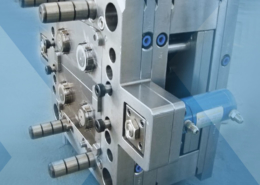
KyronMAX® | Mitsubishi Chemical Advanced Materials - strongest injection molded
Author:gly Date: 2024-10-15
Commonly known as acrylic plastic, PMMA is not highly chemically resistant nor especially resistant to cracking. However, its brittleness is not a factor in its most common applications. Transparent and glass-like, acrylic appears in many applications, including in sports equipment, commercial food displays and lighted signs.
Crystalline plastics get their name from the highly-ordered crystal structure that their polymers form. This dense structure gives crystalline plastics several key properties. They melt only at high temperatures, and typically, crystalline plastics have better chemical resistance properties and superior strength and stiffness, making them some of the most common plastics used in injection molding. Some of the most common crystalline plastics include:
Let our team provide key insights to help you make critical decisions about materials, mold forms and more. Request a free quote on your project when you contact Reliant Plastics today.
First established in 1968 at Thane, Maharashtra, a small company located in an industrial estate has now expanded to 3 different locations across India and has created a global presence for itself. Our state of the art manufacturing unit is capable to produce any plastic component through the injection moulding process. We are the first choice for most multinational companies when it comes to moulding plastics for industries like Electrical, Automotive, Textile, Medical Lab Equipment, and Kitchenware. The trust our customers show in us constantly motivates us to innovate, come up with solutions and deliver outstanding quality and service.
More commonly known as “polystyrene” or “PS,” HIPS contains materials beyond polystyrene. These materials, such as rubber, improve the impact resistance of a material that is otherwise very brittle. With its rigidity, some molding use cases for this substance include protective cases, such as those in use in hospital laboratories, medical devices or hardware tool chests.
Typically a part of applications such as tool housings, TV remote controls and other small, handheld tools or consumer products, ABS exhibits high strength and toughness without a correspondingly high material cost. ABS provides durability in products without adding a substantial amount of weight. The molding temperature of ABS influences its final characteristics.
Aurangabad - GUT No 30, Plot No 01, Ranjangaon (SP), Near MIDC Waluj Near K-74, Opp R K Press Turn Eng, Aurangabad, Maharashtra 431136, India.
Polypropylene is a common plastic in use in many industries, especially within commercial food applications due to its food-safe nature and for toys because of its affordability. PP does not perform as well in cold applications, but it does provide excellent hot water resistance for easy washing and sanitizing because of its high melting point. PP is not a very dense material.
LDPE provides many of the benefits of PE/HDPE, but it is less stiff and more ductile. These traits make it well-suited to flexible plastic applications: consumers most commonly encounter LDPE in plastic bags or consumer-grade plastic water bottles. Like PE, it is easy to mold and cost-effective for appropriate projects.
TPR is a unique material that blends plastic polymers with rubbers, creating a material with the physical properties of both. TPR products exhibit a high degree of plasticity and can withstand long-term weathering. Also strong against chemicals, TPR is most common in hospital devices and tools.
One of the most durable plastic materials, polycarbonate can withstand significant deformation without breaking or even developing stress fractures. That trait made PC an obvious choice for the developers of the optical disc when CDs were first invented, but other uses include phone screens and eyeglass lenses.
Aurangabad - GUT No 30, Plot No 01, Ranjangaon (SP), Near MIDC Waluj Near K-74, Opp R K Press Turn Eng, Aurangabad, Maharashtra 431136, India.
Plastic injection molding is a process that many industries embrace and use widely thanks to its versatility. However, its popularity isn’t solely due to the quick production that’s possible with molding but also to the variability of the available materials. When manufacturers need to create products or parts with specific material properties, there are many injection molding materials to consider.
With nearly a dozen different injection molding plastic types across three classes, there is an immense amount of variety to consider. Choosing the right injection molding materials is essential for product quality, budget planning and your long-term success. At Reliant Plastics, we leverage years of experience and an in-depth understanding of injection molding to assist your business.
POM is a material best suited for producing heavy-duty industrial plastic parts. It scores high marks in all categories, such as heat and chemical resistance, but it is also more difficult to work with at the molding stage. POM is in electrical devices, pumps and fan blades.
Also known as nylon plastic, polyamides exhibit high resistance to electricity and are heavily wear-resistant. Nylon parts are very suitable for high-stress environments, and in some cases, they can surpass comparable metal parts in performance.
A “semi-crystalline” plastic is a material in which a crystal structure is present, but it is not as rigid or as ordered as a true crystalline material. These solutions have many of the same properties as crystalline plastics but on a lesser level. A few typical semi-crystalline materials are:
Sometimes referred to as high-density polyethylene, HDPE is highly resistant to both chemical exposure and temperature extremes. HDPE melts and molds very easily with excellent fidelity. HDPE is also well-known for how easy it is to recycle it. Many products made using injection molding use plastics such as HDPE.
What are the types of plastic used in injection molding? Understanding these options is a critical first step towards successful production planning. Learn about 11 of the most popular molding materials that comes from the three key types of plastic — crystalline, semi-crystalline and amorphous thermoplastics — and why manufacturers choose them.
Most common in industrial applications, TPU is a niche material that is best suited to molding heavy-duty products that will need to withstand a punishing environment. Despite its toughness, TPU molds easily and mold design is comparatively simple. TPU is also notable for its saltwater resistance.
Amorphous plastics have no order to the arrangement of their molecules. The random nature of the molecular structure means that these plastics soften gradually as the temperature rises rather than melting immediately. These types of plastics for injection molding produce results that are waterproof and highly receptive to bonding, and they are simple to form. Common examples include:
GETTING A QUOTE WITH LK-MOULD IS FREE AND SIMPLE.
FIND MORE OF OUR SERVICES:
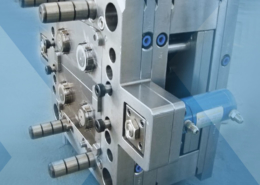
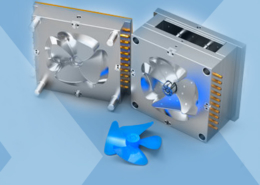
Plastic Molding

Rapid Prototyping
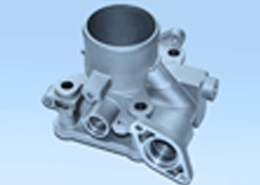
Pressure Die Casting
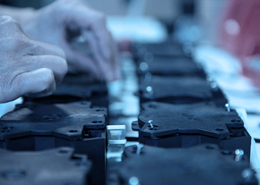
Parts Assembly
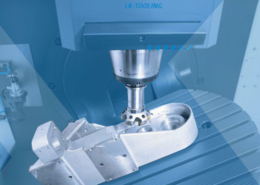