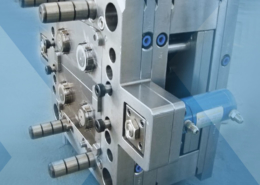
Injection moulding Automotive; Plastic parts - automotive injection molding comp
Author:gly Date: 2024-10-15
Seasky Medical serves you with medical injection molding solutions from design to tooling to material selection and manufacturing. Contact our specialized team and solve your problem now.
We fully respect if you want to refuse cookies but to avoid asking you again and again kindly allow us to store a cookie for that. You are free to opt out any time or opt in for other cookies to get a better experience. If you refuse cookies we will remove all set cookies in our domain.
Even for limited productions, executing a mold flow assessment is instrumental in pinpointing potential complications such as weld lines or air entrapments.
Low volume injection molding grants the liberty to make design alterations between production batches. Such adaptability is indispensable, especially when incorporating feedback or aligning with market dynamics. With a limited number of components in each batch, design modifications are both more feasible and economical.
When it comes to medical products, such as syringes, gloves, and masks, the ability to produce high volumes with consistency is crucial. This is where injection molding excels. With this technique, once the mold is created, thousands of identical parts can be produced without the need for maintenance.
Are you searching for high-quality, precise mold manufacturing solutions for your medical devices? At Remington Medical, we offer excellent contract manufacturing services that ensure consistent, high-volume production.
Because these cookies are strictly necessary to deliver the website, refusing them will have impact how our site functions. You always can block or delete cookies by changing your browser settings and force blocking all cookies on this website. But this will always prompt you to accept/refuse cookies when revisiting our site.
Medical injection molding ensures that the produced components meet all necessary regulatory requirements set by the FDA.
Did you know that injection molding is revolutionizing the medical device industry? This innovative manufacturing process ensures the creation of high-quality, precise, and cost-effective medical devices.
Seasky Medical serves you with medical injection molding solutions from design to tooling to material selection and manufacturing. Contact our specialized team and solve your problem now.
The medical injection molding process involves melting medical-grade plastics and molding them into the desired shape of medical devices. This process creates strong, durable equipment with impeccable surface finishes and precise measurements.
Silicone, a unique chemically inert compound similar to synthetic rubber, offers exceptional mechanical properties and compatibility with biological tissues. With its exceptional flexibility, silicone is the go-to medical-grade plastic polymer for manufacturing a wide range of products and devices, such as catheters, connectors, and tubing.
Beyond mere molding, SeaskyMedical offers holistic solutions. Our expertise encompasses product design, development, material consultation, mold creation, injection mold design, and an array of supplementary services. Our reputation as a leading medical device injection molding firm is anchored in our ability to custom-craft injection molded components while strictly adhering to medical industry protocols.
Low-volume injection molding is a refined manufacturing process tailored for the fabrication of limited quantities of plastic components. This method contrasts with high-volume or mass production techniques which generate extensive batches of uniform components. The growth in demand for bespoke, specialized products, coupled with the burgeoning emphasis on rapid prototyping in product evolution, underscores the pivotal role of low-volume injection molding in contemporary manufacturing.
Our injection mold manufacturing process is ideal for products and plastic parts that require large-scale production. With scalable injection molding machines, we can easily adjust to meet your needs with consistent, high-quality production every step of the way. Contact us today to learn more about injection molding for medical devices.
Contrary to the significant capital expenditures required for mass production, largely due to tooling and setup costs, low-volume molding presents a cost-effective alternative. This approach refines the supply chain, yielding significant cost efficiencies and augmented adaptability. Such merits are particularly advantageous for nascent enterprises and entities with constrained financial resources, enabling them to fabricate premium-quality components without overextending their budgetary provisions.
We may request cookies to be set on your device. We use cookies to let us know when you visit our websites, how you interact with us, to enrich your user experience, and to customize your relationship with our website.
Material: For productions in limited quantities, utilizing materials such as aluminum is frequently more economically advantageous compared to hardened steel. This is attributed to aluminum’s machinability and cost-effectiveness, notwithstanding its comparatively reduced longevity.
Similar to overmolding, the insert molding technique involves molding a secondary component over an existing part, or the insert. What sets insert molding apart is that it is a single process and can be used with various materials, such as plastics, metals, or alloys.
Ensure the chosen material aligns with low-volume production requirements. Certain specialty or bespoke materials may not be accessible in limited quantities or might incur significant costs.
Polycarbonate (PC) is transparent and has excellent mechanical properties. It’s tough, flexible, and resistant to abrasion, breakage, and temperature. Polycarbonate is also highly compatible with bodily tissues, making it ideal for manufacturing various medical equipment, from clear masks to protective gear and oxygenators.
Injection molding guarantees tight tolerances and dimensional accuracy, which are crucial in the medical field. With injection molding, even the smallest deviations can be avoided, reducing the risk to patients.
Uniformity in Wall Thickness: Maintain a uniform wall thickness throughout to mitigate potential issues such as sink marks or voids. Introduce modifications in thickness in a gradual manner.
Overmolding is an advanced technique that involves molding one or two components over an existing structure, resulting in a strong and durable grip. This two-step process, also known as two-shot molding, may have a longer production cycle, but the benefits are well worth it. With overmolding, manufacturers can create ergonomic handles to improve the comfort of everyday devices, which adds value and functionality to a wide range of items.
Your search for a trusted partner in custom medical injection molding is realized with SeaskyMedical. As an ISO-certified establishment in medical injection molding, we consistently maintain unparalleled standards of excellence. Utilizing only certified materials, our products have garnered extensive trust within the medical industry. All our manufacturing, assembly, and packaging procedures are meticulously conducted in an ISO 8 cleanroom, equipped with the most advanced injection molding apparatus.
Polyetheretherketone (PEEK) is a high-quality thermoplastic known for its exceptional resistance to harsh environments, including radiation, high temperatures, chemicals, and wear and tear conditions. PEEK is perfect for creating medical and surgical implants and offers impeccable dimensional stability, even after being exposed to stress.
Polyethylene (PE) is a versatile, durable medical-grade plastic polymer composed of thousands of ethylene polymers, giving it impressive tensile strength and rigidity. PE is also highly compatible with biological tissues and can withstand harsh environmental conditions, including sterilization. Thanks to these properties, PE is widely used in the medical field for manufacturing joint prostheses, connectors, tubing, pharmaceutical containers, and more.
Given the fewer components produced, there is an amplified focus on quality assurance. This guarantees that every component aligns with established benchmarks and maintains stringent tolerances. Such rigorous precision is vital, especially in sectors where meticulous accuracy is non-negotiable.
We provide you with a list of stored cookies on your computer in our domain so you can check what we stored. Due to security reasons we are not able to show or modify cookies from other domains. You can check these in your browser security settings.
Polystyrene (PS) is a high-quality engineering-grade plastic that’s not as flexible as others, but it has exceptional mechanical properties and is compatible with body tissues. Polystyrene offers excellent dimensional stability, making it ideal for creating critical medical components like petri dishes, culture trays, and diagnostic parts.
This process allows companies to produce parts efficiently, adhering to tight tolerances, and ensuring the implementation of best practices for a better surface finish, even when the quantities are limited. Such flexibility is invaluable, especially during the early stages of product development or when introducing a new product to the market. By employing low volume injection molding, companies can test the waters, gather feedback, and make essential modifications before diving into mass production. In essence, it offers a bridge between initial design considerations and full-scale production, ensuring that products are market-ready and meet the desired quality standards. Low volume injection molding is a great option for businesses looking to produce plastic parts and products in smaller quantities. Using this technique, you can save time and money on production costs while still maintaining quality.
With additive manufacturing, medical professionals can now rely on high-quality injection parts that meet the strictest industry standards. Whether it’s intricate surgical tools or complex implantable devices, injection molding for medical devices ensures that every component is flawlessly fabricated for optimal performance. This medical parts manufacturing process is common to develop a wide range of components, devices, and parts, such as:
Design Simplification: It is advisable to choose tools that are either single-cavity or have minimal cavities, as opposed to multi-cavity options. Doing so contributes to a reduction in both expenses and fabrication timeframes.
Plastic injection molding involves melting plastic polymers at high temperatures to create sterile and contaminant-free medical equipment. By reshaping the plastics in aluminum or steel molds, manufacturers can produce precise and customized medical devices that meet the highest standards of hygiene.
Assembly Considerations: If the component is to be integrated with others, prioritize its ease of assembly during its design stage.
Polypropylene (PP) is a highly effective plastic polymer commonly used in medical injection molding. With its exceptional strength and resistance to cracking, radiation, impact, temperature, wear, and tear, it’s no surprise that it is a top choice in the healthcare industry. From life-saving syringes and connectors to essential knee and hip replacements, PP is the preferred material for producing critical components in healthcare.
SeaskyMedical is distinctively recognized for our steadfast commitment to quality. It is our assurance that every product not only aligns with but exceeds industry standards, achieved through stringent quality controls. Our portfolio encompasses medical enclosures, intricate equipment components, prosthetics, and a diverse range of plastic medical and laboratory disposables.
Structural Reinforcement: Integrate ribs and gussets to enhance structural rigidity without expanding the wall dimensions.
Click on the different category headings to find out more. You can also change some of your preferences. Note that blocking some types of cookies may impact your experience on our websites and the services we are able to offer.
Injection molding is not only automated, but it also significantly reduces labor costs. With computer-controlled precision, each part is efficiently produced, resulting in lower costs per unit.
These cookies are strictly necessary to provide you with services available through our website and to use some of its features.
The world of low volume manufacturing is vast and ever-evolving. With the rapid strides in technology and changing consumer demands, the methods we employ to produce goods must also adapt. Among the plethora of manufacturing methods, injection molding has emerged as a dominant force, especially in the realm of plastic parts production. But, as with everything, the nuances matter. Not every product demands mass production of parts. Sometimes, the need is for fewer, specialized parts without compromising on quality. Enter the realm of low volume injection molding—a specialized niche that caters to specific project goals. This guide aims to shed light on the intricacies of low volume injection molding, its benefits, and its significance in today’s manufacturing landscape.
In today’s fast-paced market landscape, time is of the essence. Focusing on smaller production batches, low volume injection molding inherently leads to reduced lead times. This translates to accelerated product launches and the capability to rapidly adapt to market demand fluctuations.
When it comes to plastic injection molding, understanding the difference between low volume and high volume is pivotal for decision-making. Below is a comparative table highlighting the key distinctions:
Liquid silicone injection molding involves heating silicone to a liquid state and then molding it into various shapes, making it a versatile solution for developing medical products. Silicone, a plastic polymer, is specifically designed to meet the needs of the medical industry. However, it’s important to note that silicone molds may not be as durable as aluminum or steel molds, making this technique more suitable for small quantities and initial prototyping stages.
We also use different external services like Google Webfonts, Google Maps, and external Video providers. Since these providers may collect personal data like your IP address we allow you to block them here. Please be aware that this might heavily reduce the functionality and appearance of our site. Changes will take effect once you reload the page.
While it’s feasible to obtain precise tolerances, it might be beneficial both in terms of practicality and budget to allow for slightly relaxed tolerances in low-volume batches, given the project permits.
Selecting an optimal low volume injection molding service is of paramount importance. Please consider the following critical factors when making your decision:
Surface Specifications: Should a specific texture or finish be mandated, it’s imperative that the mold’s design encapsulates these requirements.
Low-volume injection molding plays a pivotal role in contemporary manufacturing due to its adaptability, cost efficiency, and superior quality. Collaborating with esteemed partners such as SeaskyMedical ensures a commitment to excellence. Whether introducing a novel product or searching for a reliable production ally, the implementation of low-volume injection molding offers significant
GETTING A QUOTE WITH LK-MOULD IS FREE AND SIMPLE.
FIND MORE OF OUR SERVICES:
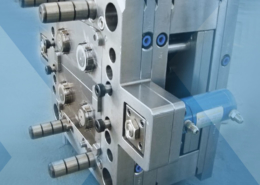
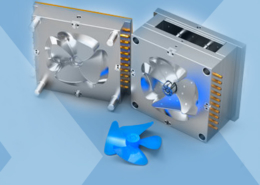
Plastic Molding

Rapid Prototyping
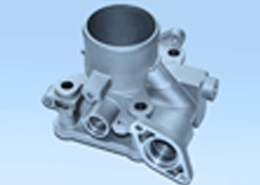
Pressure Die Casting
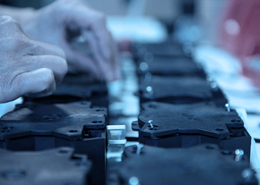
Parts Assembly
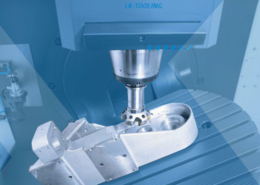