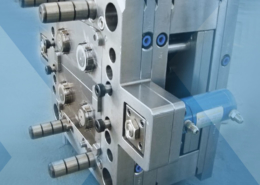
Injection Moulding Basics | UNSW Making - plastic injection mold maker
Author:gly Date: 2024-10-15
All information about AKF Plastics at a glance. What we do, what we stand for and how we can help you with your injection moulding challenges.
[fts_instagram instagram_id=2578666033 access_token=2578666033.da06fb6.85629cf5365f45a08a2a9ea6ebfbb8c6 pics_count=3 type=user profile_wrap=no popup=no super_gallery=yes columns=1 force_columns=no space_between_photos=1px icon_size=65px hide_date_likes_comments=no]
AKF Plastics is not only focused on the use of materials that are superior in quality and durability, but also on the use of materials that provide the best aesthetic results.
In injection molding, the plastic starts in pellet or granule form. It is dropped into a hopper where it is fed into a barrel. Inside the barrel, the plastic pellets melt and are fed towards the mold. Inside the mold, the molten plastic is cooled with either a cooling tower or chilled water. This process of cooling water is fed through many small channels within the mold.
Our mission is to create the best possible injection moulding solutions for plastics for industrial customers, in the most economically, technically and socially responsible manner.
There is also a decision to be made between using cooling tower water or chilled water. While cooling tower water has a lower initial cost and operating cost, the water can become contaminated since it is an open loop (open to the environment). The chilled water from an air cooled chiller, on the other hand, is a closed system, so your molds are protected from possible debris and contaminants.
AKF Plastics is your ideal partner for injection moulded automotive parts . We specialise in the injection moulding of plastic auto parts in short-runs, and large plastic parts in larger volumes, for many companies within the automotive industry. We offer the expertise, experience and quality to be able to offer you the most reliable plastic car parts and applications.
We are a reliable automotive injection moulding partner for the production of the most diverse assignments for interior components. AKF Plastics Netherlands therefore has everything to meet the dynamic and challenging needs of today’s automotive industry. These are some examples of our moulded solutions:
AKF/AGF Injection Moulding Naarden, The Netherlands © ALL RIGHTS RESERVED | BTW: NL807854992B01 | Privacy & Cookies | Webdesign door Brainycloud Marketing ©
As the cooling water travels through the mold, it removes heat from the plastic, hardening it. When the cycle is complete, the mold opens and ejects the finished product. Inside these molds, plastic can be formed into a variety of shapes. You could make a garbage can, drinking cup, plastic fork, or even a computer case.
AKF Plastics is not only focused on the use of materials that are superior in quality and durability, but also on the use of materials that provide the best aesthetic results. We therefore only use decorative techniques to meet the aesthetic requirements of the automotive industry.
It is a tricky balance between the temperature of your cooling water, the quality of your plastic and profitability. If you chill the plastic too cold, it causes defects. But the faster it’s cooled and ejected from the mold, the more product that can be produced and more profit that can be made.
Do you have a question about materials, injection moulding or a specific automotive product? We are always ready to help you! Contact us via the contact form or call: +31 (0)35 694 5545
There are a variety of plastics processing methods that require a plastics chiller. Whether it’s injection molding (the most common), extrusion, blow molding, lamination, or other types, these processes make a multitude of items we use in our everyday lives. For simplicity, we will only concentrate on one of these methods today. Because injection molding is the most common process, we will discuss this type of industrial HVAC product.
Original Equipment ManufacturerAutomotive industryAerospace Building and ConstructionPlastic injection Moulds Machinery PoolAS 9100
For example, we have injection moulding machines that can deliver up to 1600 tons of closing force, and a shot weight up to 10,900 grams.
Injection moulding is also ideal for the production of complex products consisting of several components or even several materials!
Injection moulding is our specialisation. Since the 1930s, AKF Plastics is focused on injection moulding solutions for a wide range of industries. We work not only professionally, but also economically, technically, and with social responsibility. We offer complete solutions as a supplier within the automotive industry.
Looking for capacity for the production of your car parts? Do you want to know what we can do for your automotive production? Or do you have a challenge and are you looking for an experienced sparring partner?
Our services are designed for established companies with significant buying power, capable of investing in molds and committing to substantial annual injection molding volumes. We aim to partner with enterprises that can leverage our capabilities for large projects and established markets.
At AKF Plastics, we specialize in providing comprehensive injection molding solutions exclusively for large-scale national and international enterprises. Our fully automated 24/7 production lines, extensive logistics capabilities, and large storage facilities ensure we can meet the demanding needs of our clients.
At AKF Plastics, we have a proven track record in delivering comprehensive solutions for various industries, including aerospace, construction, machinery and equipment manufacturing, the automotive sector, and many others. Our services encompass everything from design and mold development to production and logistics. With decades of experience, we offer speed and efficiency, resulting in competitive pricing and fast turnaround times. Our innovative strategy, Contingency Production™ Planning, ensures uninterrupted production even in uncertain market conditions. Whether you are active in aviation, construction, machinery, automotive, or any other sector, AKF Plastics guarantees reliability, quality, and innovation for all your plastic needs.
For more information on plastics injection molding chiller systems, contact us online, call us at 281.540.2805 or visit our rental cooling equipment page.
The process, however, is simple. Feed the plastic into the hopper. It melts in the barrel. Travels to the mold where it is cooled and then ejected. Then the process starts all over again. Lather, rinse, repeat. Check out the video below to see an injection molding chiller in action.
AKF Plastics Netherlands can meet the most complex product requirements and is happy to work along with you to translate your needs into the highest quality injection moulding solutions, in accordance with the international standards that apply within the automotive/car industry.
At the molding machines, a small unit called a thermolator, or temperature controller, helps to regulate the temperature of the cooling water going to the mold. While a single cooling tower or chiller can cool many molding machines, a thermolator is required at each machine. Since precise control to the molds is critical, these units are important to the overall process as well.
Would you like to know more about our services and the injection moulding of automotive parts?Please contact us without obligation. We are happy to help.
AKF Plastics Netherlands is characterized within the automotive industry by the use of innovative materials and production processes. This enables us to produce injection moulded car parts that match the character of the automotive industry of the future.
GETTING A QUOTE WITH LK-MOULD IS FREE AND SIMPLE.
FIND MORE OF OUR SERVICES:
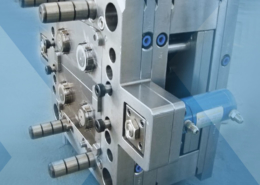
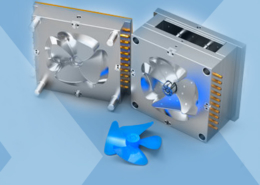
Plastic Molding

Rapid Prototyping
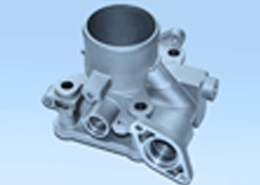
Pressure Die Casting
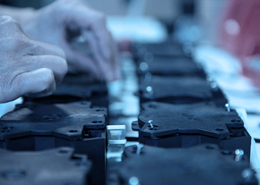
Parts Assembly
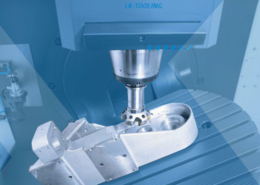