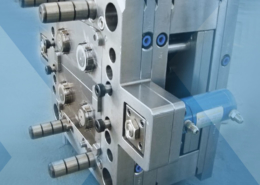
Is it possible to use sand casting for molding of plastics? - casting plastic
Author:gly Date: 2024-10-15
Finally, short-shot issues can be caused by molding machine defects. A machine that produces inadequate pressure is a common culprit.
Now that you understand how to diagnose and fix a short-shot plastic injection molding issue, you can take steps to minimize downtime and optimize output. Catching these problems early can help you avoid major losses down the road.
If not, it will become trapped in the mold, causing inadequacies. Checking your vents or adding more vents during the design phase may help alleviate this problem.
Plastic plays an integral part in almost every person’s life. It helps make products and components that are durable, corrosion-resistant, strong, and light.
Delrin 570is a 20% glass filled acetal homopolymer blend. DuPont Delrin® is a popular acetal homopolymer brand name, and the most commonly used acetal homopolymer. The combination of glass in Delrin® acetal resin gives this material excellent stiffness, strength, and stability. This combination offers higher mechanical properties at elevated temperatures.
Another mold-design problem that can cause a short shot is an imbalance in the mold or inadequate dimensions of runners and gates. Inconsistent mold thickness can lead to temperature control issues as well.
Short-shot issues are often detectable during quality control checks. These can include visible changes in the part’s appearance or dimensions. Other signs are holes or thinner segments on the product’s surface.
This article covers how to diagnose and fix short-shot problems. It will help you get your production line running again. Keep reading to learn more.
Another common cause of short-shotting is improper venting. The air inside the mold that the resin displaces needs a space through which to escape.
Plastic is used in almost every industry. These include consumer goods, construction, aerospace, computer, and automotive technologies, to name a few.
It is commonly utilized in spools, fixtures, and electrical components where dimensional stability and enhanced mechanical and insulating properties are required.
There are several main causes of short-shot issues. A common one is a high plastic viscosity. This restricts flow, so smaller crevices in the mold do not get filled.
Most components are made using plastic injection molding. This is an efficient and reliable method, but there are a few common challenges that technicians can face, including short-shot plastic injection molding issues.
Nova Stevensville is an original equipment manufacturer (OEM) that serves automotive and other industries. We pride ourselves on meeting the unique needs of each client by supplying the precise parts they need to be successful. Contact us today for pricing or to learn more about our products and services.
Nova is a world-class producer of plastic molded components for clients in both the automotive and non-automotive industries.
Our team uses high performance thermoplastics to design and manufacture solutions — whether injection molded, machined, stamped, fabricated, or assembled — that exceed the demands of your specific applications so you can focus on product and market development.
Short-shot plastic injection molding refers to a common issue in the molding process. This occurs when the melted plastic resin fails to fill every space within the mold cavity. This results in a malformed component that must be remade.
Misplaced nozzles, sprues, runners, and gates also can cause uneven polymer flow. Making minor adjustments to the placement of these–or mold design in general–can produce a more natural melt flow.
A similar cause is inconsistencies in the material. This means that not all of the resin will fill the mold cavity as intended. For this problem, you should do quality control checks on the storage of the resin or change sources to get a more consistent product.
You can easily fix this by either increasing the melt temperature or choosing a different resin with a lower viscosity. Also, better control over mold and melt temperatures throughout the process can help ensure the right viscosity.
Recalibrating your machine is a good place to start. Also, ensure that the reciprocating screw or the barrel has not been compromised.
Available in sheet and rod, it is easily machined with standard metal working equipment. Tolerances of +/-.0005 can be achieved with experience. The glass can lead to some premature wear of tooling, so care should be taken to avoid excessive tool speeds.
GETTING A QUOTE WITH LK-MOULD IS FREE AND SIMPLE.
FIND MORE OF OUR SERVICES:
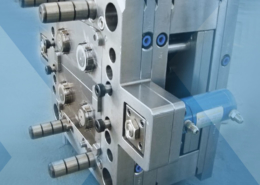
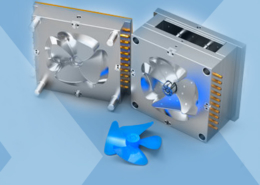
Plastic Molding

Rapid Prototyping
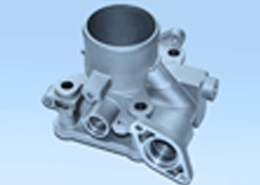
Pressure Die Casting
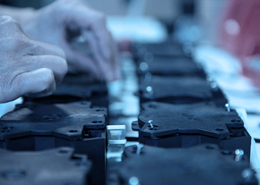
Parts Assembly
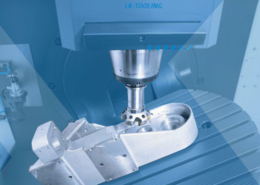