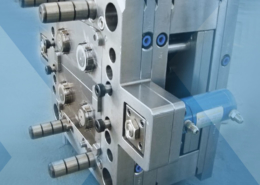
Injection-molded car components - automotive injection moulding companies
Author:gly Date: 2024-10-15
Reaction Injection Molding (RIM) During RIM, manufacturers mix liquid polyisocyanate with liquid additives (blowing agents, surfactants, catalysts, polyols, etc.), which they then inject into molds. While the urethane mixture is in the mold, it is exposed to high pressure via an impinging mixer and cured. RIM molding offers the advantages of lower tooling costs and strong and lightweight products. However, its raw materials are more expensive than other methods and it requires a higher cycle time per product.
Efficiency Urethane molding has a fast turnaround time. Polyurethane molded parts require little to no additional finishing.
If you’re in the market for molded urethane products, it’s important that you work with a reputable supplier that will understand your application needs. To find the right molded urethane provider for you, start by checking out those high-quality companies that have listed on this page. You’ll find them sandwiched in between information sections, complete with profiles and contact info. As you look through them, keep an eye out for manufacturers that offer services and products that may fit the bill. Also check out their delivery options and standard certification options, if available online. Pick out three or four to who you’d like to speak directly, and call or request a quote from each. During each conversation, discuss your specifications at length, as well as your budget, ideal timeline and delivery preferences. Make sure that if you require any certifications or safety standard adherences, they can meet get or meet those for you. Once you spoken with each contract manufacturer, compare and contrast their answers. Choose the manufacturer you believe will best serve your needs, and get to work.
Undercut features complicate and, in some cases, prevent part ejection. Get rid of them if you can, but maybe that’s not possible, if, for example, you need a side action, sliding shutoff or pick out. One alternative may be using sliding shutoffs and pass-through cores, or by changing the parting line and draft angles to provide an easier mold build. These reduce tooling costs as you avoid additional pieces to the mold that add to manufacturing costs. In addition to the rise in manufacturing costs of using hand-loaded inserts, this also may have an impact on your piece part price because of longer cycle times and manual mold operation.
Automotive Products Examples of molded urethane automotive products include: automobile seats and seat belts. While upholstered with another material, the substantial, cushion-y seat is made from injection molded urethane. In addition, polyurethane can be used for applications such as tires for trucks, due to how well it can handle compression loading.
Closed Urethane Casting Closed polyurethane molding processes, such as injection molding, involve heating the curative and pre-polymer, mixing it together, and injecting it through small holes into a closed mold cavity. Inside the mold, with the help of heat and pressure, the cast urethane cures.
Raw Polyurethane Raw polyurethane materials exist in a liquid state, as far as castable urethane is concerned. Because of this liquid state, the raw material can be easily measured and mixed and prepared for molds. Sulfur Sulfur is a slow vulcanizing agent, and is often used alongside other materials to improve the final product’s stability.
Pretty parts are nice, but they often require bead blasting, EDM, or high mold polish to achieve an elevated level of cosmetic appearance. This drives up tooling costs. Anything greater than a PM-F0 (as machined) finish requires some level of hand work, up to an SPI-A2 mirror finish using Grade #2 diamond buff. Avoid fine finishes such as these unless they’re required for the job. One thing to consider regarding cosmetics is to let Protolabs know if you need the entire half of the mold polished or maybe just one small area. You could save costs by only polishing the area needed versus the entire side of a mold. When requesting a custom finish, just send Protolabs a color-coded image of the critical areas and desired finish level for each area.
TPC, Inc. is a leader in the polyurethane molding industry. Our state-of-the-art manufacturing facilities focus on providing high-quality products, competitive pricing, and exceptional customer service. Our team of experts is dedicated to the production and innovation of our products. As a result, TPC, Inc.’s custom-fit solutions are perfected for customers of all industries.
Today, molded urethane manufacturers create products for all sorts of applications and industries. Because they have developed even more urethane varieties, they can withstand a greater variety of temperatures and environments.
Injection Molding Urethane injection molding is very similar to regular plastic injection molding. The main difference is that, instead of a liquid material, it uses thermoplastic polyurethane pellets. The pellets are placed inside a screw column where, put under high pressure and temperatures, they turn into liquid. Once liquid, the material is injected into the mold. Urethane injection molding produces high tolerance parts at high volumes. However, sometimes these products can come out low quality, with knit lines. In addition, tooling is very expensive.
If you need an electronics housing or similar box-shaped part, you can either sink the wall cavities deep into the mold base, requiring long thin tools to machine ribs into the mold, or machine the aluminum material down around the core and mold the part around it. The latter approach is known as a core cavity, and is a far more cost-effective method of molding tall walls and ribbed surfaces. Better yet, this makes it easier to provide smooth surface finishes, adequate venting, improved ejection, and can eliminate the need for super-steep draft angles.
Every quote for an injection-molded part at Protolabs is accompanied by a free design for manufacturability (DFM) analysis. This identifies potential problem areas, or opportunities for design improvement. Insufficient draft angles, “un-machinable” features, impossible geometries—these are just a few examples in which part designs can and should be improved before clicking the “accept” button. Be sure to review these suggestions thoroughly, and contact an applications engineer at Protolabs with any design-related questions.
To create a custom urethane molding for you, they can do a number of things. First, they can create a custom mold. A custom mold will ensure that your part comes out shaped and sized just how you want it. Second, they can alter your material. If your product will be made from foam, for example, they can alter it to act as rigid foam, semi-rigid foam or flexible foam. They can also put in additives that change coloring. Finally, they can engage in any number of secondary operations to create custom characteristics, like special coatings, labeling, etc. For more information of custom product design, discuss your specifications with your prospective manufacturer.
3. Polymeric Transition During the urethane molding process, the polymeric transition is completed when a curative is mixed with the pre-polymer solution.
Everyone wants to save money on manufactured parts. It sounds simple, but one of the easiest ways to reduce price-per-piece cost in injection molding is by increasing part quantity. That is because the initial upfront cost to design and machine the mold amortizes over more parts. At Protolabs, for example, up to 25,000 parts or more can be molded from the same tool.
FallLine has been a manufacturer of custom polyurethane molding products for various industries since 1981. We offer a wide range of proven materials ranging from 40A - 80D, as well as the capability to formulate materials to meet specific needs. Our knowledgeable staff, on-site design team and machine shop are dedicated to offering excellent customer service and rapid turnaround times.
Polyurethanes (PU) were first developed in 1937 by Dr. Otto Bayer and his coworkers. Finding that polyurethanes offered advantages over existing plastics, Bayer and his associates first focused on producing PU fibers and flexible foams. The use of polyurethanes quickly spread. Their first widespread application was aircraft coating during World War II. Other WWII applications included other coatings and resistant clothing.
Material Superiority Polyurethane elastomers have several laboratory-tested advantages compared to elastomers made from different materials. Polyurethane is highly resistant to radiation, ozone, oxygen, oxidation oil, tear, cut, and abrasion. Additionally, it has a greater load bearing capacity, a broader range of hardness, and is easier to color than rubber. Urethane has also been proven to resist wear and tear more effectively than some types of steel. Compared to metal, polyurethane is more resilient and more capable of reducing noise. It is highly flexible, inexpensive to fabricate, and is highly resistant to impact, corrosion, and abrasion. Polyurethane is light in weight, non-conductive, easy to mold, and doesn’t generate sparks.
Machine Products Molded polyurethane machine parts include conveyor wheels and urethane bushings. Molded urethane conveyor wheels, while more expensive than rubber conveyor wheels, are more abrasion resistant and durable than rubber wheels. Molded urethane bushings are quickly replacing rubber bushings because they hold up in situations where rubber bushings fail or wear out quickly, like: salty environments, chemical environments, high abrasion applications and oil saturated situations. In addition, urethane bushings are better at maintaining correct wheel alignment.
Open Urethane Casting During the process of open polyurethane molding, the pre-polymer and curative are heated and mixed. Next, the mixture is poured into an open mold cavity. There, the cast urethane is cured. In this case, the curing process does not involve the application of pressure.
Mass production of polyurethane foam, gum rubber and elastomers began in 1954, using toluene diisocyanate (TDI) and polyester polyols. By the late 1950s, manufacturers were producing flexible cushioning foams. During the 1960s, automotive engineers adapted one of the most common molded urethane applications we know today—automotive interior components. The first of these were safety components, like instrument and door panels. These were produced by backfilling thermoplastic skins with semi-rigid urethane foam. In 1969, Bayer (the company) presented an all-plastic car in Düsseldorf, Germany that featured certain components, like the body panels, using reaction injection molding (RIM). This was a new process that allowed them to mix urethane and reactants and then inject them into a mold for shaping. From the RIM process was soon developed reinforced RIM (RRIM), an injection molding process in which they created reinforced products with added filler (Mica, processed mineral fibers, milled glass, etc.). This process offered manufacturers added product stiffness, better thermal stability and less thermal expansion. Using RRIM, automotive manufacturers built the first American plastic-body automobile, the Pontiac Fiero, in 1983.
Tough Black (Loctite Henkel 3843) and Ceramic-Filled (BASF 3280) are two new advanced photopolymer materials now available for 3D printing.
Proto Labs, Inc. 5540 Pioneer Creek Dr. Maple Plain, MN 55359 United States P: 877-479-3680 F: 763-479-2679 E: [email protected]
1. Mold Formation In preparation for the main polyurethane molding process, manufacturers develop a silicone rubber mold (sometimes erroneously called “silicon rubber”) and a master pattern.
While injection molding may seem costly compared to processes like CNC machining and 3D printing, the ability to scale and manufacture thousands of parts makes it a cost-effective solution for mass production. Determining the cost of injection molding is a combination of several factors. The main determinant of molding cost is the amount of time it takes to produce the tooling. This means, the more complex the part's geometry, the higher your manufacturing costs will be. Simple parts, without undercuts or more advanced surface finishes, will be the most affordable.
Polyurethane The material referred to in “molded urethane” is polyurethane. Polyurethane is, generally speaking, a polymer made up of organic units joined by carbamate (urethane) links. There are many different types of polyurethane. However, most polyurethanes share the qualities of flexibility and rigidity.
At Dynatect Ro-Lab, Inc., we take pride in our expertise and specialization in polyurethane molding, offering unparalleled solutions for a myriad of applications. With our advanced capabilities, we excel in bonding urethane to diverse metal sub-surfaces, including aluminum, brass, and steel. As a team, we understand the unique demands of various industries, and our commitment to quality is reflected in our ability to seamlessly integrate polyurethane with a wide variety of metal substrates.
It is relatively easy to remove metal from an existing metal mold. Adding metal, on the other hand, can be difficult or, for all practical purposes, impossible with rapid injection molding. To look at this from the part perspective, you can add plastic, but you can’t take it away. Designing with this in mind is called “metal safe.”
Always consider part extents. In molding-speak, that means how big is the part, and will it fit comfortably in the mold while allowing for sprues, runners, ejector pins, and all the other considerations needed to make a mold work. Protolabs’ maximum part size for injection molding is currently 18.9 in. (480mm) by 29.6 in. (751mm) with a maximum depth from the parting line of 4 in. (101mm) deep. However, larger parts like these, in turn, require a larger mold. This may have an impact on your mold and part costs.
1. Eliminate undercuts 2. Get rid of unnecessary features 3. Use a core cavity approach 4. Reduce cosmetic finishes and appearances 5. Design self-mating parts 6. Modify and reuse molds 7. Pay attention to DFM analysis 8. Use a multi-cavity or family mold9. Choose on-demand production option10. Consider part size11. Use overmolding
Maybe you’re designing a snap-together case for some medical components, or two interlocking halves of a portable radio. Why build two mating parts when you can make one? Redesign the snaps so that the halves can be fit together from either direction, thus building a so-called “universal” part. Only one mold is needed, saving production expenses up front. And you can now mold twice as many of one part, instead of half the quantities of two.
Polyurethane moldings have an excellent reputation for their high performance, which is why they are so popular. Their longevity is greater than that of plastic, and they are more impact, abrasion, radiation, cold flow and low temperature resistant than rubber. They also have elastic memory, reduce noise, and resist to heat and chemicals. They possess many of the good qualities of metal, rubber, and plastics, and they are capable of forming strong adhesive bonds with most plastics and metals. Compared to most rubber materials, polyurethane has a higher resistance to petrochemicals. Polyurethane can be effectively used in casting; cast polyurethane works well with low pressure tooling and thick section molding.
Room Temperature Vulcanization (RTV) The polyurethane molding process is actually a subset of RTV. RTV often involves using materials such as polyurethanes, silicone, or wax. This process has a few benefits, including the ability to achieve an excellent surface finish and a high level of detail. Polyurethane is a popular material for this process because of its hardness and its ability to withstand temperatures up to 220F (approx. 104C). The rapid manufacturing and prototyping chemical process of RTV involves adding curatives such as sulfur in an effort to convert materials such as polyurethane into a compound that is much more durable.
Got a family of parts that all fit together? How about multiple molding projects at one time? There’s no reason to build a mold for each individual part, provided A) everything is made of the same plastic, B) each part is roughly the same size (e.g., have similar processing times), and C) can all be squeezed into the same cavity, while still allowing for proper mold functioning.
From concept, to production, to delivery, we have over 40 years experience with made-to-order cast urethane & cast polyurethane elastomer products. Weaver Industries offers urethane wheels, polyurethane molding, molded urethane, urethane sheets, & urethane/polyurethane manufacturing. Skilled at custom casting, discover the advantages of our urethane sheet and Action Mallet heads.
In addition to per-unit costs, consider the material. Many plastics overlap in strength and functionality, but some are inherently easier to mold, driving down part costs. You can experiment with different materials in the interactive quote you receive when you upload your design to Protolabs.
When designing a molded urethane part, manufacturers think about application specifications, such as: product shape, product thickness, required product characteristics (abrasion resistance, corrosion resistance, etc.), product size, product volume and standard requirements.
4. Pouring The mixture is then accelerated by pressure or heat as it is poured into a mold cavity. In this stage, coloration and other chemicals may be added for aesthetic purposes.
© Plastic Molding Manufacturers will keep your information private and secure. We will not share your email address with any third parties.
That same decade, automotive engineers replaced PVC plastisol with water-blown microcellular flexible PU foams for molding panel gaskets and air seal filters. They also developed yet another RIM process, structural RIM, also known as resin injection molding. This process involved placing glass mats into the RIM mold cavity. This allowed manufacturers to create even stiffer products.
The two main types of urethane molding are open urethane casting and closed urethane casting. Other types include: polyurethane foam molding, room temperature vulcanization (RTV), reaction injection molding (RIM) and
Our helpful design aid demonstrates part features that are too thin or too thick, bad bosses, right and wrong ribs, and other considerations to be mindful of while designing parts for injection molding.
Polyurethane urethane molding is the process used to create molded urethane parts (molded polyurethane parts). This process is used by manufacturers to fabricate a wide variety of parts and products for an equally wide range of industries, such as: athletic equipment, engineering, manufacturing, industrial, food processing, automotive, and construction. Read More...
Quality In addition, the polyurethane molding process is capable of forming parts without drafts or with undercuts. It is highly precise, is capable of working with a wide range of part sizes.
Recreational Products Examples of recreational products produced through urethane molding include: surfboards, skateboard tires, inflatable boats and high-end tennis racquet grips. Surfboards feature solid molded urethane cores, which make them light and durable. Molded urethane tires make it easier for a skateboarder to perform difficult tricks. Inflatable boats feature components made from urethane sheets. Tennis racquet grips made from molded urethane are highly stretchable, so that can create a tight, glove-like grip.
Polyurethane Foam Molding Polyurethane foam molding is a foam molding process which is frequently used by manufacturers to make soundproofing insulation. The final product is an excellent coefficient of friction, and possesses exceptional, flexibility, compression, and tension properties. Furthermore, foam urethane products are highly stable, enabling them to maintain their hardness over their entire operating lifespan.
Polyurethane Molding Manufacturers | Plastic Molding Manufacturers | Home | Privacy Policy/Terms of use | List of Companies | Sitemap
However, maybe your molding project calls for only a handful of parts. No worries. Protolabs builds cost-effective molds for production quantities as low as 25 pieces, often within a few days of ordering.
Electronic Products Molded urethane works as an excellent outer shell to electronic components of all kinds. They shield them from abrasion, mechanical stress, environmental stress and impact. Molded urethane electronic shields are effective up to 250℉.
Still another way to reduce molding costs, depending on your part volumes, is to consider on-demand manufacturing. At Protolabs, two injection molding service options are available (see table below). One is best suited for those who need smaller part quantities, usually associated with prototyping. The other option, Protolabs calls it on-demand manufacturing, is a good fit for those who require slightly larger part quantities, typically up to 10,000-plus parts from aluminum molds. On-demand production can be a great option to manage demand volatility of your parts, reduce total cost of ownership, and leverage cost-efficient bridge tooling.
Textured surfaces, molded part numbers, and company logos look cool, but be prepared to pay a bit extra for these and other non-mission critical features. That said, permanent part numbers are a requirement for many aerospace and military applications. Use a mill-friendly font such as Century Gothic Bold, Arial, or Verdana (san-serif fonts), keep it above 20 pt., and don’t go much deeper than 0.010 to 0.015 inch. Also, be prepared to increase draft if part ejection is a concern.
Some injection-molded parts go through multiple iterations until a final, workable design emerges. Instead of purchasing a new mold for every revision, a little clever planning will allow the same mold to be used multiple times. Starting with the smallest, most basic part design, mold as many pieces as needed, then re-machine the mold to include additional part features, or a larger, taller version of the same part, and mold again. This is not an exact science, but given the right part, this re-use approach can save dollars on tooling development.
This process is used by manufacturers to fabricate a wide array of moldings, parts, bowling balls, urethane bumpers, polyurethane belts, conveyor bushings, electrical potting compounds, press tool blocks, and pneumatic seals. It is especially valued for its uses in “memory foam” products. For a more in-depth look at molded polyurethane products, we can break them down into groups by industry.
Compression Molding Finally, compression molding involves using a heated mold. Manufacturers place the polyurethane inside the mold, where pressure forces the urethane to spread out and shape, then cure. Compression molding creates products with large cross sections and it can eliminate the need for secondary processing. It can, however, be expensive as well.
In addition, maybe you can join some of those parts with a living hinge? This method is a great way, for example, to mold two halves of a clamshell-style container. These parts would otherwise need a pin-type assembly to open and close. The only caveat here is that a flexible and tough material must be used, such as polypropylene (PP).
Finally, consider an overmolding option. Depending on the part, it might cost you more upfront, but could potentially save you money later. For example, overmolding a gasket on a part upfront might be an added cost, but it can save costs later from having someone install a gasket manually.
Get machined parts anodized and chromate plated with our quick-turn finishing option. Eligible materials include aluminum 6061/6082 and 7075.
Maybe you are after a higher volume of parts? You can still achieve high volumes using aluminum tooling with two-, four-, or eight-cavity molds depending on size and part geometry that can reduce your piece part price, although this would impact your tooling costs.
The RTV process is ideal in projects in which the manufacturer requires a short run of parts that must be similar in physical appearance or functional capabilities compared to parts or materials that have been previously produced.
2. Pre-Polymer Formation Once they make the mold, manufacturers mix the raw polyurethane materials so that they react and form a pre-polymer solution.
Cost Effectiveness Polyurethane molding offers lower cost tooling. Overall, it costs roughly the same as polymer molding and rubber molding.
Our digital factories create prototypes and low-volume parts fast, while our manufacturing network, offers advanced capabilities and volume pricing.
Since 1979, Uniflex has been a leading manufacturer of urethane products. We provide high-quality urethane rollers and urethane castings, as well as urethane molded products available in an array of colors. Uniflex offers customized body blocks and engine components for the automotive industry. Our team is dedicated to advancing our company and raising industry standards.
GETTING A QUOTE WITH LK-MOULD IS FREE AND SIMPLE.
FIND MORE OF OUR SERVICES:
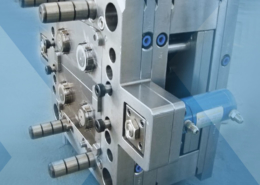
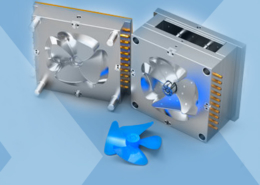
Plastic Molding

Rapid Prototyping
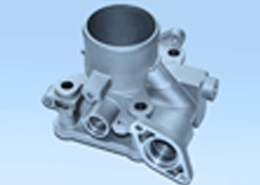
Pressure Die Casting
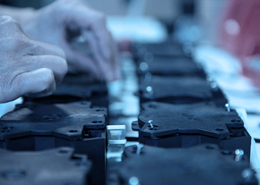
Parts Assembly
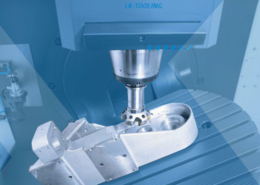