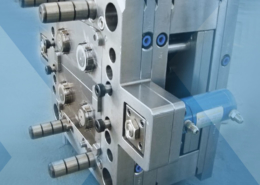
injection molding short shot - viewmold.com - short shot injection molding
Author:gly Date: 2024-10-15
An injection molding machine consists of a heated barrel equipped with a reciprocating screw (driven by hydraulic or electric motor) which feeds the molten polymer into a temperature controlled split mold via a channel system of gates and runners. The screw units (plasticizes) the polymer and acts as a ram during the injection phase. The screw action also provides additional heating by virtue of shearing action on the polymer. The polymer is injected into a mold tool that defines the shape of the molded part.
As the plastic shrinks, it applies pressure on the mold. During ejection, the walls of the part will slide and scrape against the mold, which can result to drag marks.
If sections of different thicknesses are required, make the transition as smooth as possible using a chamfer or fillet. This will allow the material to flow more evenly through the mould.
The 360 Quadrant efficiently maps the Injection Molding Machine Companies based on criteria such as revenue, geographic presence, growth strategies, investments, channels of demand, and sales strategies for the market presence of the Injection Molding Machine quadrant. While the top criteria for product footprint evaluation included Materials (Plastic, Rubber, Metal, Ceramic), Type of Machines (Hydraulic, All-Electric, Hybrid), End-Use Industry (Automotive, Consumer Goods, Packaging, Healthcare, Electronics, Others).
Thick sections can lead to various issues such as warping and sinking. Reducing the maximum thickness of the design can be achieved by making the thicker sections hollow is essential. To improve the strength of these sections, ribs can be used to create structures that are of equal strength and stiffness but with reduced wall thickness and weight.
The Injection Molding Machine Companies quadrant is a comprehensive industry analysis that provides valuable insights into the global market for Injection Molding Machine. This quadrant offers a detailed evaluation of key market players, technological advancements, product innovations, and industry trends. MarketsandMarkets 360 Quadrants evaluated over 60 Injection Molding Machine Companies of which the Top 15 Injection Molding Machine Companies were categorized and recognized as the quadrant leaders.
Here at UNSW we have 2 CR Clarke desktop injection moulders great for learning, testing and experimenting with the process!
Undercuts refer to part features that cannot be manufactured with a simple 2-part mould because material is in the way while the mould opens or during the ejection of the part. Avoiding undercuts all together is usually the best options as they add cost, complexity and maintenance requirements to the mould.
The Injection Molding Machine Companies quadrant is a comprehensive industry analysis that provides valuable insights into the global market for Injection Molding Machine. This quadrant offers a detailed evaluation of key market players, technological advancements, product innovations, and industry trends. MarketsandMarkets 360 Quadrants evaluated over 60 Injection Molding Machine Companies of which the Top 15 Injection Molding Machine Companies were categorized and recognized as the quadrant leaders. An injection molding machine consists of a heated barrel equipped with a reciprocating screw (driven by hydraulic or electric motor) which feeds the molten polymer into a temperature controlled split mold via a channel system of gates and runners. The screw units (plasticizes) the polymer and acts as a ram during the injection phase. The screw action also provides additional heating by virtue of shearing action on the polymer. The polymer is injected into a mold tool that defines the shape of the molded part. The 360 Quadrant efficiently maps the Injection Molding Machine Companies based on criteria such as revenue, geographic presence, growth strategies, investments, channels of demand, and sales strategies for the market presence of the Injection Molding Machine quadrant. While the top criteria for product footprint evaluation included Materials (Plastic, Rubber, Metal, Ceramic), Type of Machines (Hydraulic, All-Electric, Hybrid), End-Use Industry (Automotive, Consumer Goods, Packaging, Healthcare, Electronics, Others). Key trends highlighted in 360 Quadrants: The injection molding machine industry has seen steady growth in recent years. By 2027, the global market is expected to reach USD 12.4 billion, growing at a CAGR of 4.50% from USD 10.4 billion valuation in 2023. This growth can be attributed to rising demand across end-use sectors like automotive, consumer goods, packaging, healthcare, and electronics. Key drivers fostering the growth of the market include increasing healthcare needs, rapid industrialization in developing economies, and growing use of plastic molds in electric vehicle manufacturing. Asia Pacific currently leads the global market in both volume and value, followed by Europe and North America. The growth in Asia Pacific region is majorly due to the increased demands from the emerging economies in the region that are witnessing high demand from the automotive, consumer goods, packaging, medical, and other industries. Owing to this the Asia Pacific region is expected to largest and fastest growing market for injection molding machine market. This high growth in the emerging economies provides a multitude of opportunities for injection molding machine companies. Plastic was the dominant material, accounting for nearly 85.2% of the market in 2023. This is due to the versatility and cost-effectiveness of plastic injection molding for high-volume production of automotive, packaging, consumer goods, healthcare, and electronics parts. With the widespread and growing use of plastic globally, the plastic segment is expected to see the fastest growth rate from 2023 to 2027. Meanwhile, rubber injection molding holds a smaller but substantial share of the overall market, as the second largest segment in 2023, mostly because of continued demand for rubber components and products. While plastics lead the market now, there are growth opportunities across all injection molded material types as injection molding machine companies want to produce diverse components through this high-efficiency process. Hydraulic injection molding machines have historically dominated the global market due to their lower costs, longer service life, technical advantages, and widespread use. However, all-electric injection molding machines are expected to see the fastest growth at a CAGR of nearly 4.00% over the forecast period. This can be attributed to its ability to provide higher clamping force for larger parts, increased repeatability, enhanced precision, reduced downtime, and energy-efficient features. The primary hurdle lies in the substantial initial investment required. For injection molding machine companies, this shift implies a need to adapt to the evolving market demands. Injection Molding Machine Companies that have traditionally focused on hydraulic machines may face challenges in maintaining their market share unless they invest in and integrate all-electric technologies. Embracing the growing demand for all-electric machines with their advantages in higher clamping force, increased repeatability, enhanced precision, reduced downtime, and energy efficiency could be crucial for staying competitive. The injection molding machine market is highly competitive, with both global and regional injection molding machine companies holding a substantial share. The key injection molding machine companies profiled in the quadrant include Haitian International Holdings Limited (China), Chen Hsong Holdings Limited (China), Sumitomo Heavy Industries Ltd. (Japan), ENGEL Austria GmbH (Austria), Hillenbrand, Inc. (USA), and others. They consistently employ developmental strategies such as expansions, product launches, acquisitions, and contracts & agreements to strengthen their positions in the injection molding machine market. For example, in May 2023, KraussMaffei introduced a special edition of its proven CX series. The special edition, named "#185," included a package of attractive additional features that would normally incur charges but were integrated at no extra cost. This allowed users to enhance the quality and efficiency of injection molding applications in the clamping force range from 500 to 4200 kN, simultaneously achieving an immediate and noticeable reduction in operating costs. The healthcare industry is rapidly adopting injection molding technology to manufacture medical devices and products. This growth is driven by the benefits injection molding provides for producing disposable and durable goods like drug delivery systems, blood glucose tests, and mobility aids. As the population ages, the demand rises for convenient, lightweight, and cost-effective medical products. Injection molding allows mass production of these goods with consistency. The process is ideal for items used frequently in hospitals and homes. With more disposable and durable medical goods, injection molding machine companies see increasing opportunities in the healthcare sector. This rising demand from healthcare therefore promises growth for the injection molding machine market.
The outer diameter of the boss should be 2x the nominal diameter of the screw or insert and its inner diameter equal to the diameter of the core of the screw.
When the interior of a part solidifies before its surface, a small recess in an otherwise flat surface may appear, called a sink mark.
Injection moulding typically produces parts with tolerances of +/- 0.25mm. Tighter tolerances can be possible in certain situations but increase the cost of manufacture dramatically.
When certain sections cool (and as a result shrink) faster than others, then the part can permanently bend due to internal stresses.
For interior edges, use a radius of at least 0.5 x the wall thickness. For exterior edges add a radius equal to the interior radius plus the wall thickness to ensure constant thickness everywhere. This can also help to stop stress concentrating in the sharp corners which can cause weaker parts.
Bosses consist of cylindrical projections with holes designed to receive screws and other fasteners and assembly hardware, they are very common in injection moulded parts as they are used as points of attachment or assembly.
Commercially, injection moulding offers a flexible, consistent and cost-effective process of manufacturing that allows for rapid production of parts in a range of materials. Once the process has been set up and tested, machines can produce thousands of items per hour and once the mould is created (which is the most expensive element) the cost of production per component is relatively low.
Draft angle is a taper applied to the vertical walls of the component to be moulded to assist with releasing the part. Walls without draft angle may become stuck in the mould and will have drag marks on their surface.
When adding text choose embossed text over engraved text as it is more economical when creating the mould. Raising the text 0.5mm above the part surface will ensure the letters are easy to read.
When even the maximum recommended wall thickness is not enough to meet the functional requirements of a part, ribs can be used to improve the strength and stiffness of a part.
Redesigning the part to remove undercuts or moving the part line can be possible solutions to make the design more feasible.
When 2 flows meet, small hair-like discolorations may develop. These knit lines affect the parts aesthetics, but also they generally decrease the strength of the part.
To avoid warping and sink marks on the part as the melted material cools down it is important to have uniform wall thicknesses and avoid thick sections if possible.
Trapped air in the mold can inhibit the flow of the material during injection, resulting in an incomplete part. Good design can improve the flowability of the melted plastic.
360 Quadrants is a scientific research methodology by MarketsandMarkets to understand market leaders in 6000+ micro markets
Injection moulding is a manufacturing process that melts, injects and sets plastic into a metal mould. The plastics used by injection molding processes are relatively cheap and can be used to achieve a wide variety of properties, so injection molding is popular for creating many packaging and consumer products, like LEGO!
360 Quadrants is a scientific research methodology by MarketsandMarkets to understand market leaders in 6000+ micro markets
When designing ribs, use a thickness equal to 0.5 x the main thickness, define a height smaller than 3 x the rib thickness and use a base fillet with a radius greater than 1/4 x the rib thickness. Also make sure to add draft angle!
The uniform wall thickness limitations also applies to edges and corners; the transition must be as smooth as possible to ensure good material flow through the mould.
GETTING A QUOTE WITH LK-MOULD IS FREE AND SIMPLE.
FIND MORE OF OUR SERVICES:
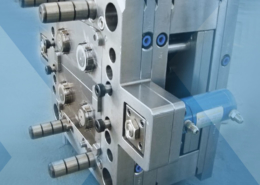
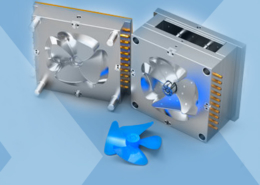
Plastic Molding

Rapid Prototyping
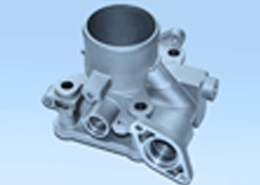
Pressure Die Casting
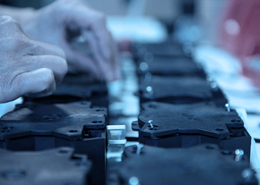
Parts Assembly
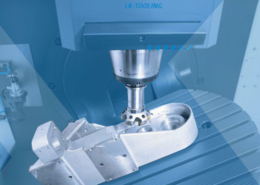