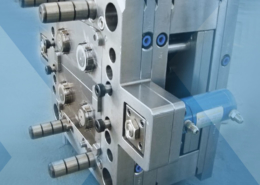
Injection Molding Tooling | A Comprehensive Guide - plastic mold tooling
Author:gly Date: 2024-10-15
When heated far above its melting temperature, ABS will release toxic fumes, which are both pollutants and a health concern to those who inhale them. This concern is pertinent to injection molding applications where potentially hundreds of kilos of ABS a day are heated and where tight temperature controls must be used to prevent smoke evolution and toxic off-gassing.
ABS plastic will degrade in the presence of ultraviolet (UV) light, such as those radiating from the sunâthat is, unless it is formulated with UV resistance in mind where it is alloyed with another polymer or otherwise treated with UV resistant strengtheners. ABS is, therefore, not a good material for outdoor equipment by itself, requiring these additives to function.Â
General fittings and fasteners made from ABS plastic molding are inexpensive, plentiful, and can be designed with complexity in mind.
Recreational goods such as sports equipment, toys, models, furniture components, and other products all benefit from the cost-effectiveness of ABS injection molding, offering a variety of complex shapes for consumers that are well within their budgets.
Appliances like kitchenware, vacuum cleaners, washing machines, and other household tools benefit from the aesthetic-yet strong profile of ABS injection molded parts. Just as with other applications, this process can help decrease the price of these tools while also providing more profit to suppliers.
ABS plastic can achieve a variety of colors and a high gloss finish with the use of acetone vapor or other finishing processes. ABS plastic is, therefore, an ideal plastic for toys, models, and other applications where looks are of key importance.
Choose from millions of possible combinations of materials, finishes, tolerances, markings, and certifications for your order.
Though resistant to temperatures up to 100 °C, ABS plastic generally does not like heat and has a range of temperatures where it is not easily controllable. This makes ABS injection molded parts non-ideal for heat exchangers or other components that will regularly experience cycles of heat above its service and heat deflection temperatures.Â
ABS plastic molding is ideal for building electronic housings and non-conductive components. Not only is it insulative, but it can be injection molded into highly complex shapes and in a variety of aesthetic colors and finishes. ABS injection molding also reduces the overhead costs for the high-volume manufacturing of personal electronics.
Below is a table containing the material property ranges across various ABS plastics and ABS resins (general ABS, high impact ABS, low viscosity ABS, plate-able ABS, and other unique blends). Note that each ABS formulation will have a unique set of material properties depending on their intended application, and the table below provides a wide range of material characteristics.Â
ABS plastic is dimensionally stable at ambient temperatures up to its maximum service temperature. This advantage makes ABS valued as a cost-efficient material for applications where other plastics would bend or warp under similar conditions, such as fittings, vacuum system components, or housings.
If your projects require subtractive manufacturing processes, Xometry provides highly accurate and expedient ABS CNC machining for your parts. To learn more, view our capability page on our ABS CNC Machining Service.Â
Fused Deposition Modeling (FDM) 3D printing offers a high-volume, low-cost alternative to injection molding. ABS FDM 3D prints can achieve comparable design complexity to ABS injection molding and also offers a wide range of thermoplastic blends to choose from. To learn more, view our capability page on our ABS FDM 3D Printing Service.Â
ABS plastic will retain its stability and rigidity under load up until its heat deflection temperature, making it useful for load-bearing applications such as brackets, fasteners, snap fits, and other load-carrying applications.
If the size of parts is of primary concern and not necessarily the material, then large part injection molding offers a variety of materials for the biggest of ideas. Designers can choose from general-use plastics to engineering materials that can be made in sizes much larger than the typical injection molding machine. To learn more, view our capability page on our Large Part Injection Molding Service.Â
ABS plastic easily incorporates into other polymers to form alloys, where ABSâs rigidity, scratch resistance, and dimensional stability are paired with another polymerâs attributes to make a material better than its sum. This ability has allowed the formulation of another highly popular polymer blend, PC-ABS, which retains ABSâs strength but is also more resistant to heat and impacts. This makes ABS an attractive choice for polymer manufacturers when making application-specific plastic grades.
Here are the typical design guidelines for ABS plastic injection molding. Note that these are general guidelines for the ABS injection molding process that may not accurately represent specific ABS plastic blends. Our Manufacturing Supplier Network of over 10,000 global partners can work outside these guidelines if they donât fit your project requirements.
We are ISO 9001:2015, ISO 13485, and AS9100D certified. Only the top shops that apply to become Suppliers make it through our qualification process.
Resistant to aqueous acids, alkalis, concentrated hydrochloric and phosphoric acids and animal, vegetable and mineral oils, but but weak to carbon tetrachloride, aromatic hydrocarbons, and concentrated sulfuric and nitric acids
The disadvantages of ABS plastic injection molding include poor temperature control, poor chemical resistance to certain substances and environments, poor friction and wear resistance, and a tendency to off-gas toxic fumes when heated. For more information, see below:
The advantages of the ABS injection molding process include impressive dimensional stability and stability under load, its ability to be alloyed by other polymers, recyclability, and its aesthetic properties. For more information, see below:
Xometry offers high-quality acrylonitrile butadiene styrene (ABS) plastic injection molding services for a variety of industries. Acrylonitrile Butadiene Styrene is a thermoplastic polymer that is easily worked, durable, and highly aesthetic. The ABS plastic injection molding process injects molten ABS under high temperature, and injection pressure into an injection mold, where the injected molded ABS parts are released and ready for use once cooled. Xometryâs ABS injection molding services are highly popular, as the high-volume plastic injection molding process combined with the low cost and material characteristics of ABS is ideal for industrial applications.Â
ABS is generally not specified for its friction or wear resistances, especially when considering its tendency to weaken when heated. Some blends attempt to remediate this weakness with additives like carbon fiber. However, pure ABS is not suitable for injection molded parts for bearings, friction components, or otherwise high-wear environments.Â
ABS experiences severe effects with acetone, carbon tetrachloride, aromatic hydrocarbons (including fuel oils), and concentrated sulfuric and nitric acids. In the presence of these substances, ABS plastic will swell or may dissolve completely, making it unsuitable for chemical containers or handling equipment that may be in contact with a variety of organic and inorganic chemicals, such as injection molded parts for chemistry labs.Â
Automotive applications leverage ABS plastic molding to fabricate parts from interior components to switches even to engine components like clasps and fasteners. In larger injection molding machines, ABS can even be used to make door or body components. The economic efficiency per part of both injection molding and ABS make it ideal for high-volume applications like vehicle manufacturing.
Get custom ABS molded prototypes and production parts in as few as 10 business days. We provide expert engineering reviews and $500 off your first mold. Dozens of materials and finishes are available.
Once the life of an ABS plastic part is complete, it can be fully recycled back into ABS material by grinding the part and re-melting it into stock material alongside new ABS. The recycled ABS cannot be melted down into new stock by itself and requires fresh ABS to retain its properties, as successive heat cycles from ABS plastic molding degrade its chemical structure. The recyclability of ABS allows it to function in roles where sustainability and cost reduction are important. Note that ABS is recyclable but not biodegradable, as it is a petroleum-based thermoplastic.
ABS plastic molding is widely used throughout industry as a general-purpose engineering material, thanks to its exceptional blend of abundance and material properties. Here are some of the most common applications of ABS injection molding in industry.
If Injection molded ABS does not seem like a good fit for your project, Xometry has an extensive portfolio of alternate plastic molding services and manufacturing tools to help you bring your ideas to life.Â
GETTING A QUOTE WITH LK-MOULD IS FREE AND SIMPLE.
FIND MORE OF OUR SERVICES:
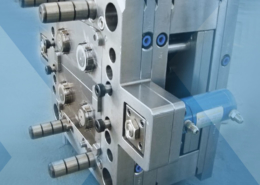
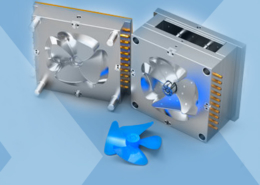
Plastic Molding

Rapid Prototyping
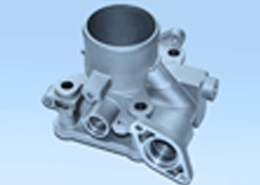
Pressure Die Casting
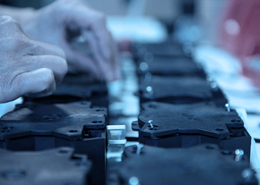
Parts Assembly
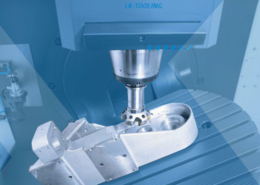