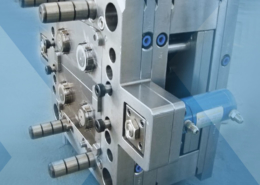
Large Size Plastic Injection Molds From Richfields ... - large scale injection m
Author:gly Date: 2024-10-15
– Reduce the injection speed. High plastic injection speeds can cause jetting, which causes trapped air to appear right at the inlet gate. Reducing the injection speed will give the displaced air at the gate enough time to escape through the aeration zones.
Occasionally, the use of high compaction pressures causes acceptable sink marks by reducing volumetric shrinkage although these cannot be completely eliminated. This is because the volumetric change of plastic from melt to solid is about 25% and the compressibility of plastics at typical injection moulding pressure is only 15%, which means that it is impossible to compact the molten plastic sufficiently to compensate for cooling shrinkage.
The jetting defect occurs when molten polymer is pushed at speed through a small area, such as the injection nozzle or gate, to access a much larger area. The jetting defect results in mechanical weakness in the part, surface imperfections and multiple internal defects.
The burr is a defect that occurs when part of the molten polymer flows through the existing gaps in the injection mould such as parting plane, aeration zones, ejectors, etc. Burring occurs for the following reasons:
Incomplete filling occurs when a one injection moulded part is missing material to correctly generate its geometry. This occurs when the molten polymer cannot fill the entire cavity (or cavities) in the Injection mould, usually the thinner sections where the polymer melt cools before completely filling the mould. Any factor that increases the flow front resistance of the polymer melt can result in incomplete filling. Some of these factors are:
The formation of wrinkles or waves is due to the fact that a part of the flow front cools rapidly on the mould walls producing a fold on the flow front itself. Themain factors influencing the formation of these wrinkles are the flow velocity, the temperature of the mould walls, and the temperature of the molten polymer, among others.
Hot Runner Temperature Controller also called HRTC in short form. Hot runner temperature controller is used to run mainly Plastic Injection Molding Machine's molds. Let's try to understand 2 main types of molds. Hot Runner vs Cold Runner Injection Mold: Key Differences You Need to Know   Home Blog Hot Runner vs Cold Runner Injection Mold: Key Differences You Need to Know Hot Runner vs Cold Runner Injection Mold: Key Differences You Need to Know Updated: October 17, 2022 An injection mold is a component designed according to the intended product using processes such as CNC machining and is where the molten plastic is injected and cooled. There are several injection molds types. However, based on the temperature held by the runner and the mold,  there are two mold systems: hot runner and cold runner. Each mold system uses a different mechanism which affects plastic fabrication differently. As a result, there is a need for a proper understanding of the hot runner mold vs cold runner mold comparison before selection. This article does the hot runner vs cold runner injection molding comparison by introducing both systems, how they work, and their differences. Furthermore, it shows how to choose the right mold for your project.   What is a Hot Runner Mold?  A hot runner mold is an injection mold with a manifold system (i.e., containing a heating component, manifold, and nozzle) that ensures that molten plastic injected into the mold maintains its temperature. Hot runner injection molding is suitable for molding plastics that require steady flow and injection pressure for part fabrication. Furthermore, with the method, there is a reduction in defects such as sink marks that occur due to fluctuating injection pressure and underfilled molds. Types of Hot Runner Mold Based on the method of maintaining the heat, here are the two types of hot runner molds used in plastic injection molding: Insulated Hot Runners Insulated hot runners molds have extremely thick runners in the mold plate, which causes part of the molten plastic to cool down and insulate the system. The insulation reduces heat loss, allowing the mold system to maintain an open plastic flow. Insulated hot runner molds are less expensive than heated ones because they do not use manifolds and drops. Furthermore, they have flexible gates, reduced defects, and favor easy color change. However, it has a few disadvantages, such as freeze-ups at the gate, non-uniform mold filling, long start-up periods, and the need for a fast cycle to maintain the thermoplastic molten state due to the absence of a manifold system.  Heated hot runners The heated hot runner is the major type of hot runner system with heating achievable using a heating component in one-half of the mold. However, they come in two designs: externally heated and internally heated. Externally heated hot runners: The heating component is outside the mold. As a result, there is no obstruction in the molten thermoplastic flow (better flow control) and no drop in injection pressure. Furthermore, the molten plastic does not freeze and is ideal for color change. Externally heated hot runner molds are suitable for thermosensitive materials. Internally heated hot runners: Here, the heating component is in the mold, leading to a drop in injection pressure, incompatibility with color change, and material hanging up and degrading in the mold. However, there is better flow due to the heated runner and gate tip control. What is a Cold Runner Mold?  A cold runner mold is the basic injection mold with runners at the same temperature as the mold cavity. The system involves injecting the molten plastic into locating ring. Afterward, the molten plastic passes through a sprue and runner, which are cold, before entering the mold cavity. As a result, when the plastic cools, it takes the shape of the mold cavity with the solidified plastic in the runner attached. The cold-runner mold features a large runner (larger than the part), removing the tendency of underfilling the mold. Aside from that, it is suitable for working with any plastic polymer irrespective of heat sensitivity, is less expensive than hot runners, and is easily maintained. However, they generate waste. Types Of Cold Runner Systems There are two types of cold runner molds system based on the number of mold plates: · Two Plate Cold Runner System The two-plate cold runner system comprises two plates with the stationary mold containing the sprue, runners, gate, and cavities. It is the fastest, simplest, and least costly cold runner system. However, the runner is attached to the final product and should be cut off. · Three Plate Cold Runner System A three-plate cold runner system is similar to the two-plate system. However, the three-plate injection mold is flexible with an additional runner plate. Furthermore, there is no need to cut the runner from the injection molded part, and the mold does not require an ejection system for part removal. 3 plate injection mold is friendlier and more flexible. They are the most suitable for working with products with complex designs, and they are a lower-cost alternative to hot runner systems. Disadvantages of this injection mold include long cycle time, complex tool design, and high material waste. Hot Runner Mold vs Cold Runner Mold â Advantages of Each System Each runner mold has its advantages making them suitable for different applications and industries. Here, we will talk about their advantages and how they compare. Hot Runner System Advantages The hot runner system is widely applicable in plastic product fabrication due to the following advantages: Reduced cycle time: One main difference between a hot runner and cold runner injection molding is the cycle time. Hot runner injection molds have a faster cycle time due to the plastic being kept at optimum temperature, increasing flowability. Reduced material wastage: Itâs more cost-effective as the mold system generates little to no material waste.    Optimal Part Quality: Parts made using hot runner molds have better final quality due to the excellent filling profile and injection pressure.  Molding Automation: Automation is possible because there is no need for post-processing processes such as trimming, waste recycling, and removal of runners.  Design Flexibility: There is flexibility in injection mold design in the placement of the gate using the hot tip gate, valve gate, or edge gate. As a result, there is an increase in part aesthetics and optimum filling of mold cavities during the injection. Cold Runner System Advantages The cold runner system has the following advantages: Lower tooling cost: The cold runner mold system has a lower investment cost in injection mold tooling. As a result of the lower tooling cost, molding is cost-effective. Less inspection and maintenance cost: Cold runner molds are not complex. Consequently, there is less need for inspection and maintenance, leading to decreased maintenance costs and downtime. Thermosensitive plastics: Another difference between hot runner and cold runner molds is their application in molding thermosensitive plastics. Cold runner systems are the most suitable for thermally sensitive polymers. Furthermore, they are also suitable for any plastics. Hot Runner Mold vs Cold Runner Mold â Drawbacks of Each System Each runner mold also has its drawbacks. Here, we will talk about their disadvantages and how they compare to each other. Hot Runner System Disadvantages The hot runner system has the following disadvantages: High investment cost: Hot runner systems have a high initial investment and maintenance cost due to the sophistication of the molds and advantages such as reduced cycle time, part quality, and flexibility. High requirement for precision in the equipment: The system requires high-end equipment due to the need for precision. Otherwise, there might be defects because of failure in the machine. An example is the plastic seal failure which can lead to the molten plastic spilling and damaging the hot runner assembly. Cold Runner System Disadvantages Cold runner injection molding has the following disadvantages: Material wastage: Material waste is another difference in the hot runner vs cold runner molding comparison. The molten plastic solidifies in the cold runner system. Consequently, these lead to scraps that need trimming. Injection pressure drop: Heat transfers from the plastic to the mold plates during plastic flow, which causes shrinkage leading to pressure drop and further forming defects such as sink marks and underfilling parts. High cycle time: Cold injection molding has a slower cycle time due to reduced plastic flowability. Aside from that, removing the runner and sprue (especially in the two mold systems) also increases the cycle time.
Traditionally, the joint angle between the two faces is used to differentiate weld lines from joint lines. A joint angle of less than 135º produces a weld line, while a joint angle of more than 135º is defined as a joint line. In general, a weld line mark disappears when the joint angle reaches between 120º and 150º. The weld lines are considered more critical than joint lines in terms of both aesthetics and mechanical properties of the joint. Translated with www.DeepL.com/Translator (free version)
Weld lines and joint lines can be caused by holes or insertions in the part, the existence of multiple injection gates, or due to areas of varying wall thickness where hesitation or race-tracking occurs.
Some of the actions to be taken to improve the surface finish are related to actions to increase the flow rate and temperature of the molten polymer and the mould walls. Therefore, the improvement of the surface quality is achieved by measures such as:
Currently it only shows your basic business info. Start adding relevant business details such as description, images and products or services to gain your customers attention by using Boost 360 android app / iOS App / web portal.
The dimensional shrinkage of parts is inherent to the injection moulding process. Shrinkage occurs because the density of the polymer varies from processing temperature to ambient temperature (see, for example, the specific volume of a semi-crystalline polymer in Figure 5.46 – PVT curve). During the stages of the injection moulding process, cooling shrinkage produces a series of internal stresses in the part. These residual stresses act on the part with similar effects as possible externally applied stresses. If the residual stresses induced during moulding are high enough, the part after ejection from the mould may warp / twist or warp, resulting in defective parts.
The trapped air defect appears when a certain amount of air cannot escape out of the mould during injection, a small area without material appeared in the injected part. In a correct Injection mould design, at each injection, air is exhausted through mould vents, mould inserts or even ejectors, which also act as vents.
Sinkage marks are depressions in the surface of the plastic injection moulded part caused in the last phase or stage of the plastic injection moulding process, during the cooling process. The thicker sections of the plastic cool at a slower rate than the others, resulting in a higher percentage of shrinkage in that local area. After the material on the outside has cooled and solidified, the material on the inside begins to cool and its shrinkage pulls the surface inwards, causing a surface depression.
Trapped air will result in voids and bubbles within the moulded plastic part, incomplete filling or surface defects such as stains or burn marks.
If welding or joining lines cannot be avoided, a good practice is to ensure that they are generated in low visibility or mechanically non-critical areas. This is often done by modifying the plastic injection gate, modifying the flow fronts and the areas where the weld/joint lines occur. Another practice is to try to achieve a good joint between the two fluxes so that the mechanical weakness that occurs is not excessive. To do this, the aim is for the junction of the two flux fronts to take place at the highest possible temperature and pressure, so that they are not far from the inlet port. Translated with www.DeepL.com/Translator (free version)
The warping or twisting of an injection-moulded plastic part is therefore due to the existence of a series of residual internal stresses in the part which are in turn generated by the differential shrinkage of the material during cooling. If the shrinkage throughout the part is uniform, the resulting part does not warp or twist, it simply shrinks uniformly and becomes smaller. Thecrystalline polymers, e.g. acetal, nylon, high density polyethylene, polyethylene terephthalate and polypropylenecause the most serious problems with shrinkage from 1 to 4%. Amorphous polymers, e.g. polystyrene, acrylic and polycarbonate are more treatable, with shrinkages of only 0.3 to 0.7%.
However, achieving uniform shrinkage is complicated by the presence and interaction of many factors such as the orientations of the polymer molecules, temperature variations in the mould walls, compaction variations in the plastic parts (over-compacted areas and under-compacted areas, due to unbalanced flow paths), etc. Note that areas of higher compaction, such as injection gates, have a lower shrinkage since part of the compaction of the molten polymer compensates for it. In contrast, areas further away from the gate are subject to less compaction and therefore tend to have a higher shrinkage.
Hot Runner Temperature Controller also called HRTC in short form. Hot runner temperature controller is used to run mainly Plastic Injection Molding Machine's molds. Let's try to understand 2 main types of molds. Hot Runner vs Cold Runner Injection Mold: Key Differences You Need to Know   Home Blog Hot Runner vs Cold Runner Injection Mold: Key Differences You Need to Know Hot Runner vs Cold Runner Injection Mold: Key Differences You Need to Know Updated: October 17, 2022 An injection mold is a component designed according to the intended product using processes such as CNC machining and is where the molten plastic is injected and cooled. There are several injection molds types. However, based on the temperature held by the runner and the mold,  there are two mold systems: hot runner and cold runner. Each mold system uses a different mechanism which affects plastic fabrication differently. As a result, there is a need for a proper understanding of the hot runner mold vs cold runner mold comparison before selection. This article does the hot runner vs cold runner injection molding comparison by introducing both systems, how they work, and their differences. Furthermore, it shows how to choose the right mold for your project.   What is a Hot Runner Mold?  A hot runner mold is an injection mold with a manifold system (i.e., containing a heating component, manifold, and nozzle) that ensures that molten plastic injected into the mold maintains its temperature. Hot runner injection molding is suitable for molding plastics that require steady flow and injection pressure for part fabrication. Furthermore, with the method, there is a reduction in defects such as sink marks that occur due to fluctuating injection pressure and underfilled molds. Types of Hot Runner Mold Based on the method of maintaining the heat, here are the two types of hot runner molds used in plastic injection molding: Insulated Hot Runners Insulated hot runners molds have extremely thick runners in the mold plate, which causes part of the molten plastic to cool down and insulate the system. The insulation reduces heat loss, allowing the mold system to maintain an open plastic flow. Insulated hot runner molds are less expensive than heated ones because they do not use manifolds and drops. Furthermore, they have flexible gates, reduced defects, and favor easy color change. However, it has a few disadvantages, such as freeze-ups at the gate, non-uniform mold filling, long start-up periods, and the need for a fast cycle to maintain the thermoplastic molten state due to the absence of a manifold system.  Heated hot runners The heated hot runner is the major type of hot runner system with heating achievable using a heating component in one-half of the mold. However, they come in two designs: externally heated and internally heated. Externally heated hot runners: The heating component is outside the mold. As a result, there is no obstruction in the molten thermoplastic flow (better flow control) and no drop in injection pressure. Furthermore, the molten plastic does not freeze and is ideal for color change. Externally heated hot runner molds are suitable for thermosensitive materials. Internally heated hot runners: Here, the heating component is in the mold, leading to a drop in injection pressure, incompatibility with color change, and material hanging up and degrading in the mold. However, there is better flow due to the heated runner and gate tip control. What is a Cold Runner Mold?  A cold runner mold is the basic injection mold with runners at the same temperature as the mold cavity. The system involves injecting the molten plastic into locating ring. Afterward, the molten plastic passes through a sprue and runner, which are cold, before entering the mold cavity. As a result, when the plastic cools, it takes the shape of the mold cavity with the solidified plastic in the runner attached. The cold-runner mold features a large runner (larger than the part), removing the tendency of underfilling the mold. Aside from that, it is suitable for working with any plastic polymer irrespective of heat sensitivity, is less expensive than hot runners, and is easily maintained. However, they generate waste. Types Of Cold Runner Systems There are two types of cold runner molds system based on the number of mold plates: · Two Plate Cold Runner System The two-plate cold runner system comprises two plates with the stationary mold containing the sprue, runners, gate, and cavities. It is the fastest, simplest, and least costly cold runner system. However, the runner is attached to the final product and should be cut off. · Three Plate Cold Runner System A three-plate cold runner system is similar to the two-plate system. However, the three-plate injection mold is flexible with an additional runner plate. Furthermore, there is no need to cut the runner from the injection molded part, and the mold does not require an ejection system for part removal. 3 plate injection mold is friendlier and more flexible. They are the most suitable for working with products with complex designs, and they are a lower-cost alternative to hot runner systems. Disadvantages of this injection mold include long cycle time, complex tool design, and high material waste. Hot Runner Mold vs Cold Runner Mold â Advantages of Each System Each runner mold has its advantages making them suitable for different applications and industries. Here, we will talk about their advantages and how they compare. Hot Runner System Advantages The hot runner system is widely applicable in plastic product fabrication due to the following advantages: Reduced cycle time: One main difference between a hot runner and cold runner injection molding is the cycle time. Hot runner injection molds have a faster cycle time due to the plastic being kept at optimum temperature, increasing flowability. Reduced material wastage: Itâs more cost-effective as the mold system generates little to no material waste.    Optimal Part Quality: Parts made using hot runner molds have better final quality due to the excellent filling profile and injection pressure.  Molding Automation: Automation is possible because there is no need for post-processing processes such as trimming, waste recycling, and removal of runners.  Design Flexibility: There is flexibility in injection mold design in the placement of the gate using the hot tip gate, valve gate, or edge gate. As a result, there is an increase in part aesthetics and optimum filling of mold cavities during the injection. Cold Runner System Advantages The cold runner system has the following advantages: Lower tooling cost: The cold runner mold system has a lower investment cost in injection mold tooling. As a result of the lower tooling cost, molding is cost-effective. Less inspection and maintenance cost: Cold runner molds are not complex. Consequently, there is less need for inspection and maintenance, leading to decreased maintenance costs and downtime. Thermosensitive plastics: Another difference between hot runner and cold runner molds is their application in molding thermosensitive plastics. Cold runner systems are the most suitable for thermally sensitive polymers. Furthermore, they are also suitable for any plastics. Hot Runner Mold vs Cold Runner Mold â Drawbacks of Each System Each runner mold also has its drawbacks. Here, we will talk about their disadvantages and how they compare to each other. Hot Runner System Disadvantages The hot runner system has the following disadvantages: High investment cost: Hot runner systems have a high initial investment and maintenance cost due to the sophistication of the molds and advantages such as reduced cycle time, part quality, and flexibility. High requirement for precision in the equipment: The system requires high-end equipment due to the need for precision. Otherwise, there might be defects because of failure in the machine. An example is the plastic seal failure which can lead to the molten plastic spilling and damaging the hot runner assembly. Cold Runner System Disadvantages Cold runner injection molding has the following disadvantages: Material wastage: Material waste is another difference in the hot runner vs cold runner molding comparison. The molten plastic solidifies in the cold runner system. Consequently, these lead to scraps that need trimming. Injection pressure drop: Heat transfers from the plastic to the mold plates during plastic flow, which causes shrinkage leading to pressure drop and further forming defects such as sink marks and underfilling parts. High cycle time: Cold injection molding has a slower cycle time due to reduced plastic flowability. Aside from that, removing the runner and sprue (especially in the two mold systems) also increases the cycle time.
A weld line (also called a weld mark) is formed when two melt flow fronts travelling in opposite directions meet. In contrast, a bond line occurs if these two fronts flow parallel to each other creating a bond line.
The following recommendations can be used to reduce the impact of weld lines and parting lines on injection moulded parts.
The locations of the air leakage areas in the moulds are located in the areas that are filled at the end of the injection cycle or phase. A common cause of the trapped air defect is an insufficient size of the mould vents. Another common cause is when racetracking occurs (tendency of the polymer melt to flow preferentially in thicker sections leaving thinner areas with trapped air). Translated with www.DeepL.com/Translator (free version)
A poor finish can be caused by the formation of wrinkles or waves at the edges of the part or in the last filling areas during injection moulding.
Some of the practices we develop in the Moldblade Engineering Department to correct the problem of incomplete filling are:
A rule of thumb to avoid excessive distortions in the part due to temperature differences after injection, is that the average temperature differences in any part of the part after injection should not be greater than 15-20ºC.
GETTING A QUOTE WITH LK-MOULD IS FREE AND SIMPLE.
FIND MORE OF OUR SERVICES:
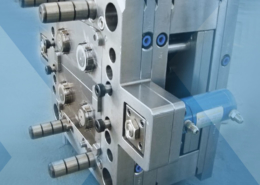
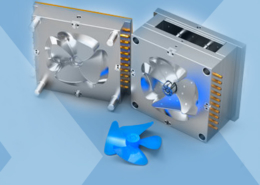
Plastic Molding

Rapid Prototyping
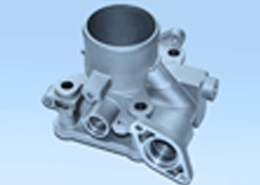
Pressure Die Casting
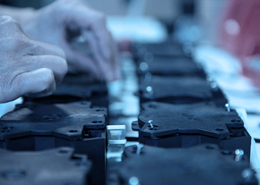
Parts Assembly
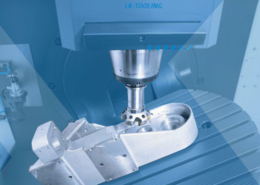