing process for the sector.
GETTING A QUOTE WITH LK-MOULD IS FREE AND SIMPLE.
FIND MORE OF OUR SERVICES:
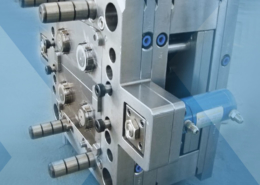
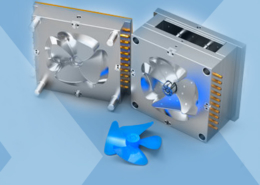
Plastic Molding

Rapid Prototyping
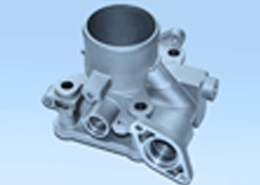
Pressure Die Casting
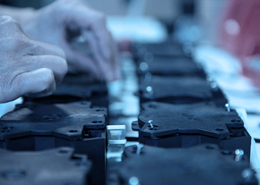
Parts Assembly
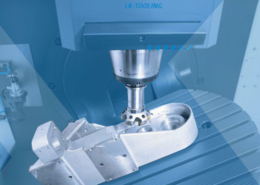