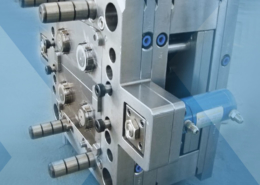
Injection Molding Service Australia | Plastic ... - mould manufacturing company
Author:gly Date: 2024-10-15
For an ultra high-temp plastic like PEEK, the injection molding machine barrel will reach temperatures above 400 °C, with the molds around 160 °C. These high temperatures can pose certain issues, such as residue getting stuck in the barrel feeder areas. High-temp materials like PEEK often necessitate purging of the machine before use of a subsequent molding material.
Cap injection molding machines consist of several essential components, including the hopper, heating cylinder, screw, mold, and hydraulic system. The process starts with plastic granules being fed into the hopper and then melted in the heating cylinder. The melted plastic is then pushed through the screw, which melts and homogenizes the material. The screw then forces the melted plastic into the mold, where it is allowed to cool and solidify into the desired shape. Once the plastic has hardened, the mold opens, and the finished cap is removed. The hydraulic system controls the movement of the mold and ensures that the process runs smoothly.Cap injection molding machines play a crucial role in the production of caps and closures for various products. When choosing a cap injection molding machine, it is essential to consider factors such as production capacity, accuracy, energy efficiency, price, and brand. By considering these factors, you can ensure that you are getting the best machine for your production needs and budget constraints
IML refers to in mold labeling. This molding technique is becoming more and more popular. Because in mold labeling technique can keep the pattern on the product all the time. We can get ready product with pattern after coming out from the mold....
Because the injection molding machine must melt down pellets of the chosen thermoplastics, high-temperature materials are necessarily more difficult to process. However, with the right setup, it is still possible to achieve high-quality moldings using these engineering materials.
Looking for ideal High Speed Pet Injection Molding Machine Price ? We are the manufacturer of PET injection molding machine and have a wide selection at great prices.....
Polyphenylene sulfide (PPS) is another high-performance polymer with engineering applications. As well as having a high CST, it exhibits excellent UV and chemical resistance, making it suitable for outdoor use. PPS parts include gaskets, seals, and electrical insulation. Polyphenylsulfone (PPSU) is slightly weaker and less thermally resistant, but exhibits greater hardness.
The most temperature-resistant injection molding plastics come at a high cost but exhibit excellent thermal performance, both in terms of their continuous service temperature (CST) — how much heat they can withstand over long periods of time — and their resistance to even higher temperatures in short bursts.
Looking for ideal High Speed Pet Injection Molding Machine Price ? We are the manufacturer of PET injection molding machine and have a wide selection at great prices...
We can provide a complete production line for making disposable syringes, Our products have the following advantages :High production efficiency: low noise: smooth gear transmission...
Cap injection molding is a manufacturing process that is widely used for producing various types of caps and closures for different products such as bottled drinks, food containers, and personal care items. The process involves melting a plastic material and injecting it into a mold to produce the desired shape. Cap injection molding machines play a crucial role in this process as they determine the quality and efficiency of the end product. In this article, we will provide a comprehensive guide on cap injection molding machines, including their working principle, types, and key factors to consider when purchasing one.
Injection molding can process a wide range of materials. In addition to metals and thermosets, injection molding is suited to a large number of thermoplastic polymers, from commodity polymers like ABS to high-performance materials like PEEK.
So which are the best heat-resistant thermoplastics for injection molding? This article discusses some of the most popular thermally resistant injection molding materials, noting their respective advantages and applications, as well as discussing the complexities of using such materials during the injection molding process.
Polyether ether ketone (PEEK) is a high-performance polymer used for engineering purposes. With a melting temperature of 343 °C, it is as robust and strong as it is difficult to process. Its extremely high CST makes it suitable for applications in demanding industries like aerospace. Example PEEK parts include bearings, pumps, and compressor plate valves.
3ERP has many years of experience making prototypes and production parts via injection molding, and we can mold parts in the above materials and many more besides. Request a free quote for your next batch of high-temperature plastic parts.
We can provide a complete production line for making disposable syringes, Our products have the following advantages :High production efficiency: low noise: smooth gear transmission.....
Another molding consideration with high-temperature plastics is unwanted freezing off of the nozzle or mold gates. If temperatures are not quite high enough, gates or the machine nozzle can freeze off before the mold cavity is completely filled. Larger gates may mitigate this issue if it persists.
Engineers will select a thermoplastic based on the requirements of the molded part. Some moldings need to be impact-resistant, some need to be food-safe, while others need to be flexible. Another property that engineers and product designers often require is heat resistance. Heat-resistant molded parts can be used in a range of situations, such as near engines, within powerful electronic parts, and in extreme outdoor environments.
Polycarbonate (PC) is often used for its high-quality appearance — especially for transparent parts — and good impact resistance, but the thermoplastic also offers good heat resistance. PC can be molded for uses in electronics, automotive, and aerospace. It is also used for optical and lighting components like headlamp lenses.
Nylon 66 is one of the more heat-resistant polyamides (PA) that is widely used in injection molding. With good mechanical strength and rigidity, nylon 66 has applications in the automotive industry for under-the-hood components like air intake manifolds. Glass-filled PA66 has a slightly higher CST, while PA46 is another good choice for high-temp applications.
Specialize in CNC machining, 3D printing, urethane casting, rapid tooling, injection molding, metal casting, sheet metal and extrusion
Polyoxymethylene (POM) or acetal is another engineering thermoplastic in a lower price bracket than ultra-premium materials like PEEK. It provides good stiffness and low friction, with a relatively high CST. Molded POM can be made into various engineering parts like gears and fasteners, as well as automotive and electronics parts.
Polyetherimide (PEI), often known by the brand name Ultem, is a high-performance polymer often used as a slightly more affordable alternative to PEEK. As well as performing well in high temperatures, it offers good strength, ductility, and chemical resistance. Applications of PEI include medical components, throttle bodies, and thermostat housings.
Engineers sometimes need temperature-resistant moldings that do not need to be of aerospace-grade quality. In these cases, they can choose from more affordable temperature-resistant polymers with good engineering properties. (For the lowest possible budgets, engineers might select a commodity polymer like ABS, which has a reasonable CST of 90 °C but which is also sold in various “high heat” ABS formulations resisting up to 110 °C.)
GETTING A QUOTE WITH LK-MOULD IS FREE AND SIMPLE.
FIND MORE OF OUR SERVICES:
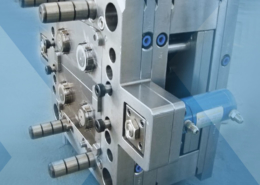
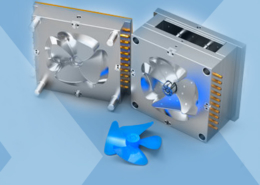
Plastic Molding

Rapid Prototyping
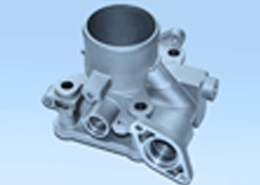
Pressure Die Casting
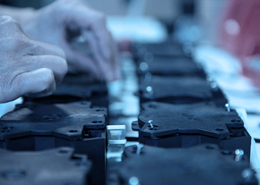
Parts Assembly
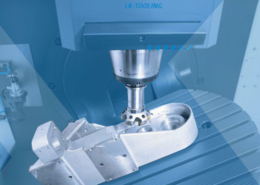