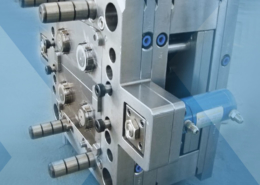
Large Part Injection Molding - Not for the Faint of Heart - large part injection
Author:gly Date: 2024-10-15
This material is typically used for automotive parts such as bearings and bushings. While they are resistant to wear and chemicals, they are not resistant to liquids.
We fully respect if you want to refuse cookies but to avoid asking you again and again kindly allow us to store a cookie for that. You are free to opt out any time or opt in for other cookies to get a better experience. If you refuse cookies we will remove all set cookies in our domain.
Utilizing materials such as epoxy resin and polyester, thermoset injection molding highlights precise dimensions, repeatability, and resistance to high temperatures.
Dimensional Precision: Ensures automotive parts meet stringent size tolerances consistently. High-Temperature Resilience: Resists melting or deformation at high temperatures, a key consideration for automotive manufacturers. Repeatability: Guarantees the production of identical components with every manufacturing cycle.
Injection molding stands as a cornerstone in modern manufacturing, especially in the automotive sector. Its overarching advantages redefine how complex-shaped parts with strict tolerances and exceptional surface finish are produced.
This type of plastic is weather resistant and ideal for injection molding and 3D printing applications. They are commonly used for covers and instrument panels.
Weighing in at 1.8 million pounds, the press was too big for Milacron’s Cincinnati-area facilities, so it was built on site at a brand-new 20/20 plant specially constructed to accommodate it, Milacron technical adviser Ron Hertzer said.
WIT MOLD serves automotive and parts customers worldwide and over 10 years of experience allows the WIT MOLD team to provide customers with fast development times and consistent quality to ensure that new projects run well.
Accuracy and Reproducibility: High precision and reproducibility are paramount in automotive manufacturing, a core reason for the industry’s preference for injection molding. Complex Shape Design: Injection molding enables the production of intricate components with a process called “screw-injection,” facilitating the creation of detailed and complex parts. Rapid and Efficient Manufacturing: The swift production process ensures that automotive manufacturers can meet their part demands efficiently. High Surface Finish Quality: Components produced through injection molding boast excellent surface finish quality, offering smooth and flawless surfaces. Color Variety: Injection molding allows for the production of parts in various textures and colors, eliminating the need for post-molding coloring processes. In summary, injection molding in the automotive industry embodies precision, versatility, and efficiency, revolutionizing the way complex automotive components are designed and manufactured.
Thermoplastic injection molding, using materials like polypropylene, nylon, and ABS, is the go-to method in the automotive industry.
Designed for producing parts from elastic materials like rubber and silicone, elastic injection molding shares similarities with thermoplastic molding but introduces exceptional shock absorption and vibration reduction.
This flexible, spongy material is primarily used for automotive seats, but because of its flexibility, it can also be used for suspension bushings, insulation panels and gaskets.
Ensuring IMMs like the 8,000-tonner will work upon delivery without the luxury of actually seeing it in action at Milacron is nerve-wracking, Hertzer said.
In the automotive industry, automotive injection molding plays a critical role in producing high-quality components. Automotive plastic injection molding is widely used to create durable and precise parts, making injection molding automotive a key process in manufacturing. Companies specializing in automotive plastic molding provide essential services for car manufacturers, with many automotive injection molding companies offering specialized solutions. The production of plastic injection molding automotive parts ensures that vehicles are built with reliable and cost-effective components. Whether it’s injection molding automotive parts or working with automotive plastic injection molding companies, the focus is on delivering excellence. Injection moulding automotive parts and injection molded plastic auto parts are essential for creating everything from small fittings to large body components. The expertise in automotive mold design and production is what drives innovation and quality in the automotive sector.
Cost-Effectiveness: Offers a cost-efficient solution for producing automotive components. Speedy Production: Boasts fast production rates, meeting the demands of the automotive sector. Multifunctionality: Versatile in applications, addressing a range of automotive part requirements.
Injection molding excels in crafting intricate components with stringent tolerances, setting a new standard for precision and complexity in the automotive industry.
“The sheer size of this machine is hard to put into words, but its unique design and processing stats speak volumes,” he said. “The C8000 is a large-part powerhouse designed by some of the best plastics processing engineers in the world that delivers the highest performance, functionality and flexibility possible in the large-tonnage space.”
These cookies are strictly necessary to provide you with services available through our website and to use some of its features.
When making durable automotive parts, manufacturers can use reinforced composites that are stronger than ordinary resins. These are commonly used for bumpers and body work.
The widespread use of injection molding in the automotive industry stems from its superiority over traditional manufacturing techniques.
“Our plastics manufacturing at 20/20 requires a great deal of redundancy ... ease of transition and reliability, and Milacron has met these expectations repeatedly, which is why we continue to turn to them when we’re ready for the next big thing,” said Ernsberger, who described Milacron presses as “workhorses.”
With our precise molding methods, you can rest assured that all of your plastic automotive parts are of the best possible quality.WIT MOLD makes it a priority to ensure that all dimensions of your plastic automotive parts are as accurate as possible.
By using injection molding for your plastic auto parts, you can rest assured that you are saving money. Countless parts can be made with just one injection mold. This means you will save on materials and production costs.
Click on the different category headings to find out more. You can also change some of your preferences. Note that blocking some types of cookies may impact your experience on our websites and the services we are able to offer.
Senior Staff Reporter Karen Hanna covers injection molding, molds and tooling, processors, workforce and other topics, and writes features including In Other Words and Problem Solved for Plastics Machinery & Manufacturing, Plastics Recycling and The Journal of Blow Molding. She has more than 15 years of experience in daily and magazine journalism.
The OEM’s technologies are reliable, and employees’ familiarity with them eases their transition to newer machines, 20/20 company owner and President Ron Ernsberger said. He praised the machine controls’ ease of use.
Because these cookies are strictly necessary to deliver the website, refusing them will have impact how our site functions. You always can block or delete cookies by changing your browser settings and force blocking all cookies on this website. But this will always prompt you to accept/refuse cookies when revisiting our site.
The multifaceted nature of injection molding makes it a versatile solution for various automotive parts. Its scalable process allows for the mass production of thousands of identical components.
One of the main advantages of our injection molding technology is the very short lead times. Simply provide us with the exact specifications and dimensions of your plastic automotive parts, and we can produce your product in record time.
This material is a perfect replacement for glass because it is both transparent and very resistant to breakage. They are perfect for interior screen and headlight cover applications.
“They’re just exciting ... to walk up to something that’s as big as your yard,” he said. “They actually built a new factory for these machines. The clamp is too big or too heavy for our facility on our floor, so the clamp gets built on site for the very first time. ... There’s tremendous logistics problems getting it from the foundry that makes it to here. I think the castings on that, the particular foundry that made it had like seven furnaces … melting the material once to get the pour for the one stationary platen.”
WIT MOLD engineers will analyze the fill to get the best gate position for optimal flow and design the best cooling channels to ensure minimal package distortionWe have a very good We have a very good injection operator to help set the best injection parameters to avoid any wasted development time and improve the reliability of molding parameters.
PVC is one of the most widely used materials in the automotive industry. Because of its chemical resistance, it is used for components such as instrument panels and cable insulation.
Due to its water resistance, this material is perfect for exterior components. It is particularly effective as a material for bumpers, cable insulation and battery covers.
These cookies collect information that is used either in aggregate form to help us understand how our website is being used or how effective our marketing campaigns are, or to help us customize our website and application for you in order to enhance your experience.
We may request cookies to be set on your device. We use cookies to let us know when you visit our websites, how you interact with us, to enrich your user experience, and to customize your relationship with our website.
We provide you with a list of stored cookies on your computer in our domain so you can check what we stored. Due to security reasons we are not able to show or modify cookies from other domains. You can check these in your browser security settings.
We pride ourselves on our ability to produce over 200 sets of molds in a year and supply them worldwide. This has earned us the reputation of being able to fulfill any order, no matter how big it is. No matter how big the order is, we are fully capable of fulfilling it.
Shock Absorption: Elevates the durability of automotive components through effective shock absorption. Vibration Reduction: Ensures a smoother ride and prolonged lifespan with superior vibration reduction. Cost-Effective Durability: Combines longevity with cost-effectiveness, a crucial aspect for automotive manufacturing.
We also use different external services like Google Webfonts, Google Maps, and external Video providers. Since these providers may collect personal data like your IP address we allow you to block them here. Please be aware that this might heavily reduce the functionality and appearance of our site. Changes will take effect once you reload the page.
WIT MOLD has always maintained high standards of control. We follow the strictest quality controls and any plastic automotive parts we distribute are tested by our dedicated team of experts. Rest assured that any product you receive from WIT MOLD will be of the best quality.
A press that weighs about as much as six blue whales has recently settled into a new injection molding facility across the state from Milacron LLC, which manufactured it. The 8,000-ton injection molding machine (IMM) — called the C8000 — enters Milacron’s product pool as its largest, capable of producing shots with about as much heft as legendary L.A. Lakers basketball big man Shaquille O’Neal.Mike Gepfert, COO at 20/20 Custom Molded Plastics LLC, Holiday City, Ohio, which took delivery of the C8000 several months ago, said the four-tie-bar IMM is a fitting complement to a 6,750-ton Milacron press that formerly held title as the molding shop’s largest.
One of the key advantages that our injection molding technology can bring to you is the rapid production of prototypes. By using 3D printers and CNC machines, we can produce your prototype automotive plastic parts in the shortest possible time.
Bumper, dashboard parts, air intake grille, wing, radiator grille, trim, engine parts, water tank parts, air conditioning parts, air filter parts, various water bottles, seat parts, floor parts, roof parts, bar parts, steering wheel parts, door trim, rear view mirror and various fasteners, front and rear lights, etc.
If you are interested in using some of our injection mold services, we are very capable of providing you with an instant quote. This helps streamline the process and increases the efficiency of all our transactions.
“The capacity these large-tonnage machines provide thrusts us into a unique position within the marketplace that’s unsurpassed,” he said.
“As a custom molder, we always want a plan for what doesn’t quite yet exist,” he said in a press release. “In order to be competitive, we can’t be constrained. Milacron understands this about us and has always been willing to take it to the next level. The capacity of these two large-tonnage machines thrusts us into a unique niche of custom molders.”
With the market continuing to grow for big parts such as large plastic pallets, underground enclosures for telecommunications and utilities, and drainage and irrigation products, the company enters 2024 planning to add yet two more massive IMMs.
GETTING A QUOTE WITH LK-MOULD IS FREE AND SIMPLE.
FIND MORE OF OUR SERVICES:
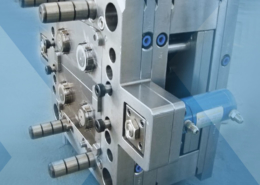
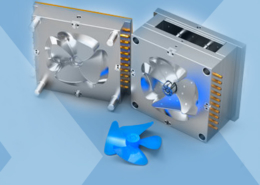
Plastic Molding

Rapid Prototyping
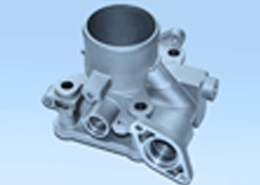
Pressure Die Casting
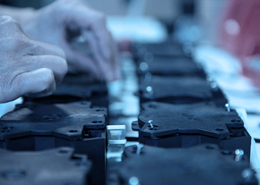
Parts Assembly
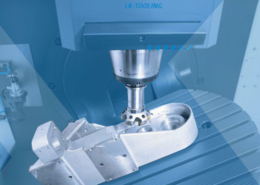