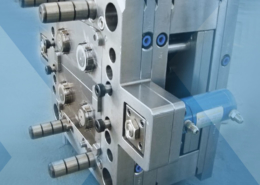
Injection Molding Service Australia | Plastic ... - injection manufacturers
Author:gly Date: 2024-10-15
Trust Kemal to turn your concept into reality through our exceptional on-demand manufacturing services. We have powerful and efficient manufacturing capabilities that allow us to produce both simple and complex prototypes and end-use parts. Our adherence to strict tolerance criteria and quality standards has helped us become China’s leading on-demand manufacturing company.
From quotation to final production, acknowledge the seamless order process at Kemal. Our qualified team ensures you get your plastic molded parts within the provided lead times.
Download our white paper for guidelines for using 3D printed molds in the injection molding process to lower costs and lead time and see real-life case studies with Braskem, Holimaker, and Novus Applications.
The molds are traditionally made out of metal by CNC machining or electric discharge machining (EDM). These are expensive industrial methods that require specialized equipment, high-end software, and skilled labor. As a result, the production of a metal mold typically takes four to eight weeks and costs anywhere from $2,000 to $100,000+ depending on the shape and the complexity of the part. For smaller part quantities, the cost, time, specialized equipment, and skilled labor required to fabricate the mold out of common tooling metals and manufacturing methods often makes injection molding at this scale unobtainable. However, there are alternatives to machining molds out of metal. Leveraging in-house 3D printing to fabricate injection molds for prototyping and low-volume production significantly reduces cost and time compared to metal molds, while still producing high-quality and repeatable parts.
Our team securely packages your plastic molded parts before dispatching them to avoid damage. We have partnered with logistics to schedule timely delivery at your place.
Prior to assembly, you may choose to finish the mold to meet critical dimensions with hand-sanding, desktop or CNC machining.
In this white paper, learn how to combine rapid tooling with traditional manufacturing processes like injection molding, thermoforming, or casting.
With a wide array of manufacturing capabilities, Kemal provides precision machining of exceptional quality. Our on-demand manufacturing services cover everything from prototyping to mass production, allowing us to produce products with complex geometries and high aesthetic demands. Our team of skilled experts, together with our advanced technologies, make this all possible.
It may take a few shots to identify your ideal process conditions as many factors are at play including part geometry, choice of plastic, injection temperatures and pressures, and other parameters.
Multiplus is an injection molding solutions provider based in Shenzhen that covers the entire production cycle from design to manufacturing of plastic products and provides services to over 250 clients per year, including some Fortune 500 companies. Some of these clients require small batch production, which is traditionally expensive and time-consuming with injection molding due to the complexity of manufacturing hard tooling.
Accelerate product development, reduce costs and lead times, and bring better products to market by incorporating 3D printing and low-volume injection molding into your development process.
Our manufacturing process adheres to a stringent quality control system that guarantees exceptional prototypes and production parts.
Read our process conditions documentation to see test results with both desktop and industrial injection molding machines.
A broad range of thermoplastics can be injected with 3D printed molds such as TPE, PP, PE, ABS, POM, ASA, PA, PC, or TPU.
Stay updated with the latest 3D printing news, interviews with experts from around the world and tutorials on how to leverage 3D printing.
We deliver T1 sampling for inspection and review before mass production. The process ensures error identification and precise manufacturing of the plastic part.
By using the same manufacturing method including mold design and materials, these parts can be tested in the field and ensure the designs are ready to be produced at scale. The 3D printed mold designs can then be easily adapted for tool-grade steel during mass production.
Working with our experts having 20+ years of experience in the injection molding industry, efficiently complete a turnaround from prototyping to production.
Custom or rapid on-demand injection molding can be required to manufacture customized end-use parts for specific purposes, such as human factors, application, or occasion, often on an expedited timeline. The limited volume and/or short lead time means traditional injection molding with hard tooling is neither efficient nor feasible. In these cases, low volume injection molding with 3D printed molds is an ideal solution to speed up the process and deliver custom parts.
Kemal’s facilities cover 8500 square meters. We have 180 staff, including 30 experienced engineers, and 80 skilled toolmakers working to HASCO, DME & LKM standards.
Braskem used a 3D printed mold in combination with a traditional industrial injection molding machine to rapidly injection mold the mask straps.
Injection molding is a fast, intensive process where high heat and pressure are involved to inject molten material inside a mold. The molten material depends on the scope of the manufacturing project. The most popular materials are various thermoplastics, such as ABS, PS, PE, PC, PP, or TPU, but metals and ceramics can be injection molded as well. The mold consists of a cavity that accommodates the injected molten material and is designed to closely mirror the final features of a part.
Short-run injection molding provides manufacturers with a means to produce smaller series of end-use parts for products that are only produced in limited quantities or manufacture a pilot series of a product for testing the market before sinking too much capital into the venture.
While injection molding is traditionally considered a manufacturing process only for mass production due to its high tooling costs, leveraging 3D printing to fabricate injection molds can empower you to use this process to produce high-quality and repeatable parts for prototyping and low-volume production.
The cooling time of a polymer printed mold is longer than that of a metal mold, as thermal transfer occurs slower in plastic than metal. As such, adding cooling channels to your printed mold is generally not suggested.
The example of Braskem, one of the world’s leading petrochemical companies, highlights the case for using 3D printed molding to fulfill rapid orders on-demand. During the first wave of the COVID-19 pandemic, the company needed to produce thousands of mask straps to protect its global workforce. Braskem identified injection molding as the ideal method to produce the parts, but without access to 3D printing, they would have had to outsource an expensive metal mold, costing the team money and valuable time.
At Kemal, we’re dedicated to bringing your injection molds related ideas to life. Our team of creative plastic molds manufacturing experts is always available to execute your project in the most efficient ways.
Using low-volume injection molding provides the opportunity to manufacture accurate and repeatable end-use parts without the high fixed costs associated with traditional injection molding.
Even though 3D printing molds can offer these advantages when used appropriately, there are still some limitations to be aware of. We should not expect the same performance from a 3D printing polymer mold as from a machined metallic one. Critical dimensions are harder to meet, cooling time is longer because the thermal transfer occurs slower in plastic, and printed molds can more easily break under heat and pressure. However, companies across the industry are continuing to implement 3D printed molds into their short-run injection molding workflows, enabling them to quickly produce hundreds to thousands of parts. From designing functional prototypes with end-use materials, fabricating parts during pilot production, or manufacturing low-volume or custom end-use parts, 3D printing injection molds is a cost-effective and quick way to produce parts in limited quantities.
Kemal delivers high-quality precision machining with an incredible range of manufacturing capabilities. From prototyping to mass production, we help manufacture products with complex geometries and high aesthetic demands. Our skilled experts and advanced technologies allow us to deliver an extensive range of on-demand manufacturing services.
With nearly 30 years of experience, Kemal supports customers with rapid prototyping, mold making, injection molding, and CNC machining for the automotive, medical, electronics — in a convenient, one-stop solution.
For example, French startup Holimaker develops a manual injection molding machine that enables engineers and product designers to process plastic parts on their desktop in low quantities for prototypes, pilot production, or even a limited series of end-use parts.
In case the parts do not conform to the specifications, please reach out to us within five business days of receipt, and we will resolve the issue within 1-3 business days.
We use preferred material for mold tooling production to provide premium-quality and tailored mold tooling that perfectly fits your application’s specifications.
In this comprehensive guide, learn how you can use 3D printed injection molds with both benchtop and industrial machines to efficiently and affordably produce hundreds of functional prototypes and parts that accelerate product development, reduce costs and lead times, and bring better products to market.
Braskem’s team turned to injection molding using a Formlabs Form 3 3D printer to print the mold for its straps and the all-electric Cincinnati Milacron 110 Ton Roboshot injection molding machine to develop the straps.
At Kemal, we take pride in our ISO 9001:2015 certification, which demonstrates our commitment to producing consistently high-quality products. Throughout our production lines, we strictly adhere to ISO standards, while our rapid prototyping and production lines incorporate cutting-edge technologies for accuracy and precision. Our sophisticated in-house testing and measuring tools guarantee that every component meets your specifications.
The three major applications for low-volume injection molding are rapid prototyping, short-run injection molding, and on-demand or custom injection molding.
Kemal provides prototyping services, including 3D printing, CNC processing, vacuum casting, prototype injection molding, Metal Sheet Fabrication, etc
Demold the part either manually or automatically with ejector pins. Apply a release agent for thermoplastics with high viscosity. Mold releases are widely available and silicone mold releases, such as Slide or Sprayon products, are compatible with Formlabs Resins.
It is recommended to place the printed mold inside a standard metal frame, or a Master Unit Die, to support against high pressures and extend the lifetime of your printed mold. Carefully assemble the 3D printed mold inside the metal frame. Add ejector pins, inserts, side-action parts, and other components as needed.
Curious to learn about the different factors that make up the total injection molding cost? Read our comprehensive guide.
Desktop 3D printing is a powerful solution to fabricate injection molds rapidly and at a low cost. It requires very limited equipment, saving CNC time and skilled operators for other high-value tasks in the meantime. Manufacturers can benefit from the speed and flexibility of in-house 3D printing to create the mold and couple it with the production force of injection molding to deliver a series of units from common thermoplastics in a matter of days. They can even achieve complicated mold shapes that would be difficult to manufacture traditionally and can be used on both desktop and industrial molding machines, enabling development teams to be more innovative. Furthermore, product development benefits from the ability to iterate on the design and test the end-use material before investing in hard tooling.
Learn how Kemal manage the whole manufacturing process of Injection Mold and complete your order on budget and on time, batch after batch.
The predictive model process analyzes molten material behavior within the mold. The advanced mold flow analysis ensures high-quality and precise molded parts.
Kemal takes responsibility for the quality of each mold. That extends as far as signing a mold quality warranty with customers for each tool.
To execute the project feasibly, we provide a DFM report to review your design and identify any flaws and errors before starting the production process.
When possible, it is advised to print the mold flat, directly on the build platform without any supports, in order to reduce warpage.
Support for the very highest standards and technical requirements. For example, we support ISO8 cleanroom injection molding.
Stereolithography (SLA) 3D printing technology is a great choice for molding. It is characterized by a smooth surface finish and high precision that the mold will transfer to the final part and that also facilitates demolding. 3D prints produced by stereolithography are chemically bonded such that they are fully dense and isotropic, producing functional molds at a quality not possible with fused deposition modeling (FDM) 3D printing. Desktop SLA printers, like those offered by Formlabs, can seamlessly be integrated into any injection molding workflow as they are easy to implement, operate, and maintain.
The company offers feasibility studies for their customers, using 3D printed molds for a fast and affordable turnaround. This allows their clients to quickly and affordably prototype designs and validate final manufacturing conditions during the pilot production phase of new product introduction.
After the trial phase, we provide low-volume production service to ensure precision with efficient machinery under expert surveillance, saving time and cost.
As an alternative for mid-volume production of about 500 to 10,000 parts, machining molds out of aluminum can also reduce the fixed costs associated with manufacturing molds. Machining aluminum is five to ten times faster than steel and causes less wear on the tooling, which means shorter lead times and lower costs. Aluminum also conducts heat faster than steel, resulting in less need for cooling channels and allowing manufacturers to simplify mold designs while maintaining short cycle times.
If you are new to injection molding and are looking into testing it with limited investment, using a benchtop manual injection molding machine such as the Holipress or the Galomb Model-B100 could be a good option. Automated small-scale injection molding equipment such as the desktop machine Micromolder or the hydraulic machine Babyplast 10/12 are good alternatives for medium-series production of small parts.
By leveraging 3D printing, the team was producing thousands of straps within a week of receiving the VP’s email and preparing them for shipping to offices around the world.
To sum up, here’s an overview of the different injection molding methods and the mold types that result in the most efficient process and the lowest cost per part depending on the production volume:
The Kemal team has a complete quality control system for incoming raw material, plastic mold manufacturing, injection molding production and delivery.
Design the mold for your part in the CAD software of your choice. Adhere to common design rules for additive manufacturing and injection mold design. Design recommendations specific to polymer 3D printed molds can be found in our whitepaper.
As the demand for small batch production started to grow, Multiplus turned to 3D printing to explore different materials in an attempt to find a cost-effective way to produce cheaper plastic molds for smaller orders and pilot production runs. Fabricating low-volume injection molds with Formlabs 3D printers reduced costs, labor, and time compared to machining aluminum molds, and could seamlessly be used with their Babyplast industrial injection molding machines.
From prototyping to production, Kemal is dedicated to delivering superior quality and reliable functionality. Our extensive range of production-grade metal and plastic materials, combined with highly advanced on-demand manufacturing techniques, enable us to offer high-quality products across several industries.
At Kemal, we follow international tolerance standards and rigorous quality control inspection to meet the highest excellence and fulfill your provided specifications.
Upload your design into PreForm, Formlabs print preparation software. Prepare your print and send it to your Formlabs 3D printer.
Injection molding is one of the leading processes for manufacturing plastics. It is a cost-effective and extremely repeatable technology that yields high-quality parts for large series production. As a result, it is widely used for mass-producing identical parts with tight tolerances.
Choose a 3D printing material and begin your print. Rigid 10K Resin at 50 micron layer height is an ideal choice for most mold designs as it combines high strength, stiffness, and thermal resistance.
Using 3D printed molds, Holimaker managed to shorten the lead time for producing molds for the injection molding process to 24 hours and they use 3D printed injection molds in 80% to 90% of their projects today.
Are you seeking the best-quality injection molding services for rapid custom plastic prototyping? With our fast quotation service, get free injection molding quote and design feedbacks from experts.
In general, 3D printing is the most common way to produce rapid prototypes. However, in the later stages of the development process, there is often a need to produce slightly larger volumes of identical prototypes using the same materials and production processes as for the final parts. These prototypes can then be used for applications like beta and field testing. Combining 3D printed molds with injection molding allows manufacturers to rapidly and efficiently develop functional prototypes and speed up the product development process.
You can request an instant quote from our quotation form. Our expert team will reach out to you within 24 hours to provide consultation throughout the process.
Rapid prototyping helps companies turn ideas into realistic proofs of concept, advances these concepts to high-fidelity prototypes that look and work like final products, and guides products through a series of validation stages toward mass production.
Count on our on-demand CNC machining services for your parts on time, every time. Achieve outstanding results with our CNC milling and turning capabilities in as fast as five days.
The type of injection press does not have a significant influence on the process for low-volume injection molding; traditional large industrial injection molding machines can also be used with 3D printed injection molds. However, these machines are expensive, come with stringent facility requirements, and require skilled labor, and as a result, most enterprises outsource mid- and high-volume production to service providers and contract manufacturers.
Kemal offers proficient technical assistance round the clock, backed by a proficient team of skilled engineers and technicians.
Holimaker used 3D printed molds to injection mold prototypes in POM of a valve connector part for a customer to carry out resistance tests to water pressure.
Insert the plastic pellets, input the required settings, and begin production. A lower clamping force is suggested, particularly if the printed mold is not protected by a metal frame.
In this video, we've partnered with injection molding service provider Multiplus to walk you through the steps of the injection molding process using 3D printed molds.
With one printed mold, Formlabs users are usually injecting 100s of parts in easy-to-process plastics such as TPE, PP, and PE with temperatures up to 250°C. With plastics that require higher injection temperature such as PA or PC, the 3D printed mold might have a shorter lifespan.
GETTING A QUOTE WITH LK-MOULD IS FREE AND SIMPLE.
FIND MORE OF OUR SERVICES:
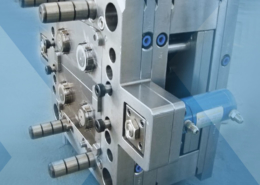
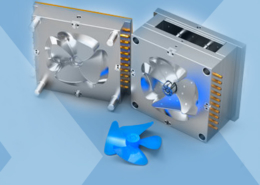
Plastic Molding

Rapid Prototyping
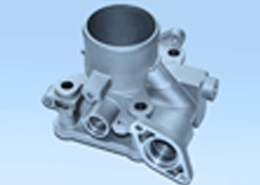
Pressure Die Casting
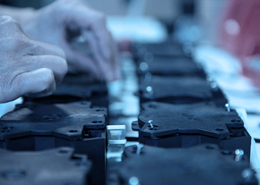
Parts Assembly
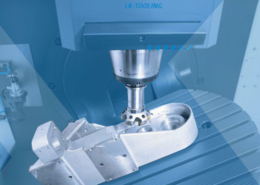