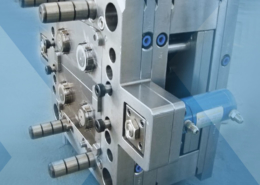
Large-tonnage machines for big injection molding projects - large plastic molds
Author:gly Date: 2024-10-15
Hi, I am interested in creating 6 different plastic figurines, each one in a 6 and a 12 in size. would I need to purchase a separate mold for each figurine and size? These would be low production, at least in the beginning, for retail and online sales. Are there options to have them manufactured in color? For example, skin tone, clothing and hair color?
The determining factors in the cost of your mold are a combination of the part size, complexity, material, and anticipated quantities. For instance, if you wanted 1,000 washers per year, we would recommend a single cavity mold, meaning it makes one washer per machine cycle. In that case, the mold would probably be $1,000-2,000.
Metal threaded inserts can be added to plastic Injection Molded parts to provide a durable threaded hole for fasteners such as machine screws. The advantage of using inserts is that they allow many cycles of assembly and disassembly. Inserts are installed in Injection Molded parts through thermal, ultrasonic or in-mold insertion. To design a boss that will receive a threaded insert, use similar guidelines as above, using the diameter of the insert as the guiding dimension.
In comparison, parts made in a desktop 3D printer can be ready for delivery overnight, while industrial 3D printing systems have a typical lead time of 3-5 days. CNC machined parts are typically delivered within 10 days or as fast as 5 days.
The uniform wall thickness limitation also applies to edges and corners: the transition must be as smooth as possible to ensure good material flow. For interior edges, use a radius of at least 0.5 x the wall thickness. For exterior edges, add a radius equal to the interior radius plus the wall thickness. This way you ensure that the thickness of the walls is constant everywhere (even at the corners). Adding to this, sharp corners result in stress concentrations which can result in weaker parts.
All thermoplastics can be injection molded. Some thermosets and liquid silicones are also compatible with the injection molding process.
Almost every thermoplastic material (and some thermosets and silicones) can be injection molded. This gives a very wide range of available materials with diverse physical properties to design with.
When certain sections cool (and as a result shrink) faster than others, then the part can permanently bend due to internal stresses. Parts with non-constant wall thickness are most prone to warping.
Hunter, That product would be too large for us, and would likely need to be extruded. Try searching http://www.thomasnet.com for a large capacity plastic extruder.
Thank you for the inquiry. That does sound like something we can help you with but would need more information. Can you provide drawings or a link to a similar product? If so please send them to [email protected]
While you don’t need to know every detail about the types of molds available, it’s always a good idea to come prepared. Supplying the basics to your mold builder will help them build the best tool for your project. We recommend that you find a mold maker who also has production capabilities. The production company won’t want to build an inadequate mold because they know they must use it.
Injection molding is widely used today for both consumer products and engineering applications. Almost every plastic item around you was manufactured using injection molding. This is because the technology can produce identical parts at very high volumes (typically, 1,000 to 100,000+ units) at a very low cost per part (typically, at $1-5 per unit).
Thank you for the inquiry. If you submit CAD drawings we will provide a quote for the cost of the injection mold and production. Once the mold is built you own it and will only pay for production parts out of it. If the mold remains in our possession it comes with a lifetime guarantee. Hopefully this answers your questions.
To recognize them, look out for these 3 things: a parting line, witness marks on the hidden side and a relatively uniform wall thickness throughout the part.
The start-up costs for a large run can be expensive, but the price for the project becomes better and better as you continue to produce. If you’re looking at price per unit, plastic injection molding is one of the cheapest, most cost-efficient forms of manufacturing. With injection molding, the more units you create with your mold, the cheaper the price per unit becomes.
Avoiding undercuts altogether might be the best option. Undercuts always add cost, complexity, and maintenance requirements to the mold. A clever redesign can often eliminate undercuts. Shut-offs are a useful trick to deal with undercuts on internal regions of the part (for snap-fits) or on the sides of the part (for holes or handles).
Once the mold is manufactured, these complex parts can be reproduced at a very low cost. But changes to the mold design at later stages of development can be very expensive, so achieving the best results on the first time is essential. Follow the guidelines below to avoid the most common defects in injection molding.
When 2 flows meet, small hair-like discolorations may develop. These knit lines affect the parts aesthetics, but also they generally decrease the strength of the part. Parts with abrupt geometry changes or holes are more prone to knit lines.
Today, injection molding is a $300 billion market. 5+ million metric tons of plastic parts are produced with injection molding globally each year. Recently, the demand of biodegradable materials is increasing for environmental reasons.
The minimum order volume for injection molding is 500 units. For these quantities, the molds are usually CNC machined from aluminum. Aluminum molds are relatively easy to manufacture and low in cost (starting at about $3,000 to $5,000) but can withstand up to 5,000 - 10,000 injection cycles.
Donât get confused by the term âpilot runâ. If you only require a few thousand parts, then this would be your final production step.
If sections of different thickness are required, make the transition as smooth as possible using a chamfer or fillet. This way the material will flow more evenly inside the cavity, ensuring that the whole mold will be fully filled.
Thanks for the inquiry. This post helping me understand more about plastic injection mold and estimation on how much it costs. And I learned from your post what an injection mold is made of.
The most common Injection molding plastic. Excellent chemical resistance. Food-safe grades available. Not suitable for mechanical applications.
Avoid designing bosses that merge into main walls Support bosses with ribs or connect them to a main wall For bosses with inserts, use an outer diameter equal to 2Ã the insert’s nominal size
The typical injection molding cycle lasts 15 to 60 seconds, depending on the size of the part and the complexity of the mold. In comparison, CNC machining or 3D printing might require minutes to hours in order to produce the same geometry. Also, a single mold can accomodate multiple parts, further increasing the production capabillities of this manufacturing process.
I was wondering how many times your molds can be used? if i were to get a basic insert tooling mold would you be able to give me an estimate of how many times it could be used?
Below are some examples of how injection molded parts can be redesigned to avoid undercuts: essentially, material is removed in the area under the undercut, eliminating the issue altogether.
In this guide we touched on everything you need to get started with injection molding - but there’s plenty more to learn. Here are the most useful resources on injection molding and other digital manufacturing technologies if you want to delve deeper.
An additive that is commonly used to improve the stiffness of the injection molded parts is fiberglass. The glass fibers can be mixed with the pellets at ratios of 10%, 15% or 30%, resulting in different mechanical properties. Colorant can be added to the mixture (at a ratio of about 3%) to create a great variety of colored parts. Standard colors include red, green, yellow, blue, black and white and they can be mixed to create different shades.
At this stage, the typical cost per part varies between $1 and $5, depending on the geometry of your design and the selected material. The typical lead time for such orders is 6-8 weeks.
{{img}}*Example of a living hinge (left) and recommended design dimensions for PP or PE (right)*Before going to full-scale production, prototype your living hinges using CNC machining or 3D printing to determine the geometry and stiffness that best fits your application. Add generous fillets and design shoulders with a uniform wall thickness as the main body of the part to improve the material flow in the mold and minimize the stresses. Divide hinges longer than 150 mm in two (or more) to improve lifetime.For detailed guidelines, please refer to this MIT guide.
Injection molding typically produces parts with tolerances of ± 0.250 mm (0.010"). Tighter tolerances are feasible in certain circumstances (down to ± 0.125 mm - and even ± 0.025 mm), but they increase the cost drastically. For small production runs (< 10,000 units), consider using a secondary operation (such as drilling) to improve accuracy. This ensures the correct interference of the part with other components or inserts (for example, when using press fits).
Hollow out thick sections and use ribs to improve the strength and stiffness of the part Design ribs with max. thickness equal to 0.5x the wall thickness Design ribs with max. height equal to 3x the wall thickness
In 1869, John Wesley Hyatt invented celluloid, the first practical artificial plastic intended to replace ivory for the production of… billiard balls! Early injection molding machines used a barrel to heat up the plastic and a plunger to inject it to the mold.
I really like reading good articles by someone who knows a lot about what they’re writing. I’m excited to see more from you. Keep it up!
Below is a quick rundown of the key advantages and disadvantages of injection molding to help you understand whether it’s the right solution for your application.
But at least to some degree, asking what plastic injection molding costs is a lot like asking, “How much is a car?” Will your mold be a Pinto or a Porsche? And don’t forget that the price of a mold is just the beginning. To determine overall plastic injection molding costs for any project, you have to consider raw material, operation, and repair costs later down the road, too.
If you look around you right now, you’ll see at least a few products that were manufactured with injection molding. You’re probably looking at one right now actually: the casing of the device you are using to read this guide.
Thinner walls mean that the mold can be filled quicker. More importantly, parts thinner parts cool and solidify much faster. Remember that about half the injection molding cycle is spent on the solidification of the part while the machine is kept idle.
how much would a console mold cost and how many would i need? Same with controllers… do i need enough to make 100,000 a month?
Thank you for the request for quote, we appreciate the opportunity. The best opportunity we have to help make your project a success is if we have as much information as possible. If you could fill out the request for quote form on our website it will be a big step in that direction. It includes questions about material, annual estimated production quantities, etc. as well as the option to upload drawings or photos.
I’d be interested in finding out about plastic molded 9mm projectiles. There would have to be a denser plastic chosen, so there is enough recoil generated by the exiting projectile to cycle a semi-automatic pistol reliably.
Care must be taken through to not overly reduce the stiffness of the part which would downgrade its mechanical performance. Ribs in key locations can be used to increase stiffness.
Model airplanes are another common example of injection molded parts. The material used here is mostly Polystyrene (PS), for its low cost and ease of molding. What’s interesting with model airplane kits is that they come with the runner system still attached. So, you can see the path the melted plastic followed to fill the empty mold.
Snap-fit joints are a very simple, economical and rapid way of joining two parts without fasteners or tools. A wide range of design possibilities exists for snap-fit joints. As a rule of thumb, the deflection of a snap-fit joint mainly depends on its length and the permissible force that can be applied on it on its width (since its thickness is more or less defined by the wall thickness of the part). Also, snap-fit joints are another example of undercuts.
Jake, That is impossible to say without looking at the design, but as a general rule of thumb if you need 1,000 or more per year injection molding is worth looking at.
If your project requires large industrial molding machines that are operated by a service provider and large manufacturers, you’re looking at spending anywhere from $50,000 to $100,000+. Unlike the small desktop injection molding machine, these larger machines require professionals who can operate, maintain, and monitor the machine.
What would be the most logical approach if I wanted to create all four? All on one mold? Each geometrical type with their own mold? Then capacity wise, 10 000 a year? 100 000 a year?
George, Thank you for the inquiry. This product is too large for us but I will try to answer your questions. -You can have a multiple cavity mold made for this part. If you built a four cavity mold you would need at least a 5,500 ton molding machine (and about $200,000 for a domestically made mold). -With that mold you would probably get four parts every 2 or 3 minutes. -A single cavity mold would still be over $50,000. -Normally toolmakers will ask for 50% down with the remainder due once samples out of the mold are approved. -Toolmakers and molder are not bound to confidentiality unless you have them sign a non-disclosure agreement. Hopefully this helps, good luck!
One of the biggest benefits of injection molding is how easily complex geometries can be formed, allowing a single part to serve multiple functions.
Injection molding is an established manufacturing technology with a long history, but it’s constantly being refined and improved with new technological advancements.
Materials used in injection molding are plastics, specifically thermoplastics. There are hundreds of thermoplastics, but the most common thermoplastics used in injection molding are:
They can be also reinforced with fibers, rubber particles, minerals or flame retardant agents to modify their physical properties. For example fiberglass can be mixed with the pellets at ratios of 10%, 15% or 30% resulting in parts with higher stiffness.
The simplest mold is the straight-pull mold. It consist of 2 halves: the cavity (the front side) and the core (the back side).
Hi, Do you also provide molding with rubber or any other elastic material? Is it (NRE and price per part) usually more or less expensive than plastic ? tx, offer
To manufacture a mold with small details require longer machining and finishing times. Text is an example of this and might even require specialized machining techniques such as electrical discharge machining (EDM) resulting in higher costs.
The typical unit cost at this stage varies between a few cents to $1 and the typical lead time is 4 to 6 months, due to the complexity of designing and manufacturing the mold.
The typical turnaround for injection molding varies between 6-10 weeks. 4-6 weeks to manufacture the mold, plus 2-4 more weeks for production and shipping. If design changes are required (something quite common) the turnaround time increases accordingly.
That’s why we’ve compiled the following price guide to help you budget for your mold. The injection molding cost examples are categorized by type (Rapid Prototyping, Insert Tooling, High-Production Tooling), and degree of difficulty (Basic, Intermediate, Advanced).
Thank you for the inquiry. Unfortunately this product is too large for us. The largest footprint we can mold is approximately 100 square inches.
Reducing the wall thickness of your part is the best way to minimize the part volume. Not only does it mean less material is used, but also the injection molding cycle is greatly accelerated.
Thermoplastic with high impact strength and good mechanical properties & hardness. Suitable for molding parts with thick walls.
Lego bricks are one of the most recognizable examples of injection molded parts. They’re manufactured using molds, like the one in the picture, which produced 120 million lego bricks (that’s 15 million cycles) before it was taken out of commission. The material used for Lego bricks is ABS because of its high impact resistance and excellent moldabillity. Every single brick has been designed to perfection, achieving tolerances down to 10 micro meters (or a tenth of a human hair). This is partly achieved by using the best design practices, which we’ll examine in the next section (uniform wall thickness, draft angles, ribs, embossed text etc.).
An injection molding machine consists of 3 main parts: the injection unit, the mold - the heart of the whole process - and the clamping/ejector unit.
“On the other hand, if you are going to need 100,000 xbox controllers every month, we would build a 12 cavity hardened “family” mold which made four Fronts, four Backs, and four Button Trees every cycle, and you’d better have $60-$80,000 or more to invest.” is the 6o-8o,ooo dollars a yearly investment or a monthly investment?
As we saw in a previous section, fitting multiple parts in the same mold is common practice. Usually, 6 to 8 small identical parts can fit in the same mold, essentially reducing the total production time by about 80%.
For smaller productions (1,000 to 10,000 units), the cost of tooling has the greatest impact on the overall cost (approximately 50-70%). So, it’s worthwhile altering your design accordingly to simplify the process of manufacturing of the mold (and its cost).
Almost every plastic part around you was manufactured using injection molding: from car parts, to electronic enclosures, and to kitchen appliances.
Before you commit to any expensive injection molding tooling, first create and test a functional prototype of your design.
In this guide you’ll find everything you need to know about injection molding. Master the technology’s basic principles and learn actionable design tips fast that will save you time and cut costs.
Simon, Thank you for your inquiry. It’s difficult to say, but you might be about right. Features that will effect tooling cost are the finish you would like on the parts (polished is more expensive than textured), and where the drilling marks are located. If there are undercuts created by them in relation to the direction the part will need to be ejected out of the mold, moving cores would need to be designed into the molds, which will significantly increase the cost. If these concerns could be worked out, we could probably build two molds to shoot these sets for $30-$60,000. If you would like tighter figures, we would need to see drawings or prototypes. Thanks again for the inquiry.
Also raising the text 0.5 mm above the part surface will ensure that the letters are easy to read. We recommend selecting a bold, rounded font style with uniform line thickness, with a size of 20 points or larger. Some font examples include: Century Gothic Bold, Arial and Verdana.
Even if we take into account all other possible manufacturing technologies, injection molding with these four materials alone accounts for more than 40% of all plastic parts produced globally every year!
Great insights on the importance of precision in manufacturing. As a Welding and cutting machine manufacturers , Weldarc India understands the need for accuracy in welding and cutting processes. Our machines are designed to meet the demands of modern manufacturing with enhanced efficiency and precision. It’s exciting to see advancements in the industry that push the boundaries of what’s possible. Looking forward to continued innovations in welding and cutting solutions that contribute to high-quality production outcomes.
Hello, Just so I’m clear, you would charge for the creation of the mold, and then create the parts as needed/requested? You would see me back a finished product correct – as in you supply the materials, ship, etc? Thank you.
We do not have minimum order quantities, but there are set up fees amortized into each order so the cost effectiveness of low quantity orders is a decision left to our customers.
I needed 1000 unit of enclosure (approx size 100 x 100 x 23 mm, fillet corner radius 20), Finishing should be fine as much as possible. I have seen the mould manufacturing costs a lot, is there any other way to manufacture enclosures at lower cost.
Modelling a thread directly on the part is possible, but not recommended, as the teeth of the thread are essentially undercuts, increasing drastically the complexity and cost of the mold (we will more about undercuts in a later section). An example of an injection molded part with a thread are bottle caps.
Riser height will depend on how far the ejection needs to push your part before it’s completely free of the cavity and any cores. Completely free in this case meaning pushed all the way out/off so that there’s no chance it’ll get hung up on anything.
Bottom line in regards to NDA is whether or not you trust the molder. If they are a legitimate company that has been around for a long time, they’re probably not stealing people’s ideas. If you are naturally a cautious person or something doesn’t seem right with the molder, you’ll feel better having one in place. Hope this helps, let us know if you have and NDA you’d like us to review or if you would like to look at the one we use.
Living hinges are thin sections of plastic that connect 2 segments of a part and allow it to flex and bend. Typically these hinges are incorporated in mass-produced containers, such as plastic bottles. A well-designed living hinge can last for up to a million cycles without failure. The material used to injection mold a living hinge must be flexible. Polypropylene (PP) and Polyethylene (PE) are good choices for consumer application and Nylon (PA) for engineering uses.
When the interior of a part solidifies before its surface, a small recess in an otherwise flat surface may appear, called a sink mark. Parts with thick walls or poorly designed ribs are most prone to sinking.
Would like to mold adult male lacrosse stick heads, wondering how much each can cost, or how much a plastic injection machine would cost.
Learn more about the main cost drivers in injection molding and actionable design tips that will help you reduce the costs of your project.
Best way to deal with the created undercuts: Use a thread with a pitch greater than 0.8 mm (32 threads per inch) For external threads, place them along the parting line
Finishes are usually applied to the mold by hand, which can be an expensive process, especially for high-grade finishes. If your part is not for cosmetic use, donât apply a costly high-grade finish.
Specific guidelines on designing snap-fit joints is a big subject that goes beyond the scope of this article. For more detailed information, please refer to this article from MIT. For best results:
It’s worth looking into the mold base CAD libraries out there, such as through PCS. They’ll generate full, downloadable 3D CAD of their offerings based on the specs you plug into their forms.
Much needed information about the cost of plastic injection molds as knowing the price details are greatly helpful for the business.
Ejector (or witness) marks which are visible on the hidden B-side of the part. They are created because the ejector pins are slightly protruding above or indented below the surface of the mold.
Trapped air in the mold can inhibit the flow of the material during injection, resulting in an incomplete part. Good design can improve the flowability of the melted plastic. Parts with very thin walls or poorly designed ribs are more prone to short shots.
There is a range of machines used for injection molding. The cheapest option is a small desktop injection molding machine perfect for in-house projects. A small desktop injection molding machine is the most cost-effective choice for producing low volumes of parts.
For slides, start by sizing the slide face. This is the block which will have the undercut detail cut into it. The face doesn’t need to be much larger than the undercut itself, but it should be rectangular or circular just for ease of manufacturing and assembly. The surrounding part geometry could factor into this too, if the undercut is in a cramped spot or located near/on curved surfaces. Leave perhaps 0.375-0.500in of steel behind the undercut detail (same idea behind determining cavity plate thickness) and assume a 0.50-1.00in perimeter on either side of the face for other hardware like guide rails, and 1.0-2.0in above and below the face for wear plates, heel blocks and bolts. The slide may well take up more space than your cavities, and drive the mold size and plate thickness all by itself.
Thermoset with excellent heat & chemical resistance and customizable shore hardness. Food-safe and medical grade available.
Would it be possible for me to request solely 2 units for my design initiative? They are quite large with a 1-meter diameter and 1.5-meter length. How much would it cost for the production of this?
It is recommended to avoid stripping undercuts in parts made from fiber reinforced plastics. Typically, flexible plastics such as PP, HDPE or Nylon (PA) can tolerate undercuts of up to 5% of their diameter.
Do you need design-for-manufacturing (DFM) assistance? Or, are you ready for production? We have a full suite of services to offer and a lifetime mold guarantee.
For lower volume productions (less than 1000 parts), it may be more cost effective to use a secondary operation to complete your injection molded parts. For example, you could drill a hole after molding rather than using an expensive mold with side-action cores.
As the plastic shrinks, it applies pressure on the mold. During ejection, the walls of the part will slide and scrape against the mold, which can result to drag marks. Parts with vertical walls (and no draft angle) are most prone to drag marks.
However, needing 100,000 Xbox controllers every month is a different story. For this requirement, we would recommend building a 12-cavity hardened “family” mold, which would make four Fronts, four Backs, and four Button Trees every cycle. Of course, this type of mold comes with a cost. You’d better have $60-$80,000 or more to invest!
The simplest way to deal with an undercut is to move the parting line of the mold to intersect with it. This solution is suitable for many designs with undercuts on an external surface. Don’t forget to adjust the draft angles accordingly.
Crush Ribs are small protruding features that deform to create friction when different components are pushed together, securing their possition. Crush ribs can be an economical alternative for manufacturing high tolerance holes for tight fits. They are commonly used to house bearings or shafts and other press fit applications.
The plastic with the highest impact strength. High thermal resistance, weather resistance & toughness. Can be colored or transparent.
We do mold with thermoplastic elastomers, which are still considered a plastic. It is more expensive than a lot of other types, and could add $.50 for a 100 gram part when compared to ABS.
Side-action cores and the other in-mold mechanisms can increase the cost of tooling by 15% to 30%. This translates to a minimum additional cost for tooling of approximately $1,000 to $1,500.
Tooling costs are constant (starting at $3,000 and up to $5,000). This cost is independent of the total number of manufactured parts, while the material and production costs are dependent on the production volume.
I understand that the small extrustion between the faces of the spheres could be an issue when removing the part from the mold, so they would not be a necessity. The geometrical shapes are just a collection of planar faces which create a sphere.
To make the ejection of the part from the mold easier, a draft angle must be added to all vertical walls. Walls without a draft angle will have drag marks on their surface, due to the high friction with the mold during ejection. A minimum draft angle of 2° is recommended. Larger draft angles (up to 5o °) should be used on taller features. Learn more about the importance of draft angles in this article â
Rienk, Thank you for the inquiry. That’s difficult to estimate without more information, but generally speaking snap fit connections will add $500-$1,000 to the cost of a mold.
This post helping me understand more about plastic injection mold and estimation on how much it costs. And I learned from your post what an injection mold is made of
Find everything you need to know about 3D printing. Whether you are getting started or youâre an experienced user, youâll find this guide packed with useful tips.
I have an Idea…know nothing about this process, but here it goes. I wan’t to make a tool that will need Insert Molding? I know it’s a pricey operation, but to make it a durable and lasting tool it will have to be. I’d also like to have 6 to 8 tools made per cycle of the mold. the product would only be approx 5 to 6 inches long and 3/4 inch wide and approx 1/4 inch deep (approx). any idea (general idea) what this process would cost? I know there are many more details for plastic and metal applications, but a round about idea for a the mold would be helpful. Thank you.
Undercuts always add cost and complexity, as well as maintenance to the mold. A clever redesign can often eliminate undercuts.
These examples are extreme, but they illustrate the range of costs to anticipate. Your particular part will most likely fall somewhere in between that. At Rex Plastics, our molds average around $12,000.
Add a draft angle to the vertical walls of your snap-fit joints Design snap-fits with thickness greater than 0.5x the wall thickness Adjust their width and length to control their deflection and permissible force
High-performance engineering thermoplastic with excellent strength and thermal & chemical resistance. Used to replace metal parts.
The Society of Plastics Industry (SPI) explains several standard finishing procedures that result in different part surface finishes.
Material selection is another consideration in determining what plastic injection molds cost. Any plastic product made from fiberglass-filled material, for example, will wear down most common molds. Only a mold made from hardened tool steel can withstand injection molding with fiberglass-filled material.
Hi, what are the estimated costs of a mold for a part with snap fit connections compared to the same part but instead of snap fit connections holes for bolts?
Side-action cores are moving elements that enter the mold from the top or the bottom and are used to manufacture parts with overhangs (for example, a cavity or a hole). Side-actions should be used sparingly though, as the cost increases rapidly.
Recommended: 3 Ã wall thickness difference Sometimes sections with different wall thicknesses cannot be avoided. In these cases, use a chamfer or fillet to make the transition as smooth as possible. Similarly, the base of vertical features (like ribs, bosses, snap-fits) must also always be rounded.
When producing parts massive quantities of identical parts (from 10,000 to 100,000+ units) then special Injection molding tooling is required.
Use a uniform wall thickness within the recommended values When different thickness are required, smoothen the transition using a chamfer or fillet with length that is 3x the difference in thickness
Thank you for the inquiry. That does sound like something we can help you with. If you could please fill out our request for quote page on this site we can provide a quote. You can upload drawings there as well.
As for plate thickness, leave at least 0.5in of steel between the upper and lowermost cavity extremities and the backsides of the cavity plates/cores. Depending on part geometry, you might need up to one full inch above and below the cavities for water lines.
For best results: Use embossed text (0.5 mm height) instead of engraved texted Use a font with uniform thickness and a minimum font size of 20 points Align the text perpendicular to the parting line Use a height (or depth) greater than 0.5 mm
Nicole, Thank you for the inquiry. A Jackson Pratt bulb is blow molded, not injection molded. Please see this article for more explanation. https://rexplastics.com/plastic-injection-molding/the-many-processes-of-plastic-part-manufacturing
For these volumes, the molds are CNC machined from tool steel and can withstand millions of Injection molding cycles. They are also equipped with advanced features to maximize production speeds, such as hot-tip gates and intricate cooling channels.
Sliding side-actions and cores are used when it is not possible to redesign the injection molded part to avoid undercuts. Side-action cores are inserts that slide in as the mold closes and slide out before it opens. Keep in mind that these mechanisms add cost and complexity to the mold. Follow these guidelines when designing a side actions:
The enclosures of almost every mass-produced consumer electronic device was injection molded. ABS and polystyrene (PS) are prefered here for their excellent impact resistance and good electrical insulation.
In some cases, the main body of 2 parts of an assembly is the same. With some creative design, you can create interlocks points or hinges at symmetrical locations, essentially mirroring the part. This way the same mold can be used to manufacture both halves, cutting the tooling costs in half.
Parts produced with injection molding have very good physical properties. Their properties can be tailored by using additives (for example, glass fibres) or by mixing together different pellets (for instance, PC/ABS blends) to achieve the desired level of strength, stiffness or impact resistance.
Hi am new here, after I submit the CAD file will I pay $60 we part or I don’t understand. after making mold what part will I pay for again?
Undercuts in injection molding are part features that cannot be manufactured with a simple two-part mold, because material is in the way while the mold opens or during ejection.
If you’re thinking of outsourcing your mold-making overseas, consider all of the factors in bringing the mold to optimum production standards outlined in this American Mold Builders Association article. You might be surprised to learn the true cost of off-shoring!
Hi I’m trying to get a project started and luckily I found the guides and explanations here, good stuff. With the guide my estimate is somewhere between 15 000 to 30 000.
The mold is like the negative of a photograph: its geometry and surface texture is directly transferred onto the injection molded part. It usually makes up the largest portion of the start-up costs in injection molding: the cost of a typical mold starts at approximately $2,000-5,000 for a simple geometry and relatively small production runs (1,000 to 10,000 units) and can go upwards to $100,000 for molds optimized for full-scale production (100,000 units or more). This is due to the high level of expertise required to design and manufacture a high-quality mold that can produce accurately thousands (or hundreds of thousands) of parts. Molds are usually CNC machined out of aluminum or tool steel and then finished to the required standard. Apart from the negative of the part, they also have other features, like the runner system that facilitates the flow of the material into the mold, and internal water cooling channels that aid and speed up the cooling of the part. Learn more about CNC machining in the manufacturing and design guide â Recent advances in 3D printing materials have enabled the manufacturing of molds suitable for low-run injection molding (100 parts or less) at a fraction of the cost. Such small volumes were economically unviable in the past, due to the very high cost of traditional mold making.
Chris, Thank you for the inquiry, I appreciate the opportunity. Without seeing the geometry it’s difficult to estimate cost. Our pricing guide can give an indication of cost, although it does not giving multi-cavity pricing.
An example of a part with crush ribs is shown below. Using three crush ribs is recommended to ensure good alignment. The recommended height/radius for each rib is 2 mm. Add a minimum interference of 0.25 mm between the crush rib and the fitted part. Because of the small surface contact with the mold, crush ribs can be designed without a draft angle.
We have not made any golf disc parts specifically but that is well within our capability. Please contact us for a free quote if you are interested.
Many sterilizable and biocompatible materials are available for injection molding. Medical grade silicone is one of the more popular materials in the medical industry. Silicone is a thermoset though, so special machinery and process control are required, increasing the cost. For applications with less strict requirements other materials, like ABS, polypropylene (PP) and Polyethylene (PE), are more common. Learn more about medical device manufacturing â
Your estimate cost for a steel p20, one cavity, cold runner, polypropylene 30%Gf matrix, with sizes of: 660mm x 220mm x 200mm. Thanks.
Hi, Would you be able to create a mold for a golf bag, and provide a quote? Approximately 35″ tall, with a diameter of 11.5″ x 10″. I’d also like to include dividers in the middle. Thank you.
Parting lines which are visible on the side of a part where the 2 halves of the mold meet. They are caused by tiny misalignments and the slightly rounded edges of the mold.
Almost every plastic component in the interior of a car was injection molded. The 3 most common injection molding materials used in the automotive industry are Polypropylene (PP) for non-critical parts, PVC for its good weather resistance and ABS for its high impact strength. More than half of the plastic parts of a car are made from one of these materials, including the bumpers, the interior body parts and the dashboards.
Thank you for the request for quote, I appreciate the opportunity. The best opportunity we have to help make your project a success is if we have as much information as possible. If you could fill out our request for quote form our website it will be a big step in that direction. It includes questions about material, annual estimated production quantities, etc. as well as the option to upload drawings.
Thanks for this post, somewhat it helped me understand more about plastic injection mold and an estimation on how much it costs.
On the far side of an injection molding machine is the clamping system. The clamping system has a dual purpose: it keeps the 2 parts of the mold tightly shut during injection and it pushes the part out of the mold after it opens.
I’m working on a school project, I was wondering how much it would cost to make a mold that contains 25 cavities, the part is kind of cylindrical and I was planning to have it made out of high density polyethylene. It has a hole straight through the part with an inside diameter of 0.515″ and an outside diameter of 0.670″ for 0.773″ of the height and an outside diameter of 1.340″ for the remaining 0.327″ of the height, the height is 1.100″ total. This is the link to the photo: https://drive.google.com/file/d/0BxyuyPDgKAbnMXdHbE1GeTA5bms/view?usp=sharing https://drive.google.com/file/d/0BxyuyPDgKAbnN0xMSjJkNzdIUE0/view?usp=sharing
Small sidenote, plan on leaving at least 0.250in of metal around all water lines. If not maintained properly they’ll eventually corrode thin walls. This consideration has occasionally led us to quoting larger mold bases.
There are several factors that may affect the quality of the final product and the repeatability of the process. To yield the full benefits of the process, the designer must follow certain design guidelines. In this section, we outline common defects of injection molding and basic and advanced guidelines to follow when designing parts, including recommendations for keeping the costs to a minimum.
We could put multiple figurines in one mold but injection molding may not be the best process if you are anticipating low volumes. 1,000+ per year may start to make sense for injection molding, otherwise you may want to talk to a plastic prototyper or polymer casting company. We can mold them in any color, but the entire figurine would be the same color. If you have drawings you can attach them to our Quote Now link and we can provide a quote.
Injection molding is compatible with a wide range of plastics. In this section, you’ll learn more about the key characteristics of the most popular materials. We’ll also discuss the standard surface finishes that can be applied to injection molded parts.
Engineering thermoplastic with excellent mechanical properties and high chemical & abrasion resistance. Susceptible to moisture.
Hello, When submitting CAD specs to you or any injection mold company, do you recommend a Non-Disclosure Agreement be signed to protect a project?
Alignment of the different moving parts of the mold is never perfect though. This causes the creation of 2 common imperfections that are visible on almost every injection molded part:
The Injection molding plastic with the lowest cost. Food-safe grades available. Not suitable for mechanical applications.
Yes that is correct. After we build the mold (that you own), we store it here and run parts from it when you send us a PO.
Injection molding cost can range anywhere from $100 to $100,000+ depending on the scope and intricacy of the project. A small and simple single-cavity plastic injection mold usually costs between $1,000 and $5,000. Very large or complex molds may cost as much as $80,000 or more. On average, a typical mold that produces a relatively simple part small enough to hold in your hand costs around $12,000.
A key strength of injection molding is it can produce finished products that need little to no extra finishing. The surfaces of the mold can be polished to a very high degree to create mirror-like parts. Or they can be bead blasted to create textured surfaces. The SPI standards dictate the level of finishing that can be achieved.
Thick sections can lead to various defects, including warping and sinking. Limiting the maximum thickness of any section of your design to the recommended values by making them hollow is essential.
Thank you for your inquiry. Here is a link to a pricing guide that will get you headed in the right direction. https://rexplastics.com/injection-mold-price-guide Rex Plastics, Inc
The main economic restriction of injection molding the the high cost of tooling. Since a custom mold has to be made for each geometry, the start-up costs are very high. These are mainly related to the design and manufacturing of the mold which typically costs between $5,000 and $100,000. For this reason, injection molding is only economically viable for productions larger than 500 units.
Learn all you need to know about CNC machining in 25 minutes or less. Whether you are an experienced design engineer or just getting started with manufacturing, this guide is for you.
What is a injection molding? How does it work and what is it used for? In this section, we answer these questions and show you common examples of injection molded parts to help you familiarize yourself with the basic mechanics and applications of the technology.
Thank you for the inquiry Ali. All of our molds have a lifetime guarantee so even if your mold wears, you won’t see a repair bill from us. Generally speaking a hardened steel mold or insert should last 100,000 cycles or more.
If you have a target price established for your parts, tell your mold builder. They can design the mold accordingly and plan for the right number of cavities to achieve that price. The more cavities (or parts made per cycle), the less expensive the parts will be, also allowing for higher output.
Add a fillet equal to 0.5x the wall thickness to internal corners Add a fillet equal to 1.5x the wall thickness to external corners
The simplest mold (the straight-pull mold) consist of 2 halves. Features with undercuts (such as the teeth of a thread or the hook of a snap-fit joint) may not be manufacturable with a straight-pull mold though. This is either because the mold cannot be CNC machined or because the material is in the way of ejecting the part.
Kelsey, Thanks you for the inquiry. That’s difficult to say without seeing the part. Small details in the design can make big differences in cost to manufacture. If it is a simple design with no undercuts and the surface doesn’t require polishing, you could perhaps get a mold built for $5-$8,000. Here is a link to a pricing guide for further reference. https://rexplastics.com/injection-mold-price-guide
In a previous section, we examined ways to deal with undercuts. To keep your production on-budget, avoid using side-action cores and other mechanisms unless absolutely necessary.
The injection molding process is highly repeatable and the produced parts are essentially identical. Of course, some wear occurs to the mold over time, but a typical pilot-run aluminum mold will last 5,000 to 10,000 cycles, while full-scale production molds from tool steel can stand 100,000+ cycles.
Hi, thanks for your contribution on Injection molding . I have basic knowlegde on mold design and would like to know how can I estimate overall mold dimensions based on part dimensions, considering one cavity mold and and no side actions. Also would like to know how can I estimate the approximate size of a slider for a side simple hole. Thanks for you support. Much appreciate. Regards
But compared to other technologies, the start-up costs of injection molding are relatively high, mainly because custom tooling is needed. A mold can cost anywhere between $3,000 and $100,000+, depending on its complexity, material (aluminum or steel) and accuracy (prototype, pilot-run or full-scale production mold).
This step is essential for launching a successful product. This way design errors can be identified early, while the cost of change is still low.
Many plastic packaging products are injection molded. In fact, packaging is the largest market for injection molding. For example, bottle caps are injection molded from Polypropylene. Polypropylene (PP) has excellent chemical resistance and is suitable to come in contact with food products. On bottle caps, you can also see all the common unavoidable injection molding imperfections (parting line, ejector marks etc.) and common design features (ribs, stripping undercuts etc.).
A well-designed hinge is shown below. The recommended minimum thickness of the hinge ranges between 0.20 and 0.35 mm, with higher thicknesses resulting in more durable, but stiffer, parts.
To improve the strength of hollow section, use ribs to design structures of equal strength and stiffness but reduced wall thickness. A well-designed part with hollow sections is shown below:
The purpose of the injection unit is to melt the raw plastic and guide it into the mold. It consists of the hopper, the barrel, and the reciprocating screw.
If you would like to send any drawings you have to our contact email directly we can provide an estimate. [email protected]
Use a uniform wall thickness throughout the part (if possible) and avoid thick sections. This is essential as non-uniform walls can lead to warping or the part as the melted material cools down.
At the point where the runner system connected with the part, a small imperfection is usually visible, called the vestige. If the presence of the vestige is not desirable for aesthetic purposes, then in can also be “hidden” in the functional B-side of the part.
Injection molding is so popular, because of the dramatically low cost per unit when manufacturing high volumes. Injection molding offers high repeatability and good design flexibility. The main restrictions on Injection Molding usually come down to economics, as high initial investment for the mold is required. Also, the turn-around time from design to production is slow (at least 4 weeks).
Here is a list of defects to keep in mind while designing a part for injection molding. In the next section, we’ll see how you can avoid each of them by following good design practices.
The $60-$80,000 is a non-recurring expense to build the mold. Once the mold was built you would just pay for production parts as need. Probably around $1 per set at that point.
Hi, Thanks for your valuable post… I really appreciate your great work. This post helped me understand more about plastic injection mold and estimation on how much it costs. An injection mold is easily the most expensive part of the project, and can dramatically increase costs for small part runs. The main factors that influence the cost of an injection mold are the size and intricacy of the part, the material used, and the number of parts being produced.
The cost of the material you use for your project is usually decided by the design, material chosen, and the amount you need to complete the project. Here is a quick chart explaining more about each thermoplastic material, their features, common applications and price per pound.
The teeth of a thread or the hook of a snap-fit joint are examples of undercuts. Here some ideas to help you deal with undercuts:
What I have is four different geometrical round shapes of varying face counts with some small extruded borders between the faces. They’d be hollow so they’d be cut in a symmetrical manner so that two printed halves can be glued together to form a whole hollow sphere. All spheres are around 7,5 cm in diameter, about 3 inches, and half that in height due to them being halves. Additionally they’d have holes in specific places on the spherical surface but that could be drilled aftetwards, so just some sort of mark where the holes are supposed to be would be sufficient.
First you locate and orient the part in the tool, which mainly depends on where/how you intend to gate it. For all gate types except center, you should have at least 0.75-1.00in of space between the sprue and the edge of the cavity. Once you have a cavity layout (assume centered sprue), determine its bounding box. Any space off-center will need to be mirrored on the other side of the sprue and included in this bounding box. In a sense, you’ll always be sizing a mold for two cavities unless you’re center-gating. For smaller molds under 12in per side (in the parting plane), you can get away with leaving 2in of space all around this bounding box. This space is occupied by the ejector housing, return pins, and leader pins among other things, all of which would interfere with the part cavities and/or their ejection. You may need extra space for cooling lines as well. For larger molds up to 24in per side, you’ll want at least a 2.5in perimeter.
Most defects in injection molding are related to either the flow of the melted material or its non-uniform cooling rate during solidification.
After a mold is manufactured, it’s very expensive to modify. Design changes usually require the creation of a new mold from scratch. For this reason, correctly designing a part for injection molding is very important.
Hello, I have designed a product that I believe the best way to manufacture will be through injection molding. I cannot share too much, but for the sake of this comment lets imagine that it is a hollow box with 1/4″ walls, 1 face missing, and that it is 1′ 8″ W x 1′ 11″ L x 1′ 3″ H. Now I understand that pricing is complex so I won’t ask you for a quote without sending the file, and I will assume that the mold will cost no less than $50,000 which is fine. My questions are below: – Considering the dimensions of the extents, is it possible to create a family mold with multiple units? What would be the maximum units per mold? And around how many could be banged out per day (again assume its a 1/4″ wall box as stated above for now)? – How long does the process of making the mold take (assuming the design and specs are ready)? – Do I have to pay the full amount immediately, or can it be paid in installments? – If I were to send over a .dwg file for a quote, are you legally bound by confidentiality? Thank you in advance!
In most cases, straight-pull molds are preferred, as they are simple to design and manufacture, keeping the total cost relatively low. There are some design restrictions though: the part must have a 2.D geometry on each side and no overhangs (i.e. areas that are not supported from below).
Stripping undercuts (also known as bumpoffs) can be used when the feature is flexible enough to deform over the mold during ejection. Stripping undercuts are used to manufacture the threads in bottlecaps. Undercuts can only be used under the following conditions:
For larger volumes to full-scale production (10,000 to 100,000+ units), the contribution of the tooling costs to the overall cost is overshadowed by the material and production costs. So, your main design efforts should focus on minimizing both the volume part and the time of the molding cycle.
Here, we touched upon all you need to get you started with injection molding. There is plenty more to learn though in our Knowledge Base - a collection of technical articles on all manufacturing technologies, written by experts from Protolabs Network and the manufacturing industry.
There are 3 ways to add fasteners to an injection molded part: by designing a thread directly on the part, by adding a boss where the screw can be attached, or by including a threaded insert.
Engineering thermoplastic with high strength, stiffness & moisture resistance and self-lubricating properties. Relatively prone to warping.
Quality articles for engineers and designers to learn about Digital Manufacturing. Written by manufacturing experts, curated by Protolabs Network.
Johnny, Thank you for the inquiry. Non-disclosure agreements are common in manufacturing so any molder you choose should not resist signing one unless it’s determined to lack certain exclusions and the ability of the molder to disclose information to third parties with written permission. Molders will often need to involve third party companies in order to provide a quote.
Without seeing the specific design it’s difficult to give an estimate. Sometimes even small design features can add thousands to the cost of the mold. If you have a drawing we could provide a free quote.
The last thing to consider when pricing out your injection molding cost is the cost of service or professional labor you will need. Professionals can help you set up the necessary equipment to create molds and your products. During the process, they’ll be able to replace defective parts and monitor the progress of the overall process.
Thank you for the request for quote, I appreciate the opportunity. I don’t know what that would take. The highest specific gravity for readily available material is around 1.4. I would recommend researching how that compares to what is currently used. I know that some law enforcement agencies are using rubber bullets now but I don’t know if any sort of ejection assistance is used. Please contact us via [email protected] if you’d like to discuss further.
In the mid 1950s, the invention of the reciprocating screw single-handedly revolutionized the plastics industry. The reciprocating screw solved key issues with uneven heating of the plastic that previous systems faced, and opened up new horizons for the mass production of plastic parts.
We’ve collected some examples of products commonly manufacturing with injection molding to help get a better understanding of what can be achieved with this manufacturing process.
Hi, Thank you for all the valuable information laid out on your site. My company has created molds and manufactured exclusively overseas, but I have tried to bring my business back stateside many times and have always found it difficult, biggest issue being MOQs. When creating a new product as a small business it’s difficult to run thousands or tens of thousands of units on a first run for an unproven product. My question is, after the mold is produced what is the average MOQ? What is your typical floor? What are the determining factors for the MOQ?
If you wouldn’t mind, how much would you ball park the cost to produce the mold, and the parts, of a standard size plastic shopping cart? Needing 100,000-500,000 units per year. I appreciate your time.
I’m working on a school invention project and I need to know how much a mold for a half-pipe like design would cost. The thickness of the mold needs to be 1.5 inches, it is 1.5 feet high (bottom to top), 5 feet wide (left to right) and is 20 feet long (front to back). If you can estimate the price to the nearest thousand, that would be great. Thank you.
I’m glad you mentioned having a target price ready before designing a mold. I have a few things I want to start molding, but I hadn’t thought about a price yet. I can see how that would make a big difference in how they would plan how many parts to make.
Parts with different geometries can also fit in the same mold (remember, the model airplane example). This is a great solution for reducing the overall cost of assembly.
Thank you for the inquiry. Mold balancing plays an important role in injection molding, because of that we would recommend a 24 cavity mold. The parts are divisible in pairs with that amount and will run much better. The ballpark estimate for a cold runner mold that size would be $15-$20,000, and the part price would be under $.09 each for 20,000 parts ordered.
I’m considering syringe barrels to be injection molded. About 3 mL and 6 mL (two different sizes) with qty of 20,000 per month for now. Actually syringe barrels without the thread, but with luer male at the end. Just empty straight (slightly tapered). Material PP.
All thermoplastic materials can be injection molded. Some types of silicone and other thermoset resins are also compatible with the injection molding process. The most commonly used materials in injection molding are:
The recommended minimum production volume for injection molding is 500 units. At this point economies of scale start to kick-in and the relatively high initial costs of tooling have a less prominent effect on the unit price.
Blend of two thermoplastics resulting in high impact strength, excellent thermal stability, and high stiffness. Vulnerable to solvents.
I’m doing a project and I was wondering how much would the injection mold cost for a width:10 inch length:15 inch height 3 inches the top lid would be the same dimensions.
Text is a very common feature that can be useful for logos, labels, warnings, diagrams and instructions, saving the expense of stick-on or painted labels. When adding text, choose embossed text over engraved text, as it’s easier to CNC machine on the mold and thus more economical.
A good rule of thumb is to increase the draft angle by one degree for every 25 mm. For example, add a draft angle of 3o degrees to a feature that is 75 mm tall. Larger draft angle should be used if the part has a textured surface finish. As a rule of thumb, add 1o to 2o extra degrees to the results of the above calculations. Remember that draft angles are also necessary for ribs. Be aware though that adding an angle will reduce the thickness of the top of the rib, so make sure that your design complies with the recommended minimum wall thickness.
Eloi, Thank you for the inquiry. Bottles are blow molded, not injection molded so we couldn’t answer that question. Here is a link to out knowledge base for more information: https://rexplastics.com/knowledge-base/product-development
Smaller parts can be molded faster resulting in a higher production output, making the cost per part lower. Smaller parts also result in lower material costs and reduce the price of the mold.
The parts manufactured with “pilot” aluminum molds have physical properties and accuracy identical to parts manufactured with âfull-scale productionâ tool steel molds.
Interesting fact: About 50% of the typical injection molding cycle is dedicated to cooling and solidification. Minimizing the thickness of a design is key to speed up this step and cuts costs.
I always enjoy reading quality articles by an individual who is obviously knowledgeable on their chosen subject. I’ll be watching this post with much interest. Keep up the great work…
The runner system is the channel that guides the melted plastic into the cavity of the mold. It controls the flow and pressure with which the liquid plastic is injected into the cavity and it is removed after ejection (it snaps off). The runner system usually consists of 3 main sections:
Once your design ready and optimized for injection molding, whatâs next? In this section we’ll take you through the steps needed to start manufacturing with injection molding.
In order to understand what the injection molding cost of your project may be, you need to understand the process and factors that will affect the price of your project.
Thank you for the request for quote, we appreciate the opportunity. Unfortunately this product is too large for us. The largest footprint we can mold is approximately 100 square inches.
Unfortunately this product is too large for us. The largest footprint we can mold is approximately 100 square inches, and the tallest piece around 10″.
Bosses are very common in Injection Molded parts and are used as points for attachment or assembly. They consist of cylindrical projections with holes designed to receive screws, threaded inserts, or other types of fastening and assembly hardware. A good way to think of a boss is as a rib that closes on itself in a circle. Bosses are used as points of attachment or fastening (in conjuction with self-tapping screws or threaded inserts).
Injection molding is a manufacturing technology for the mass-production of identical plastic parts with good tolerances. In Injection Molding, polymer granules are first melted and then injected under pressure into a mold, where the liquid plastic cools and solidifies. The materials used in Injection Molding are thermoplastic polymers that can be colored or filled with other additives.
 The image below shows the mold used to manufacture both sides of the casing for a remote controller. Quick quiz: try to locate the *core* (A-side), the *cavity* (B-side), the runner system, the ejector pins, the side-action core and the air vents on this mold.
In Part 2, we list the most important design considerations to keep in mind while designing for injection molding. It Part 5, we’ll also see how you can mitigate the risk by creating physical prototypes of your parts.
Injection molded parts have two sides: the A side, which faces the cavity (front half of the mold) and the B side, which faces the core (back half of the mold). These two sides usually serve different purposes:
When even the maximum recommended wall thickness is not enough to meet the functional requirements of a part, ribs can be used to improve its stiffness. When designing ribs: â Use a thickness equal to 0.5 Ã main wall thickness
Learn how to design the most common features encountered in injection molded parts with these practical guidelines. Use them to improve the functionality of your designs, while still complying with the basic design rules.
As a full-service plastic injection molding company that manufactures molds from conception to completion, pricing for each job we fulfill can vary dramatically.
hi I’m doing a school project and I need to know how much it will cost to make a simple 3,109 volumed container 12×14 container for the base and 12×14 for 2 sides and 14×20 for the other so 12=l 14=w 20=h
Surface finishes can be used to give an injection molded part a certain look or feel. Besides cosmetic purposes surface finishes can also serve technical needs. For example, the average surface roughness (Ra) can dramatically influence the lifetime of sliding parts such as plain bearings. Injection molded parts are not usually post-processed, but the mold itself can be finished to various degrees. Keep in mind that rough surfaces increase the friction between the part and the mold during ejection, therefore a larger draft angle is required.
Typically, injection molding will produce parts with tolerances of ± 0.500 mm (0.020ââ). Tighter tolerances down to ± 0.125 mm (0.005ââ) are also feasible in certain circumstances. This level of accuracy is enough for most applications and comparable to both CNC machining and 3D printing.
Thanks a lot for sharing this awesome info. Your article is excellent and informative. I love to read your articles.i personally like all the points you explain and follow it. Everyone should read this awesome post, I will share with my friends. Keep it up with such great content
In this section, we examine the purpose of each of these systems and how their basic operation mechanics affect the end-result of the Injection molding process.
Injection molding is the most cost-competitive technology for manufacturing high volumes of identical plastic parts. Once the mold is created and the machine is set up, additional parts can be manufactured very fast and at a very low cost.
Thanks for helping me learn more about plastic injection molds. I didn’t know that molds should be made from harden steel if a product needs a fiberglass filled material. I’m interested to learn how these molds could be made, especially of the steel mold needs to be really precise.
GETTING A QUOTE WITH LK-MOULD IS FREE AND SIMPLE.
FIND MORE OF OUR SERVICES:
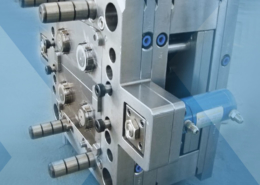
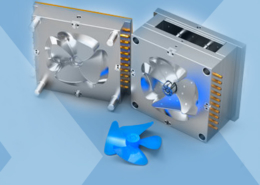
Plastic Molding

Rapid Prototyping
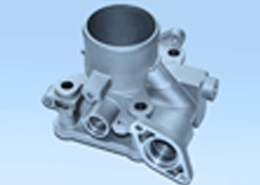
Pressure Die Casting
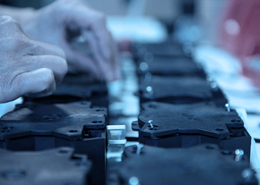
Parts Assembly
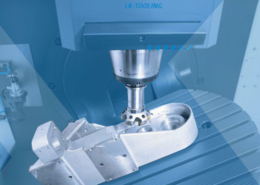