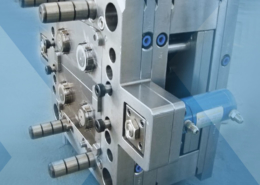
Injection moulding part design for dummies... - injection moulding for dummies
Author:gly Date: 2024-10-15
All of these prerequisites are critical in determining the success of the project and preventing any injection molding issues that will lead to failure. If you already have a prototype for the mold, our experts at Richfields Plastics can help you optimize it better, achieve part success, and come up with a final plastic part that meets your satisfaction. Read on to learn more.
Due to rapid growth in the business, the company was required to upscale its production capacity by 2x in a short span of time
Karkhana.io provided quick scaling of operations by manufacturing this fixture (Quantity – 700 components) by leveraging available capacities on 60+ CNC machines at our vetted suppliers while managing quality and timely delivery at all locations
Looking to collaborate with us? Click here to get in touch with us now! You may also view our list of products and services here, as well as, our list of available equipment.
One effective cost-saving strategy for Polystyrene (PS) in injection molding involves optimizing the design of molds and part geometry. By employing advanced mold design techniques, such as incorporating uniform wall thickness, minimizing undercuts, and reducing the number of intricate features, manufacturers can significantly lower material consumption, cycle times, and overall production costs. Streamlining part designs to eliminate unnecessary details and ensuring uniform wall thickness not only reduces the amount of PS required but also results in shorter cooling times, faster cycle rates, and improved part quality. Additionally, utilizing materials with higher flow rates and incorporating efficient gating and runner systems can further enhance production efficiency, ultimately leading to substantial savings in PS usage and operational expenses.
However, don’t let these figures discourage you — although they may seem costly initially, you also have to take into account the lifecycle of the product. Some manufacturers may promise cheap molds, but the downside is that they may not necessarily be capable of achieving tight tolerances and high-quality parts.
Richfields Plastics has been the forefront in the mass-production of large size plastic injection molds. For several decades, our molding company in China has been delivering only the best and most reliable solutions for different finished plastic parts.
In any large plastic injection molding project, the customer has to look at the molding firm’s capabilities. Do they have the right machinery to produce the molds? Can they provide insights regarding the success of the mold? Will they be able to achieve tight part tolerances? Asking all of these questions is important because you ultimately want to choose a molding company in China that can offer you the right mold designs at a reasonable value/price range.
At Richfields Plastics, we not only guarantee high-quality steel or hardened steel molds — we also ensure that you’re getting what you pay for. We will be able to provide you with an estimate based on the kind of features that you need for the final part. Do you need basic, advanced, or intermediate rapid prototyping or insert tooling? Simply tell us what you want your mold to look like and we will undertake the necessary prerequisites and pre-design procedures that can transform your initial mold design into reality.
Each mold is cut to size, according to your industrial preferences. Using only the finest and highest grade raw alloy/metal materials out there, our molds are designed to last for several decades, with only minimal maintenance required.
At Richfields, our time-testing large plastic molding solutions have allowed us to cater to different industries. Aside from specializing in small plastic consumer goods, such as safety products, we also work with clients in the fields of automotive, industrial, petrochemical, food & beverage, and many more.
The prices for our large size injection molding services rival that of our competitors. Mold tooling for large plastic parts can be expensive, depending on the size, raw materials, repair costs, and other requirements. In fact, even just a single-cavity mold may cost anywhere between $1,000 and $5,000. Family or multi-cavity molds on the other hand, may fetch for more than 70 times the price — at $80,000.
Due to rapid growth in the business, the company was required to upscale its production capacity by 2x in a short span of time
Our flexibility means that we can create large size mold prototypes for virtually all kinds of product assembly. We have served a number of car manufacturers, for example, in designing high-quality car bumpers that exceed safety standards and regulations in the industry. Using specialty resins, reinforced plastics, and other types of rubbers, we have been able to mass produce different bumper designs that fit well with the rest of the vehicle.
As the name suggests, large size plastic injection molds are molds that are capable of creating large plastic parts — whether it be customized, or OEM-grade goods (Original Equipment Manufacturer).
Looking for a molding company in China that can produce large size plastic injection molds? Here at Richfields Plastics, we have all the capabilities to provide you molding solutions ideal for large designs. Whether it’s for an automotive component, construction part, or any plastic mold that’s bigger than your typical molded product, our well-developed business model and team of resin experts can help you out.
Central to any large size plastic injection mold-making process is the equipment. At Richfields Plastics, our factory houses multiple units of CNC, EDM, wire cut EDM, lathe, gun drilling, and drilling machines to fabricate high-quality molds made out of steel.
Karkhana.io provided quick scaling of operations by manufacturing this fixture (Quantity – 700 components) by leveraging available capacities on 60+ CNC machines at our vetted suppliers while managing quality and timely delivery at all locations
Polystyrene (PS) is a versatile and widely used thermoplastic polymer characterized by its transparent or translucent appearance, low cost, and lightweight nature. It is composed of a linear chain of styrene monomers and can be produced in various forms, including solid, foamed, and expanded varieties. PS exhibits excellent electrical insulating properties, making it suitable for applications in electronics and packaging. Its low thermal conductivity, however, makes it less suited for high-temperature environments. PS boasts a good combination of mechanical properties, with high tensile strength and impact resistance, while maintaining ease of processing, such as injection molding and extrusion. Its glass transition temperature is around 100°C, and it exhibits a relatively low melting point of approximately 240°C. PS is susceptible to UV degradation, which may lead to brittleness and yellowing over time, thus necessitating the addition of stabilizers for outdoor applications. Moreover, PS is highly recyclable, contributing to its sustainability in the plastics industry. Overall, Polystyrene’s unique combination of properties makes it a valuable material in a wide range of consumer and industrial applications, from food packaging and disposable utensils to insulation and consumer electronics casings.
Due to rapid growth in the business, the company was required to upscale its production capacity by 2x in a short span of time
Karkhana.io provided quick scaling of operations by manufacturing this fixture (Quantity – 700 components) by leveraging available capacities on 60+ CNC machines at our vetted suppliers while managing quality and timely delivery at all locations
Aside from the automotive sector, we’ve also been able to produce a number of designs for electronic products, industrial storage systems, tools, and sports equipment. Versatile, dependable, and matured — our large size mold manufacturing operations continue to offer value and reliability to all our customers and professional clients.
Due to rapid growth in the business, the company was required to upscale its production capacity by 2x in a short span of time
Due to rapid growth in the business, the company was required to upscale its production capacity by 2x in a short span of time
Designing large size molds is not something that every molding company can achieve. A contributing factor to this is the machinery, expertise, and process requirements. For example, crafting molds for large size plastic products needs to undergo proper mold flow analysis to ensure that the resin will reach the mold cavities. Manufacturers may also conduct various testing methods to ensure quality of the mold.
Karkhana.io provided quick scaling of operations by manufacturing this fixture (Quantity – 700 components) by leveraging available capacities on 60+ CNC machines at our vetted suppliers while managing quality and timely delivery at all locations
Due to rapid growth in the business, the company was required to upscale its production capacity by 2x in a short span of time
Karkhana.io provided quick scaling of operations by manufacturing this fixture (Quantity – 700 components) by leveraging available capacities on 60+ CNC machines at our vetted suppliers while managing quality and timely delivery at all locations
Polystyrene is sensitive to cooling rates, so ensure the mold has sufficient cooling channels to maintain a uniform cooling rate across the part. This helps prevent differential shrinkage and ensures dimensional stability. Adequate cooling also reduces the likelihood of part distortion and warpage. Additionally, when designing parts with PS, consider using ribs and gussets to increase stiffness and reduce the risk of flexing or bending. Uniform wall thickness is also essential to maintain part quality and prevent sink marks.
Karkhana.io provided quick scaling of operations by manufacturing this fixture (Quantity – 700 components) by leveraging available capacities on 60+ CNC machines at our vetted suppliers while managing quality and timely delivery at all locations
Typically, any large size plastic mold can be classified according to weight — this could range from 50 tons to as much as 2,100 tons, depending on machine availability. With this in mind, you have to make sure that you partner with a leading molding firm like us. Here at Richfields Plastics, our mature supply chain and capacity to provide large size molds to various industries make us the go-to large size mold manufacturer. Our flexibility, price competitiveness, and commitment to industrial plastic molding quality remains unparalleled in the industry.
GETTING A QUOTE WITH LK-MOULD IS FREE AND SIMPLE.
FIND MORE OF OUR SERVICES:
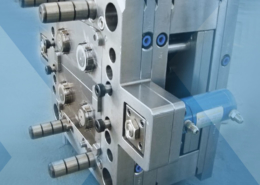
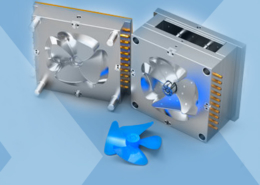
Plastic Molding

Rapid Prototyping
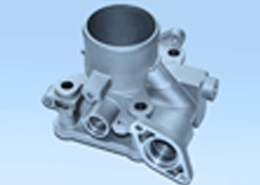
Pressure Die Casting
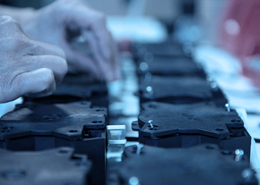
Parts Assembly
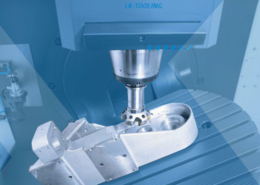