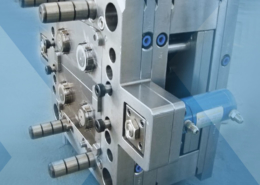
Injection Moulding Australia | Plastic Injection Moulding - plastic injection to
Author:gly Date: 2024-10-15
Offering the option to use low-cost, quick-cooling aluminum tooling for short runs of prototype parts, Fictiv’s injection molding services are a great solution for rapid prototyping. You can have a finished part made of final materials ready for testing quickly. Plus, once you’re past the prototyping stage and ready to scale up production, Fictiv offers steel molds for longer production runs or as a bridge tooling solution.
To help create parts that meet these requirements, Fictiv provides a large range of high-performance injection molding materials, including engineering-grade plastics, thermoplastics and specialty plastics. This allows you to achieve a wide variety of performance properties all in one part.
A Plus Plastics is an Australian company that was founded in 1973 and specializes in coming up with designs for various products and production of products through the plastic injection molding process. Some of these products are used in various sectors such as medical sectors, engineering, automotive and agriculture among others. A Plus Plastics has proven to have the ability to make parts that weigh up to 9kgs which makes it suitable for production of parts of high complexity. It also has the ability to produce parts of a variety sizes according to the preference of the customer. This company is the number one plastics company that deals with the designing and production of non-flexible plastic containers which are used in packaging activities, supply chain and handling of materials. Over the 40 years of its existence, A plus Plastics has helped and is still helping to ensure that its customers get innovative designs, the right materials for products, the right kind of tools to use, the right prototypes and at favorable prices. It is ISO 9001 certified which makes it able to provide products of the required highest standard and best performance. This company reduces costs of labor by the use of robots in the production process and also uses recyclable plastics in favor of the environment.
Plastools company has been in operation for more than 60 years since its founding in 1956. This company has the ability to come up with solutions for new products or old ones which need repair and also provide any changes needed on any kind of mold. It mainly specializes in solutions to be used in the 3D machining process. Plastools has recently extended its operations to precision machining, composite tooling and thin wall plastic tooling. Some industries such as Aerospace, automotive, building and construction and packaging use services from this company in the manufacturing of various parts.
Thanks to a diverse and carefully selected network of domestic and offshore manufacturing partners, Fictiv is fully equipped to offer numerous types of injection molding services for automotive applications. Manufacturing partners are thoroughly vetted by Fictiv and are required to complete rigorous testing. In addition, Fictiv continuously manages them and monitors their performance.
Aesthetics also play an important role in a car’s construction. Not only do drivers want a well-performing vehicle, they want a good-looking one too — from the inside out. To help produce the most aesthetically pleasing automotive parts, Fictiv offers custom color matching as well as custom texture and surface finishing services without impact to lead times.
From prototype to final production, Fictiv takes the guesswork out of the injection molding manufacturing and overmolding processes. The Fictiv team will work closely with your company to help design and fabricate high-quality automotive parts with fast and repeatable results while meeting stringent automotive industry requirements.
By signing up, you agree to our Terms of Use and Privacy Policy. We may use the info you submit to contact you and use data from third parties to personalize your experience.
We exist to eliminate bottlenecks in new product development by integrating the people, processes, and platform you need to source custom parts.
Formrite Group is an Australian company founded in 1957. It specializes in the designing and the manufacture of plastics used for packaging and exhibitions utilized in shelf ready trays, packagings used for medical devices, trays used to carry food, shelf management trays, freezer grades and part trays among others. The standards of their products are regulated by ISO 9001:2015 and they are also certified by HACCP in reference to the food industry. Formrite Group manufactures products to be used locally and other accepted industries across the world. The customers get to gain a great contribution by the Formrite Group in the growth of their businesses due to the provision of all services that are necessary in the production process.
In all cases, Fictiv gives you the resources to achieve the performance properties and aesthetics you require in the timeframe you need.
By signing up, you agree to our Terms of Use and Privacy Policy. We may use the info you submit to contact you and use data from third parties to personalize your experience.
We exist to eliminate bottlenecks in new product development by integrating the people, processes, and platform you need to source custom parts.
Our trained employees ensure your parts will be delivered on time and to spec.
B & C Plastics is also a family owned company that was founded in 1987 and helps its customers through the production process to ensure the required steps are followed. This company customizes products for its customers into their desired designs and they enter into the manufacturing process with partners based on contracts. This company has access to a large number of machinery and adequate labor force which contribute to its efficiency. B & C Plastics specializes in plastic end products and helps in the manufacture of PP, PET and HDPE plastic packaging. B & C Plastics uses modern day innovations to come up with different solutions for prototyping, CNC Machining, 3D printing and also in the assembly process. Some of the companies that B & C Plastics has worked with include Wagners, Dulux, Bradnam’s windows & doors, AMSL, Virgin Australia, Telstra and Ergon among others.
Plastic materials were first used in the production of automotive parts as early as the 1940s and 1950s. Since then, plastic has only become more integral in automotive manufacturing and has slowly replaced metal as the material of choice. Everything from exterior parts like tail lights, grilles and bumpers to interior parts like air vents, door handles and cup holder inserts are made from plastic. Even under-the-hood components like oil pans are now produced using plastic. And how are all these parts manufactured? Through injection molding.
In the day-to-day manufacturing processes of industries, most industries have embraced the plastic injection molding process due to its ability to produce various parts in large numbers. This process is commenced by first forming the mold and the liquefied materials are inserted into it. The materials can be in the form of metals, elastomers, glasses, thermoplastic polymers or even confections. The final products are usually of similar features as designed by the designers through the molds. Australia is one of the countries where plastic injection molding has been embraced by many manufacturing companies. Some of the manufacturing companies include: automotive companies so as to produce various parts of cars, companies that involve the production of products that are commonly used such as toys, bottle tops, containers used for storage among others. In this article, we have discussed the top ten providers of plastic injection molding services in Australia. To know more about these companies, read on.
Lightweighting, or the process of manufacturing lighter vehicles to deliver better fuel efficiency and handling, is another goal common among automotive companies. Replacing metal with plastic is the most efficient way automotive companies achieve this. However, lightweighting can prove difficult in applications that require parts with higher levels of strength and performance. That’s why heavy metal parts have traditionally been the go-to choice for more demanding applications at the expense of production time and vehicle weight. But there is a solution: overmolding.
In electric vehicles, overmolded battery components — such as enclosures and electric motor housings — can be used to offset the weight of heavy battery systems. Rigid plastic materials can also be encompassed in a soft elastomeric rubber material to create parts with enhanced electrical resistance, vibration and noise reduction, or sealing properties. And in some cases, it can help lower cost per part by eliminating the need for connectors, O-rings and other rubberized pieces and associated part assembly labor.
Romar Engineering was founded in 1968 as a shop that specialized in the production of plastic tools for the automotive sector in Australia. With time and improved technology, the company has become the biggest manufacturer for consumables made of silicone in Australia in the IVF sector. Romar Engineering is best known for its proficiency in production of elastomers, silicone, plastics and every metallic product. It also takes part in micromolding, precision molding, clean room, additive manufacturing, prototyping, packaging and labeling and computer-aided engineering. The availability of vast knowledge in the above activities helps to ensure products of high quality. It is also certified by ISO 9001 and 13485. It uses recyclable plastics to ensure that the production process is environment friendly. Most sectors rely on solutions made by this company and they include mining sectors, medical sector, aerospace, aeronautical, automotive and defense sectors. Today, Romar is trying to be the first locally-owned industry in Australia to supply vertically integrated fluid and motion control for the domestic space sector.
If you’re in need of fully rubber parts, like grommets and cup holder liners, Fictiv also offers compression molding manufacturing services.
Lincoln Plastics was founded in the year 1959 and has been very efficient over the years in the provision of solutions concerning the manufacturing processes to a number of industries in Australia. This company is aware that a customer always looks for the company that has vast knowledge on the given role and provides services and end products of high quality. It guides the customer throughout the production process, from the design to the finished end product. Some of the products that are manufactured by Lincoln Plastics include materials made of plastic, synthetic resins and non vulcanizable elastomers. The company sticks to its principles which include transparency, assurance of quality and ethics which has contributed to the good relations with customers and high quality end products. Lincoln Plastics helps to produce various plastic products for industries such as automotive, construction, building, recreation and irrigation among others. This company is also certified by ISO 9001:2015 which helps to ensure end products of high quality and customer satisfaction.
Allmould plastics is a company owned privately and controlled by a family, which was founded in 1995. It has headquarters at Orange NSW. In the course of the years, it has specialized in plastic injection molding and greatly considered the satisfaction of its customers. Allmould plastics are usually utilized by companies in the construction sectors to produce plastic parts. This company provides its customers with designs for products, prototyping of products, Polyurethane molding, warehousing and manufacturing of the products using machinery such as CNC milling. It helps in production of various equipment used in medical industries, for packaging done on food, chemicals, mining, electronics and many others. Allmould plastics Group consists of AMP Circular which helps to ensure that recycling processes are adhered to in the production process in Australia. This was formed due to the strong beliefs of the company that the environment is vital and should be kept safe.
Fictiv also has the resources and technical expertise to speed up the design, development and production of automotive components to help automakers go from prototype to finished part in as little as 10 days. This is done by analyzing your part design plans and providing Design for Manufacturability (DFM) feedback. DFM allows you to remedy part manufacturability issues early in the prototyping process to avoid costly roadblocks and pick up efficiencies along the way — which is key for keeping production lines open and ensuring speed to market.
Most automakers have to abide by strict performance and safety requirements when manufacturing their parts. For example, exterior parts like door panels, hoods and trim pieces typically need to provide extra durability and UV resistance, while components that live under the hood are often required to provide high levels of flame, chemical and impact resistance.
By signing up, you agree to our Terms of Use and Privacy Policy. We may use the info you submit to contact you and use data from third parties to personalize your experience.
By signing up, you agree to our Terms of Use and Privacy Policy. We may use the info you submit to contact you and use data from third parties to personalize your experience.
As seen above, most of the companies have been in existence for long which has helped them to acquire skills and knowledge to utilize in serving the market. Australian companies have been seen to keep the interests of their clients in mind which has made their growth significant over the years. Over the years, some of the Australian companies have gone global whereby they export their services and products. This has helped them to find ways to deal with their competitors such as China. There also consists of other companies which are going day by day and reaching more customers.
If you’re ready to join the 2,500+ companies who use Fictiv for high-quality parts, visit fictiv.com/signup to request a free quote.
To further ensure repeatability and the delivery of the highest-quality parts, Fictiv offers a wide range of injection mold manufacturing options with rigorous quality management systems and inspection protocols in place. Additionally, one of Fictiv’s quality engineers will conduct quality assessments of your parts and deliver transparent inspection documentation to ensure all standards are being met.
By signing up, you agree to our Terms of Use and Privacy Policy. We may use the info you submit to contact you and use data from third parties to personalize your experience.
Fictiv’s overmolding services expand on the benefits of injection molding by allowing you to manufacture intricate automotive parts and assemblies from two or more materials in a short amount of time. This means you can achieve lighter, quick-turn parts with superior strength and performance properties — such as thermal, chemical and impact resistance — that are better suited for more demanding automotive applications.
C & C Plastics company was founded in 1991 and over the years it has evolved into one of the best companies involved in the custom plastic injection molding process. The company currently has 16 machines used in the process that vary between 30 to 500 tonnes. C & C Plastics specialize in services such as injection molding, assembly, insert molding, project management, custom development and also assessing and the production itself. This company is very customer centered which makes it one of the company’s strengths and also the high quality end products.
A crucial step in the final production of automotive parts, injection molding is a method that heats and injects plastic material under pressure into a closed metal mold. The molten plastic is then cooled until it hardens into the desired shape — which can vary in size, volume and complexity.
Accelerate development with instant quotes, expert DFM, and automated production updates.
By signing up, you agree to our Terms of Use and Privacy Policy. We may use the info you submit to contact you and use data from third parties to personalize your experience.
Access a wide breadth of capabilities through our highly vetted network.
By signing up, you agree to our Terms of Use and Privacy Policy. We may use the info you submit to contact you and use data from third parties to personalize your experience.
By signing up, you agree to our Terms of Use and Privacy Policy. We may use the info you submit to contact you and use data from third parties to personalize your experience.
By signing up, you agree to our Terms of Use and Privacy Policy. We may use the info you submit to contact you and use data from third parties to personalize your experience.
Due to its ability to quickly and cost-effectively produce high volumes, injection molding has long been a popular manufacturing method among automotive makers. However, not all injection molding manufacturers produce the same results — especially where speed to market and repeatable quality is concerned. That’s why many automotive companies turn to Fictiv for repeatable, high-performing parts with minimal lead time.
Each company has areas whereby it is well suited in and its specializations which makes it easy for you to know who to approach. It is crucial for you to go to the right company to ensure that the final products are of the right quality and standards. Some companies also promote other companies and their products without getting involved in the manufacturing process. To learn more about plastic injection molding, visit TDL: Plastic Injection Molding.
When precision, driver safety and brand integrity are top priorities, producing identical, high-performing parts (consistently at a high volume) is crucial. Combining computer-aided design with quality injection mold tools, injection molding makes it possible to develop automotive parts with intricate details and achieve complex geometries in a very repeatable fashion.
The automotive industry is highly innovative and highly competitive, which puts pressure on automakers to be both leading-edge and first to market. However, car and truck parts often go through dozens of iterations before the final part is deemed ready for mass production according to safety standards. This makes rapid prototyping an essential step in the manufacturing process.
Create high quality custom mechanicals with precision and accuracy.
PlastixANZ is a private company that was founded purposely for the market in Australia and New Zealand. The aim of its formation was so as to make a shop available for the users, buyers and suppliers of plastic products more conveniently. This company has helped to promote the growth of plastic industries through creating awareness of the products to the market. For the efficiency of PlastixANZ, industries have to be transparent and give the necessary information to the company and also be ready to work with the opportunities that come from PlastixANZ. This company has embraced new technology to make the marketing process more easier, such as the use of social media to advertise products.
Sneddon & Kingston Plastics is a family owned company which has been operational for over six decades since it was founded in 1958. In 2014, the company joined the IML Food Packaging market. It specializes in the designing, production and distribution of products manufactured through plastic injection molding. With the improving technology, this company has enough experience and utilizes modern means to manufacture plastic end products that are of high quality and in large numbers. The company uses the 3D CAD software which enables it to have an actual picture in mind of the design. The company also produces custom plastic injection molding which helps to ensure that the given qualities and performance of the plastic products are met. Sneddon & Kingston is certified by ISO 9001 as well as HACCP. This company produces products used in the medical industry, packaging of food, automotive industries and in building and construction.
GETTING A QUOTE WITH LK-MOULD IS FREE AND SIMPLE.
FIND MORE OF OUR SERVICES:
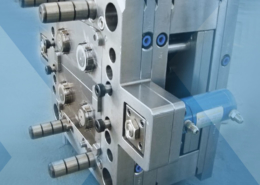
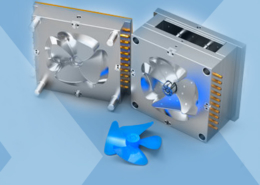
Plastic Molding

Rapid Prototyping
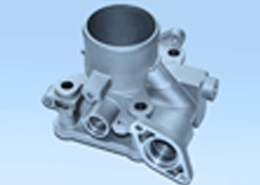
Pressure Die Casting
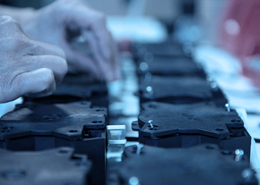
Parts Assembly
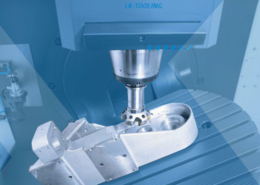