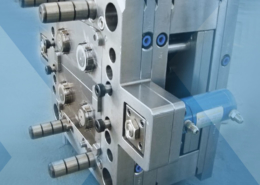
Injection Moulding Repair Service and Maintenance - plastic injection service
Author:gly Date: 2024-10-15
LLDPE and HDPE use the same basic process during rotational molding. First, powdered plastic or plastic pellets are added to a metal mold. Next, the tool is rotated and heated so that the polyethylene softens to the point that it begins to coat the inside of the mold. While rotating, the tool is then cooled so that the plastic solidifies. Finally, the mold is opened and the rotomolded part is removed.
Some businesses go so far as to hire overseas companies. But what they may recover in labor costs is overshadowed by the slow responsiveness of the contracted custom plastics company, as well as costly delays in shipping and delivery.
From the start, Streamline offers tremendous value, starting with the design phase. Many custom plastic parts get bogged down during this critical step. Streamline Plastics is eager to contribute during the design phase. We’re capable of taking your very basic napkin sketches and converting them into 3D models to the production of custom plastic molds.
Producing custom molded plastics can be costly, particularly when done in-house. Many manufacturers contract out to custom plastic molding companies, entrusting them with either all or simply a portion of the assembly process.
LLDPE has medium stiffness and high tensile strength, the maximum stress a material can withstand while being pulled or stretched before breaking. This polymer is durable but forgiving, and virgin LLDPE provides resistance to chemicals and environmental stress cracking. For outdoor applications, LLDPE can be enhanced with UV stabilizers and with anti-fungal or anti-microbial additives.
Streamline plastics manufactures the custom molded plastics expected from a leading plastic parts company. We offer plastic injection molding and insert plastic molding tailored to solve your custom plastic mold challenges. Contact a Streamline Plastics representative to receive a quote for your latest molding project.
As a third-generation, family-owned business, our American-owned company stakes its reputation on a commitment to quality, customer service, and continuous improvement.
Streamline offers a full 3D CAD (computer-assisted design)/CAM (computer-assisted manufacturing) linked to SolidWorks modeling software. We can move seamlessly from mold design to the production of custom-molded plastic parts. Our 40,000-sq. ft. facility is capable of a complete lights-out, fully automated operation.
Applications for rotomolded LLDPE include plastic tanks, buckets, bins, containers, toys, and outdoor recreational products and equipment. Because LLDPE can be blended with pigments, designers can achieve specific colors without parts painting.
Gregstrom provides LLDPE and HDPE rotational molding that adds value to your projects. For over 75 years, we’ve been the Made in USA plastics manufacturer that more customers trust. In addition to rotomolding, we offer design assistance, tooling, robotic and CNC finishing, assembly and testing, and quality assurance. To get started with polyethylene rotational molding, contact us.
Streamline Plastics provides cost-effective custom injection-molded plastics without sacrificing quality or responsiveness. You can trust us with all or part of a project, from the design phase all the way to packaging and shipping. We are a true turnkey operation with much to offer:
For nearly 70 years, Gregstrom Corporation has been building lasting relationships with partners in industries like yours.
Our highly-experienced personnel follow an SPC (statistical process control) system to maintain the highest standards of performance. Our team is capable of building high-production custom plastic molds and provides quick responses when mold repair and maintenance become necessary. Combined with our efficient equipment, we can complete your job and have it properly packaged and delivered well within schedule.
Polyethylene rotational molding can use either linear low-density polyethylene (LLDPE) or high-density polyethylene (HDPE) to produce strong, hollow parts for indoor and outdoor applications. LLDPE and HDPE are similar in terms of chemical composition but have some important differences when it comes to performance properties. This Q&A from Gregstrom examines these two rotomolding materials.
High-density polyethylene (HDPE) can support complex designs and large rotomolded products, such as those used by the food processing industry. Special HDPE grades can meet FDA and USDA requirements. Because of its performance properties, HDPE is a better choice for some plastic tanks and for products such as boat docks and underground vessels.
HDPE has high tensile strength but is stiffer than LLDPE. In addition, HDPE has a slightly higher strength-to-density ratio. HDPE plastic is lightweight, impact-resistant, withstands most chemical solvents, and is non-leaching. Like LDPE, this form of polyethylene supports the addition of UV stabilizers and anti-fungal or anti-microbial additives.
Thankfully, domestic plastic mold manufacturers have sought to alleviate these challenges by providing streamlined processes, reducing costs while also providing the responsiveness and timeliness that businesses depend on.
GETTING A QUOTE WITH LK-MOULD IS FREE AND SIMPLE.
FIND MORE OF OUR SERVICES:
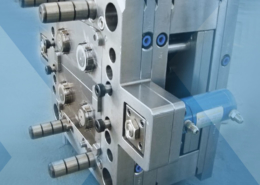
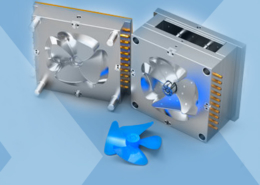
Plastic Molding

Rapid Prototyping
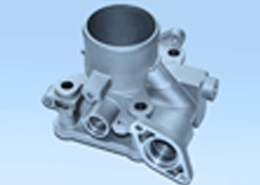
Pressure Die Casting
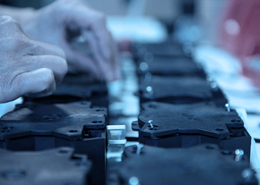
Parts Assembly
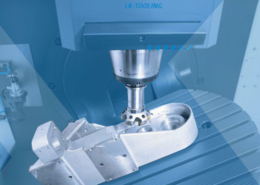