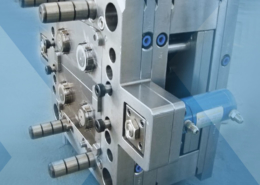
Injection moulding - injection molding dies
Author:gly Date: 2024-10-15
Design and manufacturing of tools is an important part of many industries. By creating the perfect tool, companies can improve their production efficiency and output.
Do you have plastic injection needs?Well, you’re in the right place. Plastic injection moulding and tool making and design are just some of the services that we offer.
You may be wondering what types of industries need the services of a plastic moulding manufacturer such as Anchor Plastics. Well, the answer is: plenty of them, and even some that you wouldn’t think of. We mould the components needed for many of the well-known products in many sectors of Australian industry. Electrical, lighting, swimming pools, water filtration, hospitality, furniture, building, electronic, automotive, housewares, and scientific are just a few examples of some of the many industries that we supply the components for.
After you make the finalised decisions on the design and materials of the plastic part you want, the first step to getting the part plastic moulded is to build the mould.
Our experience in moulding engineering thermoplastics is very well recognized here in Australia. Through knowledge gained by over 40 years building our business in this industry, we are confident of the quality of the advice that we provide. This confidence is important because choosing the right type of materials can often be very critical to a product’s success.
Plastic injection moulding is the preferred manufacturing process when you want or need to make hundreds or thousands of the same plastic part. This process involves heating small plastic beads at a high temperature until they reach a liquid or near liquid state, and then injecting that material under pressure into the cavity of a metal mould.
Anchor Plastics is an Australian owned and operated company that specialises in Plastic Injection Moulding. We are dedicated to providing you, the client, with excellent service, high quality products, and low overall costs. We are also capable of meeting each client’s demanding lead time requirements, as we have 17 plastic injection moulding machines. Our machines range in size from 25 tons all the way up to 550 tons. These machines are running 24 hours a day, 5 days out of the week, moulding items ranging in weight from 1 gram to 2.2 kilograms. So, we are essentially always running the machines and working hard to make sure that we have your product finished in the most efficient and effective way and time that we possibly can.
With fast and economical access to large amounts of HDPE, thanks to long-term relationships with the industry’s top suppliers, Texas Injection Molding purchases and stores large quantities of HDPE in multiple silos, offering economies of scale we pass along to our customers.
A versatile thermoplastic polymer with many cost/performance benefits, HDPE is available. Its overall toughness, flexibility and low temperature impact resistance make it ideal for consumer and industrial products, and FDA grades are appropriate for food, toy and medical applications.
High Density Polyethylene (HDPE) plastic injection molding is made of a workhorse commodity resin that is molded in a variety of uses:
High density polyethylene injection molding has many positive attributes because it’s a strong, low density plastic that can withstand high temperatures.
Do you have a question or need further information about our injection moulding / custom moulding service? Complete the form below and one of our consultants will get in touch with you.
This is a very common question. Another one that you should ask yourself after you ask that one is whether or not you need parts made, and how else you would go about accomplishing that if not by plastic injection moulding.
At Anchor Plastics, all of our products are always assembled and packaged to the highest standards and are thoroughly tested before they are packed and sent to our customers.
This process, the building of the mould as well as the finished product, is one that requires great precision and the use of specialist design software (CAD and CAM) and metal working equipment. The cost of this process varies depending on a number of factors, such as:
GETTING A QUOTE WITH LK-MOULD IS FREE AND SIMPLE.
FIND MORE OF OUR SERVICES:
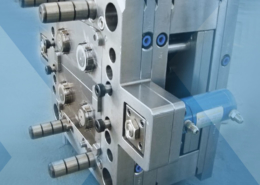
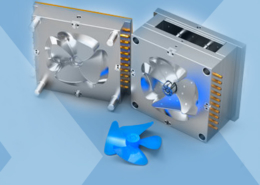
Plastic Molding

Rapid Prototyping
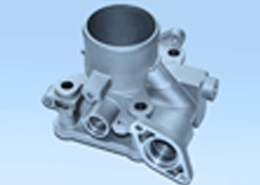
Pressure Die Casting
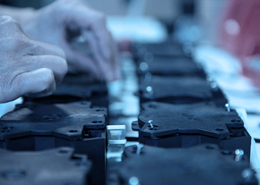
Parts Assembly
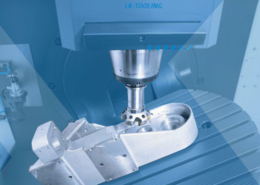