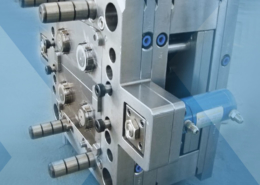
Injection moulding - precision injection molding
Author:gly Date: 2024-10-15
Infrared welding is a rapid and non-contact method that introduces infrared radiation into the plastic components. This radiation is promptly converted into heat, causing the surfaces to melt. The two parts are then pressed together, and with the application of pressure, they bond seamlessly. This technique ensures efficient and effective joining, making it a valuable tool in the plastics industry.
Corry, PA, January 26, 2021 – Viking Plastics, a leading injection molding and value-added assembly service provider to important industries such as energy, HVAC, and transportation, is pleased to announce that for the second straight year, the North American firm with facilities in Brazil, China, and Mexico has made the Plastics News Top 100 Injection Molders based on 2020 annual sales.
Overmolding stands out as an exceptional method for plastic joining, as it goes beyond merely combining multiple materials. Overmolding, in particular, offers extensive benefits for component or device design and performance. It serves as a versatile solution to dampen sound and absorb vibrations, insulate delicate electronic components, and enhance resistance to chemicals and moisture. Moreover, it facilitates the incorporation of a diverse array of colors directly into the plastic, rendering it suitable for applications like keyboards, functional buttons, branding, and customized aesthetics. Overmolding seamlessly integrates these advantages into a single, waste-reducing, efficient process that significantly lowers production costs.
Sungplastic’s melt plastic solutions include:Plastic joining: welding and bondingOvermolding for custom partsInsert molding for plastic parts with metal insertsUltrasonic Welding and common assembly methodsFor Mini parts, small parts, large parts all availableFor high volume or low volume accessibleAmple production lines and capacities and skilled workersAdvanced processing technologies and equipmentStrict quality control system
Plastic bonding involves using adhesives or chemical agents to create a strong, durable bond between plastic surfaces. Adhesives are selected based on their compatibility with the plastic materials being bonded. It is used for joining a wide range of plastic materials, including thermoplastics and thermosetting plastics. Plastic bonding is often chosen when the plastic components are heat-sensitive or have complex shapes. It is also used for applications requiring flexibility or vibration resistance.
Vibration welding is ideal for creating pressure-tight joints, especially in irregularly shaped or larger plastic parts. It is also effective when joining plastics with different melting points. Vibrational heating generates friction, and when combined with pressure, it melts and bonds the plastics. The strength of the resulting weld joint is on par with the base materials. Cycle times average around 5 to 8 seconds for manual or automated operations.
Plastic Mold Manufacturing Plastic Injection MoldingRapid PrototypingCNC MachiningSheet Metal StampingPressure Die CastingSilicone & Rubber PartsSurface Finishing
Incorporating these advanced plastic joining techniques signifies an evolution in the industry, providing versatility and efficiency while ensuring the structural integrity of the final products. These methods allow manufacturers to achieve a range of functional and aesthetic goals, driving innovation and sustainability within the field of plastics.
Spin welding creates circular weld joints by utilizing surface friction. One of the two parts to be joined is rotated at high speed, while force is applied to maintain their connection. The resulting friction generates heat, melting the plastics, and subsequent pressure ensures a strong bond. Spin welds offer high strength, hermetic sealing, and an economical approach to achieving round weld joints.
This method involves melting two plastic parts against a precisely heated platen for a specified duration. After the platen is removed, the two parts are brought together, resulting in a strong, permanent, and often hermetically sealed joint. Hot plate welding is a well-established technique known for producing durable bonds.
As technology advances, so does the realm of plastic joining, with innovative methods that harness heat to manipulate melt temperatures, enhance adhesion, and modify other key characteristics of plastic materials. Let’s delve into these advanced approaches:
The method choice of melt plastic together depends on factors such as the type of plastics being joined, the desired strength of the bond, the application, and the specific manufacturing requirements.
Melted plastic joining is a valuable process used in various industries, including automotive, aerospace, electronics, and consumer goods manufacturing.
Due to enormous versatility, plastics are a preferred material in a wide range of sectors.Plastic products manufacturing has faced some difficulties as a result of its popularity and extensive use. The connections between semi-finished plastic goods and other plastic or metallic materials are strong. Plastic overmolding is one of many tested plastic melting techniques, however the procedure that best fits a given project and budget is not set in stone and must be chosen appropriately depending on the needs of the situation.We can give you the fundamental information that will help guide your process selection and provide unique plastic joining processing services because we are a plastic molding manufacturer who has mastered the key plastic joining techniques.
Founded in 1972, Viking Plastics is a privately held company delivering innovative products including sealing solutions, custom injection molding, assembly, and post-molding secondary services. Viking Plastics’ multiple facilities house more than 200 global molding machines, with capabilities spanning the range from 50- to 720-ton injection molding, as well as capabilities including 2 shot, insert molding, and automated assembly cells. Viking Plastics is IATF 16949:2016, ISO 14002:2015 and ISO 9001:2015 certified.
This method harnesses vibrational pulses and pressure to effectively join relatively rigid plastics. As the materials vibrate and rub against each other, they generate heat and eventually fuse together. Ultrasonic welding is known for its speed and versatility. It finds applications in various tasks, such as inserting metal components into plastic, staking metal and plastic parts, and spot welding plastic.
Laser welding capitalizes on the concentrated heat and precision of a laser beam to fuse plastics. It is particularly well-suited for applications that involve plastics of varying thicknesses. Laser welding excels in high-volume production scenarios, offering the ability to create narrow and deep welds, meeting the stringent demands of complex parts.
Plastic welding involves melting the surfaces of the plastic components to be joined and fusing them together, relied on the application of heat, pressure, and sometimes the addition of filler material to melt and bond the plastic surfaces. It is typically used for joining thermoplastics plastics that can be melted and reshaped multiple times) and is well-suited for applications requiring airtight or watertight seals, high structural integrity, or hermetic bonding.
“After years of substantial growth, being recognized in the Top 100 is a nice acknowledgement of our team’s hard work. We’re very happy to have moved up in the Top 100,” said Viking President and CEO Kelly Goodsel. “We attribute this success to our people, our processes, and our forward-thinking culture here at Viking Plastics. We would like to thank all of our Viking Plastics stakeholders who have engaged, supported, and improved our business (customers, suppliers, investors, communities, and employees).”
Founded in 1972, Viking Plastics is a privately held, relationship-based injection molder making a difference in complex customer applications. An ISO and TS certified company, consistently provides unsurpassed quality and technical expertise for caps, sealing solutions and custom molded components.
GETTING A QUOTE WITH LK-MOULD IS FREE AND SIMPLE.
FIND MORE OF OUR SERVICES:
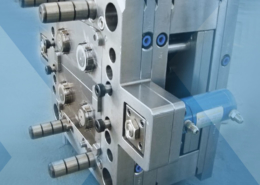
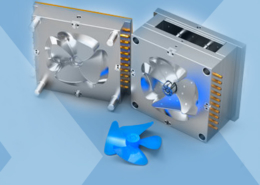
Plastic Molding

Rapid Prototyping
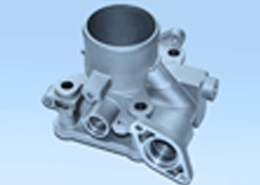
Pressure Die Casting
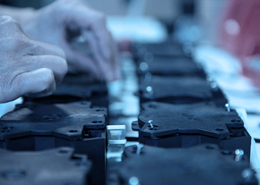
Parts Assembly
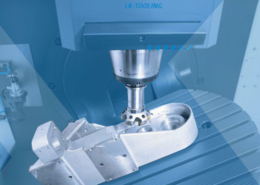