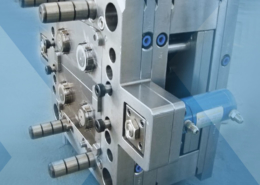
JDI Plastics: Plastic Injection Molding Company - plastics molding co
Author:gly Date: 2024-10-15
Multi-injection techniques 1 2 2 1 Overmoulding This process associates several materials by placing successive layers over the initial mouldings.This can be effected by different mould technologies such as rotation, translation, robot transfer, core movement… 2 1 Robot transfer Simultaneous injection 1 and 2, mould opening, robot transfer of the preform to the overmoulding position and evacuation of the finished product. Translation mould Injection 1, intermediate opening, translation to the overmoulding position within the mould, closing / locking, injection 2. (1) Mould with retractable...
A: The primary difference between soft tooling and hard tooling lies in the materials and durability. Soft tooling is usually made from urethane, silicone, or other flexible materials, making it cost-effective for low volume of parts. Hard tooling, on the other hand, is made from steel or aluminum, which are more durable and suitable for higher production cycles.
Soft tooling is a necessity for the low volumes of production because it is affordable, its production is fast and it can adopt to different purposes. Unlike traditional hard tooling, soft tooling can be produced quickly and at low costs, making it ideal for prototyping as well as small-batch manufacturing. This allows firms to change designs within short periods, undertake iterative testing and enter into markets faster without having to put up with huge amounts of money required by hard tooling.
BILLION ITALIA SRL Via Avataneo 50 10026 SANTENA (TO) Tel. 011 9491 972 Fax 011 9494 837 www.billion.fr ACTRONIC - BILLION Pol. Industrial Can Calderón C/Murcia n°48 nave 3B 08830 Sant Boi de Llobregat ( BARCELONA ) Tel. 93 652 87 10 Fax 93 652 87 11 COPYRIGHT BILLION S.A. - PRINTED IN FRANCE - 09/01 - DOCUMENT NON CONTRACTUEL POUVANT ÊTRE MODIFIÉ SANS PRÉAVIS BILLION UK Ltd 2 Fitzhamon Court, Featherstone Road Wolverton Mill, Milton Keynes, MK12 6LB Tel. 01908 2233 44 Fax 01908 2230 06 ANNECY BILLION SA 1, Avenue Victor Hugo 01100 BELLIGNAT - France Tél. 33 (0) 4 74 73 20 00 Fax 33 (0) 4...
4. Material Mimicry: Soft tooling replicates accurately the material properties of final products thereby giving valuable insights on performance and ergonomics of such items. It ensures functional and reliable prototypes through tests thus validation purposes are met.
1. Cost-Effectiveness: Soft tooling is far cheaper to produce than hard tooling. This is mainly because of inexpensive materials and simpler construction techniques used to make it. Hence, it is especially useful for start-up businesses and small organizations with limited budgets.
3. Small-Batch Production: In this regard, soft tooling is suitable for small volume production runs which are essential for testing, validating, refining designs before committing them to mass production thus preventing overproduction minimizing waste and ensuring that only thoroughly vetted products are produced on a large scale.
Multi-injection is synonymous with BILLION From pioneer in 1961 to expert today, BILLION offers you the benefit of their unique knowledge in the field of multi-injection. BILLION, is firstly a complete range of machines from 100 to 2200 tons, designed to be adaptable to all multi-injection technologies. It is also a control system specially tailored to integrate all the machine features. Finally and most importantly it is a team of experienced engineers with access to a wide range of injection moulding machines to progress your concepts and ideas to efficient production solutions. BILL ION,...
Longer tool life allows uninterrupted production for longer which is necessary to meet high volume manufacturing requirements. Injection moulds with these objects will withstand regular inspections and timely repairs, ensuring longer service life spans. This reduces downtime and increases productivity levels by maintaining schedules of production and keeping output consistent.
A: Soft tooling techniques often use materials such as silicone, urethane molding compounds, and cast urethanes. These materials are ideal for creating flexible molds that are quicker and less expensive to produce compared to the steel or aluminum used in hard tooling.
Additionally, soft tooling assists in producing parts that have qualities and material properties which closely resemble the final product thereby offering invaluable insights during testing and validation phases. For instance, through using prototype tooling for low volume runs companies may reduce waste while optimizing their manufacturing processes leading to lower cost per unit and decreased lead times. By making use of soft tools in low volume manufacturing, businesses can minimize waste generation while at the same time optimizing their production processes as well as ensuring quality without having to incur high costs or long cycle times associated with conventional means of manufacture.
GOLDSUPPLIER.COM expands globally, offering quality business opportunities, cost savings, convenience, and expertise in international trade. Trusted and recognized internationally.
When prioritizing lead time and cost considerations for prototyping and low-volume production runs, soft tooling is highly recommended. In such situations, it is employed by industries such as consumer products, aerospace, automotive etc., to quickly produce prototype parts used for testing and validation. Therefore, because of its flexibility and quicker turnaround times, it is an ideal choice for early-stage product development.
Tooling methods can differ greatly depending on the production volume, and this method selection will depend on factors such as budget, lead time and precision required. For small volume production, methods like soft tooling and rapid prototyping via 3D printing or CNC machining are often the best suitable. Soft tooling is cost-effective and flexible, accommodating quick changes with lower initial costs. Rapid prototyping technologies allow for quick iterations and design modifications which are good for perfecting a product before it goes to mass production.
Tool longevity is a vital issue in injection molding and affects directly the number of batches’ runs that can be made and thus, efficiency level achieved within manufacturing processes. The high-quality tool materials, such as sheet metal, significantly improve the strength and life of molds thus making it possible to increase production runs without changing tools frequently or replacing them. Manufacturers must use advanced fabrication techniques as well as strong materials that will make the molds maintain their precision for long periods so that part quality may become consistent while production costs go down.
The best place to use hard tooling with its superior durability and dimensional accuracy is in high volume production environments. For instance,the medical device production industry uses hard tollling while on the other hand the electronics manufacturing industry employs their use in mass producing components that have to be consistent enough and accurate. Even though there is a higher upfront investment required, hard tooling has a long life span which enables it withstand the stress brought about by ongoing high-volume manufacturing processes.
Once the materials have been determined, then manufacturing of mold takes place by utilizing delicate machinery processes such as CNC milling, EDM (Electrical Discharge Machining), grinding among others, so that intricate geometries with small tolerances can be made. This stage ensures that molds can endure high pressures and temperatures of the injection moulding procedure without getting damaged or losing dimensions.
A: Soft tooling is a cost-effective method of tooling that is best used for prototyping, short runs, and testing since it is quicker to produce and less expensive than hard tooling. Soft tools don’t handle high temperatures and pressures as well, so they’re ideal for applications where the production cycle is limited to a low volume of parts.
2. Flexibility and Speed: The production and modification rates of soft tooling are much higher compared to traditional hard tooling. This enables rapid prototyping as well as faster iterations hence enabling designers and engineers to rapidly fine-tune their products. This can significantly reduce overall product development cycle time by reducing lead times.
While considering tooling for short production runs, it is necessary to consider flexibility, cost effectiveness, and quickness. Generally, soft tooling is the preferred choice due to its lower initial costs, faster lead times than others and ability to accommodate design changes. Most of these tools are made from less strong materials such as silicone or urethane which are ideal for producing little number of parts.
A: Soft tooling is generally less expensive and faster to produce, making it suitable for short runs and prototyping. Hard tooling involves a higher initial investment due to the materials and precision required, but it is more cost-effective for mass production due to its long lifespan and ability to withstand numerous production cycles.
A: In injection molding, hard tooling refers to molds made from steel or aluminum. These materials are durable and can withstand higher temperatures and pressures, making them suitable for large volume manufacturing and production runs lasting thousands of shots.
V configuration : the versatility of the BILLION design Having considered all configurations, the experience of BILLION has led to the choice of a V configuration for the injection units due to the huge versatility and multiple benefits offered : minimum floor space requirement, quick mould change, ergonomics, traditional robot design compatibility, high speed production and a wide range of multi-material applications together with the capability for use in traditional single material applications. Distance between nozzle centres of 100, 150 and 300 mm, alternatives by request. Independent...
Bridge tooling is commonly used in medium volume production. It includes material such as aluminum or hybrid molds that balance between expenses and durability. Bridge tooling offers more uniformity than soft tooling and higher quality components which are produced in hundreds to thousands numbers.
High volumes call for strong and durable tooling ways including hard tools often from hardened steel. It assures consistency, durability, accuracy during long running of productions thereby making it ideal for producing several hundreds up to millions of parts. Although there is a relatively high upfront cost involved in this approach, but per part cost decreases significantly over large quantities rendering it an economical answer for huge-scale manufacturing.
When designing tools for manufacturing, a few important aspects need to be considered in order to ensure efficiency, accuracy and long life. First of all, it is important to understand the particular needs of the production process such as tolerances, material characteristics and production volumes. Moreover, designers should look at the geometry of the tool ensuring that it is optimized for both machining processes and materials being worked on. The employment of computer-aided design (CAD) and finite element analysis (FEA) can tremendously help in improving the process of designing tools by enabling performance prediction as well as detection of problems before production.
A: Yes, while soft tooling is a cost-effective method of producing parts, it has limitations. Soft tools don’t last as long and may not provide the same level of product quality and precision as hard tooling can. Additionally, they cannot withstand higher temperatures and pressures, limiting their use to short production cycles and small batches.
This subsequently calls for a series of heat treatments on machined molds aimed at further strengthening their hardness as well as long life. At this stage, strict quality checks and trials are conducted to ensure each mold conforms to dimensional accuracy and surface smoothness specifications. Once these examinations have been passed then only should one use them in mass productions so that uniformity is achieved through many cycles of injection molding in terms of quality and performance.
In summary, choice of the method should be pegged on the production volume while balancing issues such as cost, flexibility, and finesse necessary to meet specific project requirements.
Various strategic steps must be followed to achieve “hard tools” for injection molding process to meet the demand of high-volume production. The beginning point is known as design phase in which engineers create complex computer aided design (CAD) models of parts they want and molds to be used for this purpose. After finalizing the design, material selection is done whereby high toughness materials that are resistant to wear and tear like hardened steel are preferred.
A: A company might choose hard tooling for short production runs if the products require higher precision, better durability, and consistent quality. Although more expensive initially, hard tooling can produce parts with a smoother finish and more detailed mold patterns, which may justify the cost for high-quality or complex parts even in short runs.
A: Common applications for soft tooling include prototyping, short-run production, testing, and low-volume manufacturing. It is particularly useful when quick turnaround times and lower production costs are critical, such as in the development and refinement stages of product design.
However, some projects may require rapid tooling methods like 3D printing or CNC machining. These enable prompt fabrication and alterations without long tool setup process. Above all this presents a challenge on the tradeoff between hard tooling’s high expenses versus better quality of parts’ molding when volume can’t justify the cost.
A: Hard tooling typically provides a higher level of product quality due to the durability and precision of materials like steel or aluminum. This type of tooling usually allows for smoother finishes, more intricate mold patterns, and consistent part dimensions over long production runs.
During the process of choosing between soft tooling and hard tooling, application and production requirements play a crucial role.
To sum up, durable materials including sheet metal are critical in enhancing tool life in injection molding alongside effective maintenance practices.
A: Yes, soft tooling can be used for casting urethanes in injection molding. This method of tooling is suitable for creating prototypes and short-run parts with flexible materials. However, it is less durable and may require extra machining for precision compared to hard tooling.
Ultimately, various factors have to be considered before selecting the right tooling for short production runs that include: budgetary allocations; project schedules; and complexity of design among other issues in such cases. Choosing flexible approaches ensures that there remains a way through satisfying immediate manufacturing needs while also maintaining control over expences.
Another vital factor is selecting suitable coatings and surface treatments which can reduce wear and friction hence enhancing tool life and performance. Additionally, ease of maintenance and potential for modification are critical factors that should be incorporated into the design process thereby extending its usefulness while accommodating changing demands over time. Finally, collaboration with manufacturers will also produce practical decisions regarding how best to accommodate manufacturability whilst keeping costs down. By mixing these considerations together, they will facilitate an efficient way towards constructing tools suitable for modern manufacturing environments.
GETTING A QUOTE WITH LK-MOULD IS FREE AND SIMPLE.
FIND MORE OF OUR SERVICES:
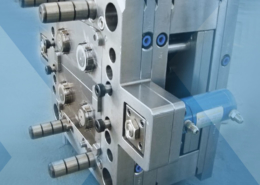
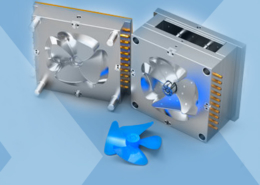
Plastic Molding

Rapid Prototyping
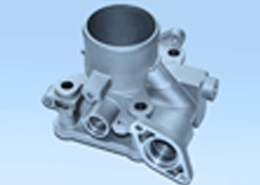
Pressure Die Casting
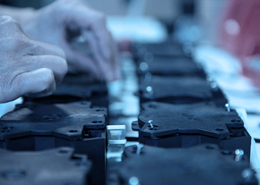
Parts Assembly
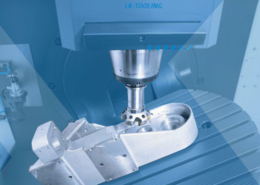