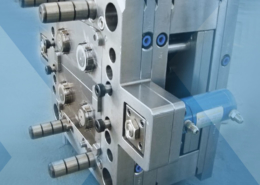
Key Factors in Plastic Injection - plasticizing injection molding
Author:gly Date: 2024-10-15
DongGuan Company Room 103,#41 Lian Ma Road,Dalingshan Town,Dongguan City,Guangdong Province,China ShenZhen Company Building 5,Juhui Mold Industrial Park,Tianliao Com,Yutang St,Guangming District,ShenZhen City, China
There are several aluminum mold manufacturers in the market, each with its own unique products and services. Some of the top manufacturers include Alcoa, Uddeholm, and Norsk Hydro. These manufacturers produce a wide range of aluminum molds for different applications and industries.
Aluminum molds can improve the plastic injection process in several ways. Firstly, they reduce the cycle time of the injection molding process, which means that more parts can be produced in a shorter period. This results in higher productivity and faster turnaround times for orders. Secondly, aluminum molds produce parts with consistent dimensions and high quality, which reduces the need for rework and improves customer satisfaction.
Aluminum molds are made from a high-strength aluminum alloy that has been heat-treated to provide excellent hardness and durability. They are designed to withstand high temperatures and pressure, making them ideal for plastic injection molding. The process of creating an aluminum mold is precise and requires skilled labor, which ensures that the molds produced are of high quality and accuracy.
Aluminum molds have several advantages over other materials used in plastic injection molding. For instance, they have a higher thermal conductivity, which means that they cool faster than other materials. Additionally, aluminum molds are lightweight and easy to handle, which reduces the risk of injuries during the manufacturing process.
To ensure the longevity of aluminum molds, they require proper maintenance and care. This includes regular cleaning, inspection, and lubrication. The molds should be cleaned after every use to remove any debris or residue that may have accumulated during the injection molding process.
Furthermore, aluminum molds produce parts with consistent dimensions and high quality, which reduces the need for rework and improves customer satisfaction. They also require less maintenance and care compared to other materials, which saves time and money in the long run.
Another advantage of aluminum molds is their ability to produce parts with high accuracy and precision. This is because they have a low thermal expansion coefficient, which means that they do not expand or contract much when exposed to different temperatures. As a result, the parts produced using aluminum molds have consistent dimensions and are of high quality.
Furthermore, aluminum molds are lightweight and easy to handle, which reduces the cost of transportation and storage. They also have a high wear resistance, which means that they can withstand constant use without getting damaged easily. This reduces the need for frequent replacements, which saves money in the long run.
Using aluminum molds for plastic injection provides several benefits that make them a better option compared to other materials. One of the main benefits is their reduced cycle time, which means that more parts can be produced in a shorter period. This, in turn, translates to higher productivity and faster turnaround times for orders.
DongGuan Company Room 103,#41 Lian Ma Road,Dalingshan Town,Dongguan City,Guangdong Province,China ShenZhen Company Building 5,Juhui Mold Industrial Park,Tianliao Com,Yutang St,Guangming District,ShenZhen City, China
Co-molding is also called to overmolding. It refers two plastic materials to bond, which usually are a hard material like ABS and a soft material like TPE. However, it could be two same hard materials to bond together depending on the melting temperature.
Thirdly, aluminum molds are lightweight and easy to handle, which reduces the risk of injuries during the manufacturing process. This, in turn, reduces the cost of insurance and liability claims. Lastly, aluminum molds require less maintenance and care compared to other materials, which saves time and money in the long run.
As a professional in the plastic injection industry, I have seen the evolution of different materials used for molds. However, one material that has been gaining momentum in recent years is aluminum. Aluminum molds for plastic injection provide a wide range of benefits and advantages that make them a better option compared to other materials. In this article, I will highlight why aluminum molds are the future of plastic injection, their advantages, benefits, types, applications, cost-effectiveness, maintenance, and care, and a comparison with other materials used in plastic injection.
One of the main advantages of using aluminum molds is their ability to dissipate heat quickly. This means that they cool faster than other materials, which reduces the cycle time of the injection molding process. Additionally, aluminum molds are lightweight, making them easy to handle and transport. They also have a high wear resistance, which means that they can withstand constant use without getting damaged easily.
Aluminum molds are used in a wide range of applications, including the automotive, aerospace, medical, and consumer goods industries. They are ideal for producing parts with complex geometries, thin walls, and high accuracy and precision.
Aluminum molds are cost-effective compared to other materials used in plastic injection molding. This is because they have a longer lifespan, require less maintenance, and reduce the cycle time of the injection molding process. Additionally, aluminum molds can produce more parts in a shorter period, which increases productivity and reduces the cost per part.
Additionally, the molds should be inspected regularly to check for any signs of wear or damage. Any issues should be addressed immediately to prevent further damage to the molds. Lastly, the molds should be lubricated regularly to reduce friction and prevent wear and tear.
There are two main types of aluminum molds: cold runner and hot runner. Cold runner molds are used for low-volume production runs and are cheaper to produce compared to hot runner molds. Hot runner molds, on the other hand, are used for high-volume production runs and are more expensive to produce.
ACE injection Moulding Company is an ISO 9001: 2015 certified mould manufacturer, providing services to the global plastic injection moulding industry.
In conclusion, aluminum molds are the future of plastic injection molding. They provide several advantages and benefits that make them a better option compared to other materials. They reduce the cycle time of the injection molding process, produce parts with consistent dimensions and high quality, and require less maintenance and care compared to other materials. Additionally, aluminum molds are cost-effective and have a longer lifespan than other materials, which saves time and money in the long run. Therefore, if you are looking for a material for your plastic injection molding needs, aluminum molds are the way to go!
Another benefit of using aluminum molds is their longer lifespan. They can withstand constant use and high temperatures without getting damaged easily, which reduces the need for frequent replacements. Additionally, aluminum molds require less maintenance compared to other materials, which saves time and money in the long run.
GETTING A QUOTE WITH LK-MOULD IS FREE AND SIMPLE.
FIND MORE OF OUR SERVICES:
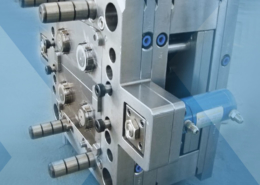
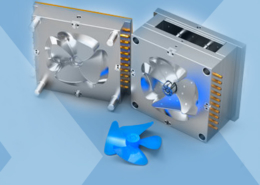
Plastic Molding

Rapid Prototyping
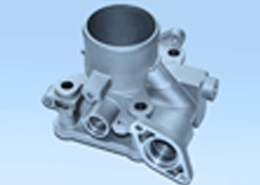
Pressure Die Casting
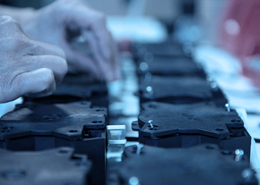
Parts Assembly
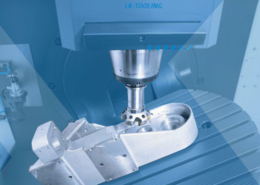