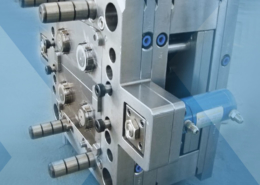
Injection Moulding with bioplastics and bio-based materials - biodegradable inje
Author:gly Date: 2024-10-15
The control panel is the brain of the machine, allowing operators to program and adjust various parameters. It enables precise control of temperature, injection speed, pressure, and cooling time, ensuring consistent product quality and efficient production. 6.Cooling System Function: The cooling system is responsible for maintaining the mould's temperature and efficiently cooling the plastic material after injection. Proper cooling is essential to prevent defects like warping and to achieve uniform product quality. 7.Safety Features Function: Safety features are designed to protect machine operators and prevent accidents. The emergency stop button provides a quick way to halt the machine in emergencies, while safety guards and interlocks ensure safe operation. Plastic injection moulding machines are complex pieces of equipment that rely on a combination of components and systems to produce high-quality plastic products. Understanding the functions of each component is crucial for achieving consistent results, minimizing defects, and ensuring operator safety. As technology continues to advance, the plastic injection moulding process becomes even more efficient and precise, making it an indispensable manufacturing method in various industries worldwide.
DEFECT IN PLASTIC INJECTION MOULDING PROCESS. INJECTION MOLD DESIGN PDT 317. DEFECT IN PLASTIC INJECTION MOULDING PROCESS. In plastic injection molding, the molded part produced are higher potential to have a plastics defects. These defects may be due to:. molds design,
Fow Mould is a highly professional custom plastic moulding manufacturer & supplier considered as the most efficient having wide moulding designs in China. This company has a great global marketing structure. There are three over sea representative offices present in USA, Russia and Egypt. Apart from that it has the import and export right in most of the countries.
a. Clamping Mechanism: This mechanism consists of a moving and stationary platen that holds the mould in place. The moving platen is driven by hydraulic or mechanical systems. b. Ejector Mechanism: After the plastic has solidified within the mould, the ejector mechanism pushes the finished product out of the mould cavity for removal. 1.Hydraulic System The hydraulic system is responsible for powering various components of the plastic injection moulding machine. It plays a crucial role in the overall functioning of the machine by providing the necessary force to: a. Actuate the clamping mechanism. b. Move the injection unit forward and backward. c. Control the speed and pressure of the plastic material injection. d. Operate the ejector mechanism. 1.Control Panel The control panel of the injection moulding machine allows operators to program and monitor various parameters throughout the manufacturing process. These parameters include: a. Temperature: The temperature of the barrel and mould is critical for ensuring proper material flow and product quality. b. Injection Pressure: Controlling the injection pressure ensures that the plastic material is injected into the mould cavity accurately. c. Injection Speed: The speed at which the plastic material is injected can influence product quality and cycle time. d. Cooling Time: Proper cooling time is essential to prevent warping and ensure the product's dimensional stability. 1.Cooling System After the plastic material has been injected into the mould cavity, it must cool and solidify before the mould can be opened and the product removed. The cooling system, typically utilizing water or oil, plays a vital role in achieving uniform cooling and maintaining the mould's temperature.
Samrat Engineers is one of the most leading manufacturers and exporters of plastic injection moulding machines in India. The plastic products which we use in our daily life are manufactured using plastic injection moulding machines.
1.Safety Features Modern plastic injection moulding machines are equipped with various safety features to protect operators and ensure efficient operation. These features may include: a. Emergency Stop: A prominent button that can immediately halt the machine's operation in case of an emergency. b. Safety Guards: Physical barriers that prevent access to hazardous machine components during operation. c. Interlocks: Mechanisms that ensure certain operations can only occur when specific conditions are met, enhancing safety. Functions of Each Component Now that we have explored the key components of a plastic injection moulding machine let's delve into their functions in more detail: 1.Injection Unit Function: The injection unit is responsible for melting the plastic material, compressing it, and injecting it into the mould cavity. The screw or plunger applies pressure to ensure the molten plastic flows smoothly and fills the mould accurately. This component's function is crucial for achieving consistent product quality. 2.Mould Cavity Function: The mould cavity defines the shape and features of the final plastic product. Its function is to hold the molten plastic material while it cools and solidifies into the desired shape. The mould's precision and quality directly impact the product's dimensional accuracy and surface finish. 3.Clamping Unit Function: The clamping unit's primary function is to securely close the mould and maintain that closure during the injection and cooling phases. It ensures that the mould cavity remains sealed under high pressure, preventing any plastic leakage. 4.Hydraulic System Function: The hydraulic system powers the machine's moving parts, such as the clamping unit and injection unit. It provides the necessary force to operate these components, allowing for precise control over the injection process's speed and pressure. 5.Control Panel Function:
We are a responsible China plastic injection molding supplier and plastic mould making company and have rich experience in supplying custom plastic injection molding service for many years. Our production sites have been accredited with the certification of TS16949, ISO 14001 and ISO 9001, etc. You can fully trust our production sites, products and place your orders. Click the right side plastic mould manufacturer video to know more about HanKing Mould plastic mould making capabilities. And Welcome to make an enquiry to us!
We are manufacturer and supplier of Injection Plastic Moulding and moulded components. The moulds we manufacture is with high quality mould steels and high quality reputed standard parts. We do the design manufacture of moulds and production of the moulded components in-house. Using latest softwares and high accuracy machines with highly experienced tool engineers. For More Information Please Contact us: - 0253-6601173 / 0253-6521272 Visit us: http://ekvira.in/injection-mould.html
We are specializes in all aspects of Plastic Injection Moulding Machinery in Tamilnadu, Chennai and Injection Molding Machine Tamilnadu offer reliable quality.
Moulding-injection.com is one of the leading Manufacturer of plastic injection molds. We have extensive know-how in plastic injection molding in Belgium based on more than 30 years of experience. Buy your molds directly from the Moulding-injection at factory price. To know more, visit us today.
Injection moulding. 120061910 Hamada s. El-Turk. Types of Plastic Processing. Injection Moulding – Usually for thermoplastics. Molten plastics are injected under pressure into a mould. The mould surface detail (profile of the product) can be accurately reproduced.
HanKing Mould Enginering Ltd. started the china custom plastic mold business in the year of 1996 as a plastic mold manufacturer China in the line of the plastic injection mold and precision molded plastics in Longgang, Shenzhen, China. With continuous developments and progresses, HanKing Mould has become a professional mould manufacturer offering custom injection mold design services, plastic moluld project management services, plastic mold manufacturing services, mold trial services, quality control plastic injection moulding services, and semi-finished & finished plastic molds assembly services.
Ayush platics is the one and only certified and leader of Plastic injection moulding machine manufacturers in india, if you want to buy one for you, dont hazitate to send us quote or visit to our website: http://www.ayushplastics.com/
Injection Moulding is a manufacturing process for producing parts in large volumes. It is most typically used in mass-production processes where the same part is being created thousands or even millions of times in succession. Injection Moulding Services File Formats Supported: 2D parts: DWG, PDF / 3D parts: IGES, IGS, STEP, STP, XT. Take a look at the work process. Our one-stop-shop prototyping services include Rapid Prototyping, CNC Machining, SLA/SLS 3D printing, Low volume production, rapid tooling, sheet metal, Injection molding and die casting. https://e-make.co/plastic-injection-molding-company/ or call us at ( 86)75527209712
PVC injection machine: kamhan industrial ltd is the leading provider of various types of machines. The PVC injection machine is manufactured in the supervision of the specialist. Our machines are available at very cheap prices.
These days, we are using almost all our daily life using components that are made up of plastic. Plastic has become one of the most sought after materials to use because of its easy availability and mass production.
Injection Moulding Technology. Part 3. Quality. Session aim. To improve the delegates understanding of quality issues, relating to injection moulding and how the process can be optimised and monitored. Session objectives. By the end of the session you will be able to:.
Primex Plastics Pvt.Ltd. is one of the leading Auto part manufacturer ,Injection & Insert molded components. These components are supplied to leading OEMs and their Tier 1 suppliers with end use in Automotive, electrical, Furniture, White Goods and other Industries. We are an ISO/TS 16949 certified company, promoted by technocrats having two decades of technical and managerial experience in the field of Plastics and Sheet Metal component manufacturing.
INJECTION MOULDING. INJECTION MOULDING. Merupakan proses cetak tekan Yaitu : Pelet dimasukkan ke dlm hopper utk dicairkan Cairan kemudian didorong utk diinjeksikan ke dalam suatu cetakan (mold). INJECTION MOULDING. INJECTION MOULDING.
ADJUSTABLE TABLE TOP FOR INJECTION MOULDING MACHINE. Presented by, rahul k.h ramesh.m sajal k.a shajeer m.k
INJECTION MOULDING. Historical Background. A single-action hydraulic injection machine was designed in the U.S.A. in 1870 by Hyatt Heating-cylinder design was first recognised in a patent issued to Adam Gastron in 1932.
Plastic injection molding is considered to be a versatile method of creating products and parts. It is known to be the most preferred method because it carries numerous advantages that any other method of plastic molding. For more information: http://www.haishi-machinery.com/
https://www.plasticmold.net/injection-molding-cost/ China professional Injection Mold Making manufacturer and plastic molding suppliers. SINCERE TECH precision plastic Injection Mold supplies our customers with high quality mould making, reasonable price, fast delivery and good service to ensure our timely pace of entering into the market of new mold products by means of advanced technic and rich throughput, our good business cooperation with customes from USA, Canada, Russia, Australia, Japan, Southeast and North Africa countries has laid a solid foundation for our large market share.
Mingli Precision Steel Molds Manufacturer specialized in insert molding, over molding, 2 shot molding, bi-injection, peek injection and peek parts manufacturing.
Plastic Injection Moulding Machine Components And Its Functions Plastic injection moulding is a versatile manufacturing process used in various industries to produce a wide range of plastic products. This process involves melting plastic material and injecting it into a mould to create a desired shape. To achieve precise and efficient results, plastic injection moulding machines consist of several essential components, each with its unique function. In this comprehensive guide, we will delve into the core components of a plastic injection moulding machine and their respective functions, providing valuable insights into this crucial industrial process. 1.Injection Unit The injection unit is the heart of a plastic injection moulding machine. Its primary function is to melt and deliver the plastic material into the mould cavity. The key components within the injection unit include: a. Hopper: The hopper stores and feeds the raw plastic material into the machine. The material is typically in the form of pellets or granules. b. Barrel: Inside the barrel, the plastic material is heated and mixed using a screw or plunger. This process is essential for melting and homogenizing the plastic. c. Screw or Plunger: The screw or plunger is responsible for pushing the molten plastic material into the mould. The choice between a screw or plunger depends on the specific machine design and requirements. 1.Mould Cavity The mould cavity is where the plastic material is injected to create the desired shape of the final product. Moulds are typically made from high-quality materials such as steel or aluminum to withstand the high pressures and temperatures during the injection process. The mould cavity's design directly impacts the final product's dimensions and quality. 1.Clamping Unit The clamping unit's primary function is to securely hold the mould in place during the injection process. It exerts a tremendous amount of force to keep the mould closed while the plastic material is injected. The key components within the clamping unit include:
http://www.plastemart.com/used-plastic-machine/used-injection-moulding-machines-(160-tons-to-250-tons)/1070 Find top dealers of small injection moulding machines, used injection molding machine & other injection molding application on sale in 150 to 250 tons capacity.
Automation helps the plastic injection moulding manufacturers Malaysia to scale back manufacturing costs because the overheads are significantly reduced. For more visit:-https://gscorp.com.my/capabilities/injection-moulding/
Following the concept of customer first, HanKing Mould dedicates to being a trustworthy China plastic mould manufacturer by designing and manufacturing plastic injection molds, providing custom plastic molding manufacturing and services according to every individual's requirements. Hanking Mould's successes are ensured by strict management capability, professional technical knowledge, advanced plastic tooling equipment, and highly-recognized injection molding services. We are pursuing better quality and technical capability to meet the demands of increasing plastic mould manufacturing markets.
GETTING A QUOTE WITH LK-MOULD IS FREE AND SIMPLE.
FIND MORE OF OUR SERVICES:
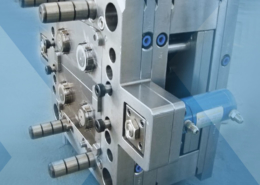
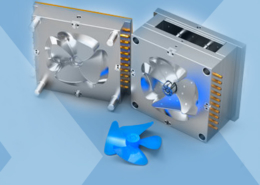
Plastic Molding

Rapid Prototyping
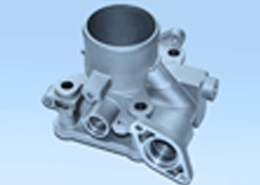
Pressure Die Casting
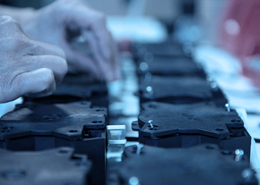
Parts Assembly
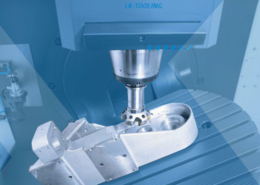