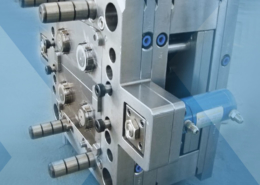
Injection Moulding - injection moulding products manufacturers
Author:gly Date: 2024-10-15
Innovation (state of the art ‘Plastic Injection Moulding’) is at the core of our values and we are always looking to design products that will serve the concrete reinforcing industry and to give our customers a competitive advantage.
We’ve taken direct concern for [our employees] interests, their safety and their comfort. It changes the whole dynamic of the culture
The more knowledge you have, the better prepared you will be to make the best choice. Before making injection molding decisions on current or future projects, get up to speed on Overmolding Fundamentals for OEMs. Click the button below to download your copy of this valuable white paper.
While they share several similar production steps, there are key differences in the techniques. It is these dissimilarities that help determine which process is best suited for a specific application.
Whenever possible, our team go onsite to understand the project's challenges and constraints, so we are better able serve our clients.
To provide context for an accurate comparison of two-shot injection molding and overmolding, a brief overview of each process is necessary:
The newly molded substrate is then transferred either robotically, manually, or via an automated rotary plane to a different cavity within the same tool. In the second phase, the substrate rotates 180 degrees in the tool. Another resin is then injected to surround and molecularly bond to it. Once cooled, the final part is ejected.
In the overmold cavity a second molten material — known as the overmold — is injected around the substrate base. The two layers bond either mechanically or chemically to form the final product.
Two-shot molding consists of two phases (or shots of material) in one injection molding operation. The first phase resembles traditional injection molding. Resin is flowed into one cavity of the tool, and allowed to solidify and cool in order that the substrate holds the proper shape.
Two-shot injection molding (or, two-stage molding) and overmolding are popular choices for many applications. They are also often mistaken as being interchangeable.
Injection-molded parts are integral to the performance and aesthetics of a wide range of products. Manufacturers depend on the expertise of their injection molding partner to guide decisions and processes that lead to desired outcomes.
To make a well-informed decision, it’s important to also consider what may make the injection molding processes less desirable.
With minor design modifications, injection-molded plastic parts can likely be made using either two-shot or overmolding processes. However, the approach to determining which technique is most appropriate for your application shouldn’t be taken lightly.
Overmolding is an ideal solution for commercial and industrial applications such as soft-grip handles on razors, toothbrushes, and handheld tools. In medical and automotive applications, overmolding may be used to decrease vibration, insulate sound, and improve chemical resistance.
Overmolding is a multi-shot process, involving two separate molding operations and two separate tools. It combines a rigid substrate base with a pliable outer layer of plastic such as thermoplastic elastomer (TPE) or liquid silicone rubber (LSR). The substrate base is formed by injecting resin into a tool, where it cools and solidifies before being moved to an overmold cavity within a different tool.
Two-shot injection molding and overmolding are versatile solutions. But, what makes one more practical than the other for a specific application?
Typically, two-shot injection molding is used for complex applications that may require multiple materials or multiple colors. Interior parts in vehicles, appliances and housewares, and device panel push buttons or handle grips exemplify common applications for this process.
Duis aute irure dolor in reprehenderit in voluptate velit esse cillum dolore eu fugiat nulla pariatur. Excepteur sint occaecat cupidatat non proident sunt in culpa qui.
GETTING A QUOTE WITH LK-MOULD IS FREE AND SIMPLE.
FIND MORE OF OUR SERVICES:
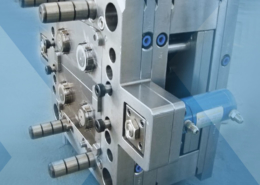
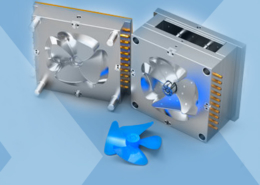
Plastic Molding

Rapid Prototyping
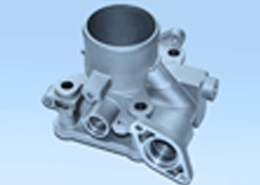
Pressure Die Casting
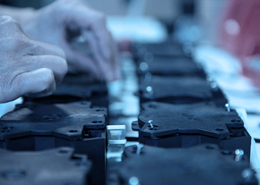
Parts Assembly
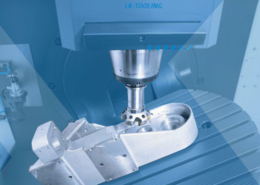