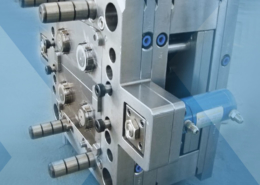
Injection Moulding Australia | Plastic Injection Moulding - injection moldable p
Author:gly Date: 2024-10-15
Metal 3D printing can also be used as a manufacturing method to 3D print injection moulds. This is one of the latest innovations in established 3D printer markets such as the US and is a game changer for the plastic injection moulding manufacturers, especially when cnc machining is most commonly used in manufacturing molds in injection molding. 3D printed free-form cooling chambers has considerably reduced cooling time over machined straight channels by lowering polymer and cavity surface temperatures. 3D printed inserts for injection molded tools is another quick way to for custom injection moulding and modify before committing to production tooling. Quicker cycles increase productivity, more variants and more uniform cooling improves part quality and minimises defects from heat transfer. Not all 3D printer for metal is alike, ask us which is best suited for your requirements in precision and manufacturing conditions.
With the high initial cost set up and time-consuming nature of injection moulding tooling design, 3D printing is more accessible for prototyping and testing of design before tooling commitments. The cost of modifications in injection moulding is high unless metal 3D printed inserts are considered, or the use of 3D printed conductive metal to improve heat dissipation in concentrated areas and 3D printing of injection moulds with conformal cooling chambers.
We provide high impact Polystyrene injection molding services in New York, New Jersey, Connecticut, Pennsylvania, Florida, California, Illinois, Oregon, Maryland, Massachusetts, Colorado, and Michigan and other regions.
On the other hand, a SLS 3D printed part can be used as an end use product, made by precise sintering layers of nylon powder with the use of powerful lasers, without the need for support structures. Such high performance 3D printing machines tend to cost more.
Our mold maintenance plans for projects that include high impact Polystyrene injection molding services ensure each mold undergoes regular cleaning and review at predefined intervals based upon the number of setups and cycles. Mold inspections, general mold maintenance, major mold maintenance and preventative maintenance are standard operating procedures.
Clients trust Natech to be the high impact Polystyrene injection molding experts in engineering and manufacturing. Our engineers’ experience includes mold qualifications in medical IQ/OQ/PQ, high volume automation and high impact polystyrene injection molding production.in consumer packaging, and engineering-grade resins and ultra-polymers in electronics.
We are an ISO-certified, family-owned provider of engineering, custom injection molding, and contract manufacturing. Our clients bring demanding applications requiring high impact Polystyrene injection molding services and best served by expert engineers.
Our assembly and joining capabilities include product filling, foil/heat sealing, ultrasonic welding, heat staking, mechanical assembly, pinning & UV/hot melt gluing, custom packaging/kitting, and pouching.
The production molds for high impact Polystyrene injection molding projects include high cavitation SPI Class 101 and 102 molds constructed from hardened steel. Cold, runner, hot sprue, and hot runner molds are designed with up to 128 cavities.
All manufacturing methods have their own strengths and disadvantages and which process to use depends on what requirement is a priority. In some cases, metal 3D printing could even manufacture inserts and complex injection moulded tools with conformal cooling chambers to improve traditionally injection moulded products.
Anyone can access multiple plastic and metal 3D printing processes with the use of Additive Engineering’s 3D printing service, 3D printing material and expertise.
We take pride in the workmanship of our high impact Polystyrene injection molding services. All Natech tools and production parts are made in the USA. We run three shifts per day, five days per week, and weekends are run on an as-needed basis.
Each development project requiring high impact Polystyrene injection molding services is managed by a Project Engineer who monitors and controls deliverables and provides regular status updates.
First of all, is it injection moulding or injection molding? Injection moulding originates in Britain and is often used in Australia and Canada while injection molding is the American spelling. Since Additive Engineering is based in Australia, we use injection moulding to answer enquiries about injection molded parts, mold cavity, injection molder, manufacture of injection mold, plastic injection molding, 3D printed injection molds / printed molds and an injection molding machine.
Cooling channels form a mesh structure to enable uniform surface cooling of a glass insert for spectacles, just 2-3mm beneath mould contour. Results : High-pressure stability throughout arched structure and temp control across large areas
Whatever you are most familiar with, whether it is ‘printing vs injection molding’, interests in ‘3D printed injection mold’, if you have an plastic part project, additive manufacturing enquiries or past experiences with different 3D systems, we like to hear from you.
The good news is, at Additive Engineering, we offer injection moulding, vacuum casting, metal and plastic 3D printing services with a range of 3D printer options and an experienced team to support you.
Is it the case of injection moulding vs 3D printing? How does one choose which manufacturing process is better suited? Why not both? When starting a project involving plastic manufacturing, the factors to consider include material properties, process’s flexibility to design change, precision, finish, volumes, time and cost.
Our high impact polystyrene injection molding product finishing capabilities include hot stamping, banding, pad printing, silk screening, flaw coating, conductive painting, cosmetic painting, metalizing, and plating.
Enable quick, uniform cooling of the ejector pin's unique shape.Results : Hot spot eliminated at contoured pin with tiny cooling channels. Ideal for cooling large surfaces 0.6-0.8mm from contour, helix-shape channel maximised part strength.
3D printing or additive manufacturing refers to the process where the material is built layer by layer. 3D printing creates 3D objects by slicing a computer aided design (CAD) file into layers to reproduce the physical part using filament or powder material. Contrary to popular belief, filament based 3D printing (Fused deposition modeling FDM or Fused filament fabrication FFF) is not the same as powder bed fusion 3D printing such as selective laser sintering (SLS) or Multijet fusion (MJF). FDM parts tend to require support structures, have uneven strength in some directions, has a strong layering effect which could result in shear failure (separation) and the nozzle tends to limit precision. This limits FDM printers to low strength rapid prototyping. Common plastic filament material includes ABS, PLA and PET.
The 3D printing process for manufacturing works best with low volumes, when it is difficult to justify tooling costs. 3D printing parts including prototypes help the customer’s decision making process and has less cost implications with modifications as compared to the traditional injection molding process.
An Industrial moulding company utilised metal 3D printing (Direct metal laser melting) technology to 3D print a mould core with conformal cooling channels. The core contained eight independent, internal conformal cooling channel at 5-8mm in diameter. 3D printing lends design freedom for a more efficient heat exchange and imcrease the overall injection moulding process’ productivity through decreased cooling cycle time, defects and improved the injected plastic parts’ aesthetics.
There is a misconception in the manufacturing world that 3D printing is going to replace injection moulding, especially with the proliferation of 3D printing technologies in recent years. Injection moulding is still used in the majority of plastic parts for industry due to the familiarity of quality and process as well as speed for mass production.
To compare both manufacturing processes, the following overview recaps pros and cons of injection moulding and 3D printing.
Injection moulding makes use of moulds or dies. The part design is used to create the inverse in split-die tooling, the tooling cavity is traditionally referred to as female die and the other as the male. These dies are commonly CNC machined out of metal material such as aluminium or tool steel that can handle molten material. Molten material is poured into the mould via an injection method and the moulds are cooled to release complete plastic parts. There is also metal injection moulding, although the following will focus on plastics.
Our precision injection molding options, including high impact polystyrene injection molding, include scientific molding, R&D molding, high-cavitation molding, micro molding, over molding, and insert molding.
Other plastics 3D printing include Stereolithography (SLA) and Material jetting such as Polyjet 3D printing. SLA technologies is typically used in high precision and low cost single use parts.
Small, unique cooling channels inside the mould of a bucket lid insert allow for parallel cooling of small geometries not possible with other methods. Results : Faster heat transfers due to short channels. Uniform cooling of material, maintained properties
Injection moulding and additive manufacturing / 3D printing are often used as manufacturing techniques for plastic parts such as drink bottles, lids, caps, covers, housings, brackets, packaging, car parts and toys.
In the electronics market we draw upon deep experience in comprehensive analysis and testing for evaluation and verification to design and build lighter, more durable electronics components.
Rather than seeing 3D printing as a potential replacement for injection moulding, these two manufacturing technologies can be complementary and used together to improve quality of plastic products, shorten pre-production cycles, take advantage of mass customisation to cater to more product variants before moving onto large batch production.
Natech’s projects that include high impact Polystyrene injection molding services are supported by MoldFlow Analysis, a Viscosity Curve, a Cavity Balance Study, a Pressure Window Characterization, a Gate Seal Time Study, and a Cooling Time Study. Natech engineers are masters of insert configuration and design single-cavity R&D molds with steel inserted areas. Interchangeable plates, inserts, and sub-inserts allow for more rapid design iterations at LOWER cost than creating new molds for each feature variation. SPI Class 103 and 104 molds are constructed from P20 steel and aluminum with hot runners and cold runners.
For the consumer market we specialize in the automated production of high-volume disposables, unit-dose packaging, caps and closures, and over-the counter diagnostics and drug delivery applications. We can help with high impact polystyrene injection molding too.
All our injection molding presses are equipped with servo-driven robotics for high-speed automation and high impact polystyrene injection molding production.
3D printing is great for batch production of less than 1000 parts, suitable for complex part that may require mass customisation, frequent design changes and can be used for creating a 3D printed mold. Injection moulding, on the other hand, is better for bulk production in the thousands of simple designs.
Our mid to high-volume automated and semi-automated manufacturing of plastic injection-molded components, including high impact polystyrene injection molding, and assemblies for single-use, metered-dose, and multi-use disposables for the drug delivery, consumer packaging and diagnostics industries offer high quality at economical value.
We have developed hundreds of products, some with high impact polystyrene injection molding, and manufactured millions of parts annually for the medical industry. Medical devices include point of care diagnostics, microfluidics, and pharmaceutical drug delivery applications.
GETTING A QUOTE WITH LK-MOULD IS FREE AND SIMPLE.
FIND MORE OF OUR SERVICES:
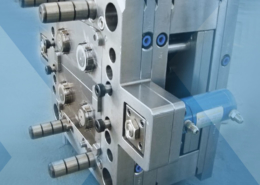
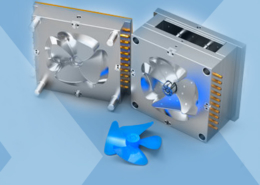
Plastic Molding

Rapid Prototyping
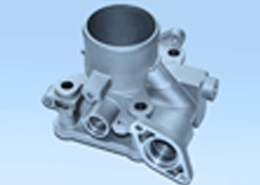
Pressure Die Casting
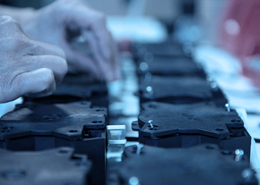
Parts Assembly
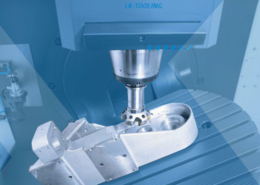