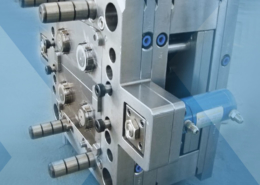
Injection Moulding - Ipoh - kilang injection moulding
Author:gly Date: 2024-10-15
To wrap up, plastic pellets are crucial to the injection molding process. But understanding the various types available for injection molding including polypropylene, ABS, and polyurethane among others is way more important. The selection of the type of plastic pellet is strictly reliant on the material property, compatibility, and quality of the material. Moreover, processing the plastic pellets includes drying and conditioning, melting, and molding, and the effects of recycled or reinforced plastic pellets on injection molding.
Moreso, there’s the option of bio-based plastic pellets which is another alternative means to create raw materials. An innovative advancement that sees plastic pellets derived from renewable, plant-based sources. Plant materials like sugarcane and corn starch are sustainable forms of plastic raw materials in contrast to petroleum-based plastics. Many of the new-age plastic manufacturing companies are environmentally conscious and devoted to reducing toxic waste. Thus, in the high-quality mold manufacturing industry and plastic molding industry more renewable and greener sources of plastic pellets materials are now available.
Considering the roles of plastic pellets and the importance of selecting the right one with accurate properties for injection molding, several types of pellets come up regularly for most projects. The major plastic injection molding materials are highlighted below.
Reinforced plastic pellets as well usually contain additives that can increase the functional features of the plastic material. Although, it may impact flow quality, and the ability to efficiently mold. Modifications can be made to accommodate them.
A noteworthy inclusion is the flow characteristics and moldability of plastic materials. This factor may require design adjustment or process modifications to attain proper filling of the mold and excellent product finish.
Adhering to these in-process parameters delivers quality products with structurally sound parts and excellent surface finish.
HDPE is a popular material for garden furniture due to its low cost. The strength and toughness of HDPE make it possible to produce lightweight and low-cost furniture without compromising mechanical strength. HDPE can also be downcycled for use in imitation lumber that can be used to produce low-cost furniture.Â
Get custom HDPE injection molded prototypes and production parts in as few as five business days. Dozens of materials and finishes are available. ISO 9001:2015, ISO 13485, IATF 16949:2016, and AS9100D certified.
Injection molding HDPE requires a large amount of initial capital investment as the tooling can be very expensive. It is only cost-effective for larger production volumes. Listed below are two potential alternatives to HDPE injection molding:
These tiny raw materials have been the major medium used for manufacturing electronic parts, toys, automotive parts, and packaging containers. However, the selection of suitable plastic pellets, the different types available, and their applications are what manufacturers have to consider before employing injection molding as the method of production.
These are determinants of how the final product turns out. Conclusively, industry trends and innovations are deriving sustainable methods of sourcing plastic pellets. Some of these are biodegradable and bio-based materials and the introduction of additives and fillers. As a manufacturer or enthusiast, arming yourself with this knowledge saves you a whole lot of stress and wastage, while providing you with the best manufactured plastic component ever.
One more factor is the cooling time. A shorter cooling time increases productivity by reducing cycle time, meanwhile longer cooling time can ensure proper solidification of parts but takes longer and productivity is negatively impacted.
HDPE is considered food-safe by the FDA (Food and Drug Administration) and is widely used to store food items. HDPE is highly inert and stable and as such does not leach dangerous chemicals into food products.Â
HDPE is susceptible to environmental stress cracking. When exposed to long-term tensile loads, cracks can form in the material. This is further exacerbated if the HDPE is exposed to a corrosive environment. These cracks can develop at loads much lower than the tensile strength of the material.Â
The accurate melting temperature must be set. Once this is in order, the plastic is melted to the required temperature. The injection speed ensures regular mold filling as too much speed can result in defects in the mold. While a slow-speed injection can result in short shots or part deficiency. Injection pressure ascertains how much flow of the melted plastic pellets enters the mold. The injection pressure must be adequate to fill the mold as insufficient pressure can negatively impact the part produced.
The melt flow rate confirms the ability of the molten plastic to flow without complications. As such, it is measured in grams every ten minutes. As there are different plastics utilized in injection molding, so does the melt flow rate vary. But the application of the material contributes to the output of the finished product.
Selecting the right plastic pellets directly affects the quality and consistency of the parts manufactured. To achieve product quality and consistency it may be wise to acquire plastic pellets from a tested and trusted supplier who understands the assignment. Additionally, consistent plastic pellets’ shape and size ensure proper and predictable melt flow that translates to the overall quality of parts produced. Any irregularly shaped plastic pellet could result in product defaults such as voids and internal stresses.
Industry trends and innovations are skyrocketing, especially in plastic manufacturing. The stakes for innovative mediums of sourcing for sustainable, improved materials to fashion out sound injection-molded plastic components just got raised. Another such introduction is additives and fillers.
In this environmentally conscious world that we live in, handling recycled or reinforced plastic pellets presents ecologically beneficial advantages. In the same vein, it poses other challenges. Recycled plastics are already formed plastic pellets that are meant for reuse. For this reason, the variation in composition should be factored in. Its material makeup may tend to lead to difficulty in processing, differences in strength, and melt flow. For this to function in injection molding, it must be subjected to a series of tests that will help determine how best to apply them.
Melting temperature is the next parameter to consider. The regulated or industry-stipulated melting temperature should be set. An exceedingly high temperature can result in material deterioration and degradation, while too low a temperature may result in an incomplete melting of the plastic. For that reason, it could be eliminated by setting the appropriate melting temperature according to material properties.
Many things can go wrong if the process of injection molding does not fulfill some qualifications. These prerequisites are likely to disrupt the balance of the injection process which can in turn lead to defects, reduced structural integrity, and reduced melt flow. However, all of these can be averted if precautions are duly executed.
A few other plastic materials such as polycarbonate, polyethylene terephthalate (PET), and nylon are some other plastics utilized in injection molding and in the high-quality mold manufacturing industry.
At this stage, the plastic pellets are appropriately dried and conditioned to meet the melting requirements and transferred from the hopper into the barrel for melting. There are in-process parameters to be adhered to at each manufacturing stage. During melting, the required temperature to melt the plastic pellets must have been set. In addition, the injection speed and pressure settings are essential to achieve the desired part intended.
Plastic bottles are one of the most popular uses for HDPE. While most bottles are formed using blow molding techniques, the blank tubes used to make these bottles must be injection molded. HDPE does not leach into the stored liquid and is highly moisture-resistant, making it ideal for bottling applications.Â
Each HDPE formulation will have a unique set of material properties depending on their intended application. Table 1 below lists some common material properties of standard HDPE:
Plastic pellets for injection molding have practically been the most important material that has happened to manufacturers of plastic parts and products, including end users from different walks of life. How has this been you may wonder?
Additives no doubt double the confidence you have in your plastic pellets to produce industry standard, excellent performance plastic parts and components.
HDPE is highly resistant to moisture and is relatively flexible. As such, it is widely used for piping to transport large volumes of water. Individual pipe sections are welded together to eliminate potential leaks. These pipes are often buried underground.Â
Hard hats must be able to withstand sudden impacts and must also absorb as much of the impact energy as possible. As such, HDPE is an excellent choice for hard hats as it is a highly durable and impact-resistant material.Â
Computer-based manufacturing techniques like high-quality CNC Machining can deliver high quality with little human input. Plastic molding on the other hand relies heavily on close monitoring of important parameters chief of which is the type of plastic material used.
Considering that the focus of this post is the selection of a suitable plastic pellet, it is paramount to consider certain aspects that assist in this area. Frankly, material property and requirements are essential aspects to be considered. The reason being that before injection molding can proceed, the project requirement must be analyzed. This includes strength, chemical resistance, and flexibility, to mention a few. On top of that, not all materials are capable of the required properties intended for the project.
HDPE has a density of around 960 kg/m3. This is lightweight compared to metals and even some plastics. HDPE also has a high strength-to-weight ratio which means it can be used to produce thin-walled products like bottles or chemical tanks but still maintain high levels of strength and rigidity.
Without plastic pellets for injection molding the process is considered inefficient. These polymer resin-made pellets are the primary input to the plastic parts and tools formed with injection molding. However, the formation of parts relies greatly on the properties of the plastic pellets. They are of different resins and can transform into any desired shape just like other advanced manufacturing techniques like 3D printing technology. The transformation process duly begins when the plastic pellets are fed into the barrel where heating and melting take place. The molten plastic is then injected into the mold cavity to take shape. These steps are crucial to part formation.
Consequently, conditioning the plastic pellets for injection molding represents keeping the pellets at a conducive temperature before proceeding to melt the plastic pellets. It’s a form of preparatory step conditioning the plastic pellets in readiness for melting. Conditioning assists the plastic pellets to melt accordingly, thereby fostering the proper melting of the pellets.
One such precaution is material drying and conditioning. Why should dry or condition the material you may be thinking about? Material drying helps to eliminate moisture content in the plastic pellets. The inclusion of moisture before sending it to the barrel for melting is liable to cause voids in the pellets. Moist can also be responsible for lower mechanical features of the pellets that can impair the product’s qualities. Drying methods such as desiccant drying, hot air drying, or vacuum drying are applied during the drying process.
Another crucial factor in part formation is the type of pellet being used. There are various types, and their application to part formation depends on what the mechanical features, aesthetical properties, and the designed lifespan of the molded part should be. Considering that, the impact and chemical resistance in each type of plastic pellet is different. Some possess higher impact resistance to chemical resistance and vice versa.
HDPE has low thermal conductivity. If cooling is too quick or uneven, this can result in the part warping or shrinking during injection molding. HDPE can have a shrinkage rate of between 1.5% and 4.0%.
HDPE is considered a commodity plastic and is relatively low-cost when compared to other plastics like polypropylene, for example. This makes it a cost-effective material to use for injection molded products. It must, however, be noted that the tooling required for injection molding is often the largest contributor to initial set-up cost.Â
Choose from millions of possible combinations of materials, finishes, tolerances, markings, and certifications for your order.
Certain parts require high heat resistance. In such projects, materials such as polyetheretherketone are likely to achieve such feats. In addition, for flexibility-related products, thermoplastic elastomers (TPE) like polyurethane (PU), or thermoplastic vulcanizates (TPV) may be appropriate.
When it comes to chemical-resistant plastic pellets, not all polymer resins are chemical resistant. While some boast of higher chemical resistance to other plastic pellets. Plastic pellets that are chemical resistant include fluoropolymers like polytetrafluoroethylene (PTFE) or polyvinylidene fluoride (PVDF). These material properties reflect on the product, and because of that proper consideration must be assigned.
HDPE has poor UV resistance as the carbon-hydrogen bonds are attacked by UV radiation. The breaking of these bonds ultimately causes photo-oxidation which degrades the material over time. Additives like UV stabilizers can be incorporated into the HDPE formulation to improve its UV resistance.Â
Biodegradable plastics are plastic wastes that naturally break down over time, making them reusable as plastic pellets for injection molding. Nonetheless, they are suitable for plastic materials whose shelf life is typically limited. An example of such plastic is disposable cutlery. They are eco-friendly and environmentally safe for production purposes and simultaneously reduce waste accumulation.
Deep concerns have sprouted over the usage and disposal of plastic waste which may have an increased environmental impact on our world today. It is for this reason that manufacturers of plastic parts and components seek to find sustainable alternatives to sourcing plastic pellets as raw materials. One such way is via biodegradable plastic pellets or bio-based materials.
In addition to material properties and requirements, understanding the plastic pellets that align with injection molding is paramount. Compatibility with the molding process must be considered to ascertain plastics with precise melt flow rate (MFR), and temperature as it relates to melting and cooling. These are determinants of its ability to mold properly.
What’s more, the features of each plastic pellet can influence the melt flow rate of each plastic pellet. This is the reason selecting the appropriate plastic pellet for the desired molded parts is essential for plastic injection molding as well as for high-quality mold manufacturing.
High-Density Polyethylene (HDPE) is a thermoplastic polymer supplied in pellet form for injection molding. HDPE is widely used for injection molding due to its low cost, chemical resistance, high tensile strength, impact resistance, and low moisture absorption. In addition to its physical properties, HDPE has excellent processability due to its relatively low melt temperature and low viscosity.Â
HDPE is a thermoplastic. It can be remelted and reused if properly processed at a recycling plant. Most recycling plants will accept HDPE due to its widespread use, in addition to HDPE being one of the easiest plastics to recycle. HDPE can also be downcycled, i.e., reused on lower-value items like imitation plastic lumber.Â
This post will be delving deeper into the amazing world of plastic pellets, while we get to understand the options available for plastic parts production. We’re ready when you are.
Xometry offers the highest quality HDPE injection molding service and is able to assist with the design of the part and tooling to ensure it follows DFM (Design for Manufacturing) best practices. This will help ensure the product can be successfully manufactured with no defects. Thereafter, Xometry can facilitate manufacturing with one of our trusted partners to ensure the parts are produced to the required specifications. HDPE is a popular injection molding material as it has excellent processability. HDPE also has a low moisture absorption rate and is lightweight, making it ideal for a wide range of applications.Â
On the other hand, uncontrolled pressure is capable of damaging the mold and as the product can suffer from internal stress.
Fillers such as glass fibers, mineral powders, and carbon fibers are not left out. They improve plastic pellets structurally by reinforcing plastic materials. With such reinforcements, plastic products become triple-strong. Offering durability, strength, and high performance to plastic pellets that lack in such areas.
HDPE is considered food-safe and is approved by the FDA. It is widely used for both single-use and long-term food storage applications. In addition, HDPE is very tough and can protect the food contents during transportation.Â
HDPE is highly resistant to moisture ingress. Also, with the addition of UV (ultraviolet) stabilizers, HDPE can be made resistant to UV radiation, making it an ideal material for outdoor applications.Â
GETTING A QUOTE WITH LK-MOULD IS FREE AND SIMPLE.
FIND MORE OF OUR SERVICES:
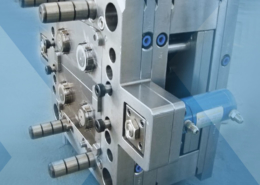
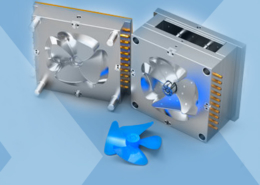
Plastic Molding

Rapid Prototyping
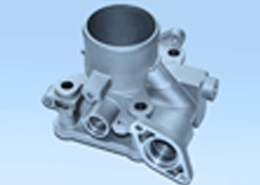
Pressure Die Casting
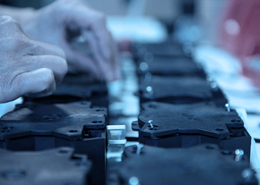
Parts Assembly
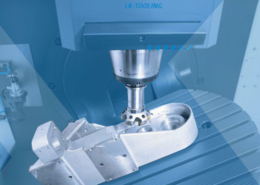