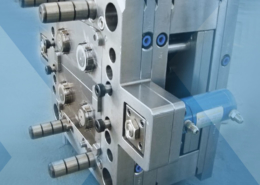
Key Strategies in Precision Injection Molding for Superior ... - precision injec
Author:gly Date: 2024-10-15
The top edge of the window is formed by the B-side mold half; the bottom edge is formed by the A-side mold half. The two mold faces must be drafted by at least 3 degrees where they shut off (sliding shutoff). To allow this, the part wall itself must be drafted by more than 3 degrees. The additional amount by which the wall must be drafted depends on the part geometry.
Custom manufacturer of plastic injection molded products including plastic & polyurethane mouldings. Materials used also include nylon, ABS & foaming agents. Products can be customized for colors, sizes, weights & applications. Services include insert molding, parts assembling, parts decorating, ultrasonic welding, secondary machining, custom packaging, prototype development, order fulfillment & warehousing. Markets served include point-of-purchase, packaging, industrial, dental & housewares.
Upmold is capable of making various molds including over mold, double injection molds, 2K plastic injection mold, gas assisted mold, hot runner mold, multi-cavity mold, insert mold, unscrewing mold, MUD rapid prototype injection mold, die casting die, fixture etc, it greatly enhances our specialty in plastic injection mold making.
Houses in Monopoly land have no doors or windows. Maybe the tiny people who live there spend a lot of time indoors, or perhaps they’ve perfected teleportation. More likely, it’s because doorless windowless plastic houses are easy to make in simple two-part molds.
1. When looking down on your shutoff, can you clearly see edge 1 and edge 2? If 2 is hidden under 1, you cannot use this shutoff design.
Our digital factories create prototypes and low-volume parts fast, while our manufacturing network, offers advanced capabilities and volume pricing.
UPMOLD is a full-service injection molding molds builder specializes in the tooling design, engineering support, molds building and qualifying of plastic injection molds, UPMOLD operates with plastic injection presses ranging from 45T to 600T operating 24/6. Our company utilizes the latest technology and equipment to provide our customers world-class product and services. we provide a wide range of product solutions for the plastic injection mold, die casting, machined components and other types of part manufacturing.
The window in Figure 7 is formed by the sliding shutoff shown in Figure 8. In this case, the shutoff between the two mold halves angles across the window.
While side-actions are a relatively simple solution, there are a couple of things to keep in mind when using them. First, they must open perpendicular to the direction of mold opening. This would be simple if part walls didn’t have to be drafted and were always positioned vertically. Since walls are not always conveniently oriented, however, care must be taken to ensure that side-actions operate (and are, themselves, drafted) perpendicular to the direction of mold opening and not necessarily perpendicular to the surfaces on which they live.
Upmold is a manufacturer that specializes in the Plastic injection mold, Die casting die, Trim die, Fixture, components machining, and injection moulding parts, We service to the customers from North America, Europe, Australia and Japan with the markets of Automotive, Household Appliance, Consumer Goods, Electronic, Medical and Telecommunication.
Sliding shutoffs can be used to produce a variety of other useful features. One is a clip like the one in Figure 5. By its very nature, the hook at the end of a clip is specifically designed to catch, so the area under it would normally be an undercut. Creating a hole in the “floor” under the hook achieves the same end result as removing the sill under the door in the previous example. In this design, it allows a rectangular-shaped pad of one mold half to extend up through the floor to create the bottom of the hook and the recessed face of the clip. The rectangular-shaped pad shuts off against the walls of the other mold half, which produces the rest of the clip.
We’ve shown how removing a sill can eliminate the need for side-actions, but there are also instances in which a fully surrounded through-hole— a window for example— can be produced by sliding shutoffs. This is achieved by adding an increased amount of draft to a wall to allow the window to be formed partially by each of the two mold halves.
By removing alternating sections of the hole’s wall, you can allow each mold half to form, alternately, inside and outside surfaces of the channel. The two mold halves meet at multiple points along the length of the through-hole and must be drafted at each of these points. This technique is demonstrated in our Design Cube, available for free at get.protolabs.com/design-cube.
SO 9001:2015 certified manufacturer of plastic injection molded parts and fabricator of custom injection molds. Services include precision plastic injection molding, part design, mold design, mold construction, engineering, contract manufacturing, automated & manual assembly, cellular manufacturing, rapid prototyping, R&D, mold maintenance, mold repair, joining, decorating, packaging, and chemical bonding. Materials include difficult-to-process engineering resins, rubber replacement and metal replacement plastics, ABS, Acrylic, TPE, TPU, PC, PE, PP, Nylon (PA), PS, PPS, PI, PEI, PPS, PES, Ultem, Radel, PEEK, Ryton, Lexan, Valox and other engineering plastics with additives. Industries serviced include medical, dental, life safety, lighting, military, automotive, aerospace, and consumer products.
Another useful feature that can be formed using shutoffs is a through-hole that is perpendicular to the direction of mold opening. (See Figure 6.)
While cams are typically used to produce small features, they can also be used to produce large portions of a part. In Figure 3, we see a part's top and bottom that were formed by A- and B-side mold halves and its entire circumference is formed entirely by two cams.
In some cases, you can eliminate the cost and complexity of side-actions by using simple two-part molds with strategically placed sliding shutoffs. This is an area in which faces of the A- and B-side mold halves move parallel to one another as the mold opens. If we remove the bottom sill from the door of the house, as shown in Figure 4, we can produce the features solely by the interaction of the A- and B-side mold halves.
Proto Labs, Inc. 5540 Pioneer Creek Dr. Maple Plain, MN 55359 United States P: 877-479-3680 F: 763-479-2679 E: [email protected]
Our helpful design aid demonstrates part features that are too thin or too thick, bad bosses, right and wrong ribs, and other considerations to be mindful of while designing parts for injection molding.
The most obvious approach to undercuts is side-actions—mold pieces that act from the outside of the part, moving perpendicular to the direction of mold opening. These produce side-facing features in a closed mold and then automatically withdraw, allowing the A-side mold half to withdraw, as the mold opens, and the part to be ejected from the B-side. In Figure 1, a side-action cam produces the door, sealing against the B-side core as the mold fills and then withdrawing to allow ejection. A similar technique could produce non-through indentations that would otherwise act as undercuts.
In Protolabs’ injection molding process, cams cannot form undercuts on non-exterior surfaces. In many cases, however, undercuts on interior surfaces can be formed using pickouts. These are inserts that are part of the mold when resin is injected, but are ejected with the part and then removed from the part, leaving undercut features in their place. By filling the undercut and becoming, temporarily, an element of the part, a pickout eliminates ejection problems.
Plastic injection mould maker Upmold is an integrated Injection molding molds manufacturer with design, production and sales. Our main products are Plastic Injection mold, Die casting mold & tooling design services, injection molds, plastic injection molding, plastic parts. Professional, quality, Prompt and Management is our pursuit of philosophy. Good credit and quality first are our commitment to all customers; we are not only a cooperator but also your reliable and long-term partner.
ISO 9001:2015 certified full service custom manufacturer of high volume and high pressure die castings. Alloys used include aluminum and zinc. Capabilities include CNC lathe work, EDM machining, horizontal CNC machining, pallet CNC machining, vertical CNC machining, wire cut machining, low/medium volume production and prototyping. Additional services include assembly, e-coat, engineering, inspection and machining. Finishing services include burnishing, painting, plating, washing, trimming, sand blasting, polishing, powder coating and anodizing. Markets served include aerospace, agriculture, architecture, auto/truck/transportation, chemical, electronic, machine tool, marine, medical, military and oil and gas. Meet ANSI and ASME standards. RoHS compliant.
Tough Black (Loctite Henkel 3843) and Ceramic-Filled (BASF 3280) are two new advanced photopolymer materials now available for 3D printing.
In the real world—including the world of plastic parts—life is more complicated. Houses have doors, and parts have indentations, through-holes, and other features that don’t point straight up or down and could act as undercuts in a two-part mold. Designers using rapid injection molding can address these challenges in a variety of ways, including side-action cams, sliding shutoffs, pickouts, and bumpoffs.
Unlike a door formed by a side-action, which is drafted toward the outside of the house, a door formed by the B-side mold half is drafted toward the bottom of the house to facilitate part ejection. Similarly, the sliding shutoff itself — the area of the B-side mold half where the pad that forms the door meets the inside of the A-side mold half—must be drafted to a minimum of 3°. This is important for two reasons. The first is to allow a tight seal when the mold is clamped shut for injection. The second is to prevent wear of the mold surfaces as the mold opens. Shutoff wear can lead to leakage of resin between the mold faces resulting in flash which is unsightly and may interfere with part function.
Get machined parts anodized and chromate plated with our quick-turn finishing option. Eligible materials include aluminum 6061/6082 and 7075.
When the mold is closed, a door-shaped pad extending from the B-side mold half seals against the wall of the A-side mold half. Because there is no sill under the door, the pad is not trapped and can exit through the bottom of the door as the mold opens.
Imagine the window in Figure 1 as a skylight in the roof rather than a dormer window. (See Figure 2). A window perpendicular to the angled roof would be partially trapped as the cam opens sideways. Fortunately, most CAD programs allow you to define the face or plane to which a feature should be oriented and drafted. In this case, in creating the skylight you would simply orient perpendicular to the plane of the parting line rather than that of the roof.
GETTING A QUOTE WITH LK-MOULD IS FREE AND SIMPLE.
FIND MORE OF OUR SERVICES:
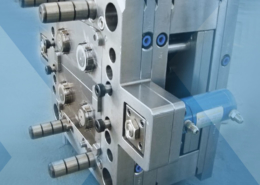
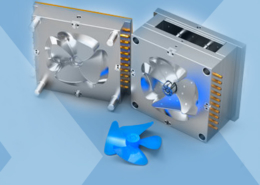
Plastic Molding

Rapid Prototyping
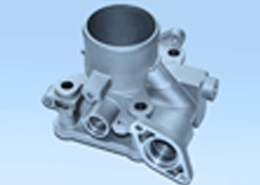
Pressure Die Casting
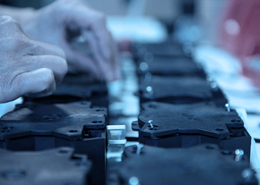
Parts Assembly
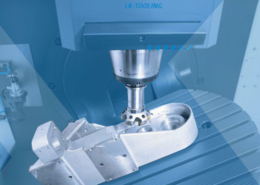