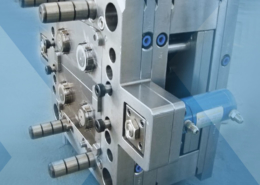
Injection Molding Service Australia | Plastic ... - plastic custom molding
Author:gly Date: 2024-10-15
Using a less expensive material for the core layer and premium material for the skin layer can reduce overall material costs without compromising product quality. This approach is particularly beneficial for high-volume production efficiency.
Technological advancements in co-injection technology, particularly in hot runner systems and process control, have significantly improved product quality and production efficiency. This has made co-injection molding a preferred choice in various industries, such as automotive, consumer goods, and beverage packaging.
The co-injection experience lets manufacturers combine at least two materials with varying characteristics, resulting in injection-molded parts with enhanced performance, durability, and cost-effectiveness.
These advancements for a hot runner system ensure precise melt delivery and temperature control, improving part quality and reducing waste.
By combining different polymers, manufacturers can optimize the properties of the final product. For example, a rigid core made of hard material can provide structural strength, while a softer skin material can offer a smooth surface finish and improved tactile properties.
In this process, skin material and core material choices are subjected to sequential or simultaneous injection into the mold cavity of an injection molding machine, creating a layered structure within the molded part–hence its nickname, “sandwich molding.”
Co-injection molding can reduce material costs by using a less expensive core material. Additionally, the process can minimize waste and reduce the need for post-processing, leading to overall cost savings.
The mold is designed to accommodate the co-injection process. It must have separate channels for skin material and core material choices, which are then injected into the mold in the correct sequence and proportions.
Co-injection molding is finding new applications in industries beyond traditional plastics manufacturing, including advanced composites and metal injection molding.
Recent advancements in co-injection technology have further expanded its capabilities and applications. Innovations include:
Co-injection molding is a complex process that requires careful consideration of material properties, mold design, and injection parameters. Compared to the creation of standard monolayer injection molded variants, here’s a breakdown of the co-injection molding process:
In the packaging industry, co-injection molding creates containers and packaging solutions that offer superior barrier properties, strength, and aesthetic appeal. This is particularly important for food and beverage packaging, where maintaining product integrity and shelf life is crucial. Creating barrier layer materials within the container walls helps extend shelf life and protect contents from external factors. Applications include:
Whether you are new to the topic or an industry professional, this comprehensive guide will provide valuable insights into the co-injection experience.
Polystyrene is a synthetic aromatic hydrocarbon polymer made from the monomer styrene. It is a lightweight, rigid plastic known for its ease of processing and ability to be molded into various shapes. Polystyrene can be categorized into two main types:
Co-injection molding allows for greater design flexibility, enabling the production of parts with excellent clarity, multiple colors, textures, and finishes. This capability is particularly valuable for consumer products, where a product’s desired appearance is a critical factor.
Evaluate the materials needed for your product. Co-injection molding is ideal if your design requires a combination of properties that cannot be achieved with a single material. Consider the compatibility of skin and core materials, as well as their individual properties.
The automotive sector leverages co-injection molding to create components that combine a robust, high-strength core material with a lightweight, aesthetically pleasing outer skin. This results in parts that are not only durable but also meet stringent safety and performance standards. Common applications include:
A hot runner system can help maintain precise temperature control within the ejection molding machine throughout the process.
For more about complete guide to polystyrene (ps) injection molding, you can pay a visit to Djmolding at https://www.djmolding.com/molding-service/ for more info.
The co-injection process requires specialized equipment, including multi-material injection units and advanced hot runner systems.
Co-injection technology differs from the one used to create standard monolayer injection molded parts by utilizing at least two materials instead of just one material.
Polystyrene (PS) injection molding is a highly versatile manufacturing process for creating intricate and durable plastic parts. Due to its efficiency and cost-effectiveness, this process is widespread in industries such as packaging, automotive, electronics, and consumer goods. Understanding the nuances of PS injection molding can significantly impact production quality and cost. This comprehensive guide will delve into the essential aspects of polystyrene injection molding, from the properties of PS to the technical details of the molding process and best practices for achieving optimal results.
Analyze your budget constraints. While the initial investment in co-injection molding equipment may be higher, the long-term cost savings from material optimization and reduced waste can be significant. To reduce costs, consider using recycled materials or virgin resin in the core layer.
This sequential or simultaneous injection ensures that the core is entirely surrounded by the outer skin material. The process also follows an optimal ratio to ensure the creation of the right plastic part.
Polystyrene injection molding is a vital process in modern manufacturing, offering a blend of cost-effectiveness, precision, and versatility. Manufacturers can optimize their production processes and achieve high-quality results by understanding PS properties, the molding process’s intricacies, and best practices. As the industry moves towards more sustainable and innovative solutions, staying informed about advancements will be crucial for maintaining competitive advantage and addressing environmental challenges. Whether a seasoned professional or new to the field, this guide provides a solid foundation for mastering PS injection molding and leveraging its benefits in your manufacturing endeavors.
Co-injection molding can reduce waste and carbon dioxide emissions using recycled or lower-grade core and skin material choices, contributing to more sustainable manufacturing practices.
One such advanced hot runner system is the Polyshot Firebox 3601F, detailed in the table below, which offers precise temperature control to ensure optimal performance throughout the co-injection molding process.
Co-injection molding is a versatile manufacturing process that excels in producing complex part designs. This advanced technique involves injecting two different materials into a single mold, allowing for the creation of parts with unique properties and intricate geometries.
Advanced simulation tools enable manufacturers to model and optimize the co-injection process, predicting potential issues and improving design efficiency before production.
Djmolding is plastic injection mold maker in china,as a china plastic injection molding manufacturer supplier factory,we supplying high-precision plastic injection products,low volume injection molding for low volume manufacturing service,high volume injection molding,quick-turn injection molded parts and so on.
automotive injection molding companies Best Top 5 Low Volume Injection Molding Companies china low volume injection molding contract manufacturing low volume Custom Low Volume Plastic Parts Manufacturing custom plastic injection molding china injection moulding of liquid silicone rubber Low-volume injection molding cost low-volume manufacturing china Low Volume Injection Molding low volume injection molding canada low volume injection molding companies low volume injection molding company low volume injection molding europe low volume injection molding in usa low volume injection molding manufacturers low volume injection molding services low volume injection moulding uk low volume low cost plastic injection moulding low volume manufacturing low volume manufacturing companies low volume manufacturing processes low volume manufacturing service low volume manufacturing services low volume manufacturing strategies Low Volume Plastic Injection Molding low volume plastic manufacturing low volume plastic parts low volume plastic parts production low volume production plastic parts low volume production sheet metal low volume silicone molding metal pressing in low volume production plastic injection molding manufacturer plastic molding low volume production pvc low volume manufacturing mold custom factory online Short Run Injection Molding short run injection molding cost short run plastic injection molding small batch injection molding small batch plastic manufacturing small plastic parts manufacturer small quantity injection molding small volume manufacturing small volume silicone manufacturing
For example, a product can have a tough, impact-resistant skin material layer and a lightweight, cost-effective core material layer. This dual-material approach not only improves the overall quality of the product but also allows for greater design flexibility.
Ongoing research and development in polymer science have led to new materials specifically designed for co-injection molding, offering enhanced properties and compatibility between skin and core materials.
Co-injection molding, also known as sandwich molding, is an advanced manufacturing process that involves injecting two different materials into the same mold to create a part with distinct properties.
The medical device industry significantly benefits from the precision and material versatility of co-injection molding. Medical components often require biocompatible materials that can withstand sterilization while maintaining structural integrity. Co-injection technology enables the production of the right mold and parts that meet these stringent requirements.
By understanding the process, benefits, and applications of co-injection molding, manufacturers and brand owners can make informed decisions to optimize their production and achieve superior part performance. If you’re ready to take your co-injection molding projects to the next level, you can check out Polyshot for efficient products for your hot runner system.
To achieve the desired distribution of skin and core materials, factors such as wall thickness, gate location, and flow path must be carefully considered.
However, some manufacturers have developed solutions to retrofit an older injection molding machine for co-injection capabilities, making the technology more accessible to existing machines.
Co-injection molding is a sophisticated manufacturing process that combines two different materials into a single molded part, offering numerous benefits over standard monolayer injection molding. This technique enhances product strength, durability, and cost-efficiency while allowing for complex designs and diverse materials.
Co-injection molding requires precise control over the injection process to ensure that the skin and core materials are distributed correctly.
Consider the production volume of your project. Co-injection molding is cost-effective for high-volume production runs due to its material efficiency and reduced cycle times. The initial investment in equipment and mold design can be offset by the benefits of high-volume production efficiency.
The field of injection molding, including PS, is evolving with advancements in technology and materials. Key trends include:
By combining materials with different properties, co-injection molding can produce parts with superior strength and durability. The core material can provide rigidity, while the skin can offer flexibility or impact resistance.
The choice of materials for co-injection molding is critical. Not all materials suit this process, and finding the right combination of core material choices and skin materials can be challenging.
By combining different materials, manufacturers can optimize the properties of the final product. For example, a rigid core material can provide structural strength, while a softer skin material can offer a smooth surface finish and improved tactile properties.
Co-injection molding is utilized across various industries due to its versatility and the ability to produce high-quality parts. Some of the key sectors benefiting from this technology include:
The integration of co-injection molding with Industry 4.0 technologies, such as IoT sensors and machine learning algorithms, is enabling real-time process optimization and predictive maintenance.
The co-injection molding machine is equipped with two injection units. The first unit will have the skin material injected into the mold cavity. Once the skin material is in place, the second unit injects the core material, which is encapsulated by the skin.
Companies like Polyshot have made significant strides in hot runner system technology, developing systems designed explicitly for co-injection molding.
Ensuring compatibility between the skin and core materials is crucial for successful co-injection molding. Incompatible materials can lead to poor bonding or inconsistent fill patterns.
Polyshot, a leading manufacturer of hot runner system products, offers hot runner manifold systems for creating advanced mold designs for a co-injection molding machine.
The ability to use recycled or bio-based materials in the core layer while maintaining a virgin resin skin drives increased adoption of co-injection molding in industries focused on reducing their carbon dioxide emissions and overall environmental impact.
Combining at least two materials or different polymers can create parts with two material properties that complement each other.
The dual-material structure can improve the product’s durability, lifespan, and mechanical properties. The core material can be chosen for its resistance to impact and wear. In contrast, the skin material can be selected for its resistance to environmental factors such as UV radiation and chemicals.
Injection molding is a manufacturing process where molten plastic is injected into a mold cavity to produce a part. The process is highly automated and suitable for producing large volumes of identical parts. The steps involved include:
A modern injection molding machine equipped for co-injection is now fitted with sophisticated control systems that allow for precise regulation of material flow, precise melt delivery, temperature, and pressure.
The aerospace industry requires materials that can withstand extreme conditions while minimizing weight. Co-injection molding can help produce components that meet these demanding specifications by combining lightweight core materials with high-strength outer skin material components. Applications include:
Factors such as melt viscosity, thermal expansion, and shrinkage rates must be considered to ensure optimal performance.
New techniques are being developed to achieve complex color gradation results and visual effects through co-injection molding, opening up new product design and branding possibilities.
The co-injection molding process allows for combining polymers with different properties, resulting in enhanced performance, aesthetics, and cost-effectiveness compared to standard monolayer injection-molded parts from a one-material source.
Ensure that co-injection molding meets your industry’s regulatory and performance standards. This process is particularly advantageous in industries with stringent quality requirements, such as automotive, medical devices, and beverage packaging.
In this article, we will explore the co-injection molding process, its benefits, and its applications across various industries. We will also discuss the technological advancements that have made this process more efficient and effective and how they contribute to improved product quality.
Due to the need for multiple material injections and the complexity of the process, co-injection molding can have longer cycle times than traditional injection molding.
Huizhou Djmolding Co., Ltd, established in 2010, is a leading plastic injection moulding and mould manufacturer in China. Djmolding is a low volume manufacturing companies specializes in plastic mould and plastic parts production for household appliances, medical equipments, electronic equipments, safety equipments as well as monitoring system.
The Complete Guide to Polystyrene (PS) Injection Molding provides an in-depth look at the advantages of this widely used manufacturing process, especially its appeal for high-volume production. Here’s a detailed exploration of the key benefits:
The dual-material structure can improve the durability and lifespan of the product. The core material can be chosen for its resistance to impact and wear, while the skin material can be selected for its resistance to environmental factors.
One of the standout benefits of co-injection molding is the ability to produce parts with enhanced mechanical properties. In packaging applications, co-injection molding can create high-performance barriers that extend shelf life and protect contents from external factors.
The Complete Guide to Polystyrene (PS) Injection Molding highlights these key benefits and demonstrates why this technique is favored across various industries. By combining cost-effectiveness, precision, versatility, and minimal waste, PS injection molding is a highly efficient and practical choice for modern manufacturing.
Co-injection molding allows for greater design flexibility, enabling the production of plastic parts with multiple colors, textures, and finishes. This capability is particularly valuable for consumer products where appearance is a critical factor.
Using different materials for the core and skin allows for greater design flexibility. Brand owners and manufacturers can achieve high-quality surface finishes, vibrant colors, and intricate textures without secondary operations.
In the consumer electronics industry, co-injection molding is used to produce parts that require a combination of strength, precision, and aesthetic quality. Using different materials in a single molding process creates complex, high-performance components essential in modern electronic devices. Applications include:
After the skin material and core material are injected into the mold, the mold is cooled to allow the part to solidify. The cooling rate can be controlled to optimize the material properties and ensure a high-quality finish.
Once the part has been injected into the mold, it is ejected upon solidification. The co-injection parts are then inspected for any defects or inconsistencies.
Assess the complexity of your plastic part design. Co-injection molding is well-suited for intricate designs that benefit from integrating multiple materials. The process can create parts with unique features, such as color gradation or clear package exteriors with barrier cores.
Advanced hot runner systems and control software help maintain the optimal ratio of materials throughout the injection cycle.
GETTING A QUOTE WITH LK-MOULD IS FREE AND SIMPLE.
FIND MORE OF OUR SERVICES:
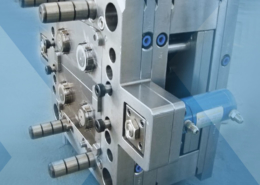
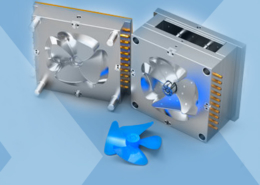
Plastic Molding

Rapid Prototyping
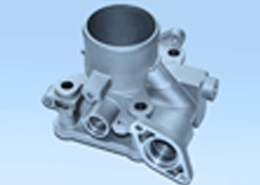
Pressure Die Casting
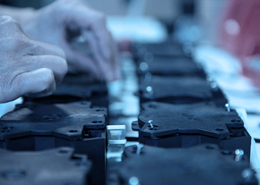
Parts Assembly
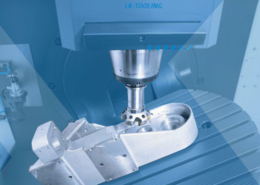