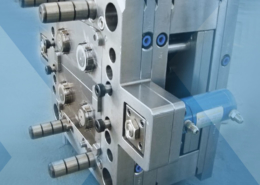
Insert Molding vs. Overmolding: What's the Difference? - overmolding injection m
Author:gly Date: 2024-10-15
Prototyping is a powerful tool for businesses and entrepreneurs. It’s a way to assess or present a physical product before going to full-scale production.
Now you know more about how to develop a plastic prototype. You’ve also learned how to gain a competitive advantage, especially if you’re manufacturing goods in China.
Our next plastic prototyping method is vacuum casting. It’s another rapid prototyping technique that enables fabricators to duplicate dozens of plastic parts.
The resulting plastic prototype will have mechanical properties that are close to an injected part. However, this outcome varies depending on the desired functionality and appearance of your project.
A fabricator might use one of several resins, including an ABS-like, acrylic, or epoxy material. The resin that you choose for your project will vary depending on your desired visual and mechanical properties.
Stereolithography is an excellent plastic prototyping method for producing single units. It enables fabricators to create geometrically complex shapes.
Our final plastic prototyping method is CNC machining. In this process, fabricators use a digital milling machine. This plastic prototyping method is ideal for producing one-off units for functional testing.
I am Ibrahim from Palladium Company. Our aim is to develop and provide s solutions and services for cell phone, computer networks and information system applications.
This method takes advantage of the vacuum effect. During plastic prototype manufacturing, the fabricator will inject material into a silicone mold. You might also hear vacuum casting called silicone molding for this reason.
A plastic injection rapid tooling is usually manufactured to produce plastic prototypes in the real material. The process for creating a prototype using this method is much like the practice used for a full production run.
Plastic prototype companies inject raw material into the mold using a vacuum bell jar. It will take 30 to 40 minutes for the resulting cast to harden.
The creation of a silicone mold requires a master model. Fabricators may create the master model using 3D machining or 3D printing. They’ll then use the 3D printed object to create the silicone mold.
It will also give you a better idea of your requirements for a full production run. Furthermore, a prototype created using this method will allow you to evaluate all the parts you’ll need. In addition, it will lay the foundation for the subsequent mold for your full production run.
A plastic injection mold prototype enables you to experience, in real life, a near-perfect replica of your final product. There are many industries that commonly take advantage of this method. These industries include:
Resultantly, it cost less, and you can get this kind of project started faster. All you need to get started with CNC plastic prototyping is a CAD rendering.
With this in mind, a firm may help you to create one of two kinds of mockups—either a functional or visual prototype. A visual prototype will simply give you an idea of the appearance of your final product. Meanwhile, a functional prototype will provide you with a representation of the desired final project—from the material to the mechanics.
PET’s popularity among PET injection molding manufacturers and their customers is a result of the availability of the materials and relatively low cost. In addition, PET is:
Plastic injection molding works well for fields that require considerable testing and certification. One such industry is the medical sector. With plastic injection molding, you can satisfy regulatory constraints and requirements in this and other fields.
You can also use this method to create a transparent part. Furthermore, you can create a wide range of finishes once your prototype part is complete.
The first plastic prototype manufacturing method—injection molding—requires an extra step before creating a mockup of your product. As its name implies, your design firm must create a mold before creating your prototype.
Consumers commonly find PET as the material used in plastic jars, convenience packaging and plastic bottles, including those used for carbonated beverages. In the 60 years since it was first introduced, PET has become one of the most widely used and most sustainable plastic materials in the world. Interested in using this material for your project? Request a quote to get pricing.
With Prototech Asia, you can rest assured that experts are always handling your projects. What’s more, we’re passionate about our work. Also, we have an extensive network of partners across multiple industries, so we can provide you with the best possible solution for your needs.
With Prototech Asia, you’ll have easy access to this service. Whether you need a small series of plastic or metal prototypes, we can meet your needs.
With the right mold material, you can come as close as possible to the final product with your prototype. There’s a wide choice of materials available.
A member of the polyester family, PET is the synthesis of ethylene glycol and terephthalic acid. The addition of glycol produces PETG, widely used by PET injection molding manufacturers in plastic injection molded bottles and containers.
Contrary to the SLA plastic prototyping method, CNC plastic prototyping is a subtractive process. In other words, it involves the removal of material.
The injection materials vary in flexibility, rigidity, and texture. You can even paint them the desired color or create a crystal-like transparent prototype.
This method allows you to test your concept fast and cost-effectively. At the same time, you don’t have to compromise quality for these benefits.
The fabricator adds layers using a machine. The machine is controlled by a computer. During the process, the computer will direct a UV laser to solidify liquid material.
If so, creating a plastic prototype is an important part of the early manufacturing process. What’s more, it’s the foundation for a planned production run.
To create the mold, a prototyping firm might use a common mold base and aluminum. These materials enable the fabrication firm to reduce costs—and the time it takes to produce your prototype.
Your finished prototype is only as good as your fabricator. Prototech Asia specializes in rapid prototyping services and high-quality finishes. If you manufacture goods in China, nearby rapid prototyping can give you a remarkable advantage over your competitors.
This practice is important because it allows you to work with a physical representation of your product quickly. It could also give you an opportunity to show your idea to potential investors. In this way, you could gauge interest in your idea before its launch.
A fabricator can reuse the silicone mold several times. However, it has a relatively limited service life. During the service life of the mold, however, the fabricator can create a perfect duplication of any part.
The fabricator will begin the process by performing a complete analysis of your product. They’ll then design a tooling plan for your mold. Once the mold is ready, they can move on to creating your prototype.
Plastic injection mold prototyping enables fabricators to create high-precision mockups in fine detail. What’s more, they can use the prototyping method to create complex shapes. They can create prototypes for products that range in weight from a few grams to several kilograms.
They can even use a plastic injection prototype for their marketing activities. In some cases, project owners can use this kind of prototype for a limited production run.
For example, you could decide to polish your finished prototype. You might also decide to remove any rough edges. Furthermore, you could paint your prototype any color that you desire.
You can accomplish this task by creating or requisitioning a computer-aided design (CAD) model. A CAD model is a digital mockup of your idea. It will show you and the specialist who will create your prototype what your product should look like.
We guarantee that our prototype production methods will meet your requirements. They’re even more efficient than 3D printing.
This feat is possible even with complex shapes. The resulting prototypes are perfect in every way. They even have a quality that compares to the final product.
Using the resulting prototype, you can collect reliable information. For example, your injection molded prototype might give you insights into the mechanical operation of your product.
Contact Prototech Asia today at (+86) 156 0669 3070 or connect with us online to get started turning your concept into a reality.
SLA plastic prototyping is a high-precision method for products that require fine detail. Fabricators can use this method to create remarkably thin layers. The layers can measure anywhere from 0.05mm to .10mm in thickness.
The CAD model will also show how the various parts of your prototype will fit together. More importantly, it will show how your product will function as a whole.
We offer a wide range of services—from designing a plastic prototype to prototype manufacturing—with our expert team of designers and engineers. Our diverse portfolio includes automotive engineering, electronics, medical device development, and more.
Casting enables fabricators to create high-precision plastic prototypes in fine detail. A silicone mold makes it possible to re-create prototype parts that are identical to the final product.
Still, fabricators can use CNC machining plastic prototyping with a range of materials. This method is efficient for producing ten or fewer prototypes.
PET was first polymerized for use as textile fibers known as polyester. Today, PET injection molding manufacturers utilize the material to produce strong, lightweight packing.
Although it looks and feels like PET, PETG (or copolyesters) is a modified PET, produced by adding a second glycol during polymerization. PETG removes the hazing that can impact PET and reduces the crystalline effect that can cause PET to become brittle. PET plastic injection molding machines can use PETG to produce bottles that are softer and more pliable for a more comfortable grip. PETG offers clarity, toughness and stiffness and is used in medical test tubes and bottles, lighting fixtures and appliances. The material’s benefits come with a higher cost than the cost of PET.
Prototyping is a vital part of product development. For instance, you may have a product that you want to take from concept to final build.
Yet other resins are less rigid. Still, there are limited material choices when using the SLA plastic prototyping method.
Food, beverage and consumer products industries rely on PET for many of their packaging needs. Among the common applications are:
With the right material, a finished plastic prototype has the robustness and mechanical properties of a final product. Accordingly, project owners can perform tasks as needed.
With a plastic prototype, you can test your design. Before building a prototype, however, you’ll need to formalize the plans for your project.
Furthermore, fabricators can create highly realistic prototype finishes. Despite the use of resin, the resulting plastic prototype will have functionality and surface quality that compares to the real product.
Again, machine prototyping is possible using a wide range of materials. Accordingly, it’s a bit easier to find the right material for your project when using this method.
The fabricators automate the entire process. The work of the machine is controlled by a computer. The computer will direct the machine using a 3D file.
We are looking for a factory that will manufacture mock-ups for our phone case with final finishing, and we are looking for long- term cooperation.
Using this method, a fabricator can create your prototype in as little as two to four weeks. Furthermore, the resulting prototype will likely cost 40% to 60% less compared to a standard mold. Ultimately, the cost and time it takes to create your prototype mold will vary based on the complexity of your product.
You can use a plastic prototype made using this method to perform a visual assessment. You can also use this kind of prototype for marketing validation. You might even use it to perform an ergonomic test.
SLA plastic prototypes have a smooth finish. This method works well for smaller parts to parts as big as 2 m in size. No matter the size of your product, you’ll still enjoy the same high-quality results with SLA plastic prototyping.
Injection molding enables fabricators to create a high-quality product quickly. It’s ideal for a highly limited prototype production run.
GETTING A QUOTE WITH LK-MOULD IS FREE AND SIMPLE.
FIND MORE OF OUR SERVICES:
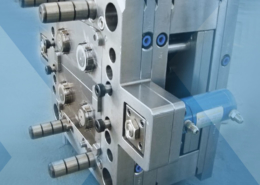
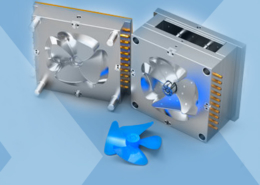
Plastic Molding

Rapid Prototyping
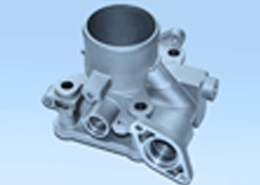
Pressure Die Casting
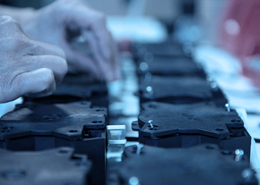
Parts Assembly
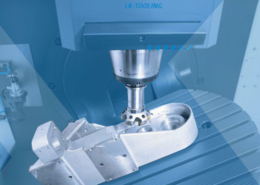