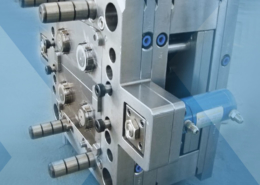
Injection Moulding Businesses for Sale - injection moulding business for sale
Author:gly Date: 2024-10-15
Over molding is effectively the use of layering effects in polymer application techniques. This process is centered around the use of a liquidous resin to add additional layers of shape and structure to an existing component. An example of such a resin could be a polymer that has been heated to a temperature just above its glass transition temperature). The existing component to which the resin is being added is often injection molded as well, and may be near its own glass transition temperature. This process works well when layers with varying geometric profiles are desired around a central "core" structure.[2]
Topics: Plastic Injection Molding Defects, Plastic Types, Quality, Texture, Choosing the right plastic injection molder
AIM Processing is an experienced American manufacturer specializing in custom injection molding services and multi-material molding solutions. An ISO 9001:2015 registered domestic manufacturer based in the Denver, Colorado region, our company is committed to uncompromising quality, consistency, and responsive customer service.
Multi-material injection molding has become increasingly popular across many different product applications, allowing us to create complex plastic products which take advantage of more than one material. For example, on handheld products, handles, and grips, we can use a much sturdier base material overmolded with a soft, ergonomic plastic to drastically improve comfort and the overall end user experience.
Also referred to as sequential injection molding,[4] multi-shot injection molding refers to creation of multiple layers relative to the starting axis of the initial mold. In other words, the warm, heated materials are inserted into the mold in a very specific sequence one after another. This creates a layering effect between materials while maintaining relatively high-energy interactions at material boundaries. This is important because it implies that the inter-layer bonds are stronger in many cases than when the layers are applied to a previously cooled part, as is more closely the case of over molding. While there are other applications, this operation is preferred when varying molds (different geometries) are desired between material layers.[2]
Each MMM primary subset can also be further subdivided into secondary and tertiary subsets, and even further in some cases.[4] This can be advantageous when fine tuning or other general calibration of a specific MMM process is desired. Each primary subset is outlined further in the following sections.
If the desired object is manufacturable using MMM, it is definitely best to use MMM over traditional injection molding. Some of the key features that makes MMM a better approach are:
Essentially, multi-material molding services let us combine multiple optimized plastics in a single molding product. There are three primary methods for multi-material injection molding, which we discuss below along with some of the advantages of each.Of course, choosing the most suitable method depends on the specific application requirements, material compatibility, and production considerations. Get in touch with the experts at AIM Processing and we’ll help you choose the most efficient, cost-effective method for your unique products.
Also referred to as co-injection molding,[4] multi-component injection molding describes insertion of multiple viscous materials injected simultaneously, as opposed to placing one material as an additional layer relative to another. In other words, it creates a sandwich-like structure where both materials mold around each other as dissimilar liquids, and exist in such a state at the same time. Relative to the part center, materials can be injected concentrically using the same mold/gate, or regionally using gates at different locations.[2]
Multi-material injection molding (MMM) is the process of molding two or more different materials into one plastic part at one time.[1] As is the case in traditional injection molding, multi material injection molding uses materials that are at or near their melting point so that the semi-liquidous (viscous) material can fill voids and cavities within a pre-machined mold, thus taking on the desired shape of designed tooling. In general, advantages of MMM over other production techniques include, but are not limited to, creating parts that have an elastic modulus that varies with location on the part (different regional polymer hardness), creating a single-structure part with different regional materials (similar to the previous advantage, but more focused on joining different types of polymers like rubber and plastic), and also creating a single part with multiple independent polymer colors. Applications range from simple household items like a toothbrush to more heavy duty construction of items like power tools.[2]
Plastic overmolding services are widely used for combining materials with disparate properties – such as hard and soft plastics, or metal and plastic combinations. The primary advantage with overmolding is the ability to create products with improved ergonomic features, enhanced aesthetics, and optimized strength for the given application.From consumer electronics and mobile devices to automotive interiors and hand tools, overmolding is an extremely popular method for enhancing molded products for comfort, usability, and longevity. Plastic overmolding is essentially the two-shot molding operation, but completed in two separate molding runs: the first for the substrate material, the second for the secondary material. While this method still requires two tools, they are typically of a reduced cost & complexity when compared to two-shot molding.
GETTING A QUOTE WITH LK-MOULD IS FREE AND SIMPLE.
FIND MORE OF OUR SERVICES:
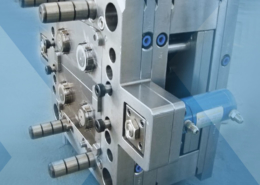
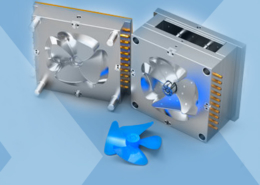
Plastic Molding

Rapid Prototyping
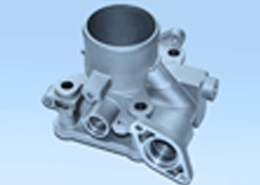
Pressure Die Casting
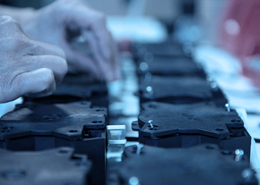
Parts Assembly
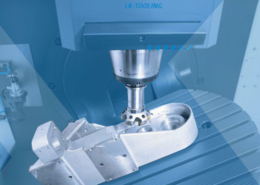