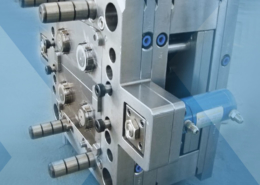
Is Short Run Injection Moulding Expensive? - short run injection molding
Author:gly Date: 2024-10-15
Additionally, considering wall thickness, runner design, and cooling channels during the mold design phase can greatly improve part performance and production efficiency.
EasyFlo Series products are easy-to-use, mercury-free polyurethane resins with simple, 1A:1B mix ratios by volume. These super low-viscosity liquids make for perfect detail penetration and bubble-free castings without the need for vacuum or pressure techniques. Rapid demold times make EasyFlo products ideal for high-volume, fast-cast applications. This series includes options that can be poured, rotocast and sprayed.
Dimensional Accuracy: Achieving high dimensional accuracy with LDPE can be challenging due to its soft nature. Careful consideration of mold design, processing parameters, and part specifications is essential to achieve desired tolerances.
Ribbing: Incorporating ribs can improve the strength and rigidity of molded parts without significantly increasing material usage. Ribs should be designed to enhance flow without obstructing it, ensuring that molten LDPE fills the mold cavity effectively.
Yes, LDPE is highly moldable due to its low viscosity and excellent flow characteristics. It is particularly well-suited for injection molding, allowing manufacturers to produce a wide range of products efficiently. LDPE’s flexibility and ease of processing make it a popular choice for items such as food containers, toys, and medical devices.
Its resistance to chemicals and moisture makes it an excellent choice for food packaging, while its flexibility allows for innovative designs in toys and household items.
Understanding the properties of Low-Density Polyethylene (LDPE) is essential for appreciating its versatility in various applications.
NOTES: Vacuum and/or pressure casting techniques are recommended for these products. These formulas are not recommended for long-term exterior use. They can be sealed with a UV-stable clear coat and/or UV Additive can be added to the liquid mixture for longer outdoor use.
Proper mold venting prevents defects like air bubbles, while optimized gate placement ensures smooth material flow throughout the mold.
These plastics are separated into five different series, highlighted below. From super low-viscosity, fast-setting resins to water-clear options, almost any color, size, shape, weight and appearance can be achieved by using these systems. Utilize available accessories to help achieve the desired look and feel.
The typical processing temperature for LDPE injection molding ranges between 160°C to 220°C (320°F to 428°F). This temperature range helps achieve optimal melt-flow properties, ensuring that the material fills the mold cavities effectively while minimizing defects such as warping and flow marks. It’s essential to adjust these temperatures based on specific material grades and product designs.
Kast Series products are two-part, room-temperature curing (RTV) systems designed for use in a variety of applications including foundry, special effects, prototyping, vacuum and thermo-forming, and many other industrial and commercial applications.
Warping: Uneven cooling can cause warping, particularly in parts with varying wall thicknesses. Proper cooling strategies and mold design can help maintain the integrity of the part.
Additionally, LDPE is used for enclosures and protective casings in various industries, providing reliable durability and resistance to chemicals.
Polytek's two-part, room-temperature curing polyurethane plastics are available in varieties that can be poured, brushed or sprayed to create castings with unlimited versatility.
This article will delve into the properties, processes, and applications of LDPE, shedding light on why it’s such a popular choice in the manufacturing industry.
It is known for its flexibility and good chemical resistance, particularly against acids and bases, making it ideal for diverse industrial applications.
Poly-Optic® 14-Series & 17-Series plastics are specifically designed for applications where optical clarity is a must. Castings will be water-clear; however, PolyColor Dyes can be added to obtain clear, colored castings. In addition, Poly-Optic systems can be filled with metal, marble and many other fine powders to achieve myriad effects. Poly-Optic® 17-Series products are mercury-free formulas.
When designing parts for LDPE injection molding, several factors must be taken into account to ensure optimal performance and quality.
HDPE (High-Density Polyethylene) and LDPE (Low-Density Polyethylene) differ primarily in their molecular structure, which impacts their properties and applications. HDPE is more rigid, with higher tensile strength and stiffness, making it suitable for items like containers and piping. In contrast, LDPE is softer and more flexible, ideal for applications requiring impact resistance and pliability, such as packaging films and toys. Additionally, HDPE typically has a higher processing temperature and can be molded into parts with greater dimensional accuracy compared to LDPE.
One of the primary uses of LDPE is in packaging. Its flexibility and moisture resistance make it ideal for food containers, films, and bags.
Kast products were developed to provide high moisture resistance, improved filler suspension, easier premixing of the components, and minimal shrinkage.
In summary, LDPE injection molding is a vital process in manufacturing, offering flexibility, impact resistance, and versatility across various applications.
Flow Design: Optimize the flow path in the mold to minimize resistance. This includes considering gate placement and runner design to achieve a smooth filling process, reducing potential issues like air traps and incomplete filling.
Its unique properties make it ideal for producing consumer products, packaging, and industrial components, making it a key player in the plastics industry.
We are committed to helping you elevate quality standards, fostering enterprise growth, and actualizing your internationalization strategy.
Poly 15-Series feature pourable, room-temperature curing resins that mimic the density of thermoplastics (e.g., ABS) or wood, while other options are great options for constructing lightweight mold shells, composites, or master models.
Dive deeper into the benefits and applications of LDPE injection molding to unlock new possibilities for your manufacturing needs!
LDPE films are commonly used for wrapping perishable items, while its lightweight nature ensures that products remain cost-effective for shipping.
If you’re curious about how low-density polyethylene (LDPE) is transformed into everyday products, you’re in the right place.
It is often used in the production of medical devices and components, where its flexibility and compliance with health standards are critical.
Poly 15-Series plastics are versatile systems that are used in countless commercial, industrial, tooling, prototyping, craft, prop and master making applications. These plastics offer an up-front cost savings compared to the expensive tooling costs associated with metal molds required for injection-molded thermoplastic parts.
LDPE plays a crucial role in the manufacturing sector, especially when it comes to producing consumer goods, packaging materials, and industrial components.
Shrinkage: LDPE tends to shrink as it cools, which can lead to dimensional inaccuracies. Understanding the material’s shrinkage rate and designing accordingly can mitigate this issue.
Its lower density makes it softer and more pliable than other types of polyethylene, like HDPE (High-Density Polyethylene).
Low-density polyethylene (LDPE) is known for its versatility and adaptability, making it a popular choice across various industries.
It can bend and stretch without breaking, with optimal performance in environments below 150°F, making it perfect for products like food packaging and toys.
Now that we’ve covered the process let’s look into the advantages and applications of LDPE injection molding in various industries!
Whether you’re a seasoned professional or just starting out, you’ll find valuable insights to enhance your understanding of this versatile thermoplastic.
Injection molding is one of the most efficient ways to manufacture products from LDPE, and understanding the process and key parameters is crucial for achieving high-quality results.
EasyFlo plastics are incredibly versatile and work well for countless commercial, industrial, hobby, craft, prop and display projects.
Select a product line below to learn more or continue to scroll to review product line features and common applications:
Thanks to its unique molecular structure, LDPE is known for its incredible flexibility, impact resistance, and overall durability.
Hi, I am Sparrow Xiang, COO of the HiTop company, me and my team would be happy to meet you and learn all about your business, requirements and expectations.
Wall Thickness: Maintaining consistent wall thickness is essential. Thicker areas may cool unevenly, leading to warping or longer cycle times. Aim for uniformity to facilitate efficient flow and minimize defects.
Absolutely, polyethylene, including both LDPE and HDPE, is one of the most commonly used materials in injection molding. Its versatility, excellent chemical resistance, and cost-effectiveness make it a popular choice across various industries. Injection molding allows for the efficient production of complex shapes and high-volume manufacturing, making polyethylene ideal for applications ranging from packaging to industrial components.
As industries look for sustainable and cost-effective materials, LDPE continues to shine as a reliable option, driving its demand and significance in today’s market.
HITOP is committed to assisting customers by offering a comprehensive one-stop solution, encompassing product design enhancement, initial sample creation, mold fabrication, injection molding, and product assembly.
Household items like storage bins, kitchenware, and even squeeze bottles often utilize LDPE due to its impact resistance and aesthetic appeal.
A well-designed mold can minimize common defects like warping or sink marks, ensuring consistent and high-quality results.
Poly Plasti-Flex is a low-density, slightly flexible plastic that can be used to make decorative trim, props or impact resistant parts.
Poly-Optic resins are the plastics of choice for mimicking glass and ice-like features and are widely used to create stunning prototypes (lenses, bottles, containers), as well as unique art, medical models, sculpture and display items.
GETTING A QUOTE WITH LK-MOULD IS FREE AND SIMPLE.
FIND MORE OF OUR SERVICES:
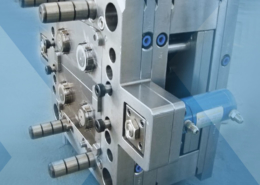
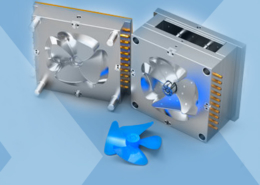
Plastic Molding

Rapid Prototyping
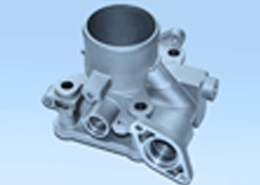
Pressure Die Casting
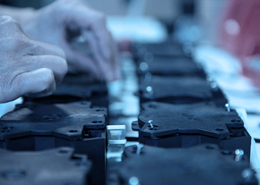
Parts Assembly
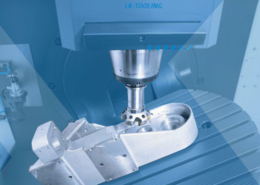