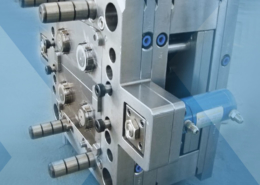
Injection molding with thermal-conductive and EMC shielding - thermal molding pl
Author:gly Date: 2024-10-15
Sulapac Luxe Flex contains 73-86 % USDA certified biobased content1, sustainably sourced biodegradable biopolymers being the main raw material. Sulapac Luxe Flex is safe for people and planet2. It has been certified industrially compostable by TÜV Austria.3 The material is recyclable by design and can also be made with recycled content.4 Available as non-GMO; ask more from your account executive!
Sulapac Solid is a sustainable injection molding material ideal for kitchenware used on a daily basis, such as plates, mugs, bowls and containers. It has high impact strength and it is dishwasher1 and microwave safe. The material is available in natural, white and black color.
1The compostability has been tested up to the thickness of 1,48 mm. As the compostability of an end product is also dependent on the geometry of product, it is the responsibility of the manufacturer of the end product to ensure compliance with the regulations.
Every Fictiv injection molding quote comes with a free DFM report and transparent pricing. Once your order kicks off, our team of program managers and quality engineers will ensure you get fully-inspected, high-quality parts in-hand, delivered on time, according to our rapid production timelines.You can learn more about our injection molding capabilities here and then create your free Fictiv account to request a quote!
3Restrictions and specifications of use apply, please refer to relevant Declaration of Compliance for further information.
T0 parts are inspected for quality and indicate if any final adjustments to the mold or modifications in the press parameters are needed. For a small part, these tooling adjustments can be done in one day, while dialing in the mold for medium or larger parts takes two days.
Our experts are happy to support you in choosing the right material. Contact our sales to discuss more or ask for a quote.
We exist to eliminate bottlenecks in new product development by integrating the people, processes, and platform you need to source custom parts.
The initial phase of mold design involves laying out the part and deciding how it will be oriented when it’s being molded. This layout provides useful information about mold size and the corresponding steel block required to create the tooling.
Fictiv manufacturing partners stock general-purpose grades of plastic that are used most often and obtain other plastics from approved suppliers as needed.
If you’re working with a traditional injection molding supplier, that timeline will typically be about twice as long (this is included in the downloadable template for your reference).
1Material is suitable for repeated use as per European Commission regulation (EU) No 10/2011. Dishwashability tested according to EN 12875 standard with 125 washing cycles.
2 Biodegradation of 56,7% in 280 days in the marine environment ASTM D6691(86°F / 30°C). Not considered biodegradable in California.
As the mold design is finalized and the CNC programming progresses, it’s time to start preparing other materials. If you’re working with Fictiv, at this point the steel for the core and cavity inserts for the mold base has already been ordered and typically arrives in a couple of days.
To maximise the functionality of your end product, there’s a range of material grades you can choose from with different flexural and tensile properties, heat resistance and density. In terms of look & feel, you can opt for a natural appearance with large wood chips or a smooth polished surface, or something in between!
Sustainable innovation approach It all began with a desire. In 2018, LES EAUX DE CHANEL introduced a new olfactory world to the...
The first step of the process is to finalize your designs for injection molding, which encompasses the part as well as the mold design.
Machining itself for the Gantt chart sample part doesn’t take too long, less than one day. This method, combined with our program managers overseeing the schedule, also avoids time lost from the steel sitting in a queue waiting to be machined.
By signing up, you agree to our Terms of Use and Privacy Policy. We may use the info you submit to contact you and use data from third parties to personalize your experience.
Our manufacturing partners combine the rough and finish machining into one step and do both on the same machine, so they can make the cavity, core, and lifter/sliders in only a few days.
Sulapac® materials are the sustainable, beautiful, and functional alternative to conventional plastic. Start using Sulapac with your existing injection molding equipment and gain competitive advantage through sustainability and innovation.
Sulapac Premium is made of wood chips from industrial side streams combined with biodegradable biopolymers. This 100% bio-based material biodegrades without leaving persistent microplastics behind1.
Please note that if the end product needs to be resistant to high temperatures (HDT-B 130 °C)6, the minimum mold temperature is 100°C7.
The copper blocks are also machined at the same time as the steel to ensure the EDM electrodes are available immediately to complete the mold.
1 Sulapac Universal Flex 30 meets the EU and US FDA requirements for food contact materials. Restrictions and specifications of use apply, please ask for Declaration of Compliance for further information.
Access a wide breadth of capabilities through our highly vetted network.
Sulapac Universal Flex 35 is safe for both people and the planet: the material is certified as industrially compostable by BPI1 and leaves no persistent microplastics2 or toxic load behind. Universal Flex 35 meets the EU and US FDA requirements for food contact materials for dry food3 .
Additionally, the longer you wait to make design adjustments, the more likely it is that your team may have limited flexibility to make changes based on other parts in the assembly.
2 Relative biodegradation of 49,7 % in 308 days in simulated marine environment test (ASTM D6691 86 °F / 30 °C) using natural sea water. Not considered biodegradable in California.
The material is processable with existing injection molding machinery. Our experts assist with the tests and production settings from mold selection to nozzle size.
Hopefully, you now have a better understanding of the many steps that go into creating a mold to manufacture your injection molded parts!
Assembly is usually done in the same 24 hours as the precision grinding, mold fitting, and polishing. Typically, Fictiv’s partners complete fitting by day and polishing by night.
This bio-based (87%) material is safe for people and the planet: it is industrially compostable and biodegrades without leaving persistent microplastics behind1.
After a few years of working abroad in Paris and Tokyo, Rebecca Dufour Partanen embarked on a journey that would see her pivot for a...
Some manufacturers use less accurate (and therefore less expensive) machines to do this rough machining before moving the inserts to a high-precision machine. However, in recent years CNC machines have become more precise and less expensive, so the cost savings from using different machines to do rough and finishing cuts are now minimal.
The unique combination of raw materials: responsibly sourced biodegradable biopolymers and naturally occurring clay minerals, gives Sulapac Solid its beautiful ceramic look and feel, even sound, that makes it stand out. Sulapac Solid meets the EU and FDA requirements for food contact materials5 and it contains zero PFAS6.
We exist to eliminate bottlenecks in new product development by integrating the people, processes, and platform you need to source custom parts.
2 Sulapac materials within the same family of recipes show biodegradation of 57,6% at 462 days in the marine environment (30ºC / 86ºF) (ASTM D6691), 28% at 153 days when tested according to ASTM 5511 (99 ºF) accelerated biodegradation in the landfill.
Typically design engineers move onto new projects once an order is placed, which leaves limited resources for any injection molding design corrections should there be issues or concerns (which is common).
For this sample part, the cavity does not require as much EDM as the core side, so once finished, the cavity side can move directly to polishing to save time while the core machining continues.
Combine those strategies with our Gantt chart template, and you can craft an efficient production plan for your next injection molding project.
1 Suitable for reusable applications as per European Commission regulation (EU) No 10/2011. Dishwashability tested according to EN 12875 standard with 20 washing cycles.
First, a fit check is in order. The two halves of the mold, the core, and cavity, are brought together to make sure they line up perfectly because any misalignment could result in flash or parting line mismatch. At the same time, some precision grinding is done on the mold parts to ensure that everything fits and meets the tight tolerances required.
Sulapac Universal Heat 30 is safe for people and the planet: It is made of industrially compostable raw-materials and leaves no permanent microplastic2 or toxic load behind.
Supplements that meet people’s unique needs In developed countries people have better living standards than ever before. A high standard of living has enabled people to focus on their health by using health apps and smart rings....
7 The heat resistance of the end product is dependent on the geometry and the manufacturing process of the product. It is the responsibility of the manufacturer of the end product to test and validate the maximum usage temperature and optimize the manufacturing process.
With Fictiv, you can get T1 samples for an injection molded part like this in 12 business days, which is the timeline we’ll anchor around for the purposes of this article.
2 Ecotoxicity and threshold values for heavy metals tested according to EN 13432. The material complies with the EU and US FDA food contact requirements (restrictions and specifications of use apply, further information in Declaration of Compliance).
Sulapac’s patent pending innovation is a perfect fit for cosmetic brands seeking for a sustainable packaging for water-based formulas. Used as the inner layer of a jar, it provides an excellent barrier against water evaporation and enables you to pack your emulsions in beautiful, bio-based and biodegradable Sulapac packaging. The weight loss of Sulapac Barrier in one year (demonstrated shelf life) is well below 3%1, which is the typically accepted maximum weight loss for cosmetic packaging.
The material contains 100% USDA certified biobased content. Sulapac Solid has low carbon footprint2, and it is certified as industrially compostable by BPI3. It doesn’t leave persistent microplastics or toxic load behind4. Furthermore, the material is certified chemically recyclable by LOOPLA technology.
To finish off the mold materials list, the next step is to source all of the required off-the-shelf components — like screws, nuts, and bolts — plus anything else that’s on the BOM and hasn’t been obtained yet. This is also the time to order the plastic material.
Sustainable innovation approach It all began with a desire. In 2018, LES EAUX DE CHANEL introduced a new olfactory world to the fragrances of the House: a singular collection, inspired by Mademoiselle Coco Chanel’s favorite places,...
3 Raw materials fulfil the requirements for heavy metal tresholds and ecotoxicity according to EN13432 and ASTM D6400.The material complies with the EU and US FDA food contact requirements (restrictions and specifications of use apply, further information in Declaration of Compliance).
Universal material is made of wood from side streams and biodegradable biopolymers. This 100% bio-based material biodegrades without leaving persistent microplastics behind1.
20,57 kg CO2 eq/kg based on cradle-to-gate LCA performed by an independent third-party consultancy (biogenic carbon included).
4 Can be recycled through hydrolysis back to monomers, suitable as feedstock for recycled biopolymers. Mechanical and chemical recyclability tested and proven technically feasible by third parties. Field tests have also verified that Sulapac materials can be collected and sorted out of a mixed waste stream. When collected together, Sulapac materials do not interfere with the current mechanical recycling of conventional fossil- based or bio-based non-biodegradable plastics. The technology for chemical recycling of bio-based and biodegradable materials exists, but the infrastructure is still under development.
2Biodegradation of 79% in 308 days in the marine environment (30 °C / 86 °F) (ASTM D6691). Tested according to ASTM 5511 (accelerated biodegradation in the landfill 37°C / 99 °F): 52% relative biodegradation in 210 d. Not considered biodegradable in California.
6Sulapac Solid has been tested for per-and polyfluoroalkyl substances (PFAS) by an independent laboratory (ISO/IEC 17025 certified) based on CEN/TS 15968 test method; No PFAS compounds were detected.
Sulapac materials for injection molding are sustainable alternatives for PS, ABS, PC and PP. They can be used for various applications including cosmetic packaging, kitchenware, and cutlery.
4Relative biodegradation of 77,3% in 420 days in simulated marine environment test (ASTM D6691 86 °F/30 °C) using natural sea water. Not considered biodegradable in California
By signing up, you agree to our Terms of Use and Privacy Policy. We may use the info you submit to contact you and use data from third parties to personalize your experience.
By signing up, you agree to our Terms of Use and Privacy Policy. We may use the info you submit to contact you and use data from third parties to personalize your experience.
The next material to prepare is the mold base. A mold base encloses the core and cavity parts of the mold itself and helps absorb the pressure from the injection process. The mold base is often made of a softer steel than the core and cavity because it’s cheaper than the harder steel used for those inserts.
How long will it take to go from the initial part designs to your first molded parts? This is a long and complicated process that can intimidate many an engineer.
Replace your traditional plastic material and start mass-producing truly sustainable products with minimal investment. Universal material is designed to fit to existing production lines and molds. It is suitable for rigid products such as jars and hangers. Technical specification and easy processing instructions are available in the technical datasheet.
The material is processable with existing injection molding machinery. Our experts assist with the tests and production settings from mold selection to nozzle size.
That’s why we recommend customers engage early on in the process to start optimizing their designs for injection molding, which can take significant time. For more tips here, check out our Injection Molding Design Guide.
3 Fully biodegradable in simulated marine environment tests according to ISO 22403 and ASTM D6691. Relative biodegradation of 100% (ISO 22403, 27°C / 80°F) and 92% (ASTM D6691, 30°C / 86°F) in 56 days using natural sea water. Not considered biodegradable in California.
The Sulapac Premium material makes your products look and feel luxurious. This grade of Premium is more flexible and has a better impact strength. The visible wood chips and haptic touch make it stand out. It is ideal for brands that value sustainability while aiming for that exclusive feel.
Sinker EDM creates super fine details like text or internal features that are difficult or impossible to make with a CNC machine.
1Biodegradation of 48%–59% in 280 days in the marine environment (30ºC/86ºF) (ASTM D6691). Tested also according to ASTM 5511 (accelerated biodegradation in the landfill, 37ºC/99ºF): 68% relative biodegradation in 160 days. Not considered degradable in California.
By working on different aspects of the mold in parallel, the mold creation process becomes a good deal more efficient — by 5 or 6 days — when compared to a more linear approach.
Relative biodegradation of 70% in 58 days when tested in simulated solid-state anaerobic condition (ASTM D5511, 37°C / 99 ºF) representing an accelerated biodegradation in a landfill.
Then the cavity, core, lifters, sliders, and inserts go through the sinker EDM process using the machined copper electrodes.
After a few years of working abroad in Paris and Tokyo, Rebecca Dufour Partanen embarked on a journey that would see her pivot for a fashion and beauty startup in New York and return home to Stockholm with a fresh idea for her own slow...
In this step, it’s a good idea to spend a little extra to get core and cavity inserts that are already the exact sizes you need — it saves time that would otherwise be spent grinding it down to get the right fit. Those sorts of adjustments can take days you can’t afford when your development cycle is on a tight deadline.
Sulapac Universal Heat 30 is a sustainable, beautiful, and functional material for injection molding containing 70% USDA certified biobased content. The material is optimized for high heat resistance without additional or post-treatment, with ideal flexural strain and impact strength, making it a great option for single-use and reusable cutlery1 with outstanding usability.
By signing up, you agree to our Terms of Use and Privacy Policy. We may use the info you submit to contact you and use data from third parties to personalize your experience.
By signing up, you agree to our Terms of Use and Privacy Policy. We may use the info you submit to contact you and use data from third parties to personalize your experience.
Sulapac® materials can be used with existing injection molding machinery, enabling a resource efficient transition towards a cleaner future.
After CNC machining the finer details into the mold components, the final touches are made to the geometry. This requires electrical discharge machining (EDM) to achieve certain geometries that cannot be created with a CNC mill. For example, wire EDM is used to cut gear teeth with sharp internal corners and square holes.
1 Material version with USDA Certified Biobased Product label (certification mark of the U.S. Department of Agriculture) available.
The first parts made with a mold are called T0 parts, and they show how the mold and all of the press parameters are working.
Once the material arrives, it’s time to start machining the mold. The core and cavity are machined from the prepared steel blocks, and the process starts with rough CNC machining using larger cutting tools to cut a rough outline.
The example timeline in the gantt chart is based on the sample part shown below using a single cavity mold. The overall part size is 95.520 x 55.541 x 16.500 mm, made of a general-purpose PC/ABS plastic that’s black and has a matte SPI-B1 finish. The tooling will be made from P20 steel, with a cold runner and automatic side action.
Once the steel arrives, initial work starts to prepare the steel for machining. The steel blocks need to be faced off so that all edges are perpendicular to each other and have a smooth surface to begin machining. This step can take 2-3 days and is needed before the CNC machining can begin.
Finally, it’s time to assemble the mold and bring together the mold core and cavity, any sliders, lifters, or inserts, and the nuts and bolts that connect it all.
By signing up, you agree to our Terms of Use and Privacy Policy. We may use the info you submit to contact you and use data from third parties to personalize your experience.
The Universal Flex 30 is ideal for single-use and reusable cutlery that ensures easy mass-manufacturing and outstanding usability. Beautiful and sustainable option for injection molding. Ideal flexural strain and impact strength for complicated designs like knives and forks. Suitable for food contact according to EU and FDA.1
Once the mold cavity, core, and other parts have been machined, it’s time to move onto the finishing touches, so we can actually manufacture some parts!
Once the mold is loaded in the press, Fictiv’s supplier quality engineers and manufacturing partners continually monitor the process to ensure it’s delivering the quality you need.
One of the key tools our technical program managers at Fictiv use to keep injection molding programs on track is a detailed gantt chart.
Once the CNC programming is done, it’s time to order the copper material for any EDM (electrical discharge machining) required by the design. This copper will be used to make the electrodes for sinker EDM.
4 Can be recycled through hydrolysis back to monomers, suitable as feedstock for recycled biopolymers. Mechanical and chemical recyclability tested and proven technically feasible by third parties. Field tests have also verified that Sulapac materials can be collected and sorted out of a mixed waste stream. When collected together, Sulapac materials do not interfere with the current mechanical recycling of conventional fossil-based or bio-based non-biodegradable plastics. The technology for chemical recycling of bio-based and biodegradable materials exists, but the infrastructure is still under development.
Sulapac® materials are the sustainable, beautiful, and functional alternative to conventional plastic. Start using Sulapac with your existing injection molding equipment and gain competitive advantage through sustainability and innovation.
And while we’re on the subject of mold bases, let’s talk about the interchangeable sort. Mold bases are often made in standard sizes that can hold a number of different mold cores and cavities. If you have a mold base available that was used for other projects, then you don’t need to spend the time or labor to make a new one. Some minor adjustments to that existing base may be needed, but overall, using an interchangeable base saves you a lot of time.
Sulapac Luxe is the ultimate answer for brands looking for a sustainable yet luxurious replacement for hard plastics like ABS. Sulapac Luxe is ideal for fragrance bottle caps, jars, and lids.
It’s common practice in the industry for molding suppliers to hold back design for manufacturability (DFM) feedback until after an order is placed. But this is where the most time in a project can be lost.
Sulapac Luxe contains 73-87% USDA certified biobased content1, sustainably sourced biodegradable biopolymers and non-visible wood flour from industrial side streams being the main components. The material is safe for people and the planet: it leaves no persistent microplastic2 or toxic load3 behind. Sulapac Luxe is recyclable by design4 and can also be made with recycled content.
3 Restrictions and specifications of use apply, please refer to relevant Declaration of Compliance for further information.
Accelerate development with instant quotes, expert DFM, and automated production updates.
The material has high density, good resistance to temperature fluctuations and a unique, ceramic look and feel, even sound. With Luxe both shiny or a matt surface can be achieved depending on your mold selection.
1 Sulapac materials within the same family of recipes show biodegradation of 26-60% at 140 days in the marine environment (30ºC / 86ºF) (ASTM D6691).
If the plastic you need is a specialty grade, Fictiv can source it for you. However, specialty-grade plastics can have longer procurement lead times and aren’t always available. Additionally, it takes longer for specialty plastic material to arrive than it does to machine the mold. So, it’s critical to determine early on if you’re going to use a specialty grade of plastic and consider ordering it before the part designs are finalized and the tooling order is released.
In this article, we’ll walk you step by step through the injection molding process from start to finish and share with you the strategies we use with our customers to help save time and avoid potential pitfalls common to this complex manufacturing process.
By signing up, you agree to our Terms of Use and Privacy Policy. We may use the info you submit to contact you and use data from third parties to personalize your experience.
Replace conventional plastic with the beautiful, functional and sustainable Sulapac material. We will help you to make the switch smoothly.
After confirming that all the pieces fit well, the next step is to give the mold the right finish. This often means polishing it to a specified level of smoothness, or adding different textures when required. Whether or not the end goal is a polished surface finish, some polishing is always required to remove machining marks and provide a smooth surface upon which to add textures.
This article will go deep into each of those gantt chart steps to help you understand the process. Plus, we’re making our template available for you to download for free here, which you can use to plan out your own program.
5 As the compostability of an end product is also dependent on the geometry of product, it is the responsibility of the manufacturer of the end product to ensure compliance with the regulations.
For any engineering project, countless hours go into 3D modeling, prototyping, and refining the design. Often, the final step is to prepare your designs for the injection molding process, but where do you start?
3The compostability has been tested up to the thickness of 150μm according to BPI (ASTM D6400). As the compostability of an end product is also dependent on the geometry of product, it is the responsibility of the manufacturer of the end product to ensure compliance with the regulations.
Finally, once the part design is confirmed, CNC programming begins, while the cooling lines and ejector pin holes are drilled. A CAM (computer-aided manufacturing) program is used to develop the G-code that will run the machine to make the mold parts. This milling process takes about two days and can begin once the DFM is approved and 3D CAD modeling starts.
Supplements that meet people’s unique needs In developed countries people have better living standards than ever before. A high...
The Sulapac Premium material makes your products look and feel luxurious. The ceramic sound and visible wood chips’ haptic touch make it stand out. It is ideal for sustainable products that aim for an exclusive feel.
4 Restrictions and specifications of use apply, please refer to the relevant Declaration of Compliance for further information.
Sulapac Luxe Flex is a sustainable material for injection molding ideal for replacing hard plastics like ABS. Luxe Flex can be used to manufacture fragrance caps, cosmetic jars, lids, compact powder boxes, and pencils, for example. The material is resistant to temperature fluctuations, has a high density and a premium look and feel, even sound. With Sulapac Luxe both shiny and matt surface can be achieved depending on your mold selection. The material has excellent processability and it is easy to color with Sulapac masterbatches. Luxe Flex is now also available as black granules!
5Restrictions and specifications of use apply, please refer to the relevant Declaration of Compliance for further information.
The next phase of mold design is to flesh out details like finalizing the design of the core and cavity and building a complete BOM (bill of materials) with all of the small parts and other components needed. After creating a 3D CAD model of the mold, (which takes one to two days depending on the size and complexity of the part) the 2D drawing is completed in another day or two.
It’s especially critical to know the size of the steel block because that way your supplier can order and ship the steel before the design of the tool is finished.
Sulapac Universal Flex 35 is a sustainable, beautiful, and functional injection molding material which contains 87% USDA certified bio-based content. The material is designed for thin-walled structures with good impact strength and is easy to process with minimal, if any adjustments needed for the existing machinery.
Our trained employees ensure your parts will be delivered on time and to spec.
Create high quality custom mechanicals with precision and accuracy.
Sulapac Barrier contains 98% USDA certified biobased content2 and biodegrades without leaving persistent microplastics3 or toxic load behind. The material is food contact compliant4 and certified industrially compostable by BPI5.
GETTING A QUOTE WITH LK-MOULD IS FREE AND SIMPLE.
FIND MORE OF OUR SERVICES:
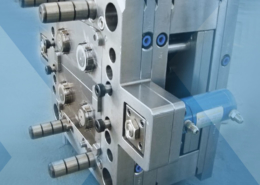
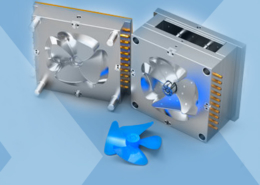
Plastic Molding

Rapid Prototyping
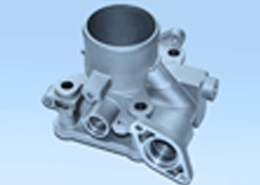
Pressure Die Casting
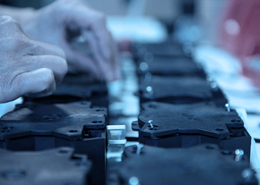
Parts Assembly
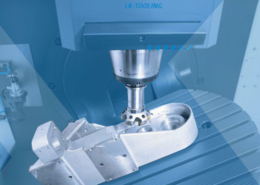