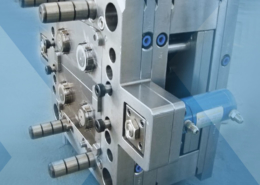
Injection Molding Service Australia | Plastic ... - precision plastic injection
Author:gly Date: 2024-10-15
In the overmold cavity a second molten material — known as the overmold — is injected around the substrate base. The two layers bond either mechanically or chemically to form the final product.
While they share several similar production steps, there are key differences in the techniques. It is these dissimilarities that help determine which process is best suited for a specific application.
Overmolding is a multi-shot process, involving two separate molding operations and two separate tools. It combines a rigid substrate base with a pliable outer layer of plastic such as thermoplastic elastomer (TPE) or liquid silicone rubber (LSR). The substrate base is formed by injecting resin into a tool, where it cools and solidifies before being moved to an overmold cavity within a different tool.
In ABS injection molding, ABS plastic pellets are melted and injected into the cavity of a two-part mold that forms a single part. As soon as the mold is filled, the plastic will solidify and cool into the shape of the mold.
To provide context for an accurate comparison of two-shot injection molding and overmolding, a brief overview of each process is necessary:
Two-shot injection molding and overmolding are versatile solutions. But, what makes one more practical than the other for a specific application?
Overmolding is an ideal solution for commercial and industrial applications such as soft-grip handles on razors, toothbrushes, and handheld tools. In medical and automotive applications, overmolding may be used to decrease vibration, insulate sound, and improve chemical resistance.
Two-shot injection molding (or, two-stage molding) and overmolding are popular choices for many applications. They are also often mistaken as being interchangeable.
To learn more about plastic injection molding, visit our blog. To browse our services, check out our services page. If you’re ready to begin your custom project, request a quote today.
Injection-molded parts are integral to the performance and aesthetics of a wide range of products. Manufacturers depend on the expertise of their injection molding partner to guide decisions and processes that lead to desired outcomes.
With minor design modifications, injection-molded plastic parts can likely be made using either two-shot or overmolding processes. However, the approach to determining which technique is most appropriate for your application shouldn’t be taken lightly.
The newly molded substrate is then transferred either robotically, manually, or via an automated rotary plane to a different cavity within the same tool. In the second phase, the substrate rotates 180 degrees in the tool. Another resin is then injected to surround and molecularly bond to it. Once cooled, the final part is ejected.
ABS refers to acrylonitrile butadiene styrene, a thermoplastic polymer commonly used for injection molding. The primary ingredients of acrylonitrile, butadiene, and styrene each impart specific properties to ABS injection molded parts. Acrylonitrile adds hardness and provides heat and chemical resistance. Butadiene offers added toughness and impact resistance. Styrene adds strength, gloss, and workability.
To make a well-informed decision, it’s important to also consider what may make the injection molding processes less desirable.
The more knowledge you have, the better prepared you will be to make the best choice. Before making injection molding decisions on current or future projects, get up to speed on Overmolding Fundamentals for OEMs. Click the button below to download your copy of this valuable white paper.
Lerner Molded Plastics is an ISO-certified plastic molding manufacturer that can create high-quality design and tooling solutions for your project. Our custom and offshore injection molding capabilities enable us to meet small, intricate, multi-cavity, or large component specifications. We aim to ensure repeatable, reliable solutions for your applications, and we meet this challenge by adhering to the strictest industry standards.
ABS plastic injection molding has multiple benefits and applications. Since injection molding is so versatile, it is a preferred method for rapid part manufacturing. The main benefits include:
Two-shot molding consists of two phases (or shots of material) in one injection molding operation. The first phase resembles traditional injection molding. Resin is flowed into one cavity of the tool, and allowed to solidify and cool in order that the substrate holds the proper shape.
To prevent part defects, consider the mold shrinkage (0.004 to 0.007 inches) and water absorption (0.16% to 0.25%) of ABS. These properties affect curing and processing. Other properties to consider when ABS molding are:
Typically, two-shot injection molding is used for complex applications that may require multiple materials or multiple colors. Interior parts in vehicles, appliances and housewares, and device panel push buttons or handle grips exemplify common applications for this process.
Plastic injection molding is a manufacturing process that injects melted plastic using high pressure into a pre-shaped mold to create products with particular specifications. Lerner Molded Plastics provides injection molding design services for ABS injection molding projects. We have over 35 years of experience designing injection molds and a cutting-edge injection molding facility. Here you can learn more about ABS injection molding and its benefits, applications, and considerations.
GETTING A QUOTE WITH LK-MOULD IS FREE AND SIMPLE.
FIND MORE OF OUR SERVICES:
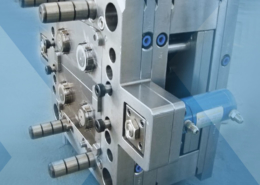
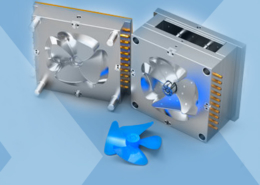
Plastic Molding

Rapid Prototyping
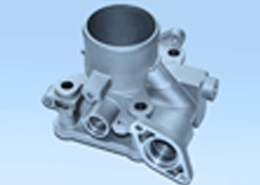
Pressure Die Casting
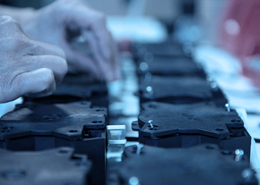
Parts Assembly
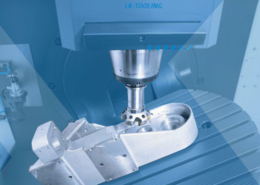