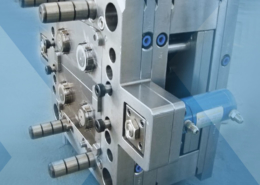
Unveiling the Intricacies of Injection Molding
Author:gly Date: 2024-06-08
Introduction:
Injection molding, an indispensable manufacturing process, lies at the heart of countless products that shape our daily lives. From the plastic casing of your smartphone to the intricate components of your car, injection molding plays a pivotal role in bringing these items to fruition. This article aims to delve into the depths of injection molding, unraveling its complexities, exploring its applications, and shedding light on its significance in the modern industrial landscape.
Understanding Injection Molding:
Process Overview:
Injection molding involves the injection of molten material, typically plastic, into a mold cavity, where it solidifies to form the desired shape. The process begins with the heating of raw materials, followed by the injection of the liquefied material into the mold under high pressure. Once cooled and solidified, the finished product is ejected from the mold, ready for further processing or assembly.
Materials Used:
A wide range of thermoplastic and thermosetting materials can be used in injection molding, each offering unique properties and characteristics. Common materials include polyethylene, polypropylene, polystyrene, and polyvinyl chloride (PVC), chosen based on factors such as durability, flexibility, and heat resistance. Material selection is crucial in determining the performance and functionality of the final product.
Equipment and Machinery:
Injection molding machines come in various sizes and configurations, ranging from small desktop units to large-scale industrial presses. These machines consist of a hopper, where raw materials are fed into a heating chamber, an injection unit, which melts and injects the material into the mold, and a clamping unit, which holds the mold in place during the injection process. Advanced technologies, such as computer numerical control (CNC) and robotics, enhance precision and automation in the manufacturing process.
Applications and Industries:
Automotive Sector:
Injection molding is widely utilized in the automotive industry for the production of interior and exterior components, such as dashboards, bumpers, and door panels. The ability to produce lightweight, yet durable parts with intricate designs makes injection molding an ideal choice for enhancing vehicle aesthetics and performance.
Consumer Electronics:
In the realm of consumer electronics, injection molding is instrumental in manufacturing casings, enclosures, and housings for devices such as smartphones, laptops, and home appliances. The seamless integration of components and the ability to achieve precise tolerances ensure the functionality and aesthetic appeal of electronic products.
Medical Devices:
Injection molding plays a critical role in the production of medical devices and equipment, including syringes, IV components, and surgical instruments. The strict regulatory requirements and stringent quality standards of the medical industry demand precision and consistency, making injection molding the preferred manufacturing method for ensuring product reliability and safety.
Challenges and Future Directions:
Environmental Impact:
Despite its numerous benefits, injection molding poses environmental challenges, particularly regarding plastic waste and pollution. As society increasingly prioritizes sustainability, there is a growing need for eco-friendly materials and recycling initiatives to mitigate the environmental impact of injection molding processes.
Technological Advancements:
The future of injection molding lies in technological innovations aimed at enhancing efficiency, reducing cycle times, and improving product quality. Advancements in materials science, automation, and digitalization are poised to revolutionize the injection molding industry, paving the way for new possibilities and applications.
Conclusion:
In conclusion, injection molding stands as a cornerstone of modern manufacturing, driving innovation and progress across various industries. From automotive to electronics to healthcare, the applications of injection molding are vast and diverse, shaping the products we interact with on a daily basis. As we navigate towards a more sustainable future, addressing challenges such as plastic waste and embracing technological advancements will be key in unlocking the full potential of injection molding and ushering in a new era of manufacturing excellence.
GETTING A QUOTE WITH LK-MOULD IS FREE AND SIMPLE.
FIND MORE OF OUR SERVICES:
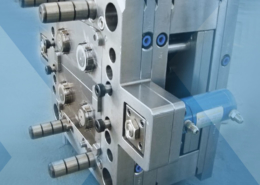
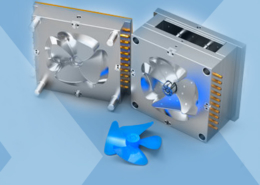
Plastic Molding

Rapid Prototyping
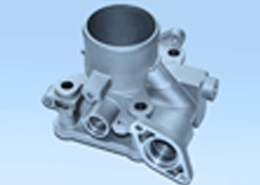
Pressure Die Casting
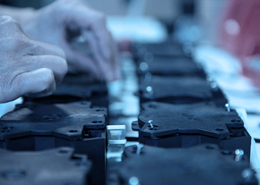
Parts Assembly
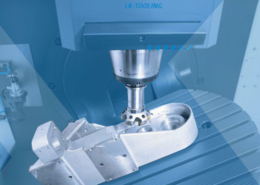