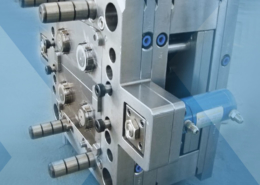
Injection Molding Tools - plastic injection mold tooling
Author:gly Date: 2024-10-15
2. Increase the outer diameter of the single-section ejector pin. If there is sufficient space in the mold, you can increase the diameter of the corresponding mold core hole, B plate, and ejector retainer plate hole to provide better support and stability.
To ensure proper functionality and avoid any interference, it is recommended to maintain a minimum distance of 3.5mm between the waterline and the ejector pin. This distance allows for sufficient clearance and prevents any potential contact or collision between the ejector pin and the waterline during the ejection process. By maintaining this distance, the mold design can effectively accommodate the necessary components and promote smooth and efficient ejection without compromising the integrity or performance of the mold or the injected part. (Please refer to the following picture.)
3. Consider using double-section ejector pins instead of single-section ones. Double-section ejector pins offer increased strength and resilience, reducing the risk of fracture compared to their single-section counterparts.
Ejector pin oil is generally a high-quality guide rail lubricant, with a tough, non-loss oil film, excellent lubrication, anti-rust, and anti-creep performance, used for the lubrication of plastic mold ejector pins (push rods).
As one of the most versatile methods for plastic part production, plastic injection molding has numerous advantages over other plastic molding methods. Custom plastic injection molding is not only a more straightforward and more reliable process than others, but it also offers the following benefits:
2. Determining Machine Injection Pressure: Based on the model and specifications of the injection molding machine, the injection pressure of the machine needs to be determined. Injection pressure is one of the key factors influencing the number of ejector pins.
During the process of demolding, if the ejector pin faces too much resistance or retracts poorly, ejector pin oil should be sprayed. A person should be assigned daily to spray the ejector pin oil on the ejector pins. This should happen at scheduled times, at least once per shift, for lubrication/protection.
1. Analyzing the Structure and Processing Requirements of Injection Molded Parts: Understanding the structure of the molded parts, including characteristics such as wall thickness, holes, protrusions, and processing requirements such as the need for support removal and punching, is crucial. These factors significantly influence the required number of ejector pins.
4. If possible, consider canceling the ejector pin if it won’t affect the ejection process. This step can be taken to avoid further complications.
For the even distribution of ejection forces, it is recommended to evenly distribute the ejector pins across the mold. However, when the product ejection surface does not have any specific appearance requirements and is located in a suitable position, it is preferable to use larger ejector pins. This choice helps to distribute the ejection force more effectively and ensures proper ejection of the molded part. By using larger ejector pins strategically, the mold design can optimize ejection performance and enhance the overall efficiency of the injection molding process. (Please refer to the following picture.)
These pins typically have a hardness ranging from 50 to 55 degrees and undergo surface hardening and nitriding treatments.
2. Enhance the surface finish around the male mold and the groove area of the rib. Polishing these surfaces or incorporating a demold slope can facilitate smoother ejection, reducing the strain on the ejector pins and decreasing the likelihood of breakage.
The varying plastic types used in custom injection molding allow for various melting points required for different applications.
Many businesses turn to injection molding for high-volume, intricate parts. The process provides many benefits, including a high production level while minimizing the cost per unit. To determine if custom plastic injection molding suits your application, you should understand the varying materials and surface finishes available.
To ensure effective operation and prevent any interference, it is important to position the ejector pin in such a way that the ejector cup does not pass through the hole of the ejector plate when it is close to the support pillar. This principle ensures that the ejector cup remains properly aligned and does not obstruct the movement of the ejector plate. By adhering to this design consideration, the mold can function smoothly, allowing for efficient ejection of the molded part without any potential complications or malfunctions. (Please refer to the following picture.)
Sometimes it is necessary to process the burrs at the ejector pin position, and even needle breakage may occur, hindering the smooth progress of production.
Material SelectionThere are various materials to choose from when it comes to plastic injection molding. To ensure your parts perform as needed, the experienced team at Rodon can guide you in selecting the proper material for your unique plastic injection molding project.
Ejector pins in molds are typically made from high-speed steel and undergo subsequent heat treatment. There are various grades available in the market, with commonly used ones being SKD61 and SKH51.
These pins undergo heat treatment in a vacuum nitriding furnace, resulting in high-quality SKD61 material with excellent hardness, heat resistance, and consistency in both internal and external hardness. They are an excellent choice for molds with high requirements for ejector pins due to their superior raw material quality, but they come at a higher price compared to the previous options.
If you find some of the above ejector pin design suggestions too complicated, you may consider the following simple advice:
The Rodon Group is an industry-leading custom plastic injection molding provider, creating billions of high-quality parts and components for various industries. We are proud to be a United States manufacturer, and with over 125 injection molding presses, we are considered one of the largest family-owned plastic injection molders in the U.S.
1. Place ejector pins in areas where it’s difficult for the product to be removed from the mold, and ensure they are evenly distributed to exert uniform force on the product, avoiding deformation during ejection.
Comprehensive ApproachRodon consistently considers all aspects of the manufacturing process, from mold design to injection molding methods. This approach is part of our concept-to-completion strategy, which ensures optimal quality from the initial design phase. Following this method involves a strong understanding of the practical and technical aspects of plastic injection molding.
2. When the surface being ejected by the ejector pin is not flat but instead inclined or curved, anti-rotation treatment is needed for the ejector pin.
1. Increase the number of ejector pins in areas where breakage is more likely, especially in regions with limited space. By distributing the ejection force among multiple pins, the stress on each pin is reduced, minimizing the risk of breakage.
Toolmaking and Precision ToolingManufacturing a high-quality tool requires precision, accuracy, and time. Since it can be a significant investment in the manufacturing process, Rodon is committed to getting it right to ensure the success of your project. We offer the following advantages with our precision tooling capabilities:
Ejector pins are a piece of knowledge that industrial product designers need to master because injection-molded products usually leave an ejector pin mark after injection molding is completed. As a result, product designers need to consider the ejector position of plastic products when designing products. Now, we will start the ejector pins of injection mold parts.
Ejector pins are commonly used in the ejector system of injection molds. Like the mold base, they are not typically a focal point for either mold manufacturers or injection molding factories. Therefore, most mold manufacturers purchase ejector pins externally.
Rodon offers a wealth of custom plastic injection molding knowledge and experience, taking a comprehensive approach to part design while featuring the following capabilities.
Quality ControlOur quality control checks play a vital role in our manufacturing process, and we conduct them at every phase of production. These checks include an assessment of color accuracy, tolerances, strength, part defects, and the overall physical appearance of a product. Our comprehensive approach to quality control is essential to maintaining high standards in our manufacturing processes.
When the ejector is positioned on a curved surface, it is essential to incorporate anti-rotation protection for the cup. This design prevents unwanted cup rotation during the ejection process, ensuring it remains properly aligned and engaged with the ejected part. The cup can effectively resist rotation forces and maintain its intended orientation by incorporating anti-rotation mechanisms or features, such as guide pins or keyways. This design principle helps to enhance the reliability and accuracy of the ejection system, minimizing the risk of misalignment or damage during mold operation. (Please refer to the following picture.)
The knowledge about the use of ejector pins in molds and injection molding is a profound subject. It requires a great deal of time to master. The ejector pin knowledge discussed in this article is relatively basic. There are many advanced topics we haven’t covered, such as the coordination between ejector pins and sliders, as well as the integration of ejector pins with lifters, among others.
To optimize the performance and durability of the ejector pin, it is recommended to position it in a flat orientation, avoiding areas with R angles, sharp angles, steep slopes, and locations too close to the gate position. By ensuring a flat and suitable placement, the ejector pin can exert consistent and efficient ejection force without encountering unnecessary obstructions or potential damage to the mold or the ejected part. This design consideration enhances the overall functionality and reliability of the mold, contributing to smoother injection molding processes and improved product quality. (Please refer to the following picture.)
To accommodate cross-shaped or deeper ribs without causing sink marks or affecting the product, additional material can be added using the method illustrated in Figure C. This approach allows for the proper filling of the mold cavities and ensures that the resulting molded product retains its intended dimensions and structural integrity. By strategically applying this technique, the mold design can effectively address the challenges posed by complex rib configurations and produce high-quality molded parts. (Please refer to the following picture.)
4. Estimating the Number of Ejector Pins: Combining the above data with practical experience, estimate the appropriate number of ejector pins. Generally, the number of ejector pins should be greater than or equal to the mold cavity area divided by the injection pressure, further divided by the ejector pin pressure value. However, it is essential to avoid overly dense ejector pin arrangements to prevent excessive scrap rates.
For injection molding manufacturers, there is another point to note. During the injection molding process, the ejector pin and the ejector pin hole rub against each other. If the ejector pin is not frequently lubricated with ejector pin oil, the ejector pin will burn out or wear. Additionally, the ejector pin hole will wear and enlarge, leading to burrs and affecting product quality (or assembly).
Additionally, there are ejector pins made from ordinary high-speed steel, which are used in less demanding applications. The prices of ejector pins vary significantly in the market, with those from branded manufacturers being more expensive.
Manufacturing/ CleanroomOur state-of-the-art facility includes 125 fully automated presses. Our production schedule runs seven days a week, 24 hours a day, for most of the year to ensure optimal efficiency.
DesignOur design team has over three decades of industry experience building and designing top-quality molds. Advanced design software, such as Solid Works, allows us to quickly and easily modify and assess part designs to meet our customers' exact specifications. Our team focuses on understanding the precise function, use, and requirements of every part to ensure it will function as needed in its intended environment.
The quantity of ejector pins significantly affects both the quality of injection molded parts and production efficiency. Insufficient ejector pins can lead to defects such as voids and sink marks within the molded parts, thereby reducing product quality. Conversely, an excessive number of ejector pins not only increases mold manufacturing costs but also decreases injection molding production efficiency, potentially causing sluggish machine actions or even jamming.
For product designers, perhaps understanding the working principle and layout basics of ejector pins is already sufficient. This knowledge can help them avoid some poor designs related to the appearance of plastic products in industrial design. That’s all for today’s share. If you’re interested in molds and would like to discuss further, feel free to email me at [email protected].
These pins offer improved hardness and heat resistance compared to regular SKD61 material. They are favored by many customers and are priced slightly higher than Chinese SKD61 pins.
Remember to assess the situation carefully. Choose the appropriate method based on the specific circumstances to effectively address the broken ejector pin issue.
1. Opt for high-quality ejector pins made from good materials. Choose ejector pins that have undergone heat treatment and surface nitriding to enhance their strength and durability.
These are the most common ejector pins available, with average hardness and heat resistance. They are suitable for molds where precision and hardness requirements are not too high, and they are relatively more affordable.
It’s worth mentioning the fact that mold suppliers can receive ejector pins from their supplier but still, it’s very important to pay enough attention to the design considerations for ejector pins when the company is designing the mold. Design plays a crucial role in providing the best ejection mold function without causing any problems like part sticking or damage. Here are the fundamental visual design principles:
Made from high-speed steel, SKH51 ejector pins are chosen by mold factories when high requirements are placed on the pins. SKH51 is a tungsten-containing high-speed steel known for its excellent heat resistance, toughness, and hardness, making it an ideal choice for demanding applications.
Before the mold design, the ejector pin position is a matter of concern, favoring as much as possible its arrangement near ribs or points with high ejection force expected. In this respect, this positioning of strategic purpose is an important factor in the use of forces with all critical points so that it is possible to eject the molded part easily and precisely. Thus, this will achieve effective and reliable ejection without causing damage or deformation of the part. By pin-placing these selected positions on the mold design, the result could improve the ejection process and increase the overall success of injection molding.
At The Rodon Group, we are a leading U.S. provider of custom plastic injection molding services. We are ISO 9001:2015 and ISO 13485-certified to ensure the highest level of quality for every project, and our comprehensive capabilities allow us to meet the needs of many industries. Regardless of your needs, the experts at Rodon can deliver superior injection-molded components that adhere to tight tolerances.
3. Calculating Mold Cavity Area: Using the structure of the molded parts and injection pressure, calculate the required mold cavity area. The mold cavity area serves as an important reference data point for establishing the upper limit on the number of ejector pins.
Positioned in the ejector plate in the mold/die, the ejector pin extends into the mold core and applies force to push the molded part out when the mold opens. Ejector pins vary in size, shape, and configuration to accommodate different mold designs and part geometries. Their precise placement and effective operation are essential for efficient part ejection and overall mold performance.
Contact us to learn more about the cutting-edge plastic injection molding services we offer. You can also request a quote to work with us on your next custom injection molding project.
To prevent difficulty in removing the product and ensure easy ejection, it is advisable to avoid placing the ejector pin too close to the edge of the product, especially when the product shrinkage is significant.
An ejector pin is a cylindrical component used in injection molding to remove the finished parts from the mold core. It is usually made of steel alloy and built for high pressures and repetitive motion durability.
2. In the case of a jammed pin, use a drill bit to make a hole and then knock out the remaining portion. This method is suitable for soft-material ejector pins.
Therefore, it is recommended for injection molding manufacturers to regularly and timely spray ejector pin oil on the ejector pins for lubrication and protection.
GETTING A QUOTE WITH LK-MOULD IS FREE AND SIMPLE.
FIND MORE OF OUR SERVICES:
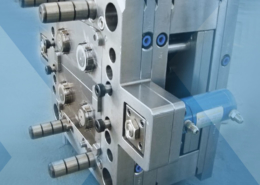
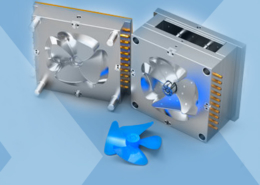
Plastic Molding

Rapid Prototyping
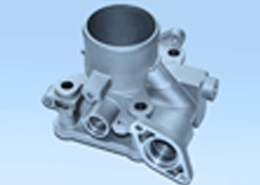
Pressure Die Casting
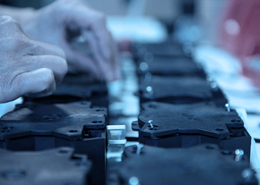
Parts Assembly
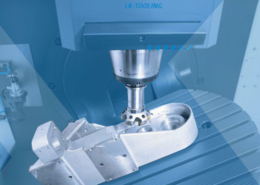