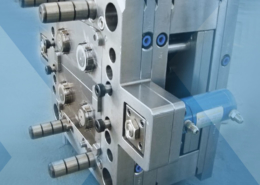
Introducing Extrusion Moulding Process - extrusion and injection moulding
Author:gly Date: 2024-10-15
As well as the usual warnings that come with handling industrial equipment, one of the biggest challenges in plastic overmolding is the reduction in chemical bonding between overmolded materials and cool substrates.
To maximize adhesion in this process, substrates must be carefully handled to prevent contamination of surfaces that could impact adhesion.
It also produces a significant amount of scrap, although there are now a number of overmolding providers that claim to have eco-friendly credentials.
Other common items include personal care products like shampoo bottles and shaving razors and tools like cordless drills and screwdrivers.
Of course, plastic can be used with plastic overmolding but remember that the process produces a single part by bringing together various materials.
Usually, this is down to their investment in R&D for manufacturing and processing materials, and using alternative materials like bio-plastic or post-consumer plastics.
But what exactly does this process entail? And how, as a designer, architect, or artist, can it help you? Is it sustainable? What are the dangers? And what should you know about it?
lastic overmolding also enhances the possibilities of design by creating an opportunity to use multi-material components.
The molding tool needed to make the moldings adds additional initial costs to the production process both in time and money.
Alternatively, multiple material plastic overmolding requires a unique injection molding machine that is equipped with two or more barrels.
Plastic overmolding plays an integral part when it comes to modern-day manufacturing, by making possible the fast assembly of different materials to create one unified product.
Filed Under: Plastic Injection Molding, Injection Molding
Typically the first material, sometimes referred to as the substrate, is partially or fully covered by subsequent materials like plastic to protect the substrate or improve the overall performance of the product being created.
The ejector pins are mounted in an ejector plate. The motion of the ejector plate forward allows the pins to move forward, pushing the part off the core. The ejector retaining plate holds the pins into the ejector plate.
This can be different plastics, used as an overmolding material, to create the substrate, or both; rubber, which can also be used as an overmolding material; and metal, which often forms the substrate people wish to overmold with a softer polymer or thermoplastic.
In both examples, heated plastic in the shape of resin pellets is injected into a mold displacing the air which escapes through vents in the injection pins.
In the automotive market, for example, it can eliminate the need for injection molding and assembly for components like gaskets or bumpers, as well as secondary finishing operations including priming, painting, and coating.
Mold halves are attached to the molding platens by the clamp plates. Mold clamps use large bolts to hold them in place; other machines hold the mold onto the platen with magnets.
Liquified plastic is pushed through the nozzle of the barrel of the molding machine. The nozzle seats against a surface on the mold called the sprue bushing and locating ring, which help center the nozzle to the mold.
Cavity and core mold halves are insured to be in proper alignment during mold close by the use of guide pins (or pillars) and guide bushings (or sleeves).
© 2022 DesignWanted S.r.l. (Innovative StartUp) Registered office: Via Aurelio Saffi 29, 20123 Milan (Italy) | VAT no.: 10565330965 | ROC no.: 36152 | REA no.: MI-2541466 | Share capital: 12.540€
An injection mold is a tool comprised of a series of parts that allows molten plastic to be formed and cooled in such a way as to create a discrete part shape.
Plastic is injected hot and is cooled by cooling channels that allow conduction to cool the part. Working fluid is typically water, although oil can be used in high temp applications.
Plastic flows through the sprue bushing in a sprue, then to individual runners which take the material to the gates - the entry point of the material to the individual cavities.
Some molds are equipped with internal cooling or heating lines where water is cycled through the mold to help with this part of the process.
East West is a global manufacturing services company focused on the realization of products, from design through distribution. As specialists in onshore, nearshore and offshore manufacturing, we offer a seamless path to scale and an exceptional speed-to-market strategy while driving down costs and adhering to the highest quality standards. We are one integrated family, working together to support our customers throughout the entire product lifecycle. Our vision is to make the world a better place – cleaner, safer, healthier and smarter.
In this sense, a huge part of evaluating the sustainability of plastic overmolding comes down to material choice and the individual’s own practice.
If you're up for an even deeper dive in the world of plastic injection molding, check out this video from a previous blog post. In it, one of our capable engineers explains the ins and outs of injection molding. The video is about 12 minutes long, and packed with great information.
Let’s begin with insert molding, a process that uses a molded material or component and places it into an overmolding tool. It is then coated with molten thermoplastic or rubber.
Used for a wide range of applications, plastic overmolding can help to improve the ergonomics of a product, break up colour, add flexibility to rigid parts, or simply be used to fuse different parts of a product together.
Kieron is a freelance writer and Digital Consultant who doesn't consider himself a design lover but a user of design - which to him is more than enough.
Perhaps the most universal example of this is the production of a toothbrush, which uses plastic overmolding to combine different coloured parts as well as the fixing of rubber grips onto the stiff handle.
Cavities are areas of the mold where the part is formed into desired shape. Molds must be balanced, so there are typically only a certain number of cavitations allowed (1,2,4,8, etc...)
In terms of production, plastic overmolding eliminates the bonding step and reduces secondary operation, which can have a positive impact on labor costs.
So you've designed a product. You've gone through the RFQ process, sharing your CAD drawings with engineers who probably made even more tweaks. The part is going to be made of plastic using the injection molding process. But you've never made a plastic injected part before. There are a lot of new words and phrases being tossed around and you don't really know what they all mean.
Plastic overmolding is a molding process resulting in a seamless combination of multiple materials to form one single part or product.
There are several sources and various videos on the internet outlining ways in which plastic overmolding processes can be replicated at home. Explore at your own will.
No one would blame you for looking for a glossary of terms right about now. Fear not. Below, we break down the components of an injection mold in simple, easy-to-understand language. It even includes labeled cutaway drawings. I promise, if you didn't understand how an injection mold worked before, you will after reading this.
GETTING A QUOTE WITH LK-MOULD IS FREE AND SIMPLE.
FIND MORE OF OUR SERVICES:
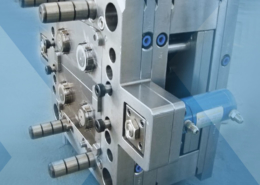
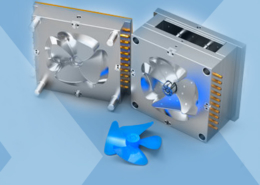
Plastic Molding

Rapid Prototyping
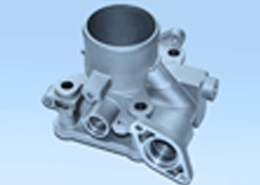
Pressure Die Casting
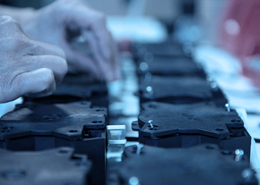
Parts Assembly
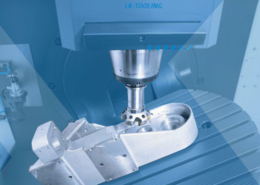