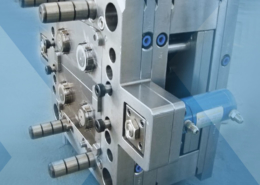
Injection Moulding Businesses for Sale - injection molding business for sale
Author:gly Date: 2024-10-15
technotrans says climate protection, energy efficiency and customization will be key discussion topics at PTXPO as it displays its protemp flow 6 ultrasonic eco and the teco cs 90t 9.1 TCUs.
When designing the EOAT to incorporate the charging applicator, a few guidelines should be considered to assure optimum label charging. For example, if the emitters are to be placed 1 in. behind the label, any metal parts of the EOAT should be grounded and at least 1.5 in. away from the emitters. Metal any closer than this will attract some of the electric field from the charging applicator, resulting in less charge on the label.
Implementing a production monitoring system as the foundation of a ‘smart factory’ is about integrating people with new technology as much as it is about integrating machines and computers. Here are tips from a company that has gone through the process.
Applying a static charge to hold the label in the injection mold eliminates the need for vacuum ports that addsignificantly to the cost of making and maintaining the tool.
At Thogus, we understand the demands of the medical device industry and can advise you on the regulatory requirements, validation processes, and material selection for your medical plastic injection molding project. We have the experience to provide support during each phase of a project’s life cycle; from our manufacturing by design process to selecting materials capable of withstanding harsh conditions to cleanroom assembly, we are here to help you succeed.
This CW Tech Days virtual event will explore the technologies, materials and strategies used by composites manufacturers working in the evolving space market. Presentations from industry experts will emphasize the use of composite materials in applications requiring the weight savings, structural benefits and ability to withstand extreme temperatures that only composites can provide.
Fig. 3—Simplified electrostatic IML approach for flat containers places the remote charging applicator in a fixed position where the robot passes it on the way to the mold.
Applying a static charge to hold the label in the injection mold eliminates the need for vacuum ports that addsignificantly to the cost of making and maintaining the tool. While the in-mold labeling (IML) pro cess for injection molding has been around for over 25 years, interest has snowballed in the last two. Applying the label during molding eliminates a secondary step for pad or screen printing or label application, as well as corona or flame treating. More important, the end result is permanent. This makes it especially attractive for product-liability and instructional information, as well as UPC codes, logos, and decoration. IML is also cleaner and more sanitary because there’s less handling of the product. And recyclability is enhanced if the label material is the same as that of the molded part.
In the U.S., IML is used on toys, office supplies, power tools, and lawn mowers. Interest is growing for food packaging, on which IML is used in Europe. (Photo: Plastics Technology)
Sustainability continues to dominate new additives technology, but upping performance is also evident. Most of the new additives have been targeted to commodity resins and particularly polyolefins.
Although some injection molders have attempted to charge the label and place it in the die manually, experience has shown this to be a labor-intensive and unreliable approach that also slows down the press cycle.
The fixture on the EOAT requires a grounded conductor such as a metal plate. The conductive surface should be at least as large as the label and mounted 0.25 to 0.5 in. directly behind the label. The suction cups should have the minimum diameter necessary to provide sufficient holding power to prevent the label from slipping and attracting to the grounded conductive surface of the fixture.
The physical and electrical characteristics of the label are extremely important to the reliability of using static charges to adhere the label to the mold. The surface of the label that is to contact the mold cavity must be a good insulator to accept and maintain the static charge. Ideally, this surface should have a resistivity of 1012 ohms/sq or greater. The higher the resistivity, the better the label will accept the charge without bleeding the charge to ground when it contacts the metal mold cavity. If the charge is not maintained when in contact with the die, adhesion is lost and the label slips from the intended position. Measurement of the label’s resistivity can be performed using a commercially available surface resistivity meter.
Thousands of people visit our Supplier Guide every day to source equipment and materials. Get in front of them with a free company profile.
Plastics Technology covers technical and business Information for Plastics Processors in Injection Molding, Extrusion, Blow Molding, Plastic Additives, Compounding, Plastic Materials, and Resin Pricing. About Us
Use of a remote-mounted charging applicator is a simplified way to apply a charge. It requires little modification of the EOAT, is relatively easy to set up, and can satisfy the requirements of many different sizes and shapes of labels with the same charging applicator.
Founded in 1950, Thogus is an established, family-owned custom plastic injection molder and contract manufacturer headquartered in Avon Lake, Ohio.
Some of the newer electrostatic power supplies contain arc-sensing circuitry designed to protect the solid-state components of the power supply when it is used with a non-current-limited applicator. If excessive current draw is sensed by the power supply, its control circuitry immediately goes into arc-protection shutdown mode, which turns off the high-voltage output to protect the power supply’s sensitive electronics. When this happens, static charging is interrupted. That can be a common and troublesome occurrence when non-current-limited applicators are used.
August 29-30 in Minneapolis all things injection molding and moldmaking will be happening at the Hyatt Regency — check out who’s speaking on what topics today.
The use of vacuum appears to be most advantageous when the shape of the molded product requires complex preformed labels or when the molded part and/or label is required to have a textured surface.
In this collection, which is part one of a series representing some of John’s finest work, we present you with five articles that we think you will refer to time and again as you look to solve problems, cut cycle times and improve the quality of the parts you mold.
While prices moved up for three of the five commodity resins, there was potential for a flat trajectory for the rest of the third quarter.
Mike Sepe has authored more than 25 ANTEC papers and more than 250 articles illustrating the importance of this interdisciplanary approach. In this collection, we present some of his best work during the years he has been contributing for Plastics Technology Magazine.
Plastics Technology Top Shops Benchmarking Survey provided both unanimous responses and divided results, but pervasive throughout is the sense of an industry still grappling with the aftermath of 2020’s global pandemic.
Join Wittmann for an engaging webinar on the transformative impact of manufacturing execution systems (MES) in the plastic injection molding industry. Discover how MES enhances production efficiency, quality control and real-time monitoring while also reducing downtime. It will explore the integration of MES with existing systems, emphasizing compliance and traceability for automotive and medical sectors. Learn about the latest advancements in IoT and AI technologies and how they drive innovation and continuous improvement in MES. Agenda: Overview of MES benefits What is MES? Definition, role and brief history Historical perspective and evolution Longevity and analytics Connectivity: importance, standards and integration Advantages of MES: efficiency, real-time data, traceability and cost savings Emerging technologies: IoT and AI in MES
The Plastics Industry Association (PLASTICS) has released final figures for NPE2024: The Plastics Show (May 6-10; Orlando) that officially make it the largest ever NPE in several key metrics.
Mold maintenance is critical, and with this collection of content we’ve bundled some of the very best advice we’ve published on repairing, maintaining, evaluating and even hanging molds on injection molding machines.
In a time where sustainability is no longer just a buzzword, the food and beverage packaging industry is required to be at the forefront of this innovation. By adopting circular packaging processes and solutions, producers can meet regulatory requirements while also satisfying consumer demand and enhancing brand reputation. Join Husky to learn more about the broader implications of the circular economy — as well as how leading brands are leveraging this opportunity to reduce costs, increase design flexibility and boost product differentiation. Agenda: The cost and operational benefits of embracing circularity Key materials in circular packaging — including rPET and emerging bioplastics How to design a circular food and beverage package Strategies for selecting sustainable closures to future-proof packaging solutions Optimization and streamlining of production processes for enhanced efficiency How Husky Technologies can enable your sustainable success
Although incorporating the charging applicator(s) on the EOAT offers a high degree of reliability and repeatability, it presents somewhat of a challenge for the designer of the EOAT. The applicator may be a straight static-charging bar of some specified length having a row of emitter pins, or it may be a series of individual emitter modules. The style and number of applicators required depends upon the size and shape of the label and contours of the die surface where the label is to be placed. Therefore, each EOAT will require its own unique charging applicator set-up.
This 1-day technical conference and exhibition showcases innovative developments in materials, processing and equipment for the additive manufacturing industry. This conference is specifically designed to inform, update and educate plastic processors about implementing new additive manufacturing technologies. Hear technical presentations on the newest advances in additive manufacturing related to: design, materials development, processing equipment and enabling technologies, new applications and more. See exhibits from engineering plastic suppliers, compounders, molders, design and engineering firms and machinery suppliers. Experts will show you how to apply the latest technologies to your next project or program. The conference includes a full day of technical presentations, plenary and keynote presentations on business trends; breakfast, lunch and breaks; exhibits of advanced technologies and an evening networking reception. Note: Additive Manufacturing Media executive editor Stephanie Hendrixson will moderate the Supporting AM Adoption in Northeast Ohio panel at 11:20 a.m.
All conductive components of the robot fixture must be grounded and should have radiused edges and corners. There should be no sharp edges or corners within 1 in. of the label.
Ultradent's entry of its Umbrella cheek retractor took home the awards for Technical Sophistication and Achievement in Economics and Efficiency at PTXPO.
In some cases, the label may not release readily from the suction cups and may skew slightly due to mutual electrostatic attraction caused by static charges building on the surfaces of the suction cups. If this occurs, a static neutralizer bar can be mounted in the robot’s path between the charging bar and the label magazine. Each time the robot returns to pick up a new label, the suction cups will be neutralized. Smaller diameter suction cups will decrease the charged surface area, which may help minimize the problem.
Use of electrostatics in the IML process offers cost and reliability benefits by eliminating the need for vacuum in the die. When a static charge is placed on a label of suitable material and construction, the label will be attracted electrostatically to the grounded metal surface of the die and may stick with excellent adhesion for up to several minutes.
In this collection of content, we provide expert advice on welding from some of the leading authorities in the field, with tips on such matters as controls, as well as insights on how to solve common problems in welding.
Although there are numerous ins and outs of IML technology, one of the most important considerations is how the label is held in place in the injection molding tool. In many applications, electrostatics offers a reliable and cost-effective alternative to the use of vacuum for holding the label in its proper location in the die. This approach can provide distinct benefits to the molder as well as the molder’s customer and the end user.
The suction cups are incorporated into the foam material and should be flush with the surface (Fig. 3). Since the foam pad has a high electrical resistance compared with the grounded metal mold surface, the charged label has a greater affinity for the mold and transfers from the foam pad to the mold when the vacuum is switched off. Figure 4 is an example of how this may be accomplished for 360° labels on round containers.
The healthcare industry depends on medical parts and devices using medical-grade plastic injection molding that is durable, reliable, and meets regulations.
A word of caution: A charged foil or conductive layer will most likely discharge in the form of an arc as it approaches the mold surface. A result of this arcing is RFI, which may cause problems with microprocessor controls, especially if unshielded sensors or cables are nearby. Ongoing arcing over a long period of time may also produce pits on the die cavity.
Despite price increase nominations going into second quarter, it appeared there was potential for generally flat pricing with the exception of a major downward correction for PP.
A textured label or die surface can also result in poor adhesion due to the reduction in intimate surface contact between the label and die surface.
While the major correction in PP prices was finally underway, generally stable pricing was anticipated for the other four commodity resins.
In this three-part collection, veteran molder and moldmaker Jim Fattori brings to bear his 40+ years of on-the-job experience and provides molders his “from the trenches” perspective on on the why, where and how of venting injection molds. Take the trial-and-error out of the molding venting process.
Coverage of single-use plastics can be both misleading and demoralizing. Here are 10 tips for changing the perception of the plastics industry at your company and in your community.
This Knowledge Center provides an overview of the considerations needed to understand the purchase, operation, and maintenance of a process cooling system.
In this collection of articles, two of the industry’s foremost authorities on screw design — Jim Frankand and Mark Spalding — offer their sage advice on screw design...what works, what doesn’t, and what to look for when things start going wrong.
In this charging process, the robot picks up the label at the magazine, orients the label, and passes it by the charging bar. The ground reference surface behind the label attracts the electric field from the charging bar and the label becomes charged. The robot places the label in position against the surface of the molding die, releases the vacuum to the suction cups, and the label stays in place on the surface of the die.
A relatively thin, non-textured label with good dielectric properties on a non-textured die surface will produce the best adhesion. However, there are still other important adhesion factors to consider, such as molding temperature, polymer compatibility with the label, gate location, and material flow when the die is injected. For all these reasons, much time and frustration can be eliminated by consulting a label supplier with IML experience.
In addition, it is very important that the robot does not miss the label. Injecting the mold without a label in place can result in very time-consuming and costly downtime to remove the die and clean out all the vacuum ports and passages. To prevent this requires a means of detecting the vacuum and stopping injection of the polymer into the die.
Across all process types, sustainability was a big theme at NPE2024. But there was plenty to see in automation and artificial intelligence as well.
Join KraussMaffei for an insightful webinar designed for industry professionals, engineers and anyone interested in the manufacturing processes of PVC pipes. This session will provide a comprehensive understanding of the technology behind the production of high-quality PVC pipes: from raw material preparation to final product testing. Agenda: Introduction to PVC extrusion: overview of the basic principles of PVC pipe extrusion — including the process of melting and shaping PVC resin into pipe forms Equipment and machinery: detailed explanation of the key equipment involved — such as extruders, dies and cooling systems — and their roles in the extrusion process Process parameters: insight into the critical process parameters like temperature, pressure and cooling rates that influence the quality and consistency of the final PVC pipes Energy efficiency: examination of ways to save material and energy use when extruding PVC pipe products
Second quarter started with price hikes in PE and the four volume engineering resins, but relatively stable pricing was largely expected by the quarter’s end.
Learn about sustainable scrap reprocessing—this resource offers a deep dive into everything from granulator types and options, to service tips, videos and technical articles.
Join this webinar to explore the transformative benefits of retrofitting your existing injection molding machines (IMMs). Engel will guide you through upgrading your equipment to enhance monitoring, control and adaptability — all while integrating digital technologies. You'll learn about the latest trends in IMM retrofitting (including Euromap interfaces and plasticizing retrofits) and discover how to future-proof your machines for a competitive edge. With insights from industry experts, it'll walk you through the decision-making process, ensuring you make informed choices that drive your business forward. Agenda: Maximize the value of your current IMMs through strategic retrofitting Learn how to integrate digital technologies to enhance monitoring and control Explore the benefits of Euromap interfaces and plasticizing retrofits Understand how retrofitting can help meet new product demands and improve adaptability Discover how Engel can support your retrofitting needs, from free consultations to execution
A global player in optical inline quality control, Pixargus is intensifying presence in U.S. & Asia under CiTex umbrella.
Join Engel in exploring the future of battery molding technology. Discover advancements in thermoplastic composites for battery housings, innovative automation solutions and the latest in large-tonnage equipment designed for e-mobility — all with a focus on cost-efficient solutions. Agenda: Learn about cutting-edge thermoplastic composites for durable, sustainable and cost-efficient battery housings Explore advanced automation concepts for efficient and scalable production See the latest large-tonnage equipment and technology innovations for e-mobility solutions
After successfully introducing a combined conference for moldmakers and injection molders in 2022, Plastics Technology and MoldMaking Technology are once again joining forces for a tooling/molding two-for-one.
As another safety precaution, the high-voltage cable from the charging applicators to the power supply must be supported along the robot arm with sufficient slack to allow for the required movement with the least physical stress on the cable. These cables should be inspected on a weekly basis and replaced if fracture, abrasion, or weakness of the cable is detected.
If conductive inks, coatings, or foil laminations are used, they must be on the back side of the label, opposite the surface that is to contact the mold. In such a case, the best method for charging the label is with the charging applicator external to the press (the simplified charging method) and the conductive surface of the label against the vacuum ports on the EOAT. If the charging applicator is mounted on the EOAT behind the label, the high-voltage field cannot penetrate the conductive layer and sufficient charge will not be applied to the surface that is to contact the mold cavity.
More than four years on, there are aspects of the COVID-19 pandemic that linger in their impacts to the plastics market and are made visible in our annual survey.
With your patients’ health and lives on the line, medical practitioners need reliable, high-quality devices and equipment. We have collaborated with healthcare professionals for decades to develop and manufacture plastic injection molding for medical parts and devices for a variety of applications, including:
Discover how artifical intelligence is revolutionizing plastics processing. Hear from industry experts on the future impact of AI on your operations and envision a fully interconnected plant.
A hard arc is a high-current arc-over, usually seen as a distinct bright white or yellow spark from the high-voltage emitter of the charging applicator to a conductive surface, such as the cavity of the metal mold. This can occur when a non-current-limited applicator is positioned too close to the mold or when its operating voltage is set too high. The high-voltage energy from the applicator’s emitter breaks down the insulation properties of the air between the emitter and the grounded metal surface of the mold, causing the arc. Such arcs can cause pits in the die surface and radio-frequency interference (RFI) that may affect microprocessor controls of the robot or the press.
This month’s resin pricing report includes PT’s quarterly check-in on select engineering resins, including nylon 6 and 66.
In the electrostatic process, the robot picks up the label from the magazine with suction. A high static charge is placed on the label either as the EOAT with the label approaches the press or as the label approaches the die surface. The robot positions the label, releases the vacuum, and the label is transferred to the surface of the die. No vacuum in the die nor adhesive on the label is needed (see Fig 1).
With this approach, a charging applicator bar is mounted on a permanent fixture between the molding press and the label magazine. The charging power supply can be turned on manually and left on during the duration of the run, or it can be turned on and off remotely by the robot’s PLC.
Positioned as a recyclable packaging alternative to traditional BOPET films, BOPE-HD film is now available from companies such as Inteplast, JK Materials, Oben Group, and Polivouga.
Introduced by Zeiger and Spark Industries at the PTXPO, the nozzle is designed for maximum heat transfer and uniformity with a continuous taper for self cleaning.
There are five specific areas that designers and manufacturers need to consider to realize the potential of these unique materials.
Multiple speakers at Molding 2023 will address the ways simulation can impact material substitution decisions, process profitability and simplification of mold design.
Plastics Technology’s Tech Days is back! Every Tuesday in October, a series of five online presentations will be given by industry supplier around the following topics: Injection Molding — New Technologies, Efficiencies Film Extrusion — New Technologies, Efficiencies Upstream/Downstream Operations Injection Molding — Sustainability Extrusion — Compounding Coming out of NPE2024, PT identified a variety of topics, technologies and trends that are driving and shaping the evolution of plastic products manufacturing — from recycling/recyclability and energy optimization to AI-based process control and automation implementation. PT Tech Days is designed to provide a robust, curated, accessible platform through which plastics professionals can explore these trends, have direct access to subject-matter experts and develop strategies for applying solutions in their operations.
Label properties such as thickness, curl, and surface texture also affect adhesion. For example, a relatively thick label that may have some curl due to an asymmetrical laminated structure or improper storage may break loose from a flat die surface if the electrostatic forces are unable to overcome the physical forces causing the label to curl. Similarly, preformed labels may be required for compatibility with contoured die surfaces.
While the label is being held by the suction cups on the EOAT, the charging applicators are located directly behind the label (Fig. 2). The emitter pins typically face the back of the label from a distance of about 1 in. When the robot places the label against the die surface, the charging power supply is turned on for a period of about 0.5 to 2 sec. This places a static charge on the label and the label instantly adheres to the grounded metal die. The vacuum is turned off and the robot extracts the EOAT from the press.
Fig. 4—Simplified electrostatic IML for round containers requires rotating the mandrel holding the label to get overall charge coverage. Antistatic foam provides good support and easy release of label.
Plastic injection molding is a growing, cost-effective method of manufacturing medical devices and parts. Along with its ability to produce complex designs that meet the stringent cleanliness requirements, medical-grade plastic injection molding offers high tensile strength as well as chemical and high-temperature tolerances. Since its inception, medical devices that are manufacturing with injection-molded plastic have contributed to a reduction in medical costs and increased patient safety.
Designing and machining the die to incorporate vacuum can add significant cost to the tooling. Next, the label must be substantial enough to prevent it from being sucked into the vacuum ports, causing a deformed image or “pimples” on the surface of the finished product. Vacuum passages in the molding die may also result in non-uniform die temperatures.
What are the basic building blocks of plastics and how do they affect the processing of that material and its potential applications in the real world? Meet the repeat unit.
Gifted with extraordinary technical know how and an authoritative yet plain English writing style, in this collection of articles Fattori offers his insights on a variety of molding-related topics that are bound to make your days on the production floor go a little bit better.
Take a deep dive into all of the various aspects of part quoting to ensure you’ve got all the bases—as in costs—covered before preparing your customer’s quote for services.
In many cases, decreasing the discharge temperature will improve product quality and perhaps even boost rate. Here are ways to do it.
Another version of the simplified method provides even better physical support and uniform transfer of the label from the EOAT to the die. This process functions the same as described above but requires the addition of a piece of antistatic foam mat bonded to the metal ground reference plate on the EOAT. This material should have a thickness of approximately 0.375 in. and should have an electrical surface and volume resistivity of approximately 109 to 1010 ohms. This type of material is available from most static-control distributors who service the circuit-board assembly industry. Most of these materials are manufactured with an embossed textured surface and may require sanding to achieve a smooth, uniform surface. Sanding the surface also enhances charging of the label.
Currier Plastics had a major stake in small hotel amenity bottles until state legislators banned them. Here’s how Currier adapted to that challenge.
Mixed in among thought leaders from leading suppliers to injection molders and mold makers at the 2023 Molding and MoldMaking conferences will be molders and toolmakers themselves.
A label can be held in the desired location in the mold by specially designed and machined vacuum ports. The sequence is as follows: A robot picks up the label from a magazine, places it in the proper position in the die, the vacuum is turned on, and the mold is shot.
Fig. 1—Mandrel with suction cups embedded in antistatic foam (left) rotates to pick up label from magazine while static charge is applied to the label. Mandrel inserts label into mold (right), where label is attracted to grounded tool. Vacuum is shut off, and mandrel retracts.
Exhibitors and presenters at the plastics show emphasized 3D printing as a complement and aid to more traditional production processes.
Resin drying is a crucial, but often-misunderstood area. This collection includes details on why and what you need to dry, how to specify a dryer, and best practices.
Formnext Chicago is an industrial additive manufacturing expo taking place April 8-10, 2025 at McCormick Place in Chicago, Illinois. Formnext Chicago is the second in a series of Formnext events in the U.S. being produced by Mesago Messe Frankfurt, AMT – The Association For Manufacturing Technology, and Gardner Business Media (our publisher).
In contrast, the current-limited applicator’s resistor limits the amount of current that can be drawn from the emitter, thereby preventing a high-voltage arc.
Equipment suppliers’ latest innovations exemplify this trend driven by factors such as labor shortages, higher-speed thermoformers and tighter quality control.
When, how, what and why to automate — leading robotics suppliers and forward-thinking moldmakers will share their insights on automating manufacturing at collocated event.
If individual emitters are to be mounted on a plate that also holds the vacuum suckers, the plate must be made of a nonconductive material such as polyethylene, PTFE, PVC, UHMW-PE, or acrylic. Any component of the EOAT close to the charging applicator should be made of a nonconductive material, if that can be done without sacrificing strength and structural integrity. Any component that is electrically conductive (metal) must be grounded.
AIM Processing has parlayed small part molding expertise and aggressive automation, even for short run production, into a highly successful custom molding business.
Two types of charging applicator are available: current-limited and non-current-limited. Current-limited types come in the straight static-bar style or as individual emitter modules. They contain a resistor that is in series with the high-voltage supply. The advantage is that this applicator will not “hard arc” if it gets too close to the metal and offers a high degree of safety if personnel should accidentally touch it while energized.
An overview on the use of chemical foaming agents (CFAs) to successfully foam single and multilayered rotational molding parts, this webinar will illustrate the multiple benefits rotational molders can achieve, including reducing resin consumption, decreasing part weight, enhancing wall thickness and improving structural rigidity. Agenda: Charging the mold Dosing ratios Venting Optimal decomposition temperatures, cycle times and drop times for drop box applications Cooling considerations
GETTING A QUOTE WITH LK-MOULD IS FREE AND SIMPLE.
FIND MORE OF OUR SERVICES:
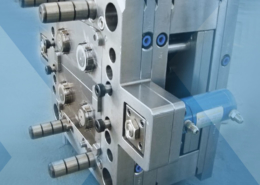
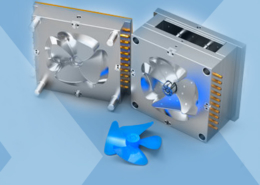
Plastic Molding

Rapid Prototyping
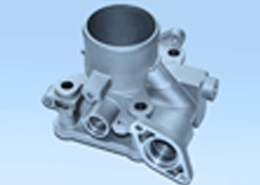
Pressure Die Casting
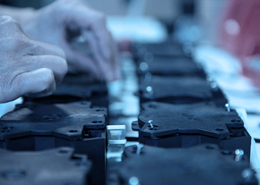
Parts Assembly
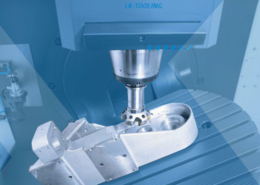