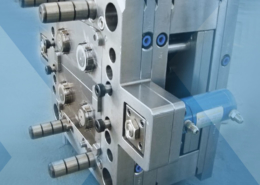
ISO Class 7 Cleanroom Molding, Pharmaceutical - clean room injection molding
Author:gly Date: 2024-10-15
When you consider that the speed of the EDM process may vary from 1,000 to 150,000 sparks per second, a machine that helps you choose the correct waveform, select the maximum power allowable by geometry, and automatically adjust the flush and cooling time between sparks is a pretty difficult machine to beat.
Sinker and wire EDMs selected for speed, volumetric accuracy, surface finish, reliability, cost of ownership and extensive warranty.
In ISO 9001 quality management systems, the Management Representative (MR) plays a crucial role. While the 2015 version of ISO 9001 no longer mandates this position, having a trusted management member serve as an MR remains vital for streamlining operations and maintaining quality standards.
Incorporating multiple automation technologies enables Industrial Molds to produce and repair highly complex, precision molds with a very lean team.
Steel supplier discusses high thermal conductivity metal powders that also address the skills gaps via user-friendly materials and promote sustainability via durability and higher cycle counts.
The work metal’s melting temperature and thermal conductivity require the EDM operator to adjust on-time, amperage, polarity, voltage and off-time parameters, which differ from one work metal to another. If the same EDM approach is used regardless of work metal, the end results could be vastly different.
Diamond compounds, with their varied grades, colors and base options, provide a comprehensive solution for mold builders in need of precise and superior polishing across diverse materials and applications.
Join MoldMaking Technology Editorial Director Christina Fuges as she gets the latest news on this mold builder's use of VR for mold design education.
However, there is one important difference necessary for the creation of structural foam rather than a solid polymer. In addition to the polyol and isocyanate, an inert gas or chemical blowing agent is added to the mix during the injection process. This changes the nature of the chemical reaction which ultimately occurs.
Intralox's integration of the Alpha Laser ALFlak has significantly improved their tool room efficiency when it comes to difficult welds and urgent repairs.
IMTS 2024: The four-axis Edmmax818W wire EDM from EDM Network offers a solution for simple 3D cutoffs to precision dies and tooling.
The structure of the material is like that of a sandwich, with the low density core completely surrounded by the higher density skin. The texture of the core has been frequently described as resembling a “sponge” or a “honeycomb”. Because of its unique core texture, structural foam is typically anywhere from 20% to 40% lighter than solid polymers, aluminum, steel, sheet molding compound or other commonly used materials.
The need for accuracy, finishes and repeatability are the biggest challenges moldmakers deal with. Electrode accuracy is incredibly important for high productivity and good product finishes. If an electrode is off by only 0.2", it will cause metal removal on one side of the cavity to work harder, leading to excessive burn time on the other side. Therefore, electrode manufacturing with better accuracy will help increase productivity and decrease burn times.
In order to reduce downtime on its EDM and CNC machines when setting up new jobs, moldmaker Kavia Tooling turned to a coordinate measuring machine from Hexagon Manufacturing Intelligence to create an offline zero transfer system ahead of the manufacturing process for parts and electrodes.
Identify pain points, tackle each one strategically and maintain flexibility to keep your moldmaking business on a path to growth.
To achieve the ultimate capability and level of productivity from your wire EDM on a consistent, repeatable and reliable basis, regular maintenance is a required task.
Explore the standout articles of September, featuring innovations, expert insights, and strategies to boost efficiency and quality for your moldmaking needs.
Less polyol and isocyanate are used than in standard solid polyurethane reaction injection molding, so that the resin does not completely fill the mold. Instead, the gas or blowing agent is activated by the reaction between the two components. It expands, filling the empty space of the mold with foam. This creates the “honeycomb” texture for which the interior core of structural foam is known. Surface cells collapse when they come in contact with the walls of the mold, resulting in the creation of the solid skin which surrounds the outside of the material.
In addition, structural foam retains the impact, element and temperature resistance common to thermoplastic and thermoset polymers. It experiences minimal to no thermal expansion, making it perfect for products which will be utilized in a wide variety of climates or temperatures. The acoustic and sound dampening properties of structural foam are also superior to those of standard solid polymers.
Smart sensors and sophisticated process and measurement data management are driving intelligent moldmaking to new heights.
Since EDM is a thermal process, the melting point/temperature and thermal conductivity of the work metal can create difficulties for the EDM operator. Knowing the elements that make up the material will help determine the optimum melting point/temperature and thermal conductivity.
Using data from a machine monitoring platform, Westminster Tool added almost 75 hours of capacity per week by shortening warmups and starting CNC and EDM machines sooner.
The EDM process, much like other metal-removal processes, presents two main difficulties that must be overcome: heat and contamination. Each tiny spark creates heat, and the more power and the higher the frequency of the spark, the more heat is created. A good spark should take a large shovel out of the workpiece and a very small piece of the electrode.
Steel supplier discusses high thermal conductivity metal powders that also address the skills gaps via user-friendly materials and promote sustainability via durability and higher cycle counts.
Five-axis electrode cutting enabled Preferred Tool to EDM complex internal screw geometry on an insert that otherwise would have had to be outsourced.
What EDM, automation and machining technologies are currently available to the mold manufacturing industry? MMT has compiled a list of some of the latest.
Formnext Chicago is an industrial additive manufacturing expo taking place April 8-10, 2025 at McCormick Place in Chicago, Illinois. Formnext Chicago is the second in a series of Formnext events in the U.S. being produced by Mesago Messe Frankfurt, AMT – The Association For Manufacturing Technology, and Gardner Business Media (our publisher).
This webinar will provide an overview of new developments in hot runners, controllers, mold components, predesigned molds, process monitoring and mold maintenance equipment. These advancements are designed with the goals of lowering scrap rates, optimizing process temperatures and managing energy consumption. The solutions also aim to support productivity and may contribute to extending the operational lifespan of tooling equipment. Agenda: Innovative undercut and thread-forming components Predesign mold bases and plate control Melt delivery and control solutions Process monitoring and maintenance
Discover how to enhance your mold design process with the right CAD/CAM tool for parting and cavity design. This webinar will explore CAD/CAM capabilities including how hybrid solid/surface modeling can streamline workflow and improve accuracy. Learn how to confidently tackle parting, runoff, and shutoff, ensuring precision and efficiency in your designs. Agenda: Part analysis QuickSplit techniques Parting and runoff strategies Shutoff solutions
EDM stands for Electrical Discharge Machining. A good way to describe the material erosion process of an electrical discharge machine is to think of the EDM spark as a shovel. Whether you are digging a hole or electrically removing material to form a cavity with an EDM, you remove material one shovel, or one spark, at a time. To dig a hole/cavity faster, you can use a bigger shovel (more power) or shovel faster (shorter pauses between sparks) or use a different-shaped shovel (electrical waveform).
The need for data to track information and the history of the mold-building process is ever-increasing, and mold component solutions can help.
EDM refers to wire, sinker and small-hole electrical discharge machining. Components include drives, generators, programming, flushing, wires, electrodes, graphite, filters and fluids.
Due to the electro-mechanical nature of wire EDM machines, there are several items in normal operation that routinely wear and require cleaning and/or replacement. If certain machine components are not properly cared for, machining speeds and accuracies will rapidly decay.
Discover how CAD/CAM functionality tailored for the mold industry can significantly enhance the mold design process. In part three of the webinar series, Cimatron will focus on designing waterlines and cooling components. It will demonstrate how CAD/CAM tools can verify drill line depths for water lines and baffles, ensure that minimum steel requirements are met while placing water lines, and provide a complete list of all baffle cutoff lengths. Additionally, it will explore how to confidently design runners and gates using CAD functionality specifically developed for these aspects of mold design. Agenda: Waterlines and verification Conformal cooling Baffles and charts Runners and gates
Engineers use properly preloaded bolts, blocks, springs and side-action cores to enhance functionality and reliability in various mechanical systems.
Burteck LLC experienced significant demand increases due to reshoring and invested in automated machining cells to step up its production output quickly and avoid losing business.
Lastly, structural foam also features highly paintable, aesthetically pleasing surfaces. In-mold painting (IMP) is possible for all structural foam products, further saving time and money. Multiple colors can also be applied to a single part in-mold. The surface is easy to clean and can be sawn, screwed, nailed or stapled without experiencing any problems.
After attending IMTS, it's clear that the integration of advanced technologies is ready to enhance precision, efficiency and automation in mold manufacturing processes. It’s a massive event, so here’s a glimpse of what the MMT team experienced firsthand.
Structural foam products have a lower than average risk of damage in the mold or during the removal process, making it a highly efficient and easily repeatable method. In addition, structural foam produces no potentially harmful styrene fumes, lowering the health risks for workers involved in the molding process.
Discover how to enhance your mold design process with CAD/CAM software specifically tailored for the moldmaking industry. In part two of this webinar series, Cimatron will demonstrate how to intelligently design mold components, such as slides and lifters, using powerful CAD/CAM tools to accelerate the design process. Additionally, it will cover how to avoid errors and ensure design accuracy for ejector pins by checking clearance distances, calculating cutoff heights correctly, and thoroughly documenting all ejector components. Agenda: Slides Lifters Inserts Ejection pins and charts
Structural foam is a composite material produced when a polymer, usually thermoset (but can be thermoplastic), is combined with either an inert physical gas, such as nitrogen, or a chemical blowing agent during the molding process. The result is not a solid material but a low-density, microcellular “core” combined with a high density outer “skin”. The core decreases the overall weight of the material while the solid skin allows it to remain strong and impact resistant.
The adoption of Mitsubishi wire and sinker EDMs, along with the OPS Ingersoll five-axis milling machine with automated cells, has enabled unmanned operations and improved precision. As a result, QTD has expanded its facility, grown its workforce and increased its business by 10-15% annually.
After attending IMTS, it's clear that the integration of advanced technologies is ready to enhance precision, efficiency and automation in mold manufacturing processes. It’s a massive event, so here’s a glimpse of what the MMT team experienced firsthand.
MoldMaking Technology addresses the complete lifecycle of the manufacture and maintenance of a mold—from design to first shot—by providing solutions and strategies to moldmaking professionals charged with designing, building and repairing molds. About Us
Sometimes, you are required to manufacture parts of a size larger than can be produced using traditional materials. How can these parts be created without sacrificing strength, stiffness and overall quality? Luckily, there is a simple, affordable solution: structural foam.
Join MoldMaking Technology Editorial Director Christina Fuges as she gets the latest news on this mold builder's use of VR for mold design education.
The use of structural foam as a manufacturing material comes with a large number of advantages. Of course, structural foam initially became known for its ability to create parts of unparalleled size, such as the roofs or body panels of vehicles. However, it soon became apparent that structural foam promised a number of additional benefits.
Gerardo (Jerry) Miranda III, former global tooling manager for Oakley sunglasses, reshares his complete mold design checklist, an essential part of the product time and cost-to-market process.
When used for conformal cooling in plastic injection, 3D printing opens a wide range of design freedom. This design freedom enables designers to develop highly-efficient thermal regulation networks. However, this blessing also comes at the expense of not only higher manufacturing cost but also higher design cost as the designer could spend weeks to develop optimal cooling channels. This webinar will explore strategies and tools — including SimForm, a front-end thermal simulation app — to help tool designers and tooling managers maximize the benefits of 3D printing while minimizing manufacturing and design costs. Agenda: 3D printing applied to the plastic injection industry 3D printing pros and cons Tools and methods to facilitate the integration of 3D printing
Due to its not quite solid nature, the base material used in the creation of structural foam is typically a thermoplastic polymer rather than a thermoset. Commonly used thermoplastics include but are not limited to: polyurethane, polycarbonate, polyphenylene oxide (Noryl), polybutylene terephthalate (Valox), and acrylonitrile butadiene styrene.
To achieve the ultimate capability and level of productivity from your wire EDM on a consistent, repeatable and reliable basis, regular maintenance is a required task.
After attending IMTS, it's clear that the integration of advanced technologies is ready to enhance precision, efficiency and automation in mold manufacturing processes. It’s a massive event, so here’s a glimpse of what the MMT team experienced firsthand.
There are several wire EDM machine tool manufacturers, and there are some significant differences in the machine design of each. But the importance and type of basic items that need to be maintained on all wire EDMs are very similar. When planning and scheduling wire EDM machine maintenance, required actions can be grouped into short interval and long interval items.
Structural foam is also highly moldable; it is able to produce variant wall thicknesses across a single part. In some cases, structural foam has even been able to generate wall thicknesses greater than the previous maximum of ½ inch (13mm). It also allows for thick ribs and bosses and reduces the risk of “sinks” over ribs or heavy cross-sections due to the lower viscosity of the mixture. Structural foam products experience less stresses overall during the molding process, and are highly resistant to warpage or deformation.
Understanding and facing the moldmaking industry’s obstacles to growth requires a strategy focused on increased profitability.
Join this webinar where Hexagon will explore how state-of-the-art CAD/CAM technology can drive your business forward. Learn how to optimize tool paths, enhance design accuracy and reduce lead times with advanced simulation. Discover the power of automation and real-time data for continuous improvement. Tailored for mold and die manufacturers, this session offers actionable insights to boost productivity and quality. Don’t miss this opportunity to gain a competitive edge in progressive die manufacturing. Agenda: Key challenges in progressive die manufacturing Optimizing tool paths Enhancing mold and die design accuracy Reducing lead times with simulation Automating processes for greater efficiency Leveraging real-time data for continuous improvement
A focus on electrode design and automation helps toolroom improve efficiency, reduce tooling costs and deliver higher quality products.
The process of molding parts from structural foam is very similar to the traditional method of reaction injection molding. Two components, for example polyol and isocyanate (which are combined in order to create polyurethane) are stored in liquid form in separate containers. They are mixed together to form a resin which is injected into a pre-prepared mold and cures via the means of a chemical reaction.
In ISO 9001 quality management systems, the Management Representative (MR) plays a crucial role. While the 2015 version of ISO 9001 no longer mandates this position, having a trusted management member serve as an MR remains vital for streamlining operations and maintaining quality standards.
After attending IMTS, it's clear that the integration of advanced technologies is ready to enhance precision, efficiency and automation in mold manufacturing processes. It’s a massive event, so here’s a glimpse of what the MMT team experienced firsthand.
The most important reason to properly schedule and perform this routine wire EDM maintenance is to ensure consistent and repeatable machining results for the aforementioned machine traits of speed, accuracy and surface finish. This level of maintenance also prevents machine failure and unexpected machine downtime.
Structural foam molding is also a highly cost-efficient process. Lower pressures and clamping forces are required during the injection and curing periods, allowing the tooling and molds to be made from lower cost materials such as aluminum. Cycle times are competitive with those of injection and reaction injection molding, making this a time-saving process as well as a money-saving one.
Structural foam parts are extremely lightweight – typical weights vary from 55 pounds per cubic foot to a mere 2 pounds per cubic foot. In addition to this decrease in weight, structural foam is strong, durable, and extremely stiff – in fact, up to 8 times stiffer than similar materials such as solid polymers. The modulus of the material increases along with its density, up to a fantastic 250,000 psi. In addition to this, since it is a foam, the material makes for a great thermal and acoustic insulator.
It’s easy to imagine the advantages automation offers the moldmaking process, but it's challenging to change one’s mindset, develop a plan and invest.
MoldMaking Technology Editorial Director Christina Fuges sits down with Murphy Forsyth, GM – Injection Molding and Director Of Marketing for Zero Tolerance LLC in Clinton Township, MI.
Released earlier, this video remains a valuable recruitment tool and is being re-promoted in celebration of Manufacturing Day 2024.
A connected software solution streamlines the moldmaking process by providing a unified source of design data, enhancing efficiency and reducing errors, with five key steps benefiting from this integration.
MoldMaking Technology Editorial Director Christina Fuges chats with Steve Michon, co-owner of Zero Tolerance in Clinton Township, Michigan, about the excitement of solving problems, the benefits of showing gratitude, the real struggle with delegation and the importance of staying on top of technology. This episode is brought to you by ISCAR with New Ideas for Machining Intelligently.
Moldmakers rely on electrical discharge machining (EDM) routinely. EDM refers to wire, sinker and small-hole EDM. Sinker includes an electrode and a workpiece both submerged in dielectric fluid; wire uses a thin wire to cut with electricity; and, with small hole an electrode is a cylinder used to machine a hole. Considerations for EDM efficiency include depth, accuracy and finish, and components to consider include drives, generator, programming system and flushing. Other facets include wires, electrodes, graphite, filters and fluids.
Good cleaning habits and care of a wire EDM machine is highly recommended. Regular and systematic cleaning of the machine also can extend the life of some consumable items.
After attending IMTS, it's clear that the integration of advanced technologies is ready to enhance precision, efficiency and automation in mold manufacturing processes. It’s a massive event, so here’s a glimpse of what the MMT team experienced firsthand.
Structural foam is a manufacturing material which pairs a foamed core with a solid outer “skin,” rather than remaining solid all the way through. It is lightweight and flexible while also maintaining the good strength and stiffness compared with traditional polymers such as polyurethane, polyester or epoxy. The ability of structural foam to produce parts of unprecedented size has led to revolutions in the production of vehicle roofs, interior and exterior body panels, housing for medical equipment, and even skis.
Steps to improve data-driven decision-making and key features of a cloud-based system for mold monitoring and asset management.
Taking advantage of the latest EDM technology will allow you to remain competitive while improving surface finishes and accuracy—in addition to reducing cycle times in your shop.
The EDM process priority refers to the desired metal removal rate, electrode wear and surface finish. This information helps the operator determine the best approach to the job. However, regardless of what is identified as the main priority, electrode size, detail and shape must be known in order to determine the appropriate machine parameters, including amperage, on time, off time, voltage and polarity.
A water-based, eco-friendly plastic mold cleaning system helps Rankine-Hinman Manufacturing restore flow rates and avoid big-ticket failures on complex and costly molds.
GETTING A QUOTE WITH LK-MOULD IS FREE AND SIMPLE.
FIND MORE OF OUR SERVICES:
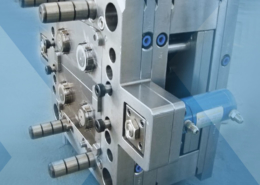
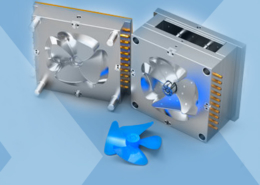
Plastic Molding

Rapid Prototyping
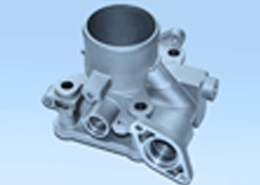
Pressure Die Casting
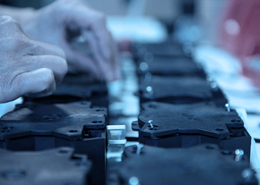
Parts Assembly
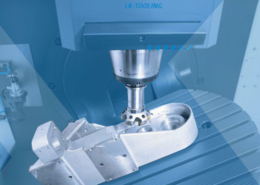