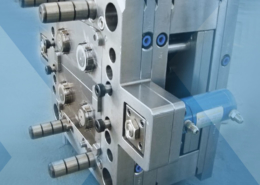
Injection Moulding | Polyethylene - polyethylene moulding
Author:gly Date: 2024-10-15
It is often found in strong mechanical parts, casings, snap-fit closures, and threaded inserts. Nylon is also used to make things like toothbrushes, medical implants, and electrical connectors.
Polystyrene (PS) is a commodity plastic and is known to be a brittle material. However, it can be compounded with additives such as butadiene rubber to improve its dimensional stability.
However, it contains BPA, so this plastic cannot be used for food preparation or storage applications. It is also expensive to mold and does not offer scratch resistance.
However, acrylic won’t absorb odors, can become easily stained by greases and oils, and they scratch more readily. They also have a service temperature that’s too low for them to be used in industrial applications. They tend to stress crack under especially heavy loads, too.
However, it is more rigid and hard than TPE. It may be too hard for some injection molded parts. It also comes with a high price tag — and drying is required before injection molding, making the process expensive.
HDPE and LDPE plastics share the same high chemical and moisture resistance but differ in terms of hardness, optical transparency, melting point, flexibility, etc. These plastics are generally chosen for their good clarity.
Polymethyl methacrylate, better known as PMMA or simply acrylic, is a strong and clear thermoplastic that allows plenty of light to pass through.
All prices are in USD Copyright 2024 JACOBS MOLD & MACHINE. Sitemap | Shopping Cart Software by BigCommerce
TPE is most often used to make footwear, medical equipment (such as breathing tubes and valves), auto components (such as weather seals), and pet products.
PS can be either opaque or have glass-like clarity, depending on which type of PS you choose. PS is also well-suited for injection molding projects, as it has a predictable and uniform shrink rate. They are also inexpensive, lightweight, and resistant to moisture and bacteria growth — making them a cost-effective material for certain applications.
The good news is that there are thousands of resins to choose from with similar – but not identical – properties, so you have many potential materials to choose from. So, to help you refine your search, we’ve prepared a short guide on the most common injection molding materials. Read on!
Because of these qualities, they are suitable for products like bearings, gears, pulley wheels, fasteners, lock systems, conveyor belts, and high-performance engineering components.
However, they are limited by poor sunlight resistance and poor resistance to high temperatures. HDPE also tends to be difficult to mold in thinner dimensions. LDPE, on the other hand, struggles to meet close tolerances. PET also absorbs too much water — requiring longer resin drying during production.
If the down payment option is selected an email will be sent to you when the machine is completed. Then select the final payment option and the machine will be shipped to you. You will receive two invoices/receipts for the down/final payment option. Shipping charges are added in the final payment option.
Acrylic plastics have high tensile strength, so they can be load-bearing. They are also lightweight, and shatter-resistant, making them a good alternative for glass. Lastly, they are resistant to sunlight and weather, so they can be used outdoors.
The two heat controllers are used to control and monitor the plastic temperature in each heating pot. A temperature difference of up to 30 F between the pots is obtainable.
However, unlike acrylic, this resin lacks strong resistance to sunlight or weather — making it a poor choice for outdoor products. ABS also creates plenty of smoke when burnt, and has poor resistance to friction and water.
ABS is an engineering thermoplastic. It is an opaque and sturdy material. It’s best known for its enhanced strength and impact resistance.
Results will vary when injecting laminate two colors baits depending on the mold layout.I can guarantee that two full streams of plastisol of different colors will flow out of the nozzle of this machine, but I can not guarantee how the plastisol will flow inside a mold. Every mold may fill out differently and those variances will have to be processed out with temperature and PSI adjustments to achieve your desired results.
You can find ABS plastics used to make things like keyboard keys, plastic enclosures for outlets, protective headgear, and the like. It is also commonly used in automotive, consumer goods, sports equipment, and industrial fitting applications.
Nylon has a few advantages, however, such as high toughness, heat resistance, abrasion resistance, fatigue resistance, and noise dampening qualities. It’s also a good choice for high friction products.
The plastic can be heated directly inside the machine. Colorants and additives can also be added to the plastic in the machine.
The benefits of this plastic are that it is tough, inexpensive, and has good resistance to heat, grease, acids, and alkalis. It also has a shiny finish.
However, it does not have flame resistance — so it may burn quickly if not treated with a fire retardant. It also degrades easily under sunlight, but again, a UV stabilizer additive can be used to improve performance.
Lastly, TPU: a type of thermoplastic elastomer. Similar to TPE, it has a rubber-like elasticity but is more durable. As a result, it is a good replacement for hard rubber materials.
Also known as Nylon, this is a synthetic polyimide that can be challenging to work with in injection molding, as it is prone to shrinkage, which results in an inadequate filling.
PS is often used for medical, optical, and electrical products. With additives, PS is a good option for appliances and equipment.
These are built when ordered, lead time is normally one to two weeks and will include everything needed to operate when delivered. (excluding an air compressor) Just plug in & play. Payment options are available. See below for more information
PP applications include a variety of consumer, commercial and industrial products, including storage containers, plastic packaging, appliance components, and power tool bodies.
We often get asked which plastic resins are the best choice for a client’s project. To answer it simply — there is no one answer for that. For each application, we can come up with suggested plastic materials, from which we choose one that works for you and your unique circumstances.
Also known as acetal, this is an engineering plastic that is typically recommended for parts that need low friction, high stiffness, and excellent integrity. This is because they have a good crystalline structure. POM resins are also naturally opaque, and white.
PC plastics are tough resins, with similar properties to acrylic. However, PCs are more resilient over a wider temperature range. It also holds pigment well over time.
The initial heat up time is 20 minutes (slightly longer when full of plastisol) and will maintain an operational temperature indefinitely after the initial heating time.
PE plastics are usually used to make things like milk bottles, water bottles, children’s toys, electronic wire, and some medical device components.
You can also explore your material selection process with a trusted plastic injection molding company in China, like Richfields! Our team is always ready to collaborate with you on your plastic project — message us here, and we can help you find the perfect resin to suit your unique project needs.
The downside to them is that they are susceptible to creep, which is when a solid material deforms permanently. TPE may also lose its rubber-like properties at higher temperatures. This material is also more expensive, compared to other plastic resins.
Common uses for acrylics are in window panels, greenhouses, solar panels, and other transparent materials for architectural and lighting projects.
To save time, preheat the next batch of plastic in a presto pot or microwave and pour in the melting pots. Color change time will be less than 5 minutes by doing this.
However, PP is extremely degradable under UV light and is also very flammable. When burnt, it produces gasses that are harmful to humans. PP is also difficult to bond, hence it is difficult to paint — but pigments can be added to change color.
PE is the most commonly used plastic in the world. It comes in three main types: high density (HDPE), low density (LDPE), and polyethylene terephthalate (PET).
TPE applications include footwear, automotive components (such as gaskets), sporting goods, enclosures for electronics, and medical devices. In some cases, they can be used to replace PVC.
However, mold shrinkage is high for POM resins, and they cannot resist UV rays in sunlight. They also cannot be fire-rated to safety standards.
PP plastics feature good chemical resistance, a high melting point, and resistance to torsion and bending. They are also resistant to water, so they won’t degrade. It is also recyclable up to four times.
When used in injection molding, POM features excellent rigidity with thermal stability and low friction generation. It also has low water retention and good chemical resistance.
This brief overview of common injection molding materials covers some of the key characteristics of these resins, which should help you narrow your list of possible material options.
TPE, also known as thermoplastic rubber (TPR), is a blend of plastic and rubber. It performs like rubber but is processed like plastic. It offers elasticity, which allows it to be stretched without losing its original shape. It also has shorter molding cycles, which makes TPE an easy and inexpensive option compared to liquid silicone rubbers.
PC plastics are very durable, and up to 250 times stronger than glass. It also has a very predictable and uniform shrinkage rate, so it’s good for projects that need precise dimensional control. It is also lightweight and has good optical properties.
The melting pots are cleaned by being drained completely and then wiped out with cloth wrapped on a wood dowel rod. The pots must be hot. It only takes a few minutes.
This machine has two separate melting pots and a nozzle that connects both which allows you to work with two colors, singly or simultaneously. Injecting laminate two color baits is possible.For use with vinyl plastisol only. (Standard soft plastic bait material)
The downside to PS is that it is flammable, not UV ray resistant, and will degrade when exposed to hydrocarbon solvents such as benzene and kerosene. And, due to its brittleness, it is prone to cracking. It is also a non-biodegradable plastic.
Polypropylene (PP) is the second most common plastic material in the world. It has similar properties to polyethylene (PE) but has slightly improved hardness and heat resistance. It also has the lowest density — though that can be changed with the use of fillers.
Unlike TPE, TPU performs better under extreme temperatures and has enhanced chemical resistance. It also has better resistance to loads, abrasion, chemicals, and grease.
GETTING A QUOTE WITH LK-MOULD IS FREE AND SIMPLE.
FIND MORE OF OUR SERVICES:
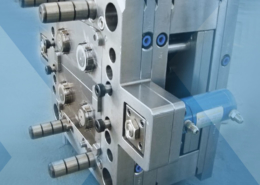
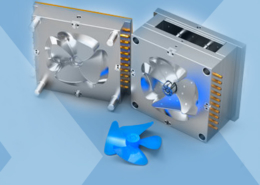
Plastic Molding

Rapid Prototyping
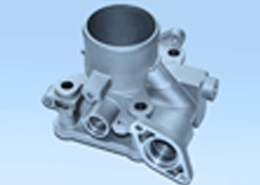
Pressure Die Casting
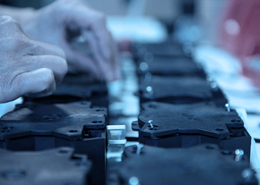
Parts Assembly
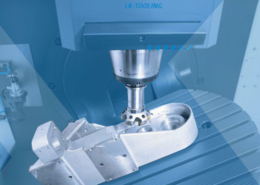