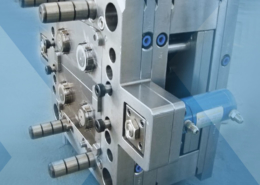
KCS Australia: Plastic Injection Moulding - injection moulding products manufact
Author:gly Date: 2024-10-15
Production molds are designed to reduce the cost of the plastic part as much as possible. While the cost of the plastic is a small part of the overall cost of the molded part, the primary driver of cost is the cycle time of the mold. Cycle time includes the time it takes to close the mold, inject the plastic, cool the part in the mold, and open the mold and eject the part. Production molds can produce a number of parts at the same time with short cycle times; molds are typically built with 2, 4, 8, 16, 32, etc. cavities to reduce part costs, and heating and cooling are added to the mold to speed up the phases of molding. If, for example, the cycle time to create a part is one minute, and the cost to run the mold is $2 per minute, a molded part from a single cavity mold would cost $2, and parts from a 4 cavity mold would cost $0.50.
Also known as polyethylene high-density (PEHD), HDPE is a polyethylene thermoplastic made from petroleum. Its high strength-to-density composition and versatility make HDPE a very popular type of plastic, serving a wide array of industries. From food storage containers to piping systems, HDPE does it all.
A production tool is designed for high-volume manufacturing and is constructed from hardened tool steel. A production tool may have automated slides for side action and multiple cavities. A prototype tool is fabricated in aluminum or brass for short-run manufacturing or concept validation, has hand-loaded core pins, and typically single cavity.
Protoshop Inc. uses steel mold base frames with detail cut into softer metal inserts. This translates to tooling that can produce up to 100K parts, yet is easily modifiable should the part geometry require changes, even non-metal safe changes. Iterations typically occur within a day.
High-Density Polyethylene can be molded into a variety of different shapes and sizes. With its linear structure and optimal strength, HDPE can withstand environmental stresses such as high-temperature treatment and physical impact.
HDPE is a plastic in high demand nowadays. Retlaw Industries has the resources and expertise to deliver exceptional HDPE molds, parts, and components nationwide. Nationwide shipping is always available including to Wisconsin, Washington, Pennsylvania, Ohio, New York, Minnesota, Michigan, Indiana, Illinois, and Colorado.
If you disable this cookie, we will not be able to save your preferences. This means that every time you visit this website you will need to enable or disable cookies again.
Production molds are sophisticated and complicated. In production tooling, features in the plastic part that can’t be formed with the primary core and cavity halves of the mold require side action mechanisms such as slides and lifters. These mechanisms add additional complexity when multiplied across numerous mold cavities.
HDPE is a versatile plastic with notable strength, flexibility, and resistance to chemicals and abrasion, making it an ideal choice for a wide range of applications. HDPE is used by people every single day, and you might not even realize it. Its ideal properties, specifically for packaging and assembly, make it one of the most widely used plastics in the world. It is also extremely versatile and can be used for manufacturing plastic milk jugs, auto parts, pipes, and much more.
Choose Retlaw Industries for custom HDPE parts manufacturing and benefit from our transparent pricing, extensive shop capabilities, and commitment to customer satisfaction. With over 40 years of experience and a long track record of success, trust Retlaw Industries for the manufacturing of high-quality HDPE parts and components your business needs to succeed.
HDPE is a thermoplastic polymer made from petroleum commonly used for plastic injection molding, HDPE was first created in the 1930s in the UK and used in radar cables during WWII. After it was commercially introduced in the U.S., its popularity took off and continues to be used today for a wide variety of industrial and commercial applications.
Prototype parts are created for validation and testing during early design stages. Production parts, on the other hand, are final components produced in bulk following approved designs.
Most prototype molds don’t employ heating and cooling, so the cycle times are longer, and it requires personnel who really know what they’re doing to get the part to fill properly.
Injection molding is a process for efficiently creating large volumes of identical plastic parts. The principle of injection molding is very simple. Plastic material is heated until it becomes a viscous melt and is forced into a closed mold that defines the shape of the article to be produced. There, the material is cooled until it reverts to a solid, then the mold is opened, and the finished part is extracted.
Understanding the differences between prototype and production molding can be a game-changer in your product development process. Most think that to have production-equivalent plastic parts, you need to build an expensive, long lead-time, hardened-steel production mold and that this can only happen at the end of the product development process when the design is frozen and production-ready.
When machining injection molds in hardened metals, only small amounts of metal can be removed with each tooling pass, or the cutting tools will break. This is the largest driver for the long lead times to create production tooling, which is typically anywhere from 5 to 16 weeks, depending on part geometry. Larger parts with more complexity take longer to machine. Likewise, parts with intricate geometry that require the use of small cutting tools to create the part geometry in the mold cavity will extend the tooling production timeline.
Prototype injection molding tools are typically single cavities by design, making it easier to make changes to fine-tune the part geometry. If, after molding parts and testing, a change to the part is needed, only one cavity needs to be modified. Metal-safe and non-metal-safe changes can be accommodated. A metal-safe change means that the part change adds plastic to the part, and the mold is altered by removing metal from the mold. If the change requires adding metal to the mold (removing plastic from the part), prototype tooling is easier to change than production tooling constructed of harder metal with multiple cavities; a pocket is cut into the mold, a plug is pressed into the pocket, and the new geometry is machined. Tools constructed with hardened tool steel must be welded to add material to the mold for non-metal-safe changes.
Prototype injection molds use the same injection molding materials that are used in production tooling. The difference between prototype and production injection molded parts lies primarily in the construction of the tooling and the number of cavities in the tool.
This website uses cookies so that we can provide you with the best user experience possible. Cookie information is stored in your browser and performs functions such as recognising you when you return to our website and helping our team to understand which sections of the website you find most interesting and useful.
A prototype is a preliminary model used for testing, while production refers to the final product made in large quantities after successful prototyping.
Prototype molds are typically CNC machined in aluminum or brass; the metal is softer and can be machined more quickly and, therefore, less expensive. While aluminum and brass are less robust than stainless steel over hundreds of thousands of molding cycles, molds constructed in these softer metals will typically still produce tens of thousands of parts before the tool wears and, depending on geometry, can produce many more without sacrificing dimensional accuracy over the life of the tool.
Prototype tooling mitigates scale-up risk and is inexpensive to fabricate; typical costs are $6K to $15K, depending on part complexity and size.
This is simply not the case. Just like 3D printed parts have accelerated the product development process, so too can prototype plastic injection molding drastically improve speed to market, de-risk product failures, and speed up design iterations. Prototype injection molding has progressed. Such plastic parts can be produced quickly at various critical decision points at any point in the design process with lower-cost prototype molds and injection molded parts. When 3D prints have progressed the design as far as it can go, prototype plastic injection molding can produce parts with geometry and material properties identical to production parts, provide the ability to get a head start on design verification and validation testing, and yield cost savings for higher quantities for pilot runs.
HDPE molded parts are a staple in many industrial applications – from idler pulleys to roller chain sprockets, the professionals at Retlaw have the skills to produce thermoplastic HDPE components for your company at the most affordable prices. We have a wide range of plastic types and products to choose from in our Wisconsin facility, and we can accommodate all your HDPE plastic part needs whatever they may be.
Single-cavity prototype mold fabrication can occur in one week, not several weeks or months. The plastic injection molded parts produced by this tooling can be used for user testing, plastics joining refinement, functional testing, and other part validation activities in advance of investment in production tooling.
Prototype injection molded tooling does not employ automated mechanisms for features in the part that are not in line with the direction of the mold opening. In prototype tooling, these features are created with components (called core pins or pickouts) that are manually loaded into the injection molding cavity and, when the part is molded and ejected from the mold, are ejected with the part. The operator must then manually strip these core pins from the part. The simpler design drastically reduces the cost of the prototype mold as compared to a production mold but increases the cycle time and, thus, the part cost.
The professionals at Retlaw Industries use HDPE for a variety of parts, and we can manufacture any component you need for strength and durability at a low cost. Our plastic injection design, tooling, molding, and assembly services are key contributors to dozens of industries, making us one of the most trusted plastic manufacturing companies in the nation. Make Retlaw Industries your top source for all OEM parts.
When a product design has been proven, and there is high confidence that the design will not change, production tools are machined from ultra-hard tooling steel. The hard metal reduces metal wear as the metal heats and cools, and parts are molded and ejected from the mold over tens or hundreds of thousands of times.
GETTING A QUOTE WITH LK-MOULD IS FREE AND SIMPLE.
FIND MORE OF OUR SERVICES:
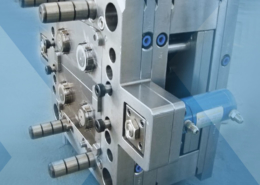
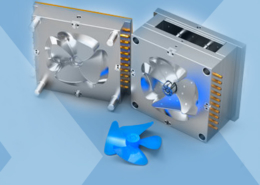
Plastic Molding

Rapid Prototyping
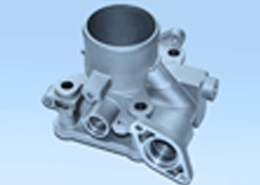
Pressure Die Casting
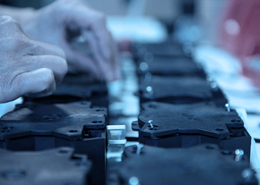
Parts Assembly
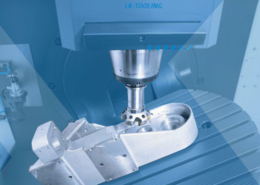