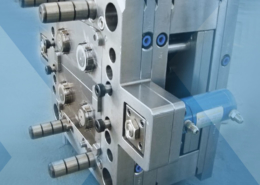
Injection molding wall thicknesses - tips? - thick wall injection molding
Author:gly Date: 2024-10-15
Polypropylene is one of the more commonly used injection molding resins for a reason: It’s extremely versatile and has a number of applications for which it’s suited. In addition, polypropylene injection molding parameters, such as melt temperature and viscosity, lend themselves to relatively easy, cost-effective production in a wide range of uses.
In this article, we’ll take a detailed look at polypropylene injection molding: when it can be used, what products and applications it’s most suited for, and what the advantages of using it are. As you read through, remember that with the wide variety of plastic resins available from which to choose, there’s no textbook “best solution” — it always depends on your specific needs. Polypropylene is one of the more versatile and commonly used materials available, which is why we’re focusing on it today, but it’s important to always compare the advantages and disadvantages of any material against the requirements of your project.
Polypropylene, as mentioned above, is a cost-effective material on a raw material basis. Although resin prices fluctuate based on supply and demand, polypropylene will almost always be a competitive option — provided that it meets your product requirements. Some secondary cost benefits of polypropylene include:
RevPart is ready to answer any questions you have about the benefits of polypropylene, and any other material selection inquiries. Contact us today.
With so many versatile applications, polypropylene is thus well-suited to a broad range of product types, as well. One of the most common uses is the living hinge — a one-piece hinged construction commonly seen in products like caps for consumer products (think of the flip-top on a mustard bottle). The living hinge is one of the most important innovations in plastic injection molding, and polypropylene is probably the most ideal resin for the job. This is mainly on account of its high property of flexibility — ability to bend multiple times — hundreds or thousands — without breaking.
At the outset, only you understand the different weight that each of these factors has in the calculus of material choice for your specific project. Of course, it’s important to share this information with your manufacturing partner so that it can best assist you in choosing the right material.
As a quick refresher, before we begin our deep dive into polypropylene, just a few of the factors that might drive your material choice include:
GETTING A QUOTE WITH LK-MOULD IS FREE AND SIMPLE.
FIND MORE OF OUR SERVICES:
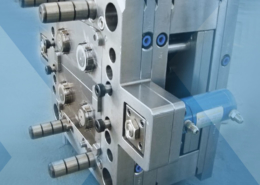
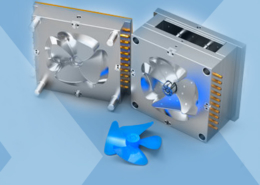
Plastic Molding

Rapid Prototyping
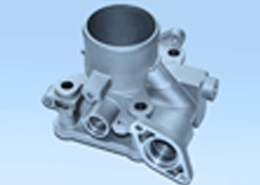
Pressure Die Casting
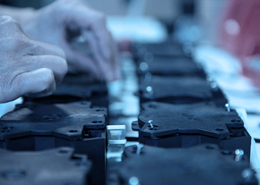
Parts Assembly
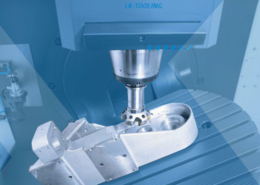